Буксa или осевая коробка что это? Значение слова Буксa или осевая коробка
Значение слова Буксa или осевая коробка по словарю Брокгауза и Ефрона:
Буксa или осевая коробка — как показывает само название — есть ящик, обыкновенно металлический, в котором вращается ось вагона или паровика. Буксы для паровозов бывают двух родов, смотря по тому, будут ли рамы относительно колес внутренние или внешние. По форме своей Б. бывают весьма разнообразны, видоизменяясь сообразно способам смазки. Каждая Б. состоит из трех частей: а) верхней — железной. б) нижней — чугунной и в) средней — бронзового вкладыша, называемого подшипником (см. Подшипник). Верхняя часть вставляется в буксовые челюсти и удерживается закраинами, она имеет два отверстия с трубочками для пропуска смазывающего ось фитиля, и в верхней своей части углубление, в котором помещается смазка. На эту часть Б. обыкновенно опирается стержень подвесной рессоры. В нижней чугунной коробке помещается смазочная щетка, нажимаемая на осевую шейку особою пружиною. В рамах делаются вырезы, обделанные кругом стальными угольниками, называемыми затем челюстями, в которых помещаются Б. Для уменьшения трения делаются на боковых частях Б. бронзовые накладки. Для возможности правильной установки Б. челюсти приделываются к раме так, что с одного бока наугольник укреплен отвесно, а с другого — наклонно настолько, чтобы между ним и Б. можно было положить клин, которым букса укреплена в челюстях. Посредством этих клиньев, изменяя лишь толщину бронзовых накладок, можно всегда правильно установить оси в рамах. Способ смазки букс бывает троякий, сообразно чему и изменяется устройство Б. Из опытов, произведенных на Нижегородской ж. д., оказалось, что наилучшими оказались Б., в которых способ смазки следующий: масло находится в верхней части Б. и опускается на подшипник посредством фитиля, верхний конец которого погружен в масло, а нижний в смазочное отверстие подшипника. Для того чтобы всасывание было хорошее, фитиль не должен быть толстым, дабы не заполнять плотно отверстия.


Расчет зубчатых колес коробки передач на прочность и долговечность
Министерство образования и науки Российской Федерации
Федеральное государственное бюджетное образовательное
учреждение высшего профессионального образования
«Кузбасский государственный технический университет
имени Т. Ф. Горбачева»
А.В. Буянкин
В.Г. Ромашко
ОСНОВЫ КОНСТРУИРОВАНИЯ АВТОМОБИЛЕЙ
(МЕТОДИЧЕСКИЕ УКАЗАНИЯ К ПРАКТИЧЕСКИМ ЗАНЯТИЯМ)
Рекомендовано учебно-методической комиссией направления подготовки бакалавров 190700.62 «Технология транспортных процессов» профилей 190701.62 «Организация перевозок на автомобильном транспорте» и 190709.62 «Организация и безопасность движения» в качестве электронного издания для использования в учебном процессе
Кемерово 2013
ОБЩИЕ ПОЛОЖЕНИЯ
Цель дисциплины «Основы конструирования автомобилей» — дать студентам инженерные знания, необходимые для объективной оценки конструкций автотранспортных средств, их агрегатов и систем. Для этого в данном курсе решаются следующие задачи:
* знакомство с основными требованиями к конструкциям автомобилей, их агрегатов и систем, изучение выходных и оценочных параметров агрегатов и систем;
* изучение условий эксплуатации и нагрузочных режимов агрегатов и систем автомобилей;
* изучение рабочих процессов агрегатов и систем автомобилей, оценка влияния конструктивных и эксплуатационных факторов на рабочие процессы и выходные параметры агрегатов и систем;
* знакомство с основами расчета агрегатов и систем автомобилей на прочность и долговечность.
При изучении данной дисциплины необходимо выделить требования, предъявляемые к конструкции агрегатов и систем автомобилей, и проанализировать, как эти требования выполняются в существующих конструкциях.
