Приспособления для отечественных тяжёлых мотоциклов.
Эксплуатация и ремонт любого мотоцикла, зависит в первую очередь от мастерства водителя, но не только от его умения, а ещё и от инструмента и удобства приспособлений. И разобрать и отремонтировать многие агрегаты (двигатель, КП, задний мост, ходовая и т.д) только с помощью молотка и обычных рожковых ключей если и удастся, то без порчи деталей это дело не пройдёт.
Для грамотного ремонта (без порчи деталей) нужен специальный инструмент и приспособления, с помощью которых при ремонте можно обеспечить точность совмещения деталей и их соосность, требуемое усилие, и т.п., ну и не покалечить самого себя. В этой статье мы рассмотрим несколько приспособлений, которые ощутимо облегчат ремонт отечественных тяжёлых мотоциклов.
Приспособление для сборки колёс.
На рисунке 1 показано полезное приспособление, которое поможет легко собрать колесо мотоцикла (например при замене ступицы, обода или спиц). Основа приспособления это диск, толщиной 35 мм (в средней части чуть толще), который можно выпилить из текстолита или толстой фанеры (фанеру можно использовать тонкую, но склеенную из нескольких слоёв).
Диск для сборки колеса.
1 — струбцина из шпильки (8 шт), 2 — обод колеса, 3 — спица, 4 — ступица, 5 — гайка оси, 6 — шайба или втулка, 7 — пластинчатый выступ упор для обода (8 шт.), 8 — втулка, 9 — ось колеса, 10 — винт упора обода (16 шт.), 11 — гайка струбцины (шпильки).
При работе, колесо (или обод) укладывается на диск (см. рисунок 1,б) и после этого нужно немного наживить (накрутить) спицы. Затем в центральное отверстие диска вставляется втулка колеса 8, и в втулку вставляется ось колеса. Затем на ось надевается шайба 6 и всё скрепляется гайкой 5. Обод 2 притягивается самодельными струбцинами 1 и после этого равномерно затягиваются все спицы.
С помощью этого приспособления, детали колеса (обод, ступица, спицы) изначально, ещё до затяжки спиц, выставляются ровно и точность сборки здесь гарантирована. Да и работу по сборке колеса можно осуществить намного проще и быстрее.
Съёмник для маховика двигателя и корпуса заднего подшипника.
На рисунке 2 показан съёмник для корпуса заднего подшипника и маховика для отечественного оппозитного двигателя (Урал, Днепр, К-750 и т.п.). Этот съёмник поможет снять маховик с конусной части коленвала, а так же позволит стянуть алюминиевый корпус заднего подшипника коленвала. Думаю на чертеже всё понятно, только добавлю, что на штоке лучше сделать упорную резьбу, а не обычную.
А на конце штока желательно установить шарик от подшипника (завальцевать шарик), это позволит штоку легче крутиться при работе и не портить торец коленвала (а точнее болт, вкрученный в торец коленвала). Ещё желательно (при стягивании маховика) вкрутить в торец коленвала болт, который с такой же резьбой как и у болта маховика, но он чуть длиннее. А в центре головки этого болта высверлена ямка для шарика штока съёмника, а затем уже устанавливать сам съёмник, уперев его шток с шариком в ямку в головке болта. Это позволит сохранить резьбу в торце коленвала (при стягивании маховика).
Для стягивания корпуса заднего подшипника, в пластине съёмника сверлятся (по месту) соответствующие отверстия для болтов, которые будут вкручиваться в алюминиевый корпус подшипника.
Приспособление для рассухаривания клапанов.
Рассухариватель клапанов
1 — пластина (90х100), 2 — втулка, 3 — рычаг для нажима на тарелку пружины.
На рисунке 3 показано приспособление для рассухаривания клапанов отечественного оппозита. А на рисунке 4 изображена опора 1 , которая закрепляется со стороны камеры сгорания головки с помощью двух шпилек М8. И упирается опора (в камере сгорания) специальным брусочком в тарелки клапанов, чтобы клапана не открывались при рассухаривании.
Если при изготовлении следовать всем размерам на рисунках 3 и 4, то приспособление встанет на головку чётко и позволит разобрать клапанный механизм легко и просто, без ударов и порчи деталей и рук.
Приспособление для разборки амортизаторов.
На рисунке 5 изображено приспособление для разборки аммортизаторов задней подвески тяжёлого отечественного мотоцикла. Изготовить его несложно, потребуются две длинные шпильки с резьбой М10 (можно и М8), которые можно купить на строительном рынке, а так же нужно будет изготовить два фланца (я использовал готовые от сантехнических задвижек — больших кранов).
На рисунке показаны все размеры под амортизаторы отечественных оппозитов, которые все почти одинаковые. Если внутренний диаметр фланца на 76 мм не подойдёт к стакану вашего амортизатора (бывают разные стаканы), то естественно нужно делать диаметр именно под ваш стакан. Тоже самое и с нижним фланцем (его внутренним диаметром). Гайки для шпилек лучше использовать барашковые, чтобы не возиться с гаечными ключами, так работа пойдёт быстрее. Приспособление поможет легко сжать пружины амортизатора и разобрать (и собрать) его для замены например сальников и доливки масла.
Приспособления, которые улучшат эксплуатацию тяжёлого мотоцикла.
Вставки для передней вилки.
Вставка в переднюю вилку.
1 — шток амортизатора, 2 — контргайка, 3 — удлинитель, 4 — пробка пера вилки.
