Двигатель УМЗ-4216. Отчет завода
Завершающим этапом совместного проекта журнала «Рейс» и «Группы ГАЗ», который продолжался с августа 2008 года по май 2010 года, по оценке качества и ресурса двигателя УМЗ- 4216 стала полная разборка одного из испытуемых двигателей с наибольшим пробегом в 104 тысячи километров. После разборки двигателя и внешнего осмотра на сервисной станции дилера «Группы ГАЗ» – ООО «Темп-Авто» в подмосковной Балашихе (см. «Рейс» №5-2010 г.) двигатель был отправлен для выяснения остаточного ресурса на Ульяновский моторный завод. Там он был детально осмотрен специалистами, была проведена техническая экспертиза, микрометраж основных деталей. Замеры проведены опытными контролерами Группы метрологии УМЗ под руководством Хализова Н. В. и отражены в картах микрометража по формам ГОСТ 14846.
Результаты замеров систематизированы в табличные формы и проведен анализ размеров сопряжений и зазоров, определяющих в процессе эксплуатации ресурс двигателя до капитального ремонта.
Гильзы цилиндров
Из данных, приведенных в аблице, видно, что износ гильз цилиндров незначительный; фактические размеры не вышли за пределы допуска по конструкторской документации (КД): +48…+60 мкм, группа В. Наибольшие размеры отмечены в 3-м цилиндре: +60 мкм. Овальность и конусность всех гильз незначительная: 5…10 мкм и находится в пределах допуска.
Это подтверждает эффективность внедрения плосковершинного и «мягкого» хонингования гильз цилиндров на двигателях УМЗ-4216 за счет значительного улучшения параметров хонингованной рабочей поверхности гильз по шероховатости и микропрофилю, что обеспечивает оптимальную маслоемкость рабочей поверхности гильзы, позволяет повысить ресурс ЦПГ и снизить расход масла на угар.
Поршень
На поршнях небольшой износ юбки, фактические размеры на 2…4 мкм меньше минимального значения допуска по КД : +12…+24 мкм, группа В. Это подтверждает эффективность перехода к обработке поршней на недавно приобретенных заводом новых полуавтоматах с ЧПУ с установкой оперативной проверки профиля поршня по специальной программе на ПК взамен обработки на токарно–копировальных станках. Это позволило в 2 раза точнее обрабатывать профиль поршня, выполнять маслоудерживающий микропрофиль на юбке, исключить приработочное микропокрытие поршня оловом. Все это в сочетании с изменениями по гильзе повышает ресурс ЦПГ и снижает расход масла на угар.
Зазор цилиндр – поршень
Величина зазора в цилиндрах 1, 2 и 4 составила 30…47 мкм и не превышает значения зазора по КД (24…48 мкм). В 3-м цилиндре максимальный зазор 52 мкм, что является незначительным, по сравнению с предельно допустимым 300 мкм. Таким образом, исходя из фактического, предельно допустимого зазора и удвоенного темпа износа при дальнейшем увеличении зазора остаточный ресурс ЦПГ будет более чем в 2 раза больше отработанного.
Распредвал
Из данных таблицы видно, что износ опорных шеек распредвала незначительный. Фактические диаметры 1, 3, 4, 5 опорных шеек находятся в пределах допуска по КД (0…20 мкм). На 3-й опорной шейке износ несколько больше, диаметр на 10…12 мкм вышел за пределы допуска по КД. Отверстия в блоке цилиндров
Зазор шейка распредвала–отверстие в блоке
Зазор между шейками распредвала и отверстиями в блоке на всех 5-ти опорах находится в пределах допуска по КД (40…85 мкм). Наибольший зазор отмечен на 1-й опоре – 79 мкм. Исходя из фактического, предельно допустимого зазора и практически линейного темпа износа этого сопряжения остаточный ресурс установки распредвала в блоке будет примерно в 2 раза больше отработанного.
Шатунные шейки коленвала
Размеры всех четырех шатунных шеек коленвала находятся в пределах допуска по КД (0…-13 мкм). Разброс значений замеров от -2 до -12 мкм, то есть в пределах всего поля допуска, явно указывает на практическое отсутствие износа шатунных шеек. Овальность и конусность всех шеек незначительная: 2…6 мкм. Наибольшие значения отклонений на 3-й шейке – три замера по -10 мкм.
Коренные шейки коленвала
Диаметры коренных шеек находятся в пределах допуска по КД (0…-13 мкм). Разброс значений замеров от -2 до -13 мкм указывает на практическое отсутствие износа коренных шеек. Овальность и конусность всех шеек незначительная – 2…6 мкм. Наибольшие значения отклонений на 3-й шейке – 2 замера -10 мкм и 1-13 мкм, что может указывать на незначительный износ этой шейки либо на наибольшее влияние биения коленвала на эту шейку при его изготовлении.
Установка коленвалов блоке
Износ вкладышей коренных подшипников коленвала незначительный: превышает верхнее значение допуска по КД (+20…+53 мкм) от 2 до 12 мкм. Наибольшие отклонения отмечены в 4-й коренной опоре – до 12 мкм. Зазоры в коренных подшипниках в 4 поясах из 10 превышает на 1…8 мкм значение зазора по КД (20…66 мкм), что является незначительным, по сравнению с предельно допустимым в коренном подшипнике – 150 мкм. Исходя из фактического и предельно допустимого зазоров, учитывая, что зазор определяется износом вкладышей с практически линейным темпом износа, остаточный ресурс коренного подшипника будет более чем в 2 раза больше отработанного.
Отверстия в бобышках поршня под палец
Отклонения размеров под поршневой палец по всем поршням и бобышкам соответствуют КД – 3-я группа по пальцу, разница в размерах 2 мкм. По шероховатости поверхности (зеркальная) видно, что износ отсутствует.
