Форсунки промышленные для воды EUSPRAY IKEUCHI BEX
Компания B4S предлагает нашим клиентам производственные решения в сфере распыления различных производителей, в том числе обладая собственной маркой пластиковых форсунок B4S для моечных машин, процессов подготовки поверхности, фосфатации, камер дождевания и др. Вы можете купить промышленные форсунки в нашей компании европейского качества по доступным ценам. Товар полностью растамаживаем и отгружаем клиенту на склад очищенный от таможенных платежей. Доставка по России и Беларуси бесплатно.
В компании B4S накоплен огромный опыт при сотрудничестве с нашими партнерами из Германии, Польши, Австрии, Чехии, Венгрии, Словакии, Беларуси, Украины и других европейских странах. Нашими клиентами являются как производственные предприятия по всей Европе, так и производители различного оборудования для широкого спектра производственных процессов.
Собственное производство пластиковых шарнирных форсунок для подготовки поверхности перед покраской, фосфатации, машин мойки тары , любой автоматической мойки.
Полный спектр распылителей для рещшения любых производственных задач:
Промышленные форсунки для любого использования
- Форсунки для металлургической промышленности
- Форсунки для пара
Форсунки B4S пластиковые собственного производства для мойки, машин мойки тары (таромоечных машин), агрегата химической подготовки поверхности (АХПП), процессов фосфатации.
Применяются в
- агрегаты подготовки поверхности перед покраской
- мойка
- мойка тары
- процесс фосфатации
- производстве кузовов автомобилей
- производстве бытовой техники, стиральных машин, холодильников…
- производстве шкафов для щитового оборудования (НКУ)
Форсунки для воды и моющие головки IKEUCHI
Головки моющие Форсунки туманообразующие Форсунки
Японский производитель форсунок для распыления жидкостей и систем создания тумана и увлажнения, IKEUCHI (ИКЕУЧИ) занимается разработкой и производством высокоточных продуктов для распыления для применения в различных отраслях промышленности.
Единственная в мире компания, обладающая технологией изготовления керамических вставок в сопла форсунок, что позволяет значительно увеличить срок эксплуатации изделий и реже менять запасные части в производственном оборудовании и экономить как на частоте закупок форсунок, так и уменьшить затраты на работу персонала и время пуска-наладки оборудования.
С момента своего основания в 1954 году поддерживает глобальные требования к промышленным распылительным соплам и распылению с помощью инновационных продуктов, увеличивая ценность для клиентов за счет технической поддержки распыления. У компании есть представительства по всему миру, открывающие офисы в 8 странах. А через нашу глобальную сеть наши представители готовы помочь с техническими характеристиками продуктов, конструкциями систем, проблемами приложений, размещением заказов…
IKEUCHI стремится предоставлять решения, основанные на наших обширных знаниях технологии распыления.
Постоянные инвестиции в исследования, разработку продуктов и производство являются основой нашего бизнеса.
Продукты компании, прецизионные сопла и связанные с ними системы предназначены для обеспечения высочайшего качества и наилучших результатов для наших клиентов. Инженерные решения
Высокоточные системы распылительных форсунок IKEUCHI и системы увлажнения Dry Fog удовлетворяют требованиям распыления и удовлетворяют любые производственные потребности.
Отдел исследований и разработок постоянно совершенствует и обновляет продукты и системы для адаптации к потребностям клиентов. Мы постоянно развиваем наши основные технологии и расширяем наши знания, полученные из широкого спектра отраслей, в области, где мы видим спрос.
Чтобы предложить наилучший выбор форсунок, мы можем рассчитать правильные условия распыления и смоделировать расположение форсунок.
Для проектных решений может быть предоставлена техническая помощь представителя компании в Европе и России.
Форсунки и моечные головки, самоочищающиеся фильтры EUSPRAY
Отличное качество по приемлемым ценам.
Распылительные форсунки, аксессуары, статические и вращающиеся моющие головки, а также промышленные самоочищающиеся фильтры производятся по самым высоким стандартам и предлагаются по адекватным ценам.
Компания EUSPRAY была создана в 2008 году, производство открылось в 1970-х годах.
Ее дочерняя компания, специализирующаяся на производстве продуктов, имеет более 37 лет технического опыта в разработке и производстве распылительных насадок, принадлежностей и фильтров, используемых в обрабатывающей и перерабатывающей промышленности по всему миру.
Более тридцати пяти лет опыта и простой и эффективной организации символизирует компанию. EUSPRAY со штаб-квартирой в Барселоне, Испания и специализированной производственной базой распылительных форсунок и систем фильтрации в Тревильо, Италия, идеально подходит для предоставления услуг, продуктов и конкурентоспособных цен, требуемых сегодня.
По факту на складах компании как в Варшаве, так и в Бресте всегда есть самое востребованные позиции товара для наших потребителей.
Накопленный опыт как инженеров EUSPRAY в Италии, так и инженеров B4S в Польше, Беларуси и России позволяет подобрать оптимальное решение как по качеству предоставляемой продукции, так и по ценовой политике.
Форсунки промышленные CBN
Форсунки полноконусные
Небольшая, по мировым меркам, семейная компания из Италии, берущая свое начало с 1963 года.
При этом производящая очень качественные продукты по приемлемым ценам, в сравнении с гигантами рынка, такие как Spraying Systems, PNR, Elpis и др.
При этом они не всегда абсолютно полностью могут совпадать с артикулами данных компаний. Но это не значит, что они качественно хуже. Тем белее чем меньше производитель, тем приятнее с ним работать, так как такие компании более качественно подходят к обслуживанию клиентов.
Форсунки могут быть выполнены из различных материалов.
Сталь таких марок как:
- AISI 303, AISI 304, AISI 310,
- AISI 316, AISI 316L, AISI 420, AISI 430, AISI 430F.
Латунь: CW614N, никелированная латунь
Пластик: PVC. PP, POM, PTFE, Nylon, ABS.
Сплавы на никелевой основе:
- Hastelloy®,
- Inconel®,
- Incoloy®
Титан и другие материалы по запросу.
Форсунки и эдукторы BEX
Форсунки для воздуха Эдукторы
BEX обладает более чем 50-летним опытом производства распылительных форсунок и эдукторов. Собственный опыт проектирования и производства удовлетворяет потребности промышленных применений для клиентов по всему миру.
Компания BEX существует с 1963 года, когда Норм Боуэн представил свои эдукторы на выставке.
В 1963 году Норм Боуэн управлял небольшим механическим цехом, когда клиент обратился к нему с проблемой. Клиент нуждался в конкретном распылительном сопле и не смог его найти. Будучи недавним выпускником инженерного факультета, Боуэн был заинтересован сложностью создания такого продукта. Он с усердием принял задание и изготовил свой первый эдуктор. Покупатель был в восторге не только от готового продукта, но и от скорости, с которой Норм производил его. Теперь, спустя более 50 лет, сын Норма, Дерек Боуэн, продолжает семейный бизнес и традицию разработки и производства качественных продуктов в настоящее время.
BEX расширился в Соединенных Штатах и Европе с офисами продаж в Анн-Арборе, Мичиган и Виллих, Германия. Продукты производятся в Онтарио и отправляются клиентам по всему миру.
Таким образом, опираясь на собственный и опыт наших проиводителей, компания B4S может предложить свои решения по распылению, мойке, сдуву, сушке для любых производственных задач, равным или лучше покачеству, чем лидеры рынка в данный момент, но при этом ниже по цене.
Некоторые наши продукты превосходят другие предлодения по качеству технологического производства. Такие как тангенциальные форсунки полного и полого конуса CBN, имеющие металлическую вставку из стали 316 SS. А также форсунки плоскоструйные и полного конуса IKEUCHI, имеющие керамические вставки, что позвяляет эксплуатировать их дольше, чем форсунки других производителей
Наше преимущество по сравнению с другими компаниями — это цена ниже при аналогичном качестве, а также полное соответствие продуктов (полные аналоги) компании BEX, так как BEX находится в Канаде и все стандарты соответствуют американским.
Полный спектр форсунок для воды в компании Б4С! Свяжитесь с нами любым удобным способом!