Бывает, что после длительной эксплуатации или даже длительного простоя мотоцикла в гараже, пружины передней подвески от усталости металла немного проседают и осанка байка нарушается (и уменьшается дорожный просвет). Вилка тяжёлых отечественных мотоциклов итак не длинная, а тут ещё и просадка пружин. Поправить дело помогут специальные вставки для пружин, которые нужно будет заказать токарю, согласно рисунку 6.
Из шестигранника на 13 нужно будет выточить удлинитель 3 (2 штуки), который нужно будет накрутить на шток вилки 1, и законтрить контргайкой 2. А сверху, на шпильку шестигранника навинчивается пробка пера вилки вместе с родной контргайкой. Этими вставками не только восстановится длина перьев вилки, но ещё и сама вилка станет немного жёстче, ведь жёсткости просевших пружин всегда не хватает.
Синхронизатор карбюраторов.
Отрегулировать синхронизацию карбюраторов не так то просто (подробнее о синхронизации читаем вот тут). Устройство, показанное на рисунке 7, поможет одному карбюратору подпитывать другой, если настройка синхронизации чуть расстроилась. Установка этого устройства к тому же сделает работу оппозитного мотора более мягкой, устойчивой, и позволит немного сократить расход топлива. Главные жиклеры штатных карбюраторов с маркировкой 210, можно будет заменить на жиклеры с маркировкой 185, которые имеют чуть меньшую пропускную способность.
Это позволит чуть обеднить топливную смесь, что вместе с электронным зажиганием, (о котором читаем здесь) позволит сократить расход топлива (особенно на средних оборотах), не снижая мощности двигателя. Да и запуск двигателя заметно улучшится, особенно в прохладную погоду.
Устройство состоит из двух шайб, сделанных из дюраля или латуни (бронзы) установленных между головками цилиндров и карбюраторами. В шайбы следует вкрутить на эпоксидном клее (или холодной сварке) штуцеры, изготовленные из медных или латунных трубок, диаметром 8 — 9 мм. Шайбы устанавливаем на каждую головку перед карбюратором (между карбюратором и впускным фланцем), с прокладками из паронита и затем на штуцеры шайб одеваем бензостойкий резиновый шланг, соединяя штуцеры обеих шайб между собой с помощью этого шланга и хомутиков (шланг проводим под двигателем).
Теперь, если какой то карбюратор будет испытывать недостаток топлива, он будет подпитываться горючей смесью от второго карбюратора и перебои на любых режимах исключены. Шайбы можно изготовить не как на чертеже круглыми, а подточить их по форме фланца карбюратора и впускного патрубка, и отполировать кромки фланца, что я и сделал на своём мотоцикле. Ну а если потребуется синхронизация карбюраторов с помощью вакуумометров, то с штуцеров нужно будет снять соединяющий их шланг и подсоединить к ним шланги от вакуумометров.
Надеюсь, что несложные приспособления описанные в этой статье, помогут владельцам тяжёлых отечественных мотоциклов, быстрей, легче и без порчи деталей произвести ремонт байка и хоть немного улучшить его эксплуатационные характеристики; успехов всем.
Теги: Полезные мелочи для отечественных тяжёлых мотоциклов., Приспособления для ремонта отечественных тяжёлых мотоциклов.
Съемник пружин в подвеске автомобиля своими руками. Установка для разборки сборки амортизационных стоек легковых автомобилей Стенд для разборки стоек амортизаторов чертеж
Одной из основных процедур при ремонте передней подвески является замена стоек. Это относится к автомобилям с подвеской Макферсон, когда стойка собрана. То есть стойка представляет собой амортизатор, пружину и опору с чашкой. Все это закреплено гайкой, которая накручена на стержень амортизатора. В итоге стойка находится в постоянной «боевой готовности», когда на сжатие работает пружина, а на растяжение амортизатор.
Но в этой статье мы хотим рассказать не о работе стоек, а о том, как трудно порой приходится автолюбителям при снятии пружины. Все дело в том, что пружина на стойке довольно мощная, а значит усилие ее сжатие очень большое. В итоге, при раскручивании гайки на штоке пружина может «стрельнуть», что может привести к травме. Да к тому же еще и при обратной сборке встанет вопрос о том, как же собрать стойку обратно, то есть сжать пружину. В помощь автолюбителям в этом случае предлагаются в основном всевозможные съемники пружин. Обычно это система шпилек с крючками или шайбами. В итоге стягивание пружин происходит за счет скручивания гайки по шпильке. Этот способ снятия пружиня вполне жизненный, однако и имеет свои недостатки. Основным из которых является большое время на закручивание раскручивание гаек по шпильке. В этой статье мы хотели бы вам предложить другую альтернативу, прекрасно справляющуюся с этой задачей, при этом требующую от механика гораздо меньших усилий.
Приспособление для быстрой разборки стоек, замены (сжатия) пружины на них в гараже своими руками
Принцип работы этого приспособления основан на увеличении крутящего момента за счет изменения плеча приложения силы. Можно сказать классическое решение для большинства случаев в механике. Так точками опоры будет стена, к которой консолью приделано плечо и стойка вернее пружина. Здесь усилия прилагаемые на стойку будут зависеть от длины рычага плеча. Фактически это ручки нашего приспособления. На них можно просто присесть и человеческого веса вполне хватит для того, чтобы сжать пружину. Взгляните на рисунок.
А теперь по порядку, как будет происходит замена, снятие пружины со стойки. Первоначально необходимо развести плечи приспособления и установить на чашку над пружиной. Далее сводим плечи между собой фиксируем, например отрезком трубы.
Дале просто садимся на трубу и тем самым сдавливаем пружину. Усилие на пружину можно регулировать собственным телом, садясь на рычаге чуть дальше или ближе к стойке. Откручиваем гайку, удерживающую поворотную опору и чашку пружины.