Поршневые кольца
Зазор в замке в рабочем состоянии верхнего и нижнего поршневых колец на всех 4-х поршнях соответствует допуску по КД (0,3…0,65 мм). Радиальная толщина всех поршневых колец, замеренная в 5-ти точках, соответствует допуску по КД (3,95…4,3 мм).
Высота всех поршневых колец, замеренная в 5-ти точках, соответствует допуску по КД (1,988…2,0 мм). Проведенные замеры показывают на незначительный износ поршневых колец.
Внутренний диаметр втулок клапанов
Отклонения внутреннего диаметра втулок клапанов находятся в допуске по конструкторской документации (0…22 мкм), за исключением одного размера: на втулке №5, выпускной клапан 3-го цилиндра (замер по поясу №2 поперек двигателя), отклонение составило 25 мкм. Этот износ можно считать незначительным, по сравнению с предельно допустимым зазором в сопряжении клапан-втулка – 250 мкм.
reis.zr.ru
УМЗ-4216: Отчет завода — журнал За рулем
Журнал «Рейс» совместно с «Группой ГАЗ» завершил проект, цель которого — оценка качества и ресурса двигателя УМЗ-4216. Измерительные работы разобранного двигателя, проведенные на Ульяновском заводе, подтвердили выводы визуального осмотра: остаточный ресурс УМЗ-4216 не менее 100 тыс. км
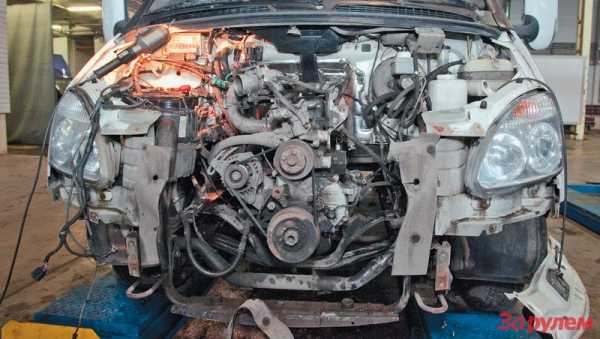
Завершающим этапом совместного проекта журнала «Рейс» и «Группы ГАЗ», который продолжался с августа 2008 года по май 2010 года, по оценке качества и ресурса двигателя УМЗ-4216 стала полная разборка одного из испытуемых двигателей — с наибольшим пробегом в 104 тысячи километров. После разборки двигателя и внешнего осмотра на сервисной станции дилера «Группы ГАЗ» — ООО «Темп- Авто» в подмосковной Балашихе (см. «Рейс» №5–2010 г.) двигатель был отправлен для выяснения остаточного ресурса на Ульяновский моторный завод. Там он был детально осмотрен специалистами, была проведена техническая экспертиза, микрометраж основных деталей. Замеры проведены опытными контролерами Группы метрологии УМЗ под руководством Хализова Н. В. и отражены в картах микрометража по формам ГОСТ 14846.
Результаты замеров систематизированы в табличные формы и проведен анализ размеров сопряжений и зазоров, определяющих в процессе эксплуатации ресурс двигателя до капитального ремонта.
Гильзы цилиндров
Из данных, приведенных в таблице, видно, что износ гильз цилиндров незначительный; фактические размеры не вышли за пределы допуска по конструкторской документации (КД): +48…+60 мкм, группа В. Наибольшие размеры отмечены в 3-м цилиндре: +60 мкм. Овальность и конусность всех гильз незначительная: 5…10 мкм и находится в пределах допуска.
Это подтверждает эффективность внедрения плосковершинного и «мягкого» хонингования гильз цилиндров на двигателях УМЗ-4216 за счет значительного улучшения параметров хонингованной рабочей поверхности гильз по шероховатости и микропрофилю, что обеспечивает оптимальную маслоемкость рабочей поверхности гильзы, позволяет повысить ресурс ЦПГ и снизить расход масла на угар.
Поршень
На поршнях небольшой износ юбки, фактические размеры на 2…4 мкм меньше минимального значения допуска по КД: +12…+24 мкм, группа В. Это подтверждает эффективность перехода к обработке поршней на недавно приобретенных заводом новых полуавтоматах с ЧПУ с установкой оперативной проверки профиля поршня по специальной программе на ПК взамен обработки на токарно-копировальных станках. Это позволило в 2 раза точнее обрабатывать профиль поршня, выполнять масло-удерживающий микропрофиль на юбке, исключить приработочное микропокрытие поршня оловом. Все это в сочетании с изменениями по гильзе повышает ресурс ЦПГ и снижает расход масла на угар.
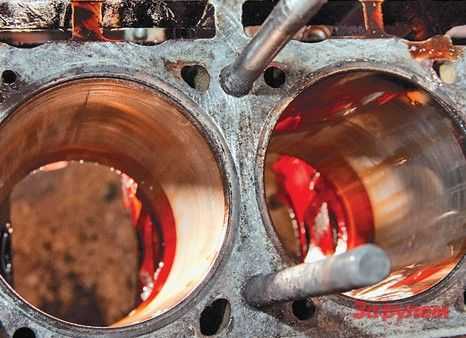
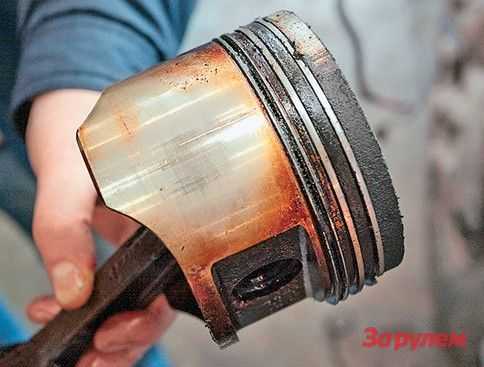
Зазор цилиндр — поршень
Величина зазора в цилиндрах 1, 2 и 4 составила 30…47 мкм и не превышает значения зазора по КД (24…48 мкм). В 3-м цилиндре максимальный зазор 52 мкм, что является незначительным по сравнению с предельно допустимым 300 мкм. Таким образом, исходя из фактического, предельно допустимого зазора и удвоенного темпа износа при дальнейшем увеличении зазора остаточный ресурс ЦПГ будет более чем в 2 раза больше отработанного.