Форсунка |
Распылитель |
ТНВД |
Потребитель двигателя |
Кол. μf, Pфо, ход игл |
33,1112010-03 (сетчатый фильтр) |
33.1112110-12 øиг.=6мм, Vk=2mm3 |
33-02 |
КамАЗ 740.13-180 (EURO-0) |
4×0.30 0,185…0.205, I 223+6, 0,25….0,30 |
33,1112010-11 (сетчатый фильтр) |
33.1112110-12 øиг.=6мм, \/к=2мм3 |
335 |
КамАЗ 7409. (EURO-0) |
4 х 0.30 0.185…0.205, 253+6, 0,25…0,30 |
271.1112010-02 (сетчатый фильтр) |
271.1112110-01 øиг,=6мм, Vk=2mm3 |
33-10, 334 |
КамАЗ 7403.10 (EURО-0)_ |
4×0.32 0.215…0.235, 238+6, 0.25…0.3C |
272. |
272.1112110 øиг.=6мм, \/к=2мм3 |
332-30 |
КамАЗ 7408.10 (EURО-0) |
4×0.33 0.220…0,240, 223+6, 0,25….0,30 |
273.1112010-20 (щелевой фильтр) |
273.1112110-20 øиг.=6мм, \/к=0,6 |
337-20.01, 337-20.02, 337-20.03, 337-20.04,
337-42 (форс. 337-70, -71,-71,01, -71.02
|
КамАЗ 740.52-260, 740.53-290, 740.51-320, 740.50-360 (EURO-2)
|
5×0,33 0.250,..0.270, 244+6, 0,33…0,38 |
273.1112010-50 (щелевой фильтр) |
OLLA 148 S1380 øиг.=6мм, Vk=0,6 |
|||
273. |
273.1112110-30 øиг.=6мм Vk=0,6mm3 |
337-10, 337-40, -40.01,-40.02, -40.03, 337-50.01,-50.02, 337-30,02, 337-42.01, -42.04, -42.05,-42.06, -42.07,-42.08 336-20, 336-21 |
КамАЗ 740.11-240, 740.12-210, 740,02-180, 740.22-240, 740,18-240, 740.03-135, 740.15-160, 740.16-180, 740.17-240, 740.54-300, 740.57-275 (EURO-1) |
5×0.35 0,270…0,290,
244+6, 0,33. |
274.1112010 (щелевой фильтр) |
335,1112110 øиг.=4.5мм, Vk=0,6 |
337-20 и модификации (в перспективе), 337-21 и модификации (в перспективе) |
КамАЗ 740.30-260, 740.50-360, 740.51-320, 740.52-260, 740.53-290, 740,13-260 (EURO-2) |
5×0.31 0.250…0.270, 254+6, 0,30….0,5 |
51.1112010-01 форсунка ЯЗТА |
335.1112110-60 øиг.=4,5мм, Vk=0,6 |
насосы ЯЗТА (компакт- 40) |
ЯМЗ-7511
С ИНДИВИД. (EURO-2) |
6 х 0,29 0.240.,.0.260, 276+6, 0,30….0,35 |
333.1112010-10 (сетчатый фильтр+ втулка) |
273,1112110-100 øиг.=6мм, \/к=0,6мм3
|
насосы ЯЗТА (60.5, 80.5) |
ЯМЗ-236 и модификации ЯМЗ-238 и модификации (EURO-1)
|
4×0,36
0. 233+6, 0,33….. 0,38
|
333.1112010-50 (щелевой фильтр) |
323-20, 337-90 |
|||
267.1112010-02 форсунка ЯЗТА
|
335.1112110-50 øиг.=4,5мм Vk=0,6 mm3 |
насосы ЯЗТА (компакт-40), 323, 323-10,337, 337-01 |
ЯМЗ-7511 с общей гол. ЯМЗ-236НЕ, -236БЕ ЯМЗ-238DЕ (ЕURО-1) |
5×0. 0.240…0.260, 276+6, 0.30…0.35 |
267.1112010-10 форсунка ЯЗТА |
335.1112110-70 øиг,=4.5мм, Vk=0,6 |
324, 324-10, 337-02, 337-03 |
ЯМЗ-236НЕ2, -236БЕ2, 236НЕ2-3, 238DE2 (ЕURО-1) __ |
5×0,285 0,210…0.230, 276+6, 0,30…0,35 |
455.1112010 (щелевой фильтр) |
335. |
773-01, -02,-03,-04,-04Э, 773-08 363-40.01, -40.02,-40.04, -40,05,-40.09, -40.11,-40.14 776, 776-01 366 и мод. |
ММЗ Типа D-245.C, D-260,1 (EURO-1) |
5 х 0.345 0.270,..0,290, 254+6, 0,30…0,35 |
455.1112010-50 (щелевой фильтр) |
335.1112110-120 øиг.=4.5мм, Vk=0,6 |
773-20. 773.11-40.02, -40.09, -40.10; 773.1100-40.02, -40.09, -40,10 363-41.04, -41,05, -41.06, -41.07,-41.07Э 363-41.07Т 773-01 Т,-07Т,-16Т |
ММЗ Типа D-245.7E2, D-260.5E2, D-260.9C2 (EURO-2) |
5×0.31 0.230..,0.260, 254+6, 0,30,..0,35 |
455.1112010-60 (щелевой фильтр) |
335. |
363-41.1 ОТ, 363-41.16Т |
ММЗ D-260.10C2, D-260.16C2 (EURO-2)_ |
5×0.33 0.290…0.310, 254<6, 0,30…0,35 |
Распылители форсунки — устройство и назначение
Распылители форсунки – это механические устройства, предназначенные для распыления топлива в инжекторных и дизельных системах. Подача бензина или солярки при этом осуществляется под высоким давлением. Что примечательно, на бензиновых двигателях распыление производит под давлением 3-5 атмосфер, в то время как на дизельных впрыск осуществляется при 1000-1200 атм.
Для чего она нужна?
Данная деталь выполняет сразу несколько функций в системе подачи топлива. Во-первых, она дозирует нужное количество впрыскиваемого бензина. Во-вторых, распылитель форсунки (КАМАЗ-5460 в том числе) выполняют функцию управления и приготовления струи топлива. И в-третьих, данное устройство отделяет систему впрыска от самой камеры сгорания двигателя.
Зачастую современные распылители дизельных форсунок состоят из одного-двух каналов (сопел), по которым топливо подается на выход и в дальнейшем распыляется в камеру сгорания. Качественная деталь должна обеспечивать ровное конусообразное распыление жидкости.
Разновидности
На данный момент существует лишь два типа механизмов:
- Штифтовые устройства.
- Многоструйные (бесштифтовые).
В первом случае штифтовые распылители форсунки применяются в механизмах вихре- и предкамерных дизельных двигателей. Многоструйными устройствами укомплектовываются чаще всего автомобили, имеющие непосредственный впрыск топлива, в том числе на машинах с системами «Коммон Райл». Оба механизма имеют свои особенности конструкции, однако их принцип работы и главная функция от этого не меняется.
Алгоритм работы
Когда распылители форсунки находятся в открытом положении, жидкость впрыскивается в камеру сгорания. От ее количества и качества подачи зависит очень много факторов, начиная от мощности двигателя и заканчивая расходом топлива. Если распыление происходит неправильно, автомобиль начинает дымить, терять динамику и при этом потреблять большее количество горючего. Происходит постоянная закоксовка форсунки, что может привести к полному выходу ее из строя. Герметичность устройства, находящегося в закрытом состоянии, обеспечивает плотная посадка наконечника иглы в седло корпуса распылителя. Когда распылители форсунки находятся в закрытом положении, данная игла удерживается специальной пружиной, которая действует от запорного конуса стороны устройства. Также стоит отметить, что в системах впрыска «Коммон Райл» вместо пружины применяется давление самой горючей жидкости.
Прежде чем топливо попадет в камеру сгорания, оно нагнетается в форсунку, после чего проходит по специальным каналам вовнутрь распылителя (о них мы говорили в начале статьи). Постепенно топливо нагнетается в данное устройство, вследствие чего в системе образуется давление. Как только его значение достигнет необходимой величины, пружина иглы распылителя открывается и начинается процесс впрыска топлива в цилиндр. При этом стержень открывшегося устройства ходит внутри направляющего канала в корпусе форсунки.
Распылители LECHLER | Агроипорт
Выберите категориюВсе Диски, стойки, <br>лапки OFAS » Диски » Стойки » Лапки » Запчасти Lemken » Колёса прикатывающие Распылители <br>LECHLER Защита растений,<br>внесение удобрений,<br>запасные части » Опрыскиватели » Разбрасыватели удобрений » Карданные валы »» Карданные валы »» Вилки / Муфты »» Крестовины »» Переходники / Профили » Насосы UDOR » Шланги » Корпуса распылителей Косилки измельчители,<br>фрезы почвенные » Фрезы почвенные Техника » Обработка почвы »» Глубокорыхлители »» Пружинные бороны » Овощеводство »» Для лука »» Для картофеля »» Для овощей » Заготовка сена »» Косилки ротационные »» Пресс-подборщики Метизы » DIN 603 Болт с полукруглой головкой » DIN 608 Болт с потайной головкой и квадратный подголовник » DIN 931 Шестигранный болт, не полная резьба » DIN 933 Шестигранный болт, полная резьба » Гайки, шайбы, стремена, гроверы Гидравлические <br>компоненты
Форсунки
Проверка работоспособности. Форсунки снимают с дизеля для ремонта с помощью выжимных приспособлений. Чтобы предотвратить попадание грязи в форсунку и повреждение сопел, на штуцера и распылитель надевают защитные колпачки и транспортируют форсунки в таре. Перед транспортировкой проверяют наличие уплотнительных по газовому стыку медных прокладок и состояние посадочных мест в стакане крышки цилиндра или адаптере гильзы. Перед испытаниями корпуса форсунок погружают на 15-30 мин в ванну с дизельным топливом, промывают, а при необходимости и очищают волосяными щетками закоксованные наружные части соплового наконечника и накидной гайки. При этом следует следить за тем, чтобы грязное топливо не попало во внутренние топливоподводящие каналы форсунки.
Работоспособность форсунок проверяют на стенде типа А106. После подсоединения форсунки включают промывочный аккумулятор и делают несколько промывочных впрыскиваний. При этом визуально контролируют истечение топлива из всех сопловых отверстий. Закоксованные сопловые отверстия, а также отверстия, дающие сужение струи топлива или уменьшение ее длины, прочищают латунной или стальной проволокой, зажатой в цанговую оправку (рис. 33). Диаметр проволоки должен быть на 0,02 — 0,05 мм меньше номинального диаметра сопловых отверстий.
Очищенные и промытые форсунки подвергают контрольным испытаниям, проверяя: качество распыливания топлива с контролем давления начала и окончания впрыскивания; герметичность запирающего конуса; герметичность форсунки в соединениях и плотность распылителя по прецизионной части. Методика испытаний должна соответствовать требованиям ГОСТ 10579-75 и ГОСТ 9928-71.
Качество распыливания проверяют прокачкой профильтрованного дизельного топлива через форсунку, отрегулированную на номинальное давление начала впрыскивания при частоте качания рычага стенда 30 — 60 в 1 мин. Качество распыливания должно отвечать следующим требованиям: распыленное топливо, выходящее из распылителя форсунки, должно быть туманообразным, без заметных на глаз отдельных капель, сплошных струек и легко различимых местных сгущений; перед началом контрольного впрыскивания, а также после его окончания подтекание топлива через сопловые отверстия не допускается; по окончании впрыскивания допускается увлажнение носика распылителя; впрыскивание топлива должно быть четким и сопровождаться характерным звуком. Для объективности оценки качественных показателей отбирают эталонные форсунки и распылители.
Допуск на номинальное значение давления начала впрыскивания не должен превы
шать 4 %. Давление окончания впрыскивания (перепад давления за период впрыскивания) регламентируется заводами-изготови-телями топливной аппаратуры. Перепад давления зависит как от конструкции форсунки, так и от условий испытаний (акку>-мулирующего объема стенда, скорости нарастания давления). Заводы уделяют большое внимание контролю оптимального значения перепада давления, так как оно характеризует качество изготовления и идентичность геометрических и гидравлических параметров проточной конусной части распылителя. Для эксплуатируемых распылителей отклонение перепада давления от оптимального значения может характеризовать дополнительно и износ запирающего конуса распылителя, ширину притирочного пояска, герметичность конусного уплотнения.