Основное внимание следует уделить изучению рабочих процессов и выходных параметров агрегатов и систем автомобилей. При этом необходимо выявить связи между рабочими процессами, нагрузочными режимами и требованиями к конструкции, а также отметить влияние конструктивных и эксплуатационных факторов на рабочие процессы, выходные параметры, надежность и долговечность автомобилей.
Знание теории рабочих процессов и теории прочности при конструировании и оценке эксплуатационных свойств автомобилей, методов и основных принципов расчета деталей и узлов на прочность и долговечность, умение применять их на практике, необходимо для объективной оценки совершенства конструкций автомобилей, правильного выбора типов подвижного состава и их оптимальной эксплуатации в различных условиях.
Проектирование трансмиссии автомобиля обычно осуществляется в такой последовательности: в зависимости от назначения автомобиля определить принципиальную схему трансмиссии, рассмотреть основные характеристики, выбрать принципиальные схемы агрегатов, провести их конструирование и выполнить расчеты на прочность основных деталей. При этом конструктор анализирует существующие конструкции, оценивает их конструктивные, производственные и эксплуатационные достоинства и недостатки, учитывает преемственность, особенности производства и возможности широкой унификации между существующими и проектируемыми образцами.
МЕТОДИЧЕСКИЕ УКАЗАНИЯ
Расчет сцепления с приводом
Сцепление – механизм трансмиссии автомобиля, передающий крутящий момент двигателя и позволяющий кратковременно отсоединить двигатель от ведущих колес и вновь плавно их соединить.
Определение основных параметров и показателей нагруженности сцепления
Выбор размеров сцепления производится из условия передачи максимального крутящего момента двигателя посредством трения с некоторым запасом.
Статический момент трения сцепления , Н×м, определяют по формуле
, (1.1)
где – максимальный крутящий момент двигателя, Н×м; – коэффициент запаса сцепления.
Значение коэффициента запаса сцепления выбирается с учетом неизбежного уменьшения коэффициента трения накладок в процессе эксплуатации, усадки нажимных пружин, наличия регулировки нажимного усилия, числа ведомых дисков. С другой стороны, пиковые нагрузки в трансмиссии, независимо от их происхождения, должны ограничиваться пробуксовыванием сцепления. По этой причине коэффициент запаса сцепления не должен превышать определенного значения.
Средние значения коэффициента запаса сцепления можно принять по рекомендациям [5]:
· для легковых автомобилей – = 1,2 ¸ 1,75;
· для грузовых автомобилей – = 1,5 ¸ 2,2;
· для АТС повышенной проходимости – = 1,8 ¸ 3,0.
Ориентировочно наружный диаметр дисков , см, определяют по формуле
, (1. 2)
где – максимальный крутящий момент двигателя, кг×см; А – эмпирический коэффициент.
Величина эмпирического коэффициента выбирается в зависимости от типа транспортного средства [2]:
· для легковых автомобилей – А= 4,7;
· для грузовых автомобилей –
· для АТС повышенной проходимости – А = 1,9.
При этом внутренний диаметр d, см, фрикционных накладок ориентировочно составляет:
. (1.3)
Рассчитанные величины необходимо привести в соответствие с требованиями ГОСТ 12238 – 76 (таблица 1.1) [5].
Таблица 1.1 – Диаметры фрикционных накладок
D, мм | 180 | 200 | 215 | 240 | 250 | 280 | 300 |
d, мм | 100, 120, 125 | 120, 130, 140 | 140, 150, 160 | 160, 180 | 155, 180 | 165, 180, 200 | 165, 175, 200 |
Продолжение табл. 1.1
D, мм | 325 | 340 | 350 | 380 | 400 | 420 |
d, мм | 185, 200, 220, 230 | 185, 195, 210 | 195, 200, 210, 240, 290 | 200, 220, 230 | 220, 240, 280 | 220, 240, 280 |
Средний радиус дисков , м, определяют по формуле
. (1.4)
Нажимное усилие пружин , Н, рассчитывают по формуле
(1.5)
где – расчетный коэффициент трения; i – число пар трения.