Аккуратно встаем, тем самым снимая напряжение сжатия на самой пружине, которая еще установлена на стойке. После распрямления пружины снимаем ее со стойки.
Установку и сжатие новой пружины производим в обратной последовательности.
Резюмируя о съемнике пружин…
Необходимо сказать о том, что применение подобного приспособления оправдано особенно в тех случаях, когда замена пружины на стойках подобного типа происходит часто. В основном это автосервисы. Также надо заметить, что приспособление универсально. На нем можно демонтировать пружины со стоек любых авто, фактически меняя высоту плеча, которым поджимается пружина. Работы связанные со снятием и заменой пружины при применении такого приспособления будут значительно упрощены, что пожалуй является определяющим фактором при решении вопроса о изготовлении чего-то подобного в вашем гараже.
Самостоятельно и не боится испачкать свои руки. Также данное приспособление будет удобно для фиксирования различных труб для их обработки или сварки.
Для того, чтобы сделать приспособление для разборки стоек подвески своими руками, понадобится:
* Углошлифовальная машинка, отрезной круг, зачистная металлическая щетка
* Токарный станок по металлу
* Сверлильный станок, сверло по металлу 10 мм
* Металлический уголок 25 мм
* Ручные тиски
* Штангенциркуль
* Карандаш, рулетка
* Дрель или шуруповерт
* Швеллер 200 мм
* Шпилька М12 и длиная гайка к ней
* Профильная труба 20*20 мм
* Сварочный аппарат, электроды
* Защитные очки, сварочная маска, краги, наушники
* Тиски
* Пластиковая заглушка для профильной трубы
* Баллончик молотковой краски
Шаг первый.
Для начала нужно зачистить заготовку от ржавчины, с этой задачей отлично справляется углошлифовальная машинка с зачистной металлической щеткой.
При работе с углошлифовальной машинкой будьте осторожны, одевайте защитные очки, перчатки, а также наушники.
Так как для этой самоделки понадобится шинка, то ее сделаем из уголка размером 63 мм. При помощи штангенциркуля делаем разметку на металлическом уголке, шинка должна быть шириной 25 мм.
Далее начинаем отпиливать нужную часть от уголка при помощи УШМ с установленным в нее отрезным кругом. После отпиливания получаем две таких заготовки шириной 25 мм.
От шинок отмеряем 200 мм и отрезаем при помощи углошлифовальной машинки четыре одинаковых заготовки.
Их края желательно немного зашлифовать, чтобы не пораниться.
Шаг второй.
Далее устанавливаем кернер на край, отступив около 10 мм и делаем небольшое углубление.
После этого фиксируем заготовку в тисках и при помощи сверлильного станка делаем два отверстия по краям диаметром 10 мм. В процессе сверления периодически добавляем техническое масло, так сверло будет меньше нагружаться, а значит дольше держать заточку режущей кромки.
От уголка размером 25 мм отрезаем две заготовки длиной 50 мм при помощи углошлифовальной машинки.
При необходимости этот размер можно увеличить.
Шаг третий.
Просверленные по краям шинки делим ровно пополам.
Устанавливаем на среднюю линию ранее отрезанный кусок уголка и при помощи него делаем разметку.
Далее по разметке отпиливаем ненужную часть при помощи УШМ, закрепив шинку в тисках, после чего примеряем 25-ый уголок.
Затем из куска 200-го швеллера отрезаем полоску шириной 25 мм и длиной 140 мм, воспользовавшись углошлифовальной машинкой. В итоге получается заготовка толщиной 9 мм, что вполне достаточно для жесткой конструкции.
На этой заготовке размечаем пять точек под будущие отверстия на одинаковом расстоянии. После чего делаем кернение и просверливаем отверстия диаметром 10 мм на сверлильном станке, закрепив деталь в ручных тисках.
В итоге должна получится такая деталь с пятью отверстиями.
Шаг четвертый.
Все детали практически готовы, нужно сделать шайбу на токарном станке по металлу, которую просто вытачиваем из металлического прута необходимого диаметра. Также изготавливаем пруток со сквозным отверстием, на замену которого можно взять обычную трубу нужного диаметра. Затем к нему нужно приварить длинную гайку. Основанием для закрепления в тисках будет профильная труба размером 20*20 мм.
Шаг пятый.
Теперь проделываем сварочные работы. При помощи болтов и ручных тисков собираем конструкцию из шинок. К ней привариваем уголок в специальный пропил, сделанный заранее. При работе со сварочным аппаратом будьте аккуратны, а также используйте средства индивидуальной защиты, такие как сварочная маска и краги.
После сварки получается такая деталь.
Шлак удаляем при помощи молоточка, после чего сварочный шов зачищаем металлической щеткой, установленной в дрель или шуруповерт. Их нам нужно сделать две, аналогичные действия производим с другой заготовкой. К одной из таких деталей с уголком привариваем профильную трубу строго посередине.
Целью проекта было создание приспособления для монтажа и демонтажа пружин подвески легковых автомобилей, иными словами стяжки для пружин. Приспособление должно удовлетворять многим требованиям. Оно должно применяется для пружин разных типов т.е. пружин различной высоты, различного диаметра, жесткости. Оно должно быть простым в использовании и обслуживании. Соответствовать требованиям по технике безопасности и отличатся высокой надежностью.
Для работы с приспособлением требуется минимум квалификации. Для того что бы демонтировать пружину с телескопической стойки легкового автомобиля нужно следующее: во-первых конечно же снять с автомобиля саму телескопическую стойку, далее необходимо подать воздух в пневмоцилиндр для развода захватов приспособления на требуемое расстояние друг от друга, т.