Герметичность распылителя по запирающему конусу проверяют созданием в форсунке давления топлива на 1 — 1,5 МПа меньше, чем давление начала впрыскивания, при этом в течение 20 с на носике распылителя (соплового наконечника) не должно наблюдаться подтекания топлива, допускается увлажнение носика без видимого объема просочившегося топлива. Герметичность запирающего конуса характеризует качество его изготовления (круг-лость, шероховатость образующих) и состояние (износ, выкрашивание, забоины) уплотнительного пояска в месте контакта конусов корпуса и иглы распылителя. Невыполнение требований по герметичности приводит к повышенному закоксовыванию сопловых отверстий и постепенному выходу из строя форсунки. Герметичность уплотнений рабочей полости форсунки проверяют статическим или динамическим (на обкаточном стенде) повышением давления на значение, превышающее на 10 — 20% максимальное рабочее давление. Течь и увлажнение топливом мест уплотнения не допускаются. Герметичность сливных каналов и внутренних полостей форсунок контролируется опрессовкой дизельным топливом давлением 0,5 МПа. Падение давления в течение 1 мин не допускается.
Гидравлическая плотность форсунки определяется временем падения давления опрессовки с 34,3 до 29,4 МПа в системе стенда с объемом 65 см3 через прецизионный зазор цилиндрического уплотнения распылителя при вязкости опрессовоч-ной жидкости 9,9-10,9 мм2/с. По ряду технологических соображений, при оценке в депо плотности распылителей, параметры испытаний могут отличаться от стандартных. Так, начальное давление опрессовки для сохранения регулировки форсунки при контрольных проверках берется обычно ниже регулируемого давления начала впрыскивания, опрессовку можно выполнять на дизельном топливе и при различных объемах системы стенда. В этом случае допускается проверка плотности распылителей сравнением их с эталонными распылителями, имеющими минимальные и максимальные допустимые зазоры в прецизионной части. Плотность контролируемой форсунки (распылителя) должна находиться в пределах плотности эталонных распылителей, аттестованных
Рис. 33. Цанговое приспособление для прочистки распиливающих отверстий:
1 — цанга; 2 — проволока в соответствии со стандартными условиями.
В технических требованиях заводов-из-готовителей также в отдельных случаях используются отличные от стандартных методы испытаний плотности и требования к опрессовочным стендам. Кроме того, при оценке герметичности запирающего конуса введены некоторые уточняющие браковочные признаки. Так, по техническим требованиям для распылителей форсунок дизелей типов Д49, Д40 при подъеме давления на аккумуляторном стенде с механическим приводом на 1 — 1,5 МПа меньше, чем давление подъема иглы, в течение 60 с не должно наблюдаться отрыва капли
Таблица 7
Давление | Опти маль- | Учи ты- | ||||||
Тип дизеля | Место испытаний | Требования и тип стенда | начала впрыски вания, | ный перепад давле- | Вязкость опрессо-вочной смеси | падение давле- | Допус тимая плот- | Браковочная плотность, с |
МПа | ния, МПа | МПа | ность, с | |||||
ДЮ0 | На заводе | По ГОСТ 9928-71 | 20,6 +0,9 | 4-6 | 9,9 — 10,9 мм2/с | 35-30 | 500-60 | — |
В депо | Стенд А106 | 1,53-1,55 °Е** | 33-28 | 100-5 | Менее 5 | |||
Д50 | На заводе | По ГОСТ 9928-71 | 27 ±0,5 | 4-6 | 9,9-10,9 мм2/с | 35-30 | 190-80 | |
В депо | Стенд А106* | 1,53-1,55 °Е** | 38-33 | 30-7 | 4 | |||
На заводе | Стенд без аккуму- | 31,4 + 0,5 | 10-13 | 1,5-1,6 °Е*** | 30-25 | 50-25 | ||
11Д45, | лятора (топливо- | |||||||
14Д40 | провод: /т = 1200 мм, <4„ = 2,8 мм) | |||||||
В депо | Стенд А106* | 1,18-12,8 °Е*** | 25-20 | 34-1,5 | Менее 0,5 | |||
На заводе | Стенд без аккумулятора (топливо- | 31,4+0,5 | 9-12 | 1,18- 1,20 °Е*** | 30-25 | 13-7 | — | |
5Д49 | провод: /т= 1200 мм, <4„ = 2,8 мм) | |||||||
В депо | Стенд А106* | 1,18 -1,20 °Е*** | 25-20 | 13-5 | Менее 5 | |||
М756 | На заводе | ПоГОСТ 9928-71 | 19,6 + 0,3 | 2-5 | 9,9-10,9 мм2/с | 35-30 | 80-60 | _ |
М753 | В депо | Стенд А106 | 1,18- 1,28 °Е** | 35-30 | 14-4 | 1 |
* С дополнительным объемом Уак = 50 см3 при оценке качества впрыскивания. ** При 20 °С.
*** При 50 °С
топлива от носика сопла. Однако при арбитражной проверке применяются только стандартные методики испытаний, и все форсунки (распылители) должны полностью соответствовать требованиям ГОСТ 10579-75 и ГОСТ 9928-71. Некоторые технические требования к форсункам отечественных дизелей по техническим условиям заводов и деповским правилам ремонта приведены в табл. 7.
Корпусные и непрецизионные детали форсунок. Форсунки, не отвечающие техническим требованиям при контрольных испытаниях, а также проработавшие более 100 тыс. км (ТР-2, ТР-3), полностью разбирают.
Корпусные и непрецизионные детали форсунок проходят промывку в моечной машине типа А328 с последующей просушкой в продувочных камерах. В отдельных случаях сильно загоревшие закок-сованные детали предварительно очищают в ванночках со специальными растворами. Детали, имеющие трещины, волосовины, сколы уплотнительной или опорной поверхности глубиной более 0,5 мм, сорванные нитки резьбы, выбраковывают. Конусные поверхности, уплотняющие ниппеля трубок высокого давления и штуцера фильтров при наличии рисок и забоин проверяют зенковкой с последующей зачисткой шкуркой или притиром с пастой М14, М20. При этом отклонение от номинала восстановленного угла конуса не должно превышать ±40′, а уплотнительная поверхность конуса иметь шероховатость не выше Кц = 2,5 мкм и биение относительно резьбы не более 0,2 мм. При износе или вытягивании резьбы в штуцерах разрешается восстанавливать профиль резьбы с помощью раздвижных плашек. Уменьшение среднего диаметра резьбы не должно превышать 1 мм, что контролируется спе-
Рис. 34. Приспособление для притирки торца форсунки:
1 — планшайба; 2 — корпус форсунки; 3 — притирочная плита циальным ремонтным резьбовым калибром.
Особое внимание должно быть уделено восстановлению плоскостности и шероховатости торцовой поверхности корпусов форсунок, обеспечивающих уплотнение с корпусом распылителя. При незначительных завалах, неглубоких (0;05 — 0,07 мм) рисках, следах коррозии плоскостность уплотнительной поверхности торца корпуса форсунки восстанавливают притиркой на доводочных чугунных плитах. Эта операция для сохранения перпендикулярности притираемого торца (0,01 — 0,025 мм) относительно оси резьбы выполняется с обязательным применением приспособлений, например набора планшайб (рис. 34). Планшайбы имеют рабочие притертые поверхности диаметром 80-120 мм, биение которых относительно резьбового отверстия не превышает допуска на неперпендикулярность торца корпуса форсунки, и отличаются размером среднего диаметра резьбы. Подбором обеспечивается плотное (без качки) ввертывание корпуса форсунки в соответствующую планшайбу до упора уплотнительной поверхности в доводочную плиту и в таком положении выполняется притирка. Дефекты устра няют с использованием пасты М14 -М20, получение нужной шероховатости Яа < 0,08 мкм -пасты М5-М7. При значительных дефектах перед доводкой торцовую поверхность шлифуют. Твердость торцовой поверхности корпуса форсунки, обеспечивающей уплотнение с распылителем и ограничивающей ход иглы, ие менее НЯС56. Поэтому максимальный съем металла при шлифовке ограничивается глубиной упрочненного слоя.
$ мм. Развертка должна иметь переходной (от образующей к торцу) радиус Я = 1,5_0.з мм с режущими кромками для устранения биения опорного торца. Корпуса с прогибом ствола свыше 0,1 мм бракуют.
В корпусах форсунок и накидных гайках поверхности, участвующие в уплотнении газового стыка, при забоинах, рисках или короблении, восстанавливают проточкой, обеспечивая геометрию, соответствующую техническим требованиям чертежа. В накидных гайках при помощи приспособления (рис.35) контролируют отклонение от перпендикулярности внутреннего торца гайки, крепящей распылитель. Геометрию изношенной поверхности штанг, соприкасающейся с торцом хвостовика иглы, восстанавливают до чертежных размеров шлифовкой или проточкой. Шероховатость этих поверхностей не выше Ля = 0,63 мкм, что обеспечивается доводкой с помощью фасонного притира или полировкой. Натиры на цилиндрической направляющей части штанг устраняют до водкой. Риски глубиной более 0,1 мм и задиры на опорных поверхностях тарелок штанг, появляющиеся в результате износа в зоне сопряжения с опорными витками пружин, устраняют шлифованием. При этом отклонения от перпендикулярности этих поверхностей к оси штанги не должны превышать 0,02 мм, а шероховатость поверхности Яа =1,25 мкм.
Большое внимание уделяют осмотру пружин и проверке их характеристик. Прн трещинах, волосовинах, сколах опорных витков и просадке с уменьшением высоты в свободном состоянии менее допустимого размера пружины бракуют. При отклонении от перпендикулярности опорных витков более 0,35 мм, а также взносах в виде рисок глубиной более 0,4 мм можно перешлифовать опорные поверхности в приспособлении с центровкой оси пружины по внутреннему или наружному диаметру пружины.
Ремонт распылителя. К эксплуатационным дефектам распылителя, которые можно устранить в условиях ремонтного участка депо, относятся: потеря или ухудшение подвижности иглы; потеря герметичности запирающегося конуса или уплотнения торцов; ухудшение качества распыливания с появлением подтекания топлива или уменьшением перепала давления после впрыскивания.