Распредвал
Из данных таблицы видно, что износ опорных шеек распредвала незначительный. Фактические диаметры 1, 3, 4, 5 опорных шеек находятся в пределах допуска по КД (0…20 мкм). На 3-й опорной шейке износ несколько больше, диаметр на 10…12 мкм вышел за пределы допуска по КД.
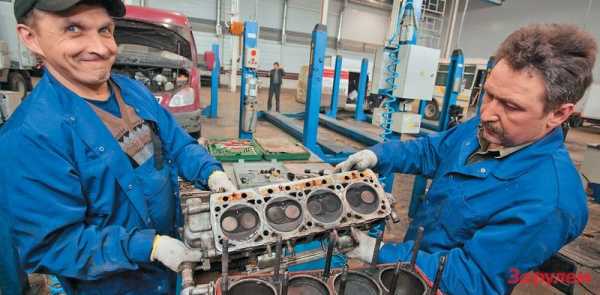
Отверстия в блоке цилиндров
Размеры отверстий в блоке под опоры распредвала находятся в пределах допуска по К Д (40…65 мкм). Наибольшие отклонения отмечены на 1-й опоре (Ø 52 мм) — +55…+60 мкм, что является типичным, поскольку она более нагружена от шестерни привода распредвала. Овальность и конусность всех отверстий незначительная: 5…10 мкм.
Зазор шейка распредвала — отверстие в блоке
Зазор между шейками распредвала и отверстиями в блоке на всех 5-ти опорах находится в пределах допуска по КД (40…85 мкм). Наибольший зазор отмечен на 1-й опоре — 79 мкм. Исходя из фактического, предельно допустимого зазора и практически линейного темпа износа этого сопряжения остаточный ресурс установки распредвала в блоке будет примерно в 2 раза больше отработанного.
Это объясняется отсутствием данных о точных значениях износов в силу отсутствия начального микрометрирования. Поэтому за начальную точку отсчета износа принимается середина допуска, либо одно из его крайних значений — исходя из большей достоверности оценки.
Шатунные шейки коленвала
Разме
www.zr.ru
Места контроля, предельные размеры и способы устранения дефекта
1. Блок цилиндров
1.1. Увеличение некруглости и нецилиндричности гильз блока цилиндров до 0,08–0, 1 мм.
Ремонтировать. Хонинговать диаметры цилиндров под ремонтный размер Æ100,1+0,084/+0,024 мм
1.1.1. Износ диаметров гильз блока цилиндров более чем на 0,1 мм.
Ремонтировать. Расточить и хонинговать диаметры цилиндров под ремонтный размер Æ100,5+0,084/+0,024 мм
1.2. Несоосность опор для коленчатого вала относительно оси коленчатого вала более 0,15 мм.
Браковать блок цилиндров.
1.3. Повреждение резьбовых отверстий в виде забоин или срыва резьбы менее двух ниток.
Ремонтировать. Прогнать резьбу метчиком номинального размера.
1.4. Износ или срыв резьбы резьбовых отверстий более двух ниток.
Ремонтировать.
- Нарезать резьбу увеличенного ремонтного размера.
- Установка резьбовых ввертышей с последующим нарезанием в них резьбы номинального размера или установкой резьбовых спиральных вставок.
1.5. Износ диаметров опор под вкладыши коренных подшипников более 68,5+0,019 мм.
Браковать. Замер диаметров опор под вкладыши коренных подшипников производить на блоке цилиндров, собранном с соответствующими крышками коренных подшипников.
1.6. Пробоины на стенках цилиндров, трещины на верхней плоскости блока и на ребрах, поддерживающих коренные подшипники, пробоины на водяной рубашке и картере. Браковать.
1.7. Износ опор распределительного вала в блоке 0,75 мм. Ремонтировать.
- – Расточить отверстия в блоке под втулки.
55,5+0,018
54,5+0,018
53,5+0,018
52,5+0,018
51,5+0,018
- Запрессовать в блок втулки распределительного вала.
- Расточить втулки, уменьшая диаметр каждой последующей втулки, начиная с 52 мм, на 1 мм. Расточку вести с допуском +0,05/+0,02 мм
2. Поршень
2.1. Износ диаметров поршней менее 99,9 мм.
Ремонтировать. Установить поршни одного из ремонтных размеров: промежуточного ремонтного размера 100,1+0,048/+0,012 мм; первого ремонтного размера 100,5+0,048/+0,012 мм.
2.2. Износ ширины канавки под компрессионное кольцо более 2,1 мм.
Браковать поршень.
2.3. Зазор по высоте между канавкой и кольцом более 0,15 мм.
Браковать поршень.
3. Гильза Цилиндров – поршень
3.1. Зазор между поршнем и цилиндром более 0,30 мм.
Ремонтировать.
Произвести подбор поршня к цилиндру, выдерживая зазор от 0,024 до 0,048 мм между цилиндром и поршнем.
4. Шатун
4.1. Износ диаметра кривошипной головки шатуна более 61,512 мм.
Ремонтировать. Осталить головку шатуна и крышки. Расточить головку совместно с крышкой шатуна в номинальный размер.