Основной частью устройства является пневмоцилиндр. В верхней части (на штоке пневмоцилиндра) крепится захват, на котором установлены крючки для зацепления витков пружины и крепится на штоке пневмоцилиндра гайкой. Непосредственно на верхней части пневмоцилиндра крепится нижний захват, в который вставляются два упора для зацепления стойки.
Сам же нижний захват собран из следующих составных частей: кронштейн, в который вставляются две лапки, в которые, после вставляются два упора. Раздвигаются лапки при помощи винта на котором нарезана правая и левая резьба, а в самих лапках запрессованы втулки с соответствующей резьбой.
Детали разработки
Детали разработки
Детали разработки
6.1 Обзор существующих приспособлений для разборки амортизационной стойки
6.2 Описание проектируемого приспособления для монтажа и демонтажа пружин
6.3 Расчёт проекта
6.3.1 Расчёт требуемого диаметра пневмоцилиндра
6.3.2 Расчёт прочности стяжной шпильки
6.3.3 Расчёт цилиндра на прочность
6.3.4 Расчёт винта крепления крючкового захвата на срез
6.3.5 Проверочный расчёт лапки верхнего захвата на изгиб
6.3.6 Проверочный расчёт лапки нижнего захвата на изгиб
6.3.7 Проверочный расчёт нижнего упора на изгиб
6.4 Расчёт себестоимости изготовления устройства
6.4.1 Полная заработная плата производственных рабочих, занятых на сборке
6.4.2 Дополнительная заработная плата сборки
6.4.3 Общепроизводственные накладные расходы на изготовление
6. 4.4 Расчёт показателей экономической эффективности
Пояснительная записка 21 лист описания и расчетов, спецификации.
При ремонте или настройке подвески автомобиля, возникает необходимость зафиксировать пружину в определенном положении.
Для этих работ есть сервисное приспособление: съемник пружин, с помощью которого можно снять элементы ходовой как в специализированной мастерской, так и в гаражных условиях.
Различные концепции инструмента:
Рассмотрим второй вариант подробнее.
Как работает съемник пружин, и какими они бывают?
Для чего нужен съемник? Он преодолевает распрямляющее усилие пружин. Прилагаемая сила на кронштейнах съемника соизмерима с весом автомобиля, но это не означает, что его конструкция слишком дорогая и высокотехнологичная.
Существует множество вариантов, но они подразделяются всего на два вида: механический и гидравлический привод.
Механический съемник пружин
Чаще всего имеет резьбовой приводной механизм.

Технология следующая: два съемника симметрично надеваются на стойку. Проворачивая шпильку с резьбой, вы сводите захваты к середине пружины прямо на амортизаторе, сжимая ее до необходимого размера.
Важно: Почему механический съемник нельзя применять поодиночке? При сжатии, пружина выгибается, контролировать этот процесс невозможно.
Установка одного съемника на пружину приведет к его поломке
Съемники, надетые с двух сторон, обеспечивают равномерное сжатие. При работе с подвеской грузовых автомобилей или тяжелых внедорожников, опытные мастера устанавливают по 3 или даже 4 съемника.
Правильная установка съемников на пружину
Полустационарные стойки
На сервисных станциях часто используют полустационарные стойки для снятия пружин со стоек амортизаторов.
Инструмент достаточно универсальный, подходит к большинству подвесок. Благодаря редуктору приводного механизма, работать с ним удобно и безопасно.
Единственный недостаток – не всегда можно сжать пружину прямо на автомобиле. Все-таки это стендовое устройство: съемник работает с подвеской, снятой с автомобиля.
Популярное: Струбцина своими руками облегчает работу мастеру и экономит его деньги
Рычажного типа
Аналогичная «проблема» у съемников рычажного типа. Механизм надежный и безопасный, но его габариты не позволяют подлезть в пространство под крылом авто.
Гидравлический съемник
Может быть переносным и стационарным. Работает по принципу домкрата: есть главный и рабочий цилиндр. Прокачивая жидкость с помощью рукоятки-рычага, оператор сжимает силовые скобы, между которыми находится пружина.
Компактный двухсекционный съемник может стать помощником и в домашнем гараже, а вот напольный стационарный станок подойдет лишь для автосервиса.
Давление в гидравлической системе нагнетается ножным рычагом. При этом руки автослесаря свободны, работать удобно и безопасно.
Разумеется, есть съемники с компрессорами, электроприводом, и прочими приспособлениями, облегчающими жизнь при обслуживании автомобиля. Всё это хорошо, пока вы не увидите ценник.
Порой выгоднее несколько раз посетить автосервис, чем приобрести промышленный съемник для личного пользования. Какой выход? Делать инструмент своими руками.
Изготовление съемника пружин амортизаторов
Многие автолюбители пользуются обычной цепью: наматывают несколько оборотов вокруг витков пружины, и затягивают цепь. После подъема автомобиля домкратом, амортизационная стойка растягивается, а пружина остается сжатой. Это опасный способ: если цепь соскользнет, распрямившаяся пружина может нанести серьезную травму.
Как сделать простейший съемник по аналогии с промышленным
Механический полустационарный «станок» можно создать из «Волговского» домкрата.
Используемые материалы:
Дрель, болгарка, напильник, сварочный аппарат – такой набор либо есть в гараже, либо доступен у соседа за пару пива. К верхней части домкрата (где расположена вертушка с редуктором) собирается площадка из уголка. Затем к ней приваривается кронштейн по размеру опорной чашки.
К штатному опорному рычагу домкрата прикручиваем шатун, в него будет заходить стойка амортизатора.