Ухудшение подвижности иглы, вызванное появлением на прецизионных цилиндрических поверхностях незначительных штриховых рисок от инородных частиц, попадающих в топливо, а также при деформировании этих поверхностей устраняют, как правило, взаимной притиркой сопрягающихся поверхностей на станке типа ПР279. 28. Предварительно промытую в бензине иглу закрепляют в цанговом патроне станка и на ее цилиндрическую, на правляющую поверхность в разных местах наносят немного пасты М3. Корпус аккуратно надвигают на иглу, предварительно вручную обеспечивая взаимное их перемещение. После этого при частоте вращения 250-300 об/мин шпинделя станка осуществляется возвратно-поступательное перемещение корпуса с частотой 30 — 40 ходов в 1 мин на 40 — 60% длины прецизионных поверхностей. При этом необходимо избегать соприкосновения конических поверхностей и попадания на них пасты. Притирают 15 — 30 с, а затем корпус сдвигают с направляющей иглы, иглу вынимают из цанги и детали тщательно промывают в бензине. Перед сборкой детали обязательно смачивают профильтрованным топливом (или его смесью с маслом), иглу вставляют в корпус и проверяют плавность ее перемещения в направляющем отверстии корпуса.
Подвижность иглы должна отвечать следующим требованиям: игла, выдвинутая из корпуса распылителя (направляющей иглы) на */з Длины ее рабочей цилиндрической поверхности, должна плавно и безостановочно опускаться под действием собственной массы при любом угле поворота (вокруг своей оси) относительно корпуса распылителя (или направляющей иглы), установленного под углом 45 ° к горизонтали. Отремонтированную пару, кроме того, дополнительно проверяют в контрольной форсунке на соответствие требованиям по плотности и качеству распыли-вания топлива.
Причиной ухудшения подвижности иглы может быть уменьшение диаметрального зазора в связи с образованием на прецизионных поверхностях пленок полимеризации топлива, осаждением смолистых веществ, частичным закоксовыванием от прорыва продуктов сгорания в камеру рас пылителя. В этом случае пытаются восстановить подвижность путем промывки и очистки прецизионных поверхностей в ванночках с бензином с применением щеток, ерша, плотной бумаги и последующим взаимным расхаживанием пары на доводочном станке без применения пасты.
Рис. 35. Приспособление для измерения биения торца накидной гайки форсунки:
1 — накидная гайка; 2 — опора; 3 — центрирующий шарик; 4 — направляющая втулка; 5 — шток; 6 — индикаторная головка; 7 — пружина; 8 — измерительный стержень
При невозможности устранения дефекта таким способом производится взаимная притирка.
При полной потере подвижности иглы или ее зависании в направляющем отверстии корпуса в связи с образованием глубоких (2-4 мкм) рисок, следов задиров и коррозии восстанавливают геометрию цилиндрической прецизионной поверхности доводкой с применением притиров и с последующей операцией подбора деталей распылителя. Дефекты на цилиндрической прецизионной поверхности иглы устраняют доводкой с помощью кольцевых притиров сначала с использованием пасты М7 -М14. При притирке необходимо избегать больших усилий резания (зажатие притира всегда должно обеспечивать его проворот от руки и перемещение вдоль обрабатываемой поверхности без вращения шпинделя станка). При значительном прижатии и прихватывании притира возможны выхваты и одностороннее снятие металла. После устранения дефектов восстанавливают геометрию и шероховатость прецизионной поверхности, которые для отремонтированных деталей должны отвечать следующим требованиям: отклонение от цилиндричности рабочей поверхности иглы не должно превышать 1 мкм при наибольшем диаметре в сторону конуса; отклонения от некругло-сти и прямолинейности не более 0,5 мкм; Доведенные поверхности должны иметь ровный отблеск без следов обработки, видимых невооруженным глазом; шероховатость поверхности не должна превышать Иа = 0,04 мкм, допускается на отдельных участках шероховатость не выше Ла = — 0,063 мкм. Параметры по шероховатости достигаются обработкой отдельным кольцевым притиром, специально заправленным на контрольной поверхности (другой иглы).
Доводка ведется при незначительном усилии резания с использованием паст зернистостью М3 — М5 и возвратно-поступательном перемещении притира в течение 20-30 с. Геометрия контролируется при помощи измерительной стойки с оптикомеханической головкой с ценой деления 0,2 мкм.
Аналогичные дефекты на цилиндрической поверхности корпуса распылителя устраняют также притиркой с помощью разрезных цилиндрических чугунных притиров. Притир надевают на конусную оправку, зажатую в цангу доводочной бабки. Подбором диаметра притира и подбивкой его на оправке добиваются прижатия обрабатываемой поверхности к рабочей поверхности притира. При этом должны обеспечиваться проворот и перемещение обрабатываемой детали от руки без включения шпинделя станка. Для устранения дефектов используют пасту М7, М14, для восстановления геометрии — М3, М5. Деталь перемещают по притиру с частотой 30 — 40 двойных ходов в 1 мин при частоте вращения шпинделя станка 250-300 об/мин. Проведение этой операции требует определенных навыков. Доводчик по изменению усилия резания должен ощущать наличие местных дефектов, отклонение формы цилиндрической поверхности и путем изменения времени доводки на различных участках исправлять их. При предварительной обработке во время устранения местных дефектов, а также при исправлении формы по длине прецизионной поверхности (обеспечение допусков линейности и конусности) притиру иногда придают коническую форму путем шлифования его напильником при вращении на оправке. При окончательной доводке притир должен быть цилиндрическим, что обеспечивается его правкой кольцевым контрпритиром или доводкой на контрольной цилиндрической поверхности другого корпуса. Цилиндричность притира контролируют микрометром.
Восстановленная цилиндрическая поверхность корпуса должна отвечать тем же требованиям по шероховатости, что и для иглы, конусность не должна превышать 0,002 мм при наименьшем диаметре в сторону конуса. Сложность соблюдения этих параметров прецизионной поверхности заключается еще и в том, что в условиях деповского ремонта их можно оценить толь ко косвенно. Такая оценка предварительно выполняется визуально или путем осмотра под микроскопом (рис. 36), а также путем опускания контрольных игл с предварительно измеренной их прецизионной поверхностью. Окончательная оценка качества восстановленной доводкой цилиндрической прецизионной поверхности корпуса дается только после ее совместной притирки с иглой по площади спаривания.
Совместная притирка включает операцию подбора деталей, так чтобы игла плотно входила в отверстие корпуса на
Рис. 36. Микроскоп для осмотра поверхностей конуса и цилиндра корпуса распылителя:
1 — стойка; 2 — осветитель; 3 — линза осветителя; 4 — световодная линза; 5 — корпус распылителя; 6 — направляющая втулка с зеркалом для осмотра цилиндра; 7 — направляющая втулка для осмотра конуса; 8 — корпус; 9 — оптическая увеличительная трубка; 10 — держатель 30-50% длины цилиндрической части. Для облегчения подбора иглы и корпуса предварительно рассортировывают через 1 мкм и укладывают в тару по возрастающим размерам. При малом количестве ремонтных деталей для получения нужных размеров проводят размерную притирку цилиндрической поверхности одной из деталей. Для совместной притирки иглу распылителя за хвостовик зажимают в цангу доводочной бабки. Цилиндрическую поверхность иглы смазывают тонким слоем пасты М3, М1. На корпус распылителя надевают державку и надвигают на иглу. Пустив станок, с частотой вращения шпинделя 200-250 об/мин перемещают корпус распылителя вдоль иглы, постепенно увеличивая размах, но не допуская соприкосновения конусов и свисания корпуса более чем на 40% длины прецизионной направляющей части.
Совместно доведенные цилиндрические поверхности должны иметь ровный отблеск на всей площади соприкосновения, без следов обработки, видимых невооруженным глазом. Оттенки матовости в виде пятен на отдельных участках или по краям прецизионной поверхности характеризуют неполное спаривание. В этом случае совместную притирку необходимо продолжить. Однако признаки неполного спаривания могут быть вызваны и отступлением от требований, предъявляемых к прецизионным поверхностям в процессе их подготовки к совместной притирке, например, при конусности, корсетности, бочкообразное™, завалах краев цилиндрической поверхности более 2 — 3 мкм. В этом случае продолжение совместной притирки может привеста к значительному увеличению диаметрального зазора и, следовательно, не обеспечить допустимых требований по плотное™ прецизионной пары.
Ремонт конического сопряжения распылителя, а также восстановление его работоспособное™ после спаривания по цилиндру иглы и корпуса в условиях депо производится с помощью взаимной пригарки конусов. Возможные случаи взаимного расположения поверхностей запирающих конусов при их притирании представлены на рис. 37, где изображены схема и реальные образующие конусов в продольном сечении (профилограммы) и в поперечном сечении (круглограммы) по месту контакта. Для нового распылителя (рис. 37, б, в, I), взаимная притирка конусов которого выполнена на заводе после финишных операций шлифования (игла) и электроискровой обработки (корпус), характерно неглубокое на 1 — 2 мкм взаимное втирание конических запирающих поверхностей. При этом притарочный поясок (место взаимного контакта) по ширине, как правило, не превышает 0,15 — 0,25 мм и располагается на игле, начиная с кромки большого основания конуса, а на конусе корпуса — ниже на 0,1-0,3 мм от кромки большего основания конуса. В поперечном сечении притирочные пояски иглы и корпуса плотно прилегают друг к другу и обеспечивают необходимую герметичность. Конусное соединение после притирочного пояска в этом случае сохраняет заложенную технологическим процессом разницу (0,5-1,5°) углов конусов, а линейность образующих мало искажается во время притирки. При потере герметичности конусного соединения, вызванной разрушением или износом притарочного пояска в поперечном сечении (рис. 37, в, II), что характеризуется при испытании форсунки на опрессовочном стенде появлением отрывающейся капли или подтеканием до и после впрыскивания при ухудшении качества распиливания, работоспособность вос станавливается взаимной притиркой конусов только в области самого притирочного пояска.