4.2. Износ диаметра поршневой головки шатуна более 25,045 мм.
Ремонтировать. Заменить втулку поршневой головки шатуна ремонтной втулкой, запрессовать в шатун. Расточить в номинальный размер.
5. Вал распределительный
5.1. Наличие трещин любого характера и расположения. Браковать.
5.2. Износ кулачков распределительного вала по высоте более чем на 0,5 мм.
Распределительный вал заменить на новый.
5.3. Задиры и глубокие раковины на поверхности опорных шеек и кулачков распределительного вала. Браковать.
6. Коленчатый вал
6.1. Трещины любого характера и расположения. Браковать.
6.2. Повреждения резьбы или срыв резьбы в отверстиях не более двух ниток.
Ремонтировать. Прогнать резьбу метчиком до номинального размера.
6.3. Износ или срыв резьбы в отверстиях более двух ниток.
а) в отверстиях под болты крепления маховика; Ремонтировать установкой резьбовых спиральных вставок.
б) в отверстиях под пробки, в отверстиях под храповик. Ремонтировать нарезанием ремонтной резьбы.
6.4. Износ диаметра коренных шеек менее 63,934 мм. Ремонтировать.
Шлифовать коренные шейки под один из ремонтных размеров:
первый ремонтный 0 63,75–0,013 мм;
второй ремонтный 0 63,50–0,013 мм;
третий ремонтный 0 63,25–0,013 мм;
четвертый ремонтный 0 63,00–0,013 мм;
пятый ремонтный 0 62,75–0,013 мм;
шестой ремонтный 0 63,50–0,013 мм.
6.5. Износ диаметра шатунных шеек менее 57,951 мм. Ремонтировать.
Шлифовать шатунные шейки под один из ремонтных размеров:
первый ремонтный 0 57,75–0,013 мм;
второй ремонтный 0 57,50–0,013 мм;
третий ремонтный 0 57,25–0,013 мм;
четвертый ремонтный 0 57,00–0,013 мм;
пятый ремонтный 0 56,75–0,013 мм;
шестой ремонтный 0 56,50–0,013 мм.
6.6. Биение коренных шеек более 0,02 мм. Браковать.
7. Головка блока цилиндров, клапанный механизм
7.1. Наличие пробоин, прогара и трещина стенках камеры сгорания и разрушение перемычек между гнездами. Браковать головку блока цилиндров
7.2. Износ или срыв резьбы более двух ниток. Ремонтировать.
- Нарезание резьбы увеличенного ремонтного размера.
- Постановка резьбовых ввертышей с последующим нарезанием в них резьбы номинального размера.
7.3. Ослабление посадки втулки клапанов в головке блока цилиндров
Ремонтировать. Установить втулки клапанов одного из ремонтных размеров:
первый ремонтный Æ 17+0,007/+0,04 мм;
второй ремонтный Æ 17,2+0,007/+0,04 мм;
7.4. Коробление тарелки клапана и прогорание клапана и седла клапана.
Ремонтировать
- Седло прошлифовать.
- Клапан заменить на новый.
7.5. Износ диаметра стержня клапана менее 8,925 мм. Ремонтировать.
- Хромировать стержень клапана до Æ 9,1 мм
- Шлифовать стержень клапана в номинальный размер Æ9–0,075 мм.
7.6. Разница между диаметром втулки запрессованной в головку блока цилиндров, и диаметром стержня клапана должна быть не более 0,25 мм.
Ремонтировать.
- Клапан и втулку заменить новыми.
- Фаски седел прошлифовать, центрируя по отверстию во втулке, выдерживая размеры, указанные на рисунке, обеспечивая концентричность фаски на седле клапана с отверстием во втулке в пределах 0,025 мм.
7.7. Износ диаметров отверстий направляющих втулок более 9,022 мм.
Ремонтировать.
- Выпрессовать направляющие втулки.
- Запрессовать новые ремонтные втулки в головку блока цилиндров (см. дефект 6.3). Развернуть отверстия втулок до Æ9+0,022 мм.