Не нужно беспокоиться за прочность конструкции. Домкрат поднимает автомобиль, шатун также выдерживает огромную нагрузку. А для усиления консольной конструкции кронштейна, привариваем тяги из штоков амортизатора.
Съемник универсален: длина амортизатора позволяет обслуживать любые стойки для легковых автомобилей, а также большинство внедорожников.
Следующий съемник пружин, который легко сделать своими руками – стягивающего типа. Подойдет для небольших размеров пружин, поскольку развить на таком приспособлении большое усилие – нереально.
Комплектующие еще более доступные, чем в предыдущей конструкции. Кусок трубы, уголок и длинный болт М14 – М18. Можно использовать шпильку.
Из уголка и распиленных кусочков дюймовой трубы свариваем кронштейны. Съемник состоит из двух одинаковых стяжек, так что кронштейнов должно быть четыре.
Обязательно ввариваем направляющие втулки для шпильки. Иначе при затяжке кронштейны будут подклинивать.
Пружина стягивается при синхронном закручивании гаек на шпильках. Если вы пользуетесь набором из 2-х стяжек – устанавливать их следует строго симметрично.
Эксплуатация и ремонт любого мотоцикла, зависит в первую очередь от мастерства водителя, но не только от его умения, а ещё и от инструмента и удобства приспособлений. И разобрать и отремонтировать многие агрегаты (двигатель, КП, задний мост, ходовая и т.д) только с помощью молотка и обычных рожковых ключей если и удастся, то без порчи деталей это дело не пройдёт.
Для грамотного ремонта (без порчи деталей) нужен специальный инструмент и приспособления, с помощью которых при ремонте можно обеспечить точность совмещения деталей и их соосность, требуемое усилие, и т.п., ну и не покалечить самого себя. В этой статье мы рассмотрим несколько приспособлений, которые ощутимо облегчат ремонт отечественных тяжёлых мотоциклов.
Приспособление для сборки колёс.
На рисунке 1 показано полезное приспособление, которое поможет легко собрать колесо мотоцикла (например при замене ступицы, обода или спиц). Основа приспособления это диск, толщиной 35 мм (в средней части чуть толще), который можно выпилить из текстолита или толстой фанеры (фанеру можно использовать тонкую, но склеенную из нескольких слоёв).
1 — струбцина из шпильки (8 шт), 2 — обод колеса, 3 — спица, 4 — ступица, 5 — гайка оси, 6 — шайба или втулка, 7 — пластинчатый выступ упор для обода (8 шт.), 8 — втулка, 9 — ось колеса, 10 — винт упора обода (16 шт.), 11 — гайка струбцины (шпильки).
При работе, колесо (или обод) укладывается на диск (см. рисунок 1,б) и после этого нужно немного наживить (накрутить) спицы. Затем в центральное отверстие диска вставляется втулка колеса 8, и в втулку вставляется ось колеса. Затем на ось надевается шайба 6 и всё скрепляется гайкой 5. Обод 2 притягивается самодельными струбцинами 1 и после этого равномерно затягиваются все спицы.
С помощью этого приспособления, детали колеса (обод, ступица, спицы) изначально, ещё до затяжки спиц, выставляются ровно и точность сборки здесь гарантирована. Да и работу по сборке колеса можно осуществить намного проще и быстрее.
Более удобный и универсальный стапель для сборки мотоциклетных колёс, можно сделать как показано в видеоролике чуть ниже, но для такой конструкции потребуется приобрести патрон от токарного станка.
Но у кого что-то не получится при сборке, и колесо после сборки станет кривым, то его не сложно подравнять подтяжкой соответствующих спиц. Очень подробно я об этом написал в статье «Как выровнять деформированное колесо мотоцикла» — статья находится .
Съёмник для маховика двигателя и корпуса заднего подшипника.
Рассухариватель клапанов
1 — пластина (90х100), 2 — втулка, 3 — рычаг для нажима на тарелку пружины.
На рисунке 3 показано приспособление для рассухаривания клапанов отечественного оппозита. А на рисунке 4 изображена опора 1 , которая закрепляется со стороны камеры сгорания головки с помощью двух шпилек М8. И упирается опора (в камере сгорания) специальным брусочком в тарелки клапанов, чтобы клапана не открывались при рассухаривании.
1 — шток амортизатора, 2 — контргайка, 3 — удлинитель, 4 — пробка пера вилки.
Бывает, что после длительной эксплуатации или даже длительного простоя мотоцикла в гараже, пружины передней подвески от усталости металла немного проседают и осанка байка нарушается (и уменьшается дорожный просвет). Вилка тяжёлых отечественных мотоциклов итак не длинная, а тут ещё и просадка пружин. Поправить дело помогут специальные вставки для пружин, которые нужно будет заказать токарю, согласно рисунку 6.
Из шестигранника на 13 нужно будет выточить удлинитель 3 (2 штуки), который нужно будет накрутить на шток вилки 1, и законтрить контргайкой 2. А сверху, на шпильку шестигранника навинчивается пробка пера вилки вместе с родной контргайкой. Этими вставками не только восстановится длина перьев вилки, но ещё и сама вилка станет немного жёстче, ведь жёсткости просевших пружин всегда не хватает.
Синхронизатор карбюраторов.
Отрегулировать синхронизацию карбюраторов не так то просто (подробнее о синхронизации читаем ). Устройство, показанное на рисунке 7, поможет одному карбюратору подпитывать другой, если настройка синхронизации чуть расстроилась. Установка этого устройства к тому же сделает работу оппозитного мотора более мягкой, устойчивой, и позволит немного сократить расход топлива. Главные жиклеры штатных карбюраторов с маркировкой 210, можно будет заменить на жиклеры с маркировкой 185, которые имеют чуть меньшую пропускную способность.