Притирка выполняется при частоте вращения шпинделя доводочного станка 80-150 об/мин с применением пасты М5, М7. Пасту тонким слоем накладывают на конус иглы, хвостовик которой закреплен в цанге шпинделя, а цилиндрическую поверхность смазывают чистым маслом МС-20 или дизельным. После этого корпус распылителя во избежание попадания пасты на цилиндр аккуратно надвигают до соприкосновения конусов. Процесс притирания состоит в чередовании соприкосновения конусов в течение 3 — 5 с с усилием 3 — 7 Н (300 — 700 гс) с поворачиванием корпуса на 30 — 60° по направлению и против вращения шпинделя и соударением конусов в течение 1-2 с с частотой, превышающей частоту вращения шпинделя в 1,5 — 3 раза, при выдвижении корпуса до 25 % длины направляющей части. В первом случае обеспечивается съем металла из дефектной зоны пояска, во втором при соударении происходит разрушение кольцевых рисок с образованием нового притирочного пояска с зоной уплотнения, смещающейся в сторону вершины конусов. Общее время притирочной операции зависит от характера дефекта, при этом работоспособность пасты в зоне притирки сохраняется в течение не более 20 — 30 с. На профилограмме (рис. 37,6, 11) восстановленного таким способом распылителя можно видеть уже более глубокое до 2 — 3 мкм взаимное внедрение конических поверхностей с увеличением общей ширины притирочного пояска, которая не должна во всех случаях превышать более 0,5 мм.
Это контролируется визуально с помощью лупы на предварительно протертой или промытой бензином кониче ской поверхности иглы. Окончательный контроль качества этой восстановительной операции выполняют путем проверки работоспособности собранного в форсунке распылителя на опрессовочном стенде типа А106.
При неудовлетворительных показателях качества распыливания топлива или герметичности распылителя и ширине притирочного пояска более 0,5 мм дальнейшее совместное притирание конусов с введением пасты в область уплотнительного пояска
Рис. 37. Взаимное расположение образующих запирающих конусов в распылителе: а — схема (корпус К, игла И)\ б — профилограммы продольного сечения; в — круглограммы поперечного сечения по месту контакта; /-/К-различные случаи притирания конусов может привести к слиянию образующих (рис. 37, б, III). Распылители с таким конусным соединением уже не будут обеспечивать необходимого качества распылива-ния вследствие изменения гидравлических свойств проточной части (отсутствия разницы углов конусов), а также достаточной герметичности из-за контактирования сопряженных конических поверхностей в отдельных точках их поперечных сечений. Восстановление таких распылителей, а также распылителей, имеющих значительные дефекты (сколы и трещины глубиной более 5-10 мкм с большим углом раскрытия), на притирочном пояске может быть выполнено только с помощью специальных технологических приемов и операций, которые, как правило, дают положительные результаты только при определенных навыках у доводчиков. Одним из таких приемов является использование при ремонте конусного соединения распылителя крупного свободного абразива — микропорошка М20 (экстра 500) или пасты М28. Микропорошок, разведенный на масле МК22, наносят на конусную поверхность иглы, не тронутую совместной притиркой. В процессе совместного притирания крупные зерна порошка попадают в первую очередь в область начала слияния конусов и, разрушаясь, выцарапывают между ними зазор. Разрушенные и размельченные при этом зерна постепенно вклиниваются все дальше между слитыми поверхностями конусов, вытирая металл и образуя таким образом клиновидный зазор (рис. 37,6, IV). Процесс притирания ведется до образования пояска шириной 0,3 — 0,1 мм.
После этого в область пояска наносят пасту М5 -М3 и совместно притирают для получения герметичности пояска по методике, рассмотренной для предыдущего случая (см. рис. 37, в, 11).
Восстановление угла конуса корпуса распылителя и профиля его образующей возможно также с помощью специальной доводочной технологической операции, предусматривающей применение набора притиров (ПР299, ПР435 и др., см. рис. 30). Шлифование конусной рабочей поверхности притира выполняется на станке для притирки деталей напильником и с использованием клинового приспособления типа ПР2717 (см. рис. 31). В этом случае угол конусной поверхности притира должен быть на 1,0-1,5° меньше угла конуса иглы, что технологически обеспечивает упомянутое выше приспособление. Для выборочного контроля угла конуса отшлифованного притира можно использовать малый инструментальный микроскоп.
При шлифовке притиров следует обращать внимание на необходимость плотного зажима направляющей оправки притира в разрезной втулке приспособления. При качке направляющей во время операции шлифования возможны отклонения угла конуса за счет перекоса осей оправки и приспособления, а также отклонения от прямолинейности образующей конической поверхности (завал, бочкообразность) и его радиального биения относительно направляющей более 4-5 мкм. Такие притиры не могут обеспечить необходимой точности при восстановлении геометрии конуса корпуса.
Для доводки конуса подбирают притиры с зазором по прецизионным поверхностям не более 4 мкм (свободное проворачивание корпуса без качки сопрягающихся поверхностей при смазке маслом МС20). В процессе доводки производится 3 — 6 шлифований притира. После первого шлифования на конус притира наносят пасту MIO -М14. Притирка ведется в течение 30 — 40 с при частоте вращения шпин деля 200 — 300 об/мин с периодическим поворачиванием корпуса по направлению и против вращения шпинделя на 30 — 40° и усилии нажатия 4-8 Н. После второго-третьего шлифования перед нанесением пасты конусные поверхности вводят в соприкосновение для оценки площади их соприкосновения. При недостаточно четком отпечатке доводку на пасте MIO — М14 повторяют. При отпечатке на образующих более 80 % их длины наносят пасту М7 — М5 и ведут вторую доводку в течение 20-30 с. Третья доводка выполняется на пасте М3 — М5 при уменьшении до 50-100 об/мин частоты вращения шпинделя и чередовании притирочного процесса с периодическим соударением силой в 2 — 4 Н и с частотой, превышающей частоту вращения шпинделя в 2 — 3 раза.
После восстановления таким образом геометрии конуса корпуса производится его взаимная притирка с конусной поверхностью иглы в области притирочного пояска. В отдельных случаях, там где есть необходимость в увеличении разницы углов или снятии глубоких дефектов (до 7-10 мкм) на притирочном пояске конуса иглы, производится предварительная совместная притирка конусов с использованием свободного абразива микропорошка М20. В результате последней операции может потребоваться дополнительная повторная притирка конуса корпуса отшлифованным притиром и взаимная притирка конусов в области притирочного пояска.
Для распылителей, ремонт конического соединения которых не обеспечивает удовлетворительного качества распыливания и герметичности при испытаниях в контрольной форсунке, допустима замена одной из деталей. Ремонт в этом случае начинают с подбора и спаривания (взаимной притирки) деталей по цилиндру. Гео метрию конуса корпуса рекомендуется предварительно восстанавливать с применением набора притиров. В качестве игл, как правило, используются иглы, не подвергавшиеся неоднократной взаимной притирке по конусу, не имеющие глубоких (более 4-5 мкм) дефектов на конусе, а также иглы, конусы которых предварительно прошлифованы на специальном шлифовальном оборудовании. Восстановление рабочих поверхностей корпусов распылителей ограничивается как наличием эксплуатационных дефектов (глубокими задирами, эрозионно-кавитационными пора-
Рис. 38. Приспособление для измерения подъема иглы форсунок дизелей 2Д100 (а) и
Д50 (б):
1 — наконечник; 2 — корпус; 3 — цанговый зажим; 4 — измерительная головка жениями конуса), так и толщиной оставшегося после многократных восстановительных операций упрочненного поверхностного слоя (для цементации не менее 0,4 мм, для азотации 0,25 мм).
При взаимном притирании конусов распылителя, а также во время его работы в эксплуатации из-за износа рабочего пояска происходит просадка иглы. Допустимый подъем иглы при его увеличении на 0,10 — 0,25 мм восстанавливают путем шлифования торца корпуса распылителя на плоскошлифовальном станке с последующей притиркой торцовой уплотнительной поверхности на доводочных чугунных плитах. Технологический процесс притирки аналогичен разобранному выше при притирке уплотнительных торцов корпусов форсунок. Подъем иглы измеряют с помощью приспособления, представленного на рис. 38. Общая толщина металла, снятого с торцовой уплотнительной поверхности корпуса распылителя, ограничивается глубиной упрочненного слоя (цементации, азотации), при этом допускается понижение твердости на уплотнительном торце до НЯС 54. Для распылителей дизелей типа Д100 подъем иглы в пределах (0,45 + ±0,05) мм может быть восстановлен таким же путем или подбором ограничителя необходимой высоты.
Для оценки состояния площади проходного сечения распыливающих отверстий носик распылителя или сопла очищают от нагара. Загоревшие отверстия прочищают латунной проволокой, после чего распылитель промывают на стенде А106 под давлением топливом из аккумулятора большой вместимости. Визуальным осмотром с помощью лупы проверяют состояние кромок на выходе из распыливающих отверстий; недопустимы сколы, оплавленные, рваные или неравномерно из ношенные края. Предельный износ распыливающих отверстий контролируют по эталонам пропускной способности на воздушных или гидравлических стендах.
Сборка, испытания и монтаж форсунок на дизеле. Форсунки собирают, применяя приспособления, обеспечивающие в первую очередь удобство и возможность создания нормальных монтажных усилий, а также строгое взаимное положение отдельных деталей. Осевые усилия при сборке форсунок устанавливают динамометрическими или специальными тарировочны-ми ключами, определяющими крутящий момент затяжки накидной гайки или нажимного стакана (форсунки типа Д100). Кроме того, усилие затяжки может быть проконтролировано по углу поворота накидной гайки от момента полного соприкосновения уплотнительных поверхностей деталей. Расчетные оптимальные осевые усилия для различных конструкций форсунок и соответствующие технические требования, обеспечивающие при сборке эти усилия, имеют следующие значения:
Тип | Осевое усилие, Н | Технические |
дизеля | требования | |
Д100 | 23000 | Тарированный ключ с усилием, обеспечивающим момент 120±55 Н-м |
Д50, Д70 | 40000 | Полное усилие руки на ключе с рычагом 600-700 мм |
11Д45 | 50000 | От полного соприкоснове |
ния торцов довернуть ключом на 2,5 — 3 деления (~20°) | ||
Д49 | 60000 | От полного соприкоснове- |
ни я торцов довернуть ключом на 5 — 6 делений на накидной гайке (~40°)
Особое внимание уделяют технологическому процессу сборки форсунок дизелей типа Д100. Перекосы, вызванные чрез мерным обжатием прокладок, и повышенные торцовые биения деталей неизбежно вызывают в этой форсунке деформации прецизионных поверхностей, соизмеримые с допустимыми отклонениями к их геометрической форме и взаимному положению. В связи с этим необходимо ставить при каждой сборке только отожженные медные прокладки, соответствующие техническим требованиям чертежа. Использование бывшей в употреблении прокладки разрешается в том случае, если она не имеет коробления, заусенцев, глубоких (более 0,2 мм) рисок и снята путем легкого обстукивания.