gazavtomir.ru
Размеры сопрягаемых деталей двигателя. Инструкция по ремонту двигателей УМЗ-4216 и УМЗ-4213
№ | Сопряженные детали | Размер, мм | Посадка, мм | ||
---|---|---|---|---|---|
Отверстие | Вал | ||||
![]() | |||||
1 | Поршень (канавка) – нижнее компрессионное кольцо | ⌀2,0+0,070+0,050 |
⌀2,0-0,012 |
Зазор 0,082 0,050 |
|
2 | Поршень (канавка) – верхнее компрессионное кольцо | ⌀2,0+0,070+0,050 |
⌀2,0-0,012 |
Зазор 0,082 0,050 |
|
3 | Поршень (канавка) – маслосъемное кольцо чугунное | ⌀5+0,050+0,035 |
⌀5-0,010-0,030 |
Зазор 0,085 0,045 |
|
4 | Гильза цилиндра – юбка поршня, диаметр | Группа А | |||
⌀100+0,036+0,024 |
⌀100-0,012 |
Зазор 0,048 0,024 |
|||
Группа Б | |||||
⌀100+0,048+0,036 |
⌀100+0,12 |
Зазор 0,048 0,024 |
|||
Группа В | |||||
⌀100+0,060+0,048 |
⌀100+0,24+0,12 |
Зазор 0,048 0,024 |
|||
Группа Г | |||||
⌀100+0,072+0,060 |
⌀100+0,036+0,024 |
Зазор 0,048 0,024 |
|||
Группа Д | |||||
⌀100+0,084+0,072 |
⌀100+0,048+0,036 |
Зазор 0,048 0,024 |
|||
![]() | |||||
1 | Шкив коленчатого вала – ступица шкива, диаметр | ⌀57+0,060 |
⌀57-0,60 |
Зазор 0,12 | |
2 | Крышка распределительных шестерен – сальник в сборе, диаметр | ⌀81,5+0,06 |
⌀81,5+0,35+0.20 |
Натяг 0,35 0,14 |
|
3 | Шестерня коленчатого вала -коленчатый вал, диаметр | ⌀40+0,027 |
⌀40+0,025+0,009 |
Зазор 0,018 Натяг 0,025 |
|
4 | Упорная шайба – коленчатый вал, диаметр | ⌀40+0,250+0,080 |
⌀40+0,025+0,009 |
Зазор 0,241 0,055 |
|
5 | Втулка шатуна – поршневой палец (разбиваются на 4 группы, маркировка – краской), диаметр | Белая | |||
⌀25+0,0070+0,0045 |
⌀25-0,0025 |
Зазор 0,0005 0,0045 |
|||
Зелёная | |||||
⌀25+0,0045+0,0020 |
⌀25-0,0025-0,0050 |
То же | |||
Жёлтая | |||||
⌀25+0,0020+0,0005 |
⌀25-0,0050-0,0075 |
То же | |||
Красная | |||||
⌀25+0,0003+0,0030 |
⌀25-0,0075-0,0100 |
То же | |||
6 | Верхняя головка шатуна – втулка шатуна, диаметр | ⌀26,25+0,045 |
⌀26,27+0,145+0,100 |
Натяг 0,145 0,055 |
|
7 | Поршень– поршневой палец (разбиваются на 4 группы), диаметр | I | |||
⌀25-0,0025 |
⌀25-0,0025 |
Зазор 0,0025 Натяг 0,0025 |
|||
II | |||||
⌀25-0,0025-0,0050 |
⌀25-0,0025-0,0050 |
То же | |||
III | |||||
⌀25-0,0050-0,0075 |
⌀25-0,0050-0,0075 |
То же | |||
IV | |||||
⌀25-0,0075-0,0100 |
⌀25-0,0075-0,0100 |
То же | |||
8 | Поршень – стопорное кольцо | ⌀2,2+0,12 |
⌀2±0,03 |
Зазор 0,035 0,017 |
|
9 | Ступица шкива коленчатого вала – шпонка ступицы | ⌀8+0,110+0,080 |
⌀8+0,05 |
Зазор 0,010 0,030 |
|
10 | Коленчатый вал – шпонка ступицы | ⌀8+0,006-0,016 |
⌀8+0,05 |
Зазор 0,0006 Натяг 0,0066 |
|
11 | Коленчатый вал – шпонка шестерни коленчатого вала | ⌀6-0,010-0,055 |
⌀6-0,30 |
Зазор 0,0020 Натяг 0,0055 |
|
12 | Шестерня распределительного вала – шпонка шестерни | ⌀5+0,065+0,015 |
⌀5-0,30 |
Зазор 0,095 0,015 |
|
13 | Коленчатый вал – подшипник первичного вала коробки передач, диаметр | ⌀40-0,0012-0,0028 |
⌀40-0,0011 |
Натяг 0,0028 0,0001 |
|
14 | Маховик – коленчатый вал, диаметр | ⌀80,02+0,30 |
⌀80-0,010-0,029 |
Натяг 0,079 0,030 |
|
15 | Зубчатый венец – маховик, диаметр | ⌀345+0,15 |
⌀345+0,064+0,054 |
Натяг 0,064 0,039 |
|
16 | Коленчатый вал – шатун (осевой размер) |
⌀36+0,1 |
⌀36-0,015-0,020 |
Натяг 0,032 0,015 |
|
17 | Ступица шкива – коленчатый вал, диаметр | ⌀38,05+0,27 |
⌀38+0,020+0,003 |
Натяг 0,074 0,048 |
|
18 | Шатун, вкладыш – коленчатый вал | ⌀61,5+0,012 |
⌀58-0,013 |
Натяг 0,010 0,049 |
|
19 | Блок, коренные вкладыши – коленчатый вал | ⌀68,5+0,019 |
⌀64-0,013 |
Натяг 0,020 0,066 |
|
![]() | |||||
1 | Распределительная шестерня – распределительный вал, диаметр | ⌀28+0,023 |
⌀280,0230,008 |
Зазор 0,015 Натяг 0,023 |
|
2 | Блок цилиндров – 1 опора распределительного вала, диаметр | ⌀52+0,050+0,025 |
⌀52-0,020 |
Зазор 0,070 0,025 |
|
Блок цилиндров – 2 опора распределительного вала, диаметр | ⌀51+0,050+0,025 |
⌀51-0,020 |
То же | ||
Блок цилиндров – 3 опора распределительного вала, диаметр | ⌀50+0,050+0,025 |
⌀50-0,020 |
То же | ||
Блок цилиндров – 4 опора распределительного вала, диаметр | ⌀49+0,050+0,025 |
⌀49-0,020 |
То же | ||
3 | Блок цилиндров – 5 опора распределительного вала, диаметр | ⌀48+0,050+0,025 |
⌀48-0,020 |
То же | |
4 | Распределительный вал (распорная втулка) – упорный фланец | ⌀4,1+0,05 |
⌀4-0,05 |
Зазор 0,020 0,010 |
|
5 | Распределительный вал – шпонка распределительной шестерни | ⌀5-0,010-0,055 |
⌀5-0,030 |
Зазор 0,020 Натяг 0,055 |
|