Это позволит чуть обеднить топливную смесь, что вместе с электронным зажиганием, (о котором ) позволит сократить расход топлива (особенно на средних оборотах), не снижая мощности двигателя. Да и запуск двигателя заметно улучшится, особенно в прохладную погоду.
Устройство состоит из двух шайб, сделанных из дюраля или латуни (бронзы) установленных между головками цилиндров и карбюраторами. В шайбы следует вкрутить на эпоксидном клее (или холодной сварке) штуцеры, изготовленные из медных или латунных трубок, диаметром 8 — 9 мм. Шайбы устанавливаем на каждую головку перед карбюратором (между карбюратором и впускным фланцем), с прокладками из паронита и затем на штуцеры шайб одеваем бензостойкий резиновый шланг, соединяя штуцеры обеих шайб между собой с помощью этого шланга и хомутиков (шланг проводим под двигателем).
Теперь, если какой то карбюратор будет испытывать недостаток топлива, он будет подпитываться горючей смесью от второго карбюратора и перебои на любых режимах исключены. Шайбы можно изготовить не как на чертеже круглыми, а подточить их по форме фланца карбюратора и впускного патрубка, и отполировать кромки фланца, что я и сделал на своём мотоцикле. Ну а если потребуется синхронизация карбюраторов с помощью вакуумометров, то с штуцеров нужно будет снять соединяющий их шланг и подсоединить к ним шланги от вакуумометров.
Надеюсь, что несложные приспособления описанные в этой статье, помогут владельцам тяжёлых отечественных мотоциклов, быстрей, легче и без порчи деталей произвести ремонт байка и хоть немного улучшить его эксплуатационные характеристики; успехов всем.
Обзор системы осушки газа| Kimray
Система осушки газа используется производителями нефти и газа для осушки природного газа до состояния, при котором его можно продавать ниже по течению. В этом видео мы проследим за трубами вокруг системы осушки газа и объясним, что делает каждая часть оборудования для обработки газа.
Вход в систему осушки газа
Вход в типовую сборную станцию предназначен для нескольких разных скважин. После прохождения магистрали, пробкоуловителя и коллектора газ проходит через компрессоры.
После того, как газ был сжат, он поступает из нагнетания компрессора в опору контактора.
Трехвентильный коллектор
Расположенный в основании башни контактора трехвентильный коллектор, включающий впускной газовый клапан, перепускной клапан и выпускной газовый клапан.
При запуске системы осушки газа все три клапана открыты. Это позволяет газу обходить градирню, но также позволяет газу из трубопровода повышать давление в градирне.
После того, как вся процедура запуска будет завершена, перепускной клапан будет медленно закрываться, вытесняя весь газ из компрессоров в нижнюю часть башни контактора.
Башня контактора
Башня контактора гликоля иногда называется абсорбционной башней. Внутри башни находятся лотки, расположенные на расстоянии примерно 18 дюймов друг от друга, обозначенные снаружи очистными отверстиями. Эти корпуса можно снять, чтобы очистить лотки от мусора.
Манометры температуры и давления
Для расчета размера гликолевого насоса необходимы три параметра: температура, давление и расход. Температура газа, необходимая для этого расчета, находится на контакторной башне.
На башне на видео температура газа 82 градуса. Манометр показывает, что он работает примерно при 760 фунтах.
Производитель может предоставить данные о расходе или получить его от счетчика в точке продажи.
Контроллер уровня жидкости и клапан сброса
В основании башни контактора находится контроллер уровня жидкости, клапан сброса и смотровое стекло. Эти компоненты помогают предотвратить контакт свободной воды, конденсата или загрязнений с триэтиленгликолем или ТЭГ в градирне.
В эту башню встроен скруббер, но в некоторых местах может быть отдельный сепаратор до того, как он попадет в башню контактора.
Газоотвод на линию счетчика
После осушки газа в градирне газ поступает в измерительную ветвь для измерения и отправки за пределы площадки для дальнейшей обработки.
Ребойлер системы осушки газа
Перед запуском установки осушки мы смотрим на уровень гликоля, отображаемый в смотровом стекле ребойлера. После того, как мы убедились, что ребойлер заполнен гликолем, мы зажгли горелку.
Ребойлер на видео выглядит как единый сосуд, но на самом деле состоит из двух частей — ребойлера и расширительного бака. Имеется перегородка, которая гарантирует, что уровень гликоля покроет жаровую трубу. Затем регенерированный гликоль перетекает через эту перегородку в расширительный бачок.
Термостат отключения при высокой температуре и термостат, управляющий основной горелкой, настроены на соответствующие настройки.
Внутри узла горелки или пламегасителя находится стоящая пилотная и основная горелка. После того, как горелка зажжется, ТЭГ в ребойлере начнет нагреваться до 375 градусов, прежде чем мы начнем циркулировать гликоль.
Газ из башни контактора также поступает в блок котла для обеспечения приборного газа для термостата и регулирующих клапанов, а также для привода насоса и обеспечения циркуляции триэтиленгликоля.
Вкратце об этом процессе:
- перепускной клапан открыт, чтобы позволить газу обходить опору контактора
- выпускное отверстие градирни открыто, поэтому давление во всей градирне выравнивается
- горелка зажжена и ребойлер прогрет до температуры
- Итак, пришло время начать циркуляцию гликоля
Уравнительный резервуар
На некоторых объектах осушки газа уравнительный резервуар является частью ребойлера.