При сборке форсунок угловое расположение (в пределах 1-2°) распыливающих отверстий сопел (корпусов распылителей) относительно корпуса форсунки обеспечивается либо конструктивно, например совмещением контрольной плоскости сопла с ограничивающей проворачивание плоскостью в корпусе форсунки (форсунки дизелей типа Д100), или путем постановки штифтов, либо с помощью специальных кондукторных приспособлений (рис. 39). Это приспособление обеспечивает путем совмещения контрольных плоскостей сопла и кондуктора, правильное положение распыливающих отверстий относительно диаметральной плоскости, проходящей через оси шпилечных отверстий корпуса форсунки. В форсунках дизелей типов Д50 и Д70, где допуск на расположение любого из распыливающих отверстий относительно вертикальной диаметральной плоскости, проходящей через ось штуцера подвода топлива, составляет ±5°, установка распылителей может быть выполнена на опрессовочном стенде по направлению вытекающей струи топлива при прокачке.
При постановке в форсунки новых деталей, имеющих взаимное перемещение при работе, а также при их ремонте с примене нием механических и доводочных операций собранные форсунки должны пройти обкатку продолжительностью не менее 20 — 40 мин. Допустимо совмещение обкатки форсунок с обкаткой топливных насосов, а также с обкаточными реостатными испытаниями дизелей. После проведения обкатки форсунки обязательно испытывают на качество распыливания и герметичность.
Для равномерного распределения топлива по цилиндрам форсунки при постановке на один двигатель должны Иметь пропускную способность на режиме номинальной частоты вращения и средней подачи с отклонениями в комплекте, не превышающими более ±2%. Для тепло-
Рис. 39. Приспособление для сборки форсунок дизелей типа Д49:
/-основание; 2 — кондуктор для фиксации сопла; 3 — форсунка; 4 — стойка; 5 — подвеска; 6 — штифты для шпилечных отверстий корпуса; 7 — подвижная планка; 8 — эксцентриковый зажим сопда возных дизелей, значительную часть времени работающих на холостом ходу, не меньшую роль играет и обеспечение равномерной подачи по цилиндрам на режимах малых подач и минимальных частот вращения. Требования по допустимым отклонениям пропускной способности форсунок в первую очередь обеспечиваются контролем истечения распыливающих отверстий при комплектовке форсунки соплом и распылителем. Для дизелей типов Д70 и Д50 для снижения отклонений в пропускной способности в комплекте форсунок, идущих для установки на один двигатель, разница по времени истечения между двумя любыми распылителями желательна не более одной секунды. Для дизелей типа Д49 рекомендуется проверять идентичность подачи форсунок на технологической секции топливного насоса. Для дизелей типов 11Д45 и М756, имеющих многоплунжерные блочные топливные насосы, допускается сортировка форсунок по пропускной способности на группы. Установка на каждом дизеле форсунок только одной группы позволяет заменять любую вышедшую из строя форсунку, без опасения резко изменить регулировку насоса и ухудшить равномерность работы секций. Технические условия для определения пропускной способности форсунок тепловозных дизелей типов 11Д45, М756, Д49 и разбивка их на группы по минимальной подаче приведены в табл.
8. Форсунки проверяют (сортируют) на специальном односекционном стенде или на регулировочных стендах с использованием контрольной секции технологического насоса. Перед началом работы на стенд ставят эталонные комплекты с аттестованной на заводе подачей и фиксированными положениями реек.
Распылители, поступающие в запас, а также после ремонта конусного уплотнения сортируют по такой же методике, устанавливая в контрольный корпус фор-
Таблица 8
Тип | Контрольная секция с эталонной | Контрольная секция с испытываемой | |||
форсункой | форсункой | ||||
дизеля | |||||
п, об/мин | е | л, об/мин | е | № группы | |
750 | (550 ± 5) г/мин | (140 + 20) г* | 1 | ||
11Д45 | 400 | (100 + 20) г* | 2 | ||
400 | (130+5) г* | (60 ±20) г* | 3 | ||
(180 ±10) г/мин | 1 | ||||
М756, М753 | 900 | (12 + 0,15) кг/ч | 900 | (190± 10) г/мин (200+ 10) г/мин | 2 3 |
(210 ± 10) г/мин | 4 | ||||
1А-5Д49 | 500 | (565 ± 5) г/мин | 500 | (565І$)) г/мин | 1 |
сунки. Номер группы маркируют рисками, нанося их на поверхности бурта распылителя.
Рабочую камеру цилиндра дизеля при монтаже форсунки уплотняют медной прокладкой (дизели типов Д100, Д70, М756), устанавливаемой между уплотнительным торцом форсунки и посадочным местом в крышке цилиндра или адаптере. Надежным также является уплотнение газового стыка с помощью неширокого конусного пояска, выполненного на накидной гайке и в форсуночном отверстии цилиндровой крышки (дизели 11Д45 и Д49). Уплотнение осуществляется приложением осевого усилия (5000-10000 Н) путем затяжки гаек на крепящих форсунку шпильках. В эксплуатации отказы форсунок могут быть из-за монтажных деформаций, проявляющихся главным образом при неравномерной затяжке гаек. Более других подвержены деформациям от монтажных усилий форсунки дизелей типа Д100 вследствие недостаточной их жесткости в поперечном сечении. На рис. 40 показана схема возможных деформаций этой форсунки при неравномерной и чрезмерной затяжке шпилечных гаек адаптера. При неравномерной затяжке гаек (перекос на одну-полторы грани) вследствие возникновений изгибающего момента, действующего на ствол форсунки, корпуса форсунки и распылителя испытывают не только усилия сжатия, но и изгиба.
Во время установки форсунок дизелей типов Д70 и Д50 неравномерное обжатие прокладки, уплотняющей газовый стык, а также при разностенности прокладки может возникнуть поперечное одностороннее воздействие на корпус распылителя. Все это приводит к изменению формы прецизионной цилиндрической поверхности, ухудшая подвижность иглы, а также смещение оси конической поверхности, вызывая нарушение герметичности. У форсунок дизелей типа Д100, подвергшихся чрезмерной де-
Рис. 40. Схема возможных деформаций форсунки дизелей типа Д100 при неравномерных усилиях и Л’, затяжки шпилечных гаек:
N — суммарное усилие; М — изгибающий момент; 8 — деформационный изгиб ствола корпуса формации, даже при ослаблении гаек и их последующей равномерной затяжке, качественная работа форсунки может не восстановиться. Для восстановления работоспособности такой форсунки необходима полная ее переборка с заменой прокладок.
Гайки крепления форсунки, как правило, затягивают в три этапа. Сначала равномерно затягивают гайки ключом, но не создают полного рабочего осевого усилия, частично обжимая прокладку, уплотняющую газовый стык. Затем, отвернув гайки, завертывают их вручную до отказа. Окончательно затягивают усилием одной руки, ключом с длиной рукоятки не более 200 мм на две с половиной — три с половиной грани за 5 — 7 приемов, равномерно и поочередно поворачивая гайки на половину грани за прием. Достаточно эффективным мероприятием по снижению монтажных деформаций, но не устраняющим их полностью при неравномерной затяжке, является крепление форсунок дизелей типа Д100 с помощью дополнительного центрирующего фланца. Форсунки дизелей Д50, Д70, 11Д45 и Д49 можно крепить ключом с длиной рукоятки не более 250 мм при усилии одной руки человека. Для крепления форсунок дизелей Д49 рекомендуется использование динамометрического ключа с фиксированным моментом (100±20)Н м.
При монтаже очень важно проверить состояние уплотнительной прокладки и чистоту форсуночного отверстия. Не допускается уплотнение газового стыка с помощью двух прокладок или прокладок, имеющих отклонения от чертежных размеров, так как в этих случаях нарушится положение распыливающих отверстий по отношению к объему камеры сгорания. Допуск на выступание носика соплового наконечника из форсуночного отверстия крышки цилиндра (адаптера) не превышает 1 мм. Перед монтажом форсунок с коническим уплотнением газового стыка необходимо проверить состояние уплотнительных поверхностей. На этих поверхностях не допускаются забоины, вмятины, следы коррозии. Конус контролируется калибром по краске. Прилегание должно быть по всему периметру уплотнительного пояска и не менее 50% высоты пояска, а шероховатость конических поверхностей, уплотняющих газовый стык, не выше Да =1,25 мкм.
⇐Оборудование и стенды | Топливные системы тепловозных дизелей. Ремонт, испытания, совершенствование. | Топливопроводы⇒
Пневматические форсунки распылителя | Штукатурные работы
Форсунки (наконечники), надеваемые на конец растворного шланга, служат для распыления раствора по оштукатуриваемой поверхности при его нанесении машинами. Конструкции форсунок различные.
Пневматические форсунки применяются для нанесения раствора с помощью сжатого воздуха, подаваемого от компрессора к форсунке по шлангу. Сжатый воздух как бы разбивает раствор на мелкие частицы и несет их с большой скоростью на оштукатуриваемую поверхность.
Форсунки пневматического действия не требуют увеличения давления в растворонасосе и растворопроводе, поэтому находят широкое применение. Пневматические форсунки бывают с кольцевой и центральной подачей воздуха.
Рис. 83. Форсунка с кольцевой подачей воздуха
Форсунка с кольцевой подачей воздуха (рис. 83) устроена следующим образом. На штуцере 1 закрепляется хомутом растворный (материальный) шланг, по которому к форсунке подается раствор от растворонасоса. К другому концу штуцера закрепляется гайкой резиновый наконечник 2. В корпусе штуцера, около наконечника, имеется кольцевая выточка 4, в. которую ввертывается патрубок 5 с вентилем 6. По патрубку в форсунку подается сжатый воздух.
Во время работы раствор, проходящий через форсунку, подхватывается сжатым воздухом и с силой выбрасывается на оштукатуриваемую поверхность распыленной струей — факелом. Вентиль служит для регулирования подачи сжатого воздуха и изменения величины факела.
При работе необходимо следить за количеством сжатого воздуха, попадающего в форсунку. Излишнее количество воздуха вызывает чрезмерное распыление раствора и увеличивает его потери. Если воздуха недостаточно, то раствору не сообщается нужная скорость, в результате чего он падает на пол, не долетев до оштукатуриваемой поверхности.