6 | Распределительная шестерня – шпонка распределительной шестерни | ⌀5+0,065+0,015 |
⌀5-0,030 |
Зазор 0,020 0,055 |
|
![]() | |||||
1 | Втулка – ось коромысел, диаметр | ⌀22+0,020+0,007 |
⌀22-0,14 |
Зазор 0,034 0,007 |
|
2 | Головка блока цилиндров – втулка клапана, диаметр | ⌀16,980,035 |
⌀17+0,066+0,47 |
Натяг 0,086 0,092 |
|
3 | Втулка клапана – впускной клапан, диаметр | ⌀9+-0,022 |
⌀9-0,050-0,075 |
Зазор 0,097 0,050 |
|
Втулка клапана – выпускной клапан, диаметр | ⌀9+-0,022 |
⌀9-0,075-0,095 |
Зазор 0,117 0,075 |
||
4 | Головка блока цилиндров – седло впускного клапана, диаметр | ⌀49+0,027 |
⌀49+0,125+0,100 |
Натяг 0,125 0,073 |
|
Головка блока цилиндров – седло выпускного клапана, диаметр | ⌀42+0,027 |
⌀42+0,125+0,100 |
Натяг 0,125 0,073 |
||
![]() | |||||
1 | Корпус насоса системы охлаждения – подшипник насоса, диаметр | ⌀38+0,008-0,017 |
⌀17-0,009 |
Зазор 0,017 Натяг 0,017 |
|
2 | Ступица шкива вентилятора – вал подшипника насоса, диаметр | ⌀17-0,050-0,077 |
⌀17-0,018 |
||
3 | Ступица крыльчатки насоса – вал подшипника насоса, диаметр | ⌀16-0,033-0,060 |
⌀13-0,018 |
Натяг 0,060 0,015 |
|
1 | Шестерня привода распределителя – валик привода, диаметр | ⌀13+0,002-0,025 |
⌀13-0,011 |
Зазор 0,013 Натяг 0,025 |
|
2 | Блок цилиндров – толкатель (разбивается на 2 группы, маркировка – клеймением цифрами 1 и 2), диаметр | 1 | |||
⌀25+0,023+0,011 |
⌀29-0,008-0,015 |
Зазор 0,038 0,019 |
|||
2 | |||||
⌀25+0,011 |
⌀29-0,015-0,022 |
Зазор 0,033 0,015 |
|||
3 | Блок цилиндров – корпус привода распределителя, диаметр | ⌀29+0,023 |
⌀13-0,020-0,053 |
Зазор 0,086 0,020 |
|
![]() | |||||
1 | Втулка и вал масляного насоса в сборе – штифт, диаметр | ⌀4+-0,037 |
⌀4-0,048 |
Зазор 0,085 Натяг 0,037 |
|
2 | Корпус масляного насоса – шестерня (радиальный зазор), диаметр | ⌀40+0,119+0,080 |
⌀40-0,025-0,075 |
Зазор 0,194 0,055 |
|
3 | Ведомая шестерня масляного насоса – ось шестерни, диаметр | ⌀13-0,022-0,048 |
⌀13-0,064-0,082 |
Зазор 0,060 0,016 |
|
4 | Корпус масляного насоса – ось ведомой шестерни, диаметр | ⌀13-0,098-0,116 |
⌀13-0,064-0,082 |
Натяг 0,034 0,016 |
|
5 | Ведущая шестерня масляного насоса – валик, диаметр | ⌀13-0,022-0,048 |
⌀13-0,012 |
Натяг 0,034 0,016 |
|
6 | Корпус масляного насоса – валик, диаметр | ⌀13-0,043-0,016 |
⌀13-0,012 |
Зазор 0,055 0,016 |
|
7 | Валик масляного насоса (паз) – пластина привода | ⌀4+0,090 |
⌀4-0,070-0,185 |
Зазор 0,275 0,070 |
gazavtomir.ru
УМЗ-4215.10.Сборка шатунно-поршневой группы | AUTOFIZIK.RU / авторемонт
Все детали шатунно-поршневой группы делятся на категории и подбираются индивидуально друг к другу.
ПОСЛЕДОВАТЕЛЬНОСТЬ ДЕЙСТВИЙ
По букве, нанесенной краской на блоке, подбираем поршень к цилиндру.Буквы на блоке и поршне должны совпадать. Римская цифра «||» обозначает требуемую группу поршневого пальца.
Обозначение «421» на поршне указывает на то, что он предназначен для двигателя УМЗ-4215.
При ремонте с расточкой цилиндров требуемые зазоры обеспечиваются в процессе расточки и хонингования под заранее приобретенные поршни одинакового ремонтного размера.
Диаметры отверстий в бобышках поршня, головке шатуна и наружные диаметры поршневого пальца делятся на четыре группы, помеченные краской: I – белой, II – зеленой, III – желтой, IV – красной.
На пальцах номер группы обозначен краской на внутренней поверхности или торцах. Он должен совпадать с группой, указанной на поршне.
На шатуне номер группы обозначается также краской. Он должен либо совпадать, либо быть соседней с пальцем группы.
Смазанный моторным маслом палец должен с небольшим усилием перемещаться в головке шатуна, но не выпадать из нее.
Замки вкладышей должны быть расположены с одной стороны шатуна,…
…а выступ на крышке шатуна совпадать по направлению с надписью «ПЕРЕД» на поршне.
Нагреваем поршень до температуры 60–80 °С. Допускается нагревать поршень в горячей воде. Вводим головку шатуна между бобышками поршня и запрессовываем смазанный моторным маслом поршневой палец.
Если нет приспособления, запрессовать палец можно медным или обычным молотком через оправку из мягкого металла, удерживая поршень на весу.
Поршневой палец фиксируем с обеих сторон стопорными кольцами.
Проверяем поршневые кольца:
поочередно устанавливаем поршневые кольца в цилиндр на глубину 20–30 мм и щупом измеряем зазоры. Компрессионные кольца должны иметь зазор в замке 0,3–0,5 мм, маслосъемные — 0,5–1 мм.