ТЭГ выходит из расширительного бачка под углом 375 градусов и, как видно здесь, сжег краску на трубопроводе. Бедный или сухой гликоль выходит из расширительного бака и проходит через значительное количество трубопроводов, связанных с теплообменниками.
Y-образный сетчатый фильтр
Y-образный сетчатый фильтр — это простое, но важное устройство, которое блокирует ржавчину или частицы, которые могли попасть из повторного бойлера перед попаданием в насос.
Гликолевый насос для осушки газа
Бедный гликоль поступает на всасывание насоса через Y-образный сетчатый фильтр. Бедный гликоль проходит через внутренние механизмы насоса и попадает в выпускной блок насоса.
Это правильный звук работы 450-энергетического обменного гликолевого насоса. Звучит приглушенно — нет металлического звука.
Обратный клапан
После прохождения бедного гликоля через насос он проходит через обратный клапан, который установлен для уменьшения износа насоса. Обратный клапан может заклинить и быть ограниченным ржавчиной, поэтому время от времени это хорошее место для устранения неполадок.
Осушка газа: от обедненного до обогащенного гликоля
Отощенный гликоль направляется по подземной трубе к опоре контактора. Естественное охлаждение, которое обеспечивает земля, действует как теплообмен и охлаждает гликоль еще больше, прежде чем он попадет в градирню.
Вход обедненного гликоля в градирню идет вверх по теплообменнику газ-гликоль. Затем он поступает в верхнюю часть колонны и сбрасывает гликоль вниз через серию тарелок.
Когда газ поднимается вверх через нижнюю часть градирни, а гликоль стекает из верхней части градирни.
Газ поднимается вверх через колпачки, что вынуждает его контактировать с гликолем, текущим вниз. Газ отдает воду и становится более сухим по мере того, как он проходит через каждую последующую тарелку, чтобы соответствовать критериям трубопровода, когда он выходит из верхней части башни.
Водяной пар в газе поглощается ТЭГ, а тощий гликоль затем насыщается водой, становясь «богатым» или влажным гликолем, где он выходит из нижней части колонны и возвращается в ребойлер для регенерации.
После того, как влажный гликоль покидает градирню, он проходит через канистру фильтра перед подачей в гликолевый насос. Этот фильтр имеет решающее значение для снижения износа гликолевого насоса и предотвращения засорения теплообменника, и его необходимо регулярно очищать или заменять.
Поступая в насос, этот насыщенный гликоль проходит через внутренние механизмы и помогает поршням перемещаться вперед и назад.
Насыщенный гликоль выходит из насоса и в месте на видео испытывает падение давления с 750-фунтового рабочего давления до атмосферного. Он проходит по трубе и начинает использоваться в системе теплообмена гликоль-гликоль.
Система теплообмена гликоль-гликоль
Система теплообмена гликоль-гликоль работает, потому что перепад давления создает перепад температуры. Этот перепад температуры затем действует как охлаждающий агент.
Когда холодный гликоль проходит по трубе, теплый сухой гликоль выходит из расширительного бачка снаружи трубы. Влажное и сухое никогда не вступают в прямой контакт друг с другом. Охлаждающий эффект, вызванный движением двух температур гликоля, охлаждает гликоль, когда он проходит через систему.
Богатый продукт выходит с другого конца теплообменника и попадает в сепаратор.
Сепаратор мгновенного испарения
Трехфазный сепаратор мгновенного испарения отделяет насыщенный гликоль от загрязнений, смазочного масла, свободной воды и конденсата. Загрязненные жидкости выходят и перемещаются в резервуар для хранения.
Испарительная колонна
Гликоль выходит из этой системы на вход дистилляционной колонны. Испарительная колонна представляет собой насадочную колонну, которая позволяет насыщенному гликолю стекать через нее.
Этот гликоль, богатый водой, достигает 375-градусного гликоля. Вода, которая кипит при температуре 212 градусов по Фаренгейту, испаряется в виде пара. Пар возвращается через дистилляционную колонну, но гликоль задерживается и сбрасывается обратно в ребойлер.
Затем гликоль проходит через ребойлер и снова начинает свой путь несколько раз в день. Как правило, гликоля хватает на 18–24 месяца, прежде чем его нужно будет заменить.
BTEX
Очень важной функцией безопасности системы осушки газа является BTEX.
Пар из дистилляционной колонны поступает в систему удаления BTEX (бензол, толуол, этилбензол и ксилол) , используемую для улавливания и рециркуляции BTEX и ЛОС (летучие органические соединения) .
Загрязненный пар конденсируется обратно в жидкость, собирается и отправляется на хранение, а остаточные пары летучих органических соединений направляются в горелку для сжигания.
Чтобы поговорить со специалистом о вашей системе осушки газа, обратитесь в местный магазин Kimray или к авторизованному дистрибьютору.
Дегидратор гликоля | Exterran
Гликолевые дегидраторы, часть систем осушки природного газа, удаляют водяной пар из газовых потоков, чтобы предотвратить образование гидратов и коррозию в трубопроводах.
Установка осушки гликоля — это надежная и эффективная система для удаления воды из потоков природного газа в соответствии с типичными спецификациями трубопроводов и технологических процессов. Несколько этапов демонтажа объединены в один блок, смонтированный на салазках, что дает вам широкий спектр возможностей и гибкость для настройки системы в соответствии с вашими конкретными задачами.