Применение мощного компрессора дает возможность получить струю длиной в 2,5—3 м. При уменьшении подачи сжатого воздуха длина факела распыления раствора уменьшается и оштукатуривание производят с расстояния 1—1,5 м.
Если высота оштукатуриваемых помещений более 3,5—4 м, то потолок и верх стен необходимо оштукатуривать с подмостей или столиков.
При правильном выборе длины факела потери раствора при оштукатуривании потолков составляют 6—8%. Поэтому оператор должен строго следить за правильным выбором длины факела распыления.
Форсунку с центральной подачей воздуха иногда называют универсальной, потому что, изменяя расстояние между воздушной трубкой и наконечником, можно получать требуемый факел распыления в зависимости от густоты раствора и выполняемой работы. При приближении воздушной трубки к наконечнику форсунка дает широкий факел, а при удалении воздушной трубки от наконечника факел распыления сужается.
Этой форсункой можно наносить раствор на расстоянии 100— 400 мм от поверхности, создавая им в зависимости от назначения различные по виду фактуры на оштукатуриваемой поверхности.
Рис. 84. Форсунка Росминжилгражданстроя с центральной подачей воздуха
Форсунка Росминжилгражданстроя (рис. 84) состоит из сменного наконечника 1, корпуса 2, в который вставлена воздушная трубка 3. Воздушная трубка может передвигаться по втулке, приближаясь или удаляясь от наконечника; закрепляется она в нужном положении винтом 4. На одном конце воздушной трубки имеется калиброванное отверстие, а на другом — кран 5, который служит для пуска или прекращения подачи сжатого воздуха из присоединенного к патрубку 6 воздушного шланга. Сменный наконечник 1 закрепляют накидной гайкой 7. К корпусу форсунки прикреплен патрубок 5, на который надевается растворный шланг.
Кроме форсунки Росминжилгражданстроя, по принципу центральной подачи воздуха работают форсунка ВНИОМС, форсунка треста «Строитель» и др. Все пневматические форсунки имеют сменные наконечники. Это необходимо, во-первых, потому что они быстро изнашиваются и требуют замены, а во-вторых, для лучшего нанесения раствора различной густоты.
Рис 85 Форсунка конструкции А. Е. Суржаненко для нанесения быстросхватывающихся растворов
Форсунка для нанесения быстросхватывающихся растворов конструкции А. Е. Суржаненко (рис. 85) состоит из корпуса, наконечника и штуцера, на который надевают растворный шланг. В форсунку вставлена воздушная трубка с краном. На конце трубки имеется штуцер для воздушного шланга, по которому подается сжатый воздух с пылевидным вяжущим (сухим гипсом).
Перемешивание гипса с известковым раствором происходит в корпусе форсунки, который устроен так, что известковый раствор и сухой гипс, переходя из его узкой части в широкую, а из широкой в узкую, хорошо перемешивается. Форсунка изготовлена специально для работы на дозаторе-транспортере.
Vortec.com | Форсунки для распыления жидкости Sprayvector
Обзор продукта
Форсунки Vortec обеспечивают распыление сверхмелких капель для охлаждения испарением, распыления, увлажнения и смачивания. Превосходя обычные гидравлические и пьезоэлектрические форсунки, распылительные форсунки создают формы распыления, которые можно широко рассеивать или направлять. Поток жидкости увлекается высокоскоростным сжатым воздухом для создания капель распыления микронного уровня, что приводит к большему охвату поверхности, чем у обычных форсунок. Благодаря такому более эффективному использованию жидкости распылительные форсунки ускоряют взаимодействие воздуха и жидкости, обеспечивая более эффективное охлаждение, увлажнение, смачивание и контроль пыли.
Доступны три типа распылительных форсунок, каждая из которых обеспечивает регулируемый расход от 6 до 30 галлонов (23 — 114 литров) в час.
- Запотевание: направленное распыление с размером капель от 20 до 60 микрон. Вязкость жидкости до 1100 сП.
- Распыление: Направленное распыление с размером капель от 60 до 200 микрон.Вязкость жидкости до 1100 сП
- Увлажнение: Широкий спрей с размером капель от 20 до 200 микрон. Вязкость жидкости до 100 сП.
Преимущества
- Более эффективное использование жидкости, поскольку она увлекается сжатым воздухом
- Постоянное эффективное охлаждение поверхностей снижает тепловую деформацию деталей
- Устраняет повреждение дерева и других чувствительных к воде поверхностей из-за низкой влажности
- Обеспечивает равномерное покрытие при нанесении покрытий, ингибиторов ржавчины, смазок, консервантов и т.
Д.на детали, дерево, резину, пластик, продукты питания и т. д.
- Снижает уровень шума
- Испытание скоростей на влияние влажности из-за различных уровней влажности
- Расход жидкости под высоким давлением не требуется
- Прецизионная скорость потока сводит к минимуму использование дорогих покрытий, консервантов, ингибиторов коррозии и т. Д.
- Создает более мелкие капли, чем гидравлические форсунки
- Размер капель и производство не зависят от давления жидкости
- Внешнее смешивание воздуха и жидкости для минимизации засорения
Характеристики
- Производство контролируемых ультратонких капель
- Съемные наконечники сопел для легкой очистки и замены
- Сменные наконечники форсунок для универсального распыления, распыления и увлажнения
- Может использоваться в широком диапазоне вязкости от 1 до 1100 сПс
- Обеспечивает широкий диапазон расходов жидкости (6-30 галлонов в час / 23-114 литров в час)
- Не требует электрического подключения к форсунке
- Допускается подача жидкости под низким давлением (2-20 фунтов на кв.
Дюйм / 0.14-1,4 бар)
- Используйте только 12 стандартных кубических футов в минуту сжатого воздуха
- Унос жидкости с помощью сжатого воздуха сводит к минимуму засорение
Особенности продукта:
Модель 1703:
- Форсунка для туманообразования, производящая капли размером 20-60 микрон
- Туман распространяется до 30 дюймов в валок на расстоянии 8 футов (2,5 метра) от сопла
- Для жидкостей с вязкостью до 1100 сПс
Модель 1707:
- Увлажняющая форсунка, производящая капли размером 20-200 микрон
- Широкий увлажняющий туман распространяется на 6 футов (2 метра) всего на 12 дюймов (130 см) от сопла
- Перекачивает жидкости с вязкостью до 100 сПс
Модель 1713:
- Форсунка для распыления, производящая капли 60-200 микрон
- Распространение тумана расширяется до 30 дюймов (76 см) при ширине 8 футов (2.5 метров) от сопла
- Для жидкостей с вязкостью до 1100 сПс
Технические характеристики
Модель № | 1703 | 1707 | 1713 | 1723 | 1727 | 1733 |
Приложение | Туман | Увлажнение | Распыление | Туман | Увлажнение | Распыление |
Размер капли, мкм | 20-60 | 20-200 | 60-200 | 20-60 | 20-200 | 60-200 |
Максимальная вязкость жидкости, сПс | 1100 | 100 | 1100 | 1100 | 100 | 1100 |
Форма распыла | Плотный | широкий | Плотный | Плотный | широкий | Плотный |
Включает фильтр и сетчатый фильтр для жидкости | № | № | № | Есть | Есть | Есть |
Модель # | 1703 | 1707 | 1713 | 1723 | 1727 | 1733 |
Приложение | Запотевание | Увлажнение | Распыление | Туман | Увлажнение | Распыление |
Размер капли, мкм | 20-60 | 20-200 | 60-200 | 20-60 | 20-200 | 60-200 |
Максимальная вязкость жидкости, сПс | 1100 | 100 | 1100 | 1100 | 100 | 1100 |
Форма распыла | Плотный | широкий | Плотный | Плотный | широкий | Плотный |
Включает фильтр и сетчатый фильтр для жидкости | № | № | № | Есть | Есть | Есть |
Видео
Форсунки
Форсунки Vortec обеспечивают распыление сверхмелких капель для охлаждения испарением, распыления, увлажнения и смачивания. Превосходя обычные гидравлические и пьезоэлектрические форсунки, распылительные форсунки создают формы распыления, которые можно широко рассеивать или направлять. Поток жидкости увлекается высокоскоростным сжатым воздухом для создания капель распыления микронного уровня, что приводит к большему охвату поверхности, чем у обычных форсунок. Благодаря такому более эффективному использованию жидкости распылительные форсунки ускоряют взаимодействие воздуха и жидкости, обеспечивая более эффективное охлаждение, увлажнение, смачивание и контроль пыли.
Литература
Инструкция по установке и эксплуатации
Размеры и характеристики
Китай Форсунка, Производители форсунок, Поставщики, Цена
Цена FOB для Справки: US $ 1.0-6,0 / шт.
Мин. Минимальный заказ: 200 Штука
Лучшее качество Mentallic Spray Nozzle
1. Размер резьбы: 3/8 », 3/4 », 1/2 », 1 », 1-1 / 2 », 2 », 2-1 / 2 ‘и т. Д.
Поставщики с проверенными бизнес-лицензиями
Поставщики проверены инспекционными службами
CY Spraying & Purification Technology Limited- Гуандун, Китай ISO 9001, ISO 9000, ISO 14001, ISO 20000
определение распылительной форсунки и синонимы распылительной форсунки (английский)
Из Википедии, бесплатная энциклопедия
Распылительная форсунка — это устройство, которое облегчает формирование распыления.Когда жидкость распыляется в виде струи капель (распыление), это называется спреем. Распылительные форсунки используются для достижения двух основных функций: увеличения площади поверхности жидкости для усиления испарения или распределения жидкости по площади.
Применение распылителей
Существуют сотни областей применения, где необходимы системы распыления для эффективного нанесения или использования жидкости. Ниже указаны несколько промышленных применений распылителя:
Распылители топлива
Распыление углеводородных жидкостей (ископаемое топливо) — одно из наиболее экономически важных применений распылительных форсунок. Примеры включают топливные форсунки для бензиновых и дизельных двигателей, форсунки для реактивных двигателей (газовых турбин), форсунки в ракетных двигателях. Эта группа приложений имеет большое влияние на эффективность этих систем и снижение выбросов загрязняющих веществ (сажи, NOx, CO).
- Аэрокосмическая промышленность
- Для получения жидкости с очень высоким отношением площади поверхности к массе. Это ускоряет испарение, способствуя высокой скорости сгорания.
Промышленные распылители
Линейная и цементная промышленность: Распылительная жидкость для охлаждения и кондиционирования газа или распыление псевдоожиженного топлива в печах для сжигания.