Надеваем кольца на поршень, начиная с маслосъемного кольца.
Раздвинув замок радиального расширителя, надеваем его на поршень в нижнюю канавку.
Аналогично устанавливаем нижний кольцевой диск,…
…осевой расширитель и верхний кольцевой диск.
Кольцевые диски маслосъемного кольца взаимозаменяемые.
Последовательно надеваем два компрессионных кольца, так, чтобы…
…фаска на наружной стороне нижнего компрессионного кольца была обращена в сторону юбки поршня,…
…а фаска с внутренней стороны верхнего компрессионного кольца – к днищу поршня.
www.autofizik.ru
Двигатель УМЗ 4216: характеристики, особенности, тюнинг
Двигатель УМЗ 4216 разрабатывался на Ульяновском моторном заводе. Силовой агрегат разрабатывался на основании ЗМЗ 402, только имеет инжекторную систему впрыска. Изменений особых силовой агрегат не притерпел.
Технические характеристики и описание
Несмотря на высокий расход, двигатель 4216 полюбился многим автомобилистам. Мотор был разработан на базе классической версии движка 421. Основой данного силового агрегата стал ЗМЗ 402. Изменения внесены только незначительные. По большому счёту устройство ДВС осталось неизменным.
Так, в моторе вместо обычной ненадёжной сальниковой набивки установлен сальник коленчатого вала, а вот гидрокомпенсаторы, как на аналогах — не установлены, поэтому приходится регулировать клапана каждые 10 000 км пробега.
Итак, рассмотрим, основные характеристики двигателя УМЗ 4216, а также устройство работы:
Наименование | Описание |
Производитель | УМЗ |
Объем | 2,9 литра (2890 см куб) |
Количество цилиндров | 4 |
Количество клапанов | 8 |
Топливо | Бензин |
Система впрыска | Инжектор |
Мощность | 117 л.с. |
Расход топлива | 10,5 л/100 км |
Диаметр цилиндра | 100 мм |
Порядок работы цилиндров | 1-3-4-2 |
Эконорма | Евро-4 |
Техническое обслуживание
Как правильно проводится обслуживание на двигателе УМЗ 421? Согласно заводских данных и технических карт, распишем, как проводиться ТО для 4216. Техническое обслуживание силового агрегата проводится каждые 10 тыс. км пробега для эксплуатации на бензине, и 8-9 тыс. км — при наличие газовой установки:
- ТО-0. 1000 км: замена масла и масляного фильтра.
- 10000 км: замена масла, маслянного и воздушного фильтра, свечей зажигания, высоковольтных проводов, фильтра тонкой очистки топлива, регулировка зазора клапанов.
- 20000 км: замена масла, масляного фильтра, топливного фильтра.
- 30000 км: замена масла, маслянного и воздушного фильтра, свечей зажигания, высоковольтных проводов, фильтра тонкой очистки топлива.
- 40000 км: замена масла, масляного фильтра, топливного фильтра, замена ремня ГРМ и генератора.
- 50000 км и последующие: замена масла и масляного фильтра. Каждые 20000 км меняется — топливный и воздушный фильтр, регулируются клапана. Каждые 40000 км пробега — замена ремня ГРМ.
Ремонт и основные проблемы
Двигатель УМЗ 4216 и его модификации достаточно легко поддаются ремонту даже в самом худшем техническом состоянии. Так, проводится переборка силового агрегата, головки блока и замена расходных элементов. Сам процесс ремонта проводится поэтапно, как и для любого силового агрегата. Итак, рассмотрим, поэтапный процесс капитального ремонта УМЗ 4216.
Разборка
На данном этапе разбирается ДВС полностью, а именно демонтируется головка блока, снимается поддон и все детали разбираются. Для данного типа моторов процесс дефектовка проводиться в процессе разборки. Сюда не входят только промеры блока цилиндров, опрессовка головки, а также замер коленчатого вала.
Диагностические операции
На данном этапе проводятся работы по определению твёрдости и толщины шеек коленвала, а также его ремонтопригодности. Так, если деталь можно отремонтировать, то определяется размер шеек и изделие отдаётся на последующую обработку. То же самое ждёт и блок цилиндров. Гильзы промеряются, и определяется ремонтный размер поршней.
Опрессовка ГБЦ УМЗ 4216 инжектор — это процесс определения наличия трещин в корпусе. На головке закрываются все отверстия, кроме впускного для охлаждающей жидкости, в которое подаётся горячая вода или керосин. Далее, специалист смотрит, есть ли протеки и трещины. Если нет, то ГБЦ отправляется на ремонт, а если есть — то все дефекты необходимо заварить. Поскольку деталь сделана с алюминия, то применяется аргонная сварка.
В гаражных условиях, для заделывания отверстий в корпусе силового агрегата, автомобилисты пользуются холодной сваркой.
Расточка
Блок цилиндров и коленчатый вал подвергаются расточке. Если цилиндры уже вышли с ремонтного размера, то устанавливаются гильзы стандартного диаметра 100 мм. Для блока цилиндров характерным становиться хонинговка — это один из процессов расточки цилиндров блока при помощи специального станка.
Коленчатый вал растачивается на специальном агрегате, при помощи высоких оборотов и камня, который полирует шейки.
Работы по ГБЦ
Головка блока цилиндров также поддаётся переборке. Так, зачастую меняются клапана, седла, сальники и манжеты. Неоднократно специалистам приходится заменять направляющие втулки клапанов. С развитием современной технологии ремонта, для УМЗ 4216 можно применить гильзовку технологией k-line. Для этого применяются бронзовые втулки размером 11 мм.