скрытый текст в пробел из-за странностей js
Ключевые преимущества
- Ускоренные производственные чертежи доступны уже через 4-5 рабочих дней для более быстрого планирования конструкция салазок и приверженность обслуживанию помогают быстро перевести операции в режим онлайн
- экономичное техническое обслуживание
- установка и ввод в эксплуатацию агрегатов для облегчения и ускорения запуска
- Лучшая в отрасли поставка для быстрого запуска
Как это работает
Влажный газ поступает в нижнюю часть колонны абсорбера и поднимается через экстрактор тумана, где удаляются мелкие жидкие частицы. По мере того, как газ поднимается через насадочные или колпачковые тарелки градирни, вода поглощается нисходящим бедным гликолем (вода, удаляемая в процессе регенерации), которая постоянно перекачивается наверх градирни. Осушающий газ выходит из верхней части колонны и проходит через гликоль/газовый теплообменник к выпускному отверстию для газа. Насыщенный гликоль (смоченный абсорбированным гликолем) собирается в поддоне в нижней части градирни и поступает на сторону питания гликолевого насоса. От насоса насыщенный гликоль проходит через змеевик флегмы, теплообменник и сепаратор мгновенно выделяющегося газа, который отделяет газ и уносимые углеводороды от гликоля. Затем газ поступает в скруббер топливного газа, а обедненный гликоль проходит через фильтр в ребойлер. По мере того как ребойлер отводит водяной пар через дистилляционную колонну, горячий реконцентрированный гликоль поступает из ребойлера в барботер для удаления дополнительного количества водяного пара. Бедный гликоль поступает в отсек для хранения, а затем в теплообменник для охлаждения. Охлажденный обедненный гликоль затем проходит через носовой гликолевый фильтр, прежде чем попасть в гликолевый насос. Бедный гликоль и газ из абсорбера вместе приводят в действие гликолевый насос, который перекачивает гликоль через теплообменник гликоль/газ для минимизации потерь гликоля, а затем в колонну абсорбера для продолжения цикла процесса обезвоживания.
Стандартные функции и опции
Регенератор
- Энергосберегающая теплоизоляция с алюминиевым кожухом
- Съемная жаровая труба и дымовая труба
- Термостат с защитной гильзой
- Термометр 50-550°F с защитной гильзой для топлива
- 2
- 2 -off с ручным сбросом
- Регулятор топливного газа, скруббер и манометры
- Пламегаситель с горелкой и запальником в сборе
- Встроенный изолированный отсек для хранения
- Датчик уровня жидкости в сборе
- Гликолевый фильтр с начальными элементами
- Гликолевый сетчатый фильтр высокого давления
- Внешний гликоль/гликолевый теплообменник
- Клапаны для выпуска воздуха из насоса )
- Прочная сварная опора из конструкционной стали с подъемными проушинами и тяговыми стержнями
- Набивная успокоительная колонна с обратным змеевиком (все установки мощностью более 125 МБТЕ/ч)
- Полный трубопровод для подсоединения установки, включая абсорбер и запорные клапаны ребойлера для агрегатов до 500 МБТЕ/ч
- Изогнутые трубки и приварные враструб гликолевые трубы и клапаны для труб диаметром один дюйм и более для предотвращения утечек
Абсорбер
- Распределитель гликоля
- Расчетное давление 1440 фунтов на кв.
теплообменник
- циферблатный термометр 0–200 °F с защитной гильзой
- манометр с запорным клапаном
- пневматический регулятор уровня жидкости
- термопредохранительный клапан
- Столевой клапан
- Сборка рефлекторного измельчения стеклянной стеклянной сборки с измельчающими петухами
- Подъемные бурунки
- Случайный упакованный поглотитель
- .
- Возможность работы с более горячим газом
- Диапазон регулирования 10:1
- Эквивалентная вместимость 10 тарелок
- Диаметры от 24 до 60 дюймов
- 8 поднос с пузырчатой крышки
- 5: 1 ОБНОВЛЕНИЕ
- Размеры диаметром от 16 до 72 дюймов
Поглотитель лотка
Полный гликол дегидационный блок
- 80
Полный гликол дегидационный блок
- 80
Полный гликол дегидрирующий блок
- 8080
Полный гликол дегидационный блок
- 808080
.
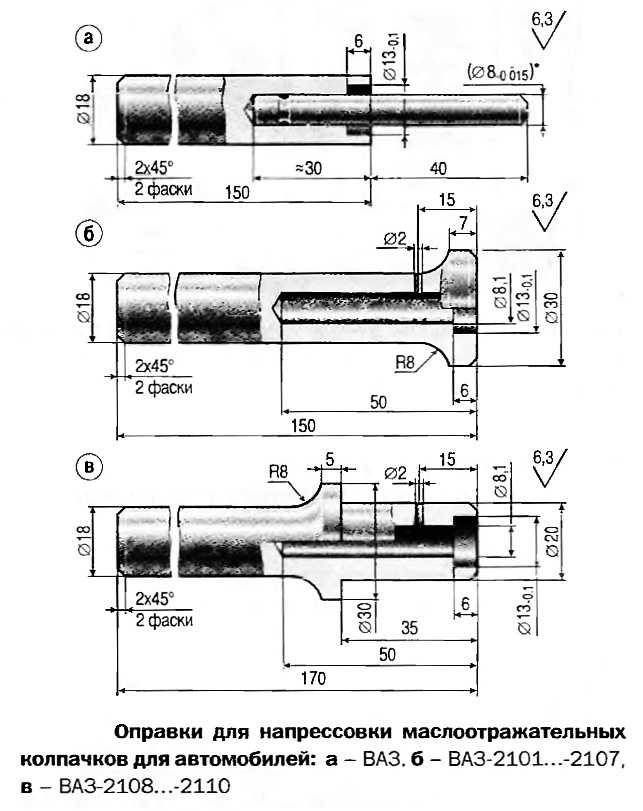