- Энергетические / экологические приложения
- Навозная жижа распыляется для контроля выбросов SO2, химический раствор распыляется для контроля NOx, а вода распыляется для удаления твердых частиц с использованием распылительной башни или циклонного скруббера с распылением
- Пищевая промышленность
- Перед / после выпечки на тесто наносят жидкое масло.
- Производство напитков
- Струи воды используются для очистки резервуаров для хранения
- Химическая промышленность
- Распыление реагентов для улучшения диспергирования и увеличения массопереноса жидкость-газ.Используются многие системы, включая распылительные башни
- Фармацевтическая промышленность
- Покрытие таблеток и распылительная сушка
- Электронная промышленность
- Эффективное покрытие электронных деталей
- Горнодобывающая промышленность
- Вода распыляется для контроля выбросов пыли, образующейся во время шлифовальные, распылительные форсунки также используются для промывки гравия на сортировочных установках.
- Автомобильная промышленность
- Водные и моющие спреи для мойки автомобилей и окраски автомобилей распылением.
- Сталелитейная промышленность
- Для удаления накипи из раскаленной стали и ее закалки используется вода под высоким давлением
- Лакокрасочная промышленность
- Равномерно распределите краску по поверхности.
Окраска распылением широко используется во многих производственных процессах.
- Промышленность по переработке отходов
- Удалите излишки тепла из биоразлагаемого осадка отходов путем аэрации и поддержания ила в прохладном состоянии для достижения оптимальной температуры для микробов
Сельскохозяйственные распылители
Распылительные форсунки используются для эффективного распределения и диспергирования инсектицидов и пестицидов, включая воду. поля.См. Применение с воздуха, применение пестицидов, распылитель.
Потребительские товары
Распылители используются с распылителями бытовых чистящих средств с помпой. Эти форсунки предназначены для распределения продукта по площади. см. Аэрозольный спрей и баллончик
Типы распылительных форсунок
Распылительные форсунки можно разделить на несколько типов в зависимости от потребляемой энергии:
Гидравлическое распыление
Гидравлическое распылительное сопло использует кинетическую энергию жидкости как источник энергии для разбивания жидкости на капли. Этот тип распылителя потребляет меньше энергии, чем газовое или двухжидкостное распылительное сопло. По мере увеличения давления жидкости поток увеличивается, а размер капли уменьшается. Но это приводит к проблемам при выборе размера капель и достижении определенной скорости потока при заданном давлении. Для преодоления этой ситуации была разработана специальная гидравлическая форсунка (Lechler Spillback Nozzle). Это сопло может изменять расход жидкости при определенном размере капель и давлении. Эта форсунка обеспечивает лучший и оптимальный контроль над распылением жидкости и в некоторых случаях может устранить необходимость в дорогом сжатом воздухе.
Распыление газом (воздухом)
Воздух, пар или другие газы могут разбивать жидкость, образуя струю, при этом газ является источником энергии.
Внутреннее смешивание
Форсунки внутреннего смешивания смешивают жидкости внутри форсунки.
В распыляемом газе распылителе используется газовый источник для разделения жидкости на капли. Внутренний смешанный двойной распылитель жидкости может использовать два разных способа распыления жидкости:
В первом типе жидкость ударяется о поверхность, разбивая поток жидкости, а затем смешивается воздух для ее распыления.Преимущество этого процесса заключается в уменьшении количества воздуха, необходимого для образования капель, но обратная сторона заключается в том, что со временем ударная поверхность разрушается и влияет на размер распыляемых капель. Срок службы сопла может быть очень коротким, если в жидкости есть примеси.
Во втором типе жидкость разбивается на капли, используя только газ. Преимущество этого типа состоит в том, что сопло служит дольше, но недостатком является то, что этому типу распылителя требуется больше газа для образования капель того же размера.
Внешнее смешивание
Сопла внешнего смешивания смешивают жидкости вне сопла.
Для этого типа форсунки может потребоваться больше воздуха, но смешивание и распыление жидкости происходит за пределами форсунки. Если жидкость распыляется с использованием любого газа, который может реагировать с жидкостью, возможно, что реакция может повредить внутреннюю часть сопла. Этот тип сопла наиболее выгоден для жидкости, которая может испаряться внутри смесительной камеры сопла для внутреннего смешивания или с использованием пара для распыления жидкости.Также эта форсунка подходит для распыления вязкой жидкости.
Ротационный (вращающийся диск)
Роторные распылители используют высокоскоростной вращающийся диск, чашку или колесо для распыления жидкости в полый конус. Скорость вращения контролирует размер капли. Распылительная сушка и окраска распылением — наиболее распространенные применения этой технологии.
См .: Форсунки для ULV и CDA
Ультразвуковые
Ультразвуковые форсунки В этом типе распылительных форсунок используется высокочастотная (от 20 кГц до 50 кГц) вибрация для получения почти узкого распределения капель по размеру и распыления жидкости с низкой скоростью. Вибрация пьезоэлектрического кристалла вызывает капиллярные волны на поверхности жидкой пленки сопла.
Control
Каждая форсунка имеет кривую производительности и будет производить капли, размер которых определяется расходом жидкости и газа. Если процесс чувствителен к размеру капель, то управление потоками становится критической проблемой. Без хорошего контроля над расходами жидкости и газа сопло может не генерировать капли требуемого размера. Это может привести к катастрофическому отказу оборудования или может оказать серьезное негативное влияние на процесс.
Материал конструкции
Материал конструкции выбирается в зависимости от свойств распыляемой жидкости и окружающей среды. Форсунки чаще всего изготавливаются из металлов, но также используются пластмассы и керамика. Для распыления суспензии в десульфуризаторе псевдоожиженного газа (FGD) наиболее предпочтительным материалом являются кремниевые сплавы, такие как стеллит, которые являются твердыми, но не такими стойкими к истиранию, как карбид кремния. Для коррозионной стойкости используются такие материалы, как Hastelloy.Износ материала форсунки отрицательно сказывается на распылителях. Они могут образовывать полосы более крупного размера, выходящие из сопла, что может оказать нежелательное влияние на процесс. Например: в градирне для кондиционирования газа на цементном заводе целью распыления жидкости является увлажнение и охлаждение газа перед его поступлением в оборудование для удаления твердых частиц. Для работы этого приложения требуется определенный размер капли. Если размер капель превышает определенный порог, они не испаряются полностью и не охлаждают газ до желаемой температуры.Неиспарившаяся капля упадет на дно башни. Когда запыленные газы попадают в градирню, пыль будет прилипать к влажной поверхности и создаст серьезные проблемы при повышенном техническом обслуживании. Если их не обслужить, они могут даже засорить выпускной газовый канал и нарушить работу установки.
См. Также
Ссылки
- Nasr, Yule and Bending, «Industrial Sprays and Atomization», Springer, 2002, ISBN: 1-85233-611-0
- Lefebvre, Arthur, Atomization and Sprays , Hemisphere, 1989, ISBN 0-89116-603-3
- (ILASS) Институт систем распыления и распыления жидкости
- Распылительные форсунки — водная основа и основание для растворителей — OTSON Technologies Corp
- [1]
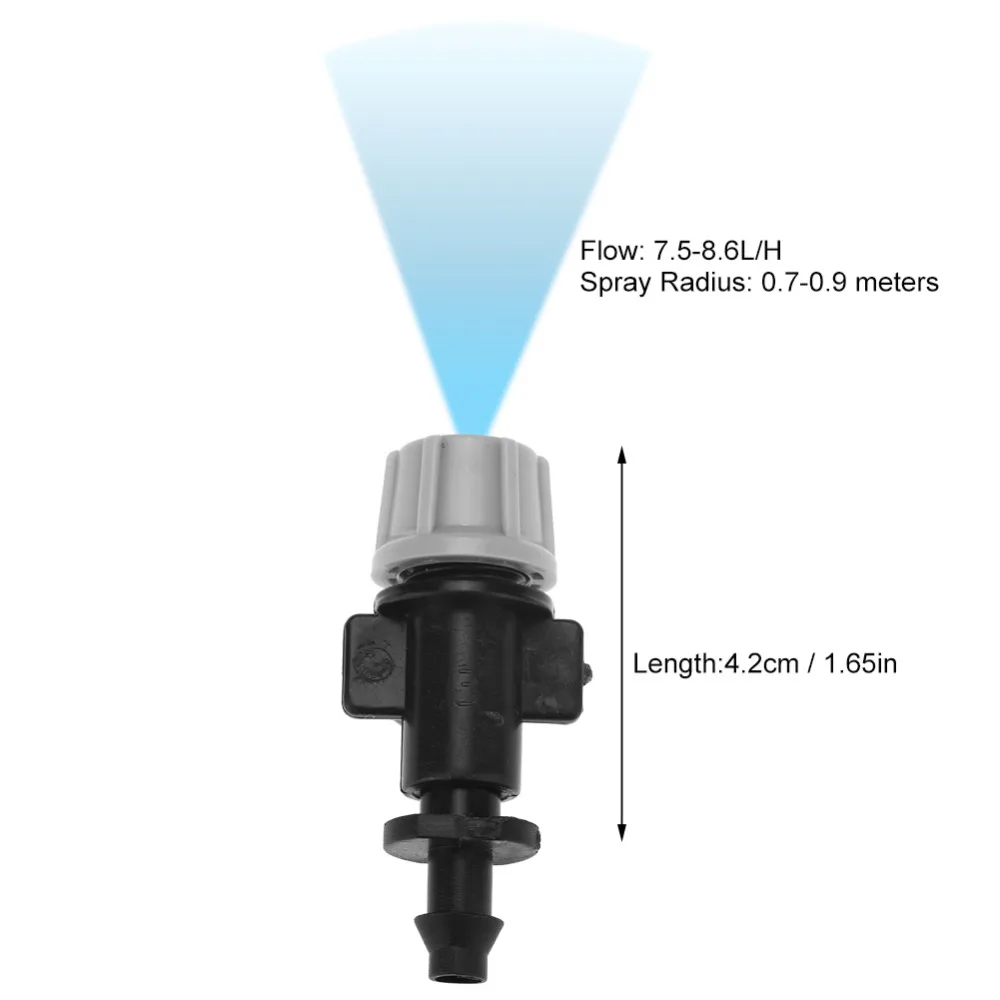