На сегодняшний день, достаточно часто встречается замена распределительного вала. Это связано с тем, что двигателям по 20-30 лет и эта деталь уже несколько раз изнашивалась. Поэтому при проведении ремонта ГБЦ на эту деталь стоит обратить особое внимание.
При необходимости рабочая поверхность головки блока шлифуется.
Сборка
Сборочные операции проводятся на специальном стенде. Все детали устанавливаются в той же последовательности, что и разбирались. Так, замене, зачастую, поддаются масляный и водяной насос, устанавливается новый комплект прокладок.
Вывод
Как видно двигатель УМЗ 4216 стал более надёжным, чем его предшественник УМЗ 4213. Обслуживания и ремонт силового агрегата проводится достаточно легко. Капитальный ремонт, лучше всего, проводить в условиях автосервиса.
avtodvigateli.com
МАРКИРОВКА ДВИГАТЕЛЕЙ 4216
содержание .. 1 2 3 4 5 ..
1.1 Идентификационный номер двигателя выбит на специальной площадке с левой стороны блока цилиндров (см. рис. 1).
Рис. 1. Расположение идентификационного номера двигателя 4216 |
Идентификационный номер состоит из двух частей, разделенных звездочкой:
— первая часть – условный код двигателя, принятый в качестве описательной части (VDS), состоящий из шести знаков, где первый три цифры обозначают индекс базовой модели, четвертая – индекс модификации, пятая цифра — климатическое исполнение (при отсутствии пробивается цифра ноль), на шестом месте пробивается цифра ноль или буквы означающие комплекцию двигателя.
— вторая часть – указательная (VIS), состоит из восьми знаков (цифр и букв латинского алфавита), обозначающих номер двигателя, в котором первый знак (буква латинского алфавита или цифра) обозначает год выпуска двигателя, второй и третий знаки – месяц выпуска, последующие знаки – порядковый номер двигателя, выпущенного в текущем месяце.
Для обозначения года выпуска двигателя приняты следующие коды:
2002 г. – 2 |
2006 г. – 6 |
2010 г. – A |
2003 г. – 3 |
2007 г. – 7 |
2011 г. – B |
2004 г. – 4 |
2008 г. – 8 |
2012 г. – C |
2005 г. – 5 |
2009 г. – 9 |
2013 г. – D и т.д. |
Пример маркировки двигателя 4216.1000400-01, изготовленного в мае 2002 года :
. |
4 |
2 |
1 |
6 |
0 |
U |
. |
2 |
0 |
5 |
0 |
9 |
9 |
9 |
9 |
. |
1.2 Двигатель имеет паспорт, маркированный товарным знаком, знаком соответствия, имеет клеймо технического контроля и дату произведенной консервации. В паспорте указан адрес предприятия — изготовителя, а также информация о сроках устранения дефектов, возникших в гарантийный период эксплуатации двигателя.
1.3 Двигатели сертифицированы. Знак соответствия нанесен на крышке коромысел с левой стороны методом аппликации.
1.4 При упаковке двигателей в ящики, на упаковочных ящиках нанесены несмываемой краской следующие данные:
– наименование предприятия- изготовителя;
– товарный знак предприятия-изготовителя;
– обозначение модели двигателя;
– знак соответствия;
– обозначение ТУ на двигатель;
– срок изготовления двигателя, срок и дата консервации;
– предупредительные (манипуляционные) знаки №1, 3, 11 по ГОСТ 14192.
2.1 Требования безопасности
1. При работе с низкозамерзающей жидкостью системы охлаждения двигателя необходимо соблюдать следующие правила:
— избегать любых операций, в результате которых жидкость или ее пары могут попасть в полость рта;
— не давать высохнуть жидкости, попавшей на кожу, а сразу же смыть теплой водой с мылом;
— не допускать проливания жидкости в моторном отсеке автомобиля или в помещении. Облитое место необходимо смыть водой, помещение проветрить;
— облитую одежду перед стиркой высушить вне помещения.
2. Не пользоваться просторной одеждой при обслуживании и регулировании двигателя.
3. Запрещается производить прогрев двигателя в закрытом помещении, не имеющем хорошей вентиляции, во избежание отравления угарным газом.
4. Соблюдать осторожность, открывая пробку расширительного бачка системы охлаждения на горячем двигателе, во избежание ожога паром.
5. Во избежание пожара в моторном отсеке следить за тем, чтобы не было утечек бензина из топливопроводов и шлангов.
6. Не пользоваться открытым пламенем для подогрева масляного картера двигателя при низкой окружающей температуре.
2.2 Предупреждения
1. Для двигателей применяйте бензин автомобильный неэтилированный марок А-92 ТУ 38.001.165. Дублирующие: “Регуляр-91”, “Регуляр-92” ГОСТ Р 51105.
2. В начальный период эксплуатации строго соблюдать все рекомендации изложенные в подразделе «Обкатка».
3. Не допускается работа двигателя, незаправленного охлаждающей жидкостью и маслом.
4. При появлении в работающем двигателе выделяющихся шумов и стуков следует выяснить причину их возникновения и до устранения неисправности автомобиль не эксплуатировать.
5. Перед запуском двигателя убедитесь в отсутствии подтекания ГСМ и охлаждающей жидкости.
6. Необходимо помнить, что система питания двигателя при работающем двигателе находиться под давлением около 3 кгс/см2. Поэтому не допускается производить обслуживание (например, подтягивать соединения) или ремонт узлов системы при работающем двигателе или сразу после его остановки, не сбросив избыточное давление через пробку выпуска воздуха на фильтре тонкой очистки топлива.
7. Не допускается эксплуатация автомобиля без термостата в системе охлаждения, т.к. это приводит к перегреву двигателя.
содержание .. 1 2 3 4 5 ..
zinref.ru