Расчетный коэффициент трения зависит от ряда факторов: параметров фрикционных материалов, состояния и относительной скорости скольжения поверхностей трения, давления, температуры.
Расчетный коэффициент трения – = 0,25 ¸ 0,3 [3].
Число пар трения [5]:
· для однодисковых сцеплений – i = 2;
· для двухдисковых сцеплений – i = 4.
Для сцепления с периферийными цилиндрическими пружинами (рис. 1.1) нажимное усилие пружин , Н, рассчитывают по формуле
(1.6)
где – диаметр проволоки пружины, м; – напряжение кручения пружины, Па; – число нажимных пружин; – диаметр пружины, м.
Рисунок 1.1 – Схема цилиндрической нажимной пружины
Обычно сцепление проектируется так, чтобы при выключении нажимное усилие пружин увеличивалось на 20 %, то есть:
(1.7)
где – усилие пружины при выключении сцепления, Н; – максимальное напряжение кручения, Па.
Максимальное напряжение кручения – = 700 ¸ 900 МПа [4].
Число пружин выбирается в зависимости от наружного диаметра фрикционных накладок (таблица 1.2) [2] и должно быть кратно числу рычагов выключения.
Таблица 1.2 – Число нажимных пружин
D, мм | 180 ¸ 250 | 280 | 300; 325 | 350; 380 | 400; 420 |
6 | 9 | 12 | 16 | 28 |
Нагрузка на пружину не должна превышать = 800Н [4].
Принимается = 3 ¸ 10 [4].
После выбора отношения по формуле определяются диаметры проволоки и пружины, после чего согласовываются в соответствии с [5]:
– 1,0; 1,2; 1,6; 2,0; 2,5; 3,0; 4,0; 5,0; 6,0; 7,0; 8,0; 9,0; 10,0.
– 16,0; 18,0; 20,0; 22,0; 25,0; 28,0; 32,0; 36,0; 40,0; 45,0; 50,0; 55,0; 60,0; 70,0.
После согласования уточняют нажимное усилие пружин по формуле (1.6).
Диафрагменная пружина (рисунок 1.2) представляет собой пружину Бельвиля, модифицированную для использования в автомобильных сцеплениях.
Рисунок 1. 2 – Расчетная схема диафрагменной пружины
Нажимное усилие , Н, диафрагменной пружины определяют по формуле
, (1.8)
где Е – модуль упругости первого рода, Па; d – толщина диафрагменной пружины, м; – перемещение пружины в месте приложения силы, действующей со стороны ведомого диска, м; k1, k2 – коэффициенты; h – высота сплошного кольца диафрагменной пружины, м; – коэффициент Пуассона; – наружный диаметр сплошного кольца диафрагменной пружины, м.
Модуль упругости 1-го рода – Е = 2·105 МПа [4].
Толщина диафрагменной пружины – d = 2,0 ¸ 2,5 мм [4].
Перемещение пружины в месте приложения силы – = 1,5 ¸ 2,0 мм [2].
Коэффициент Пуассона = 0,25 [4].
Коэффициенты определяют по формулам (1.9), (1.10):
, (1. 9)
где – внутренний диаметр сплошного кольца диафрагменной пружины, м.
Поскольку в расчетах можно принять , то из рекомендуемого соотношения = 1,2 ¸ 1,5 [5] можно найти внутренний диаметр сплошного кольца.
, (1.10)
где – средний диаметр сплошного кольца диафрагменной пружины, м.
Средний диаметр , м, сплошного кольца диафрагменной пружины можно приближенно вычислить по формуле
. (1.11)
Усилие при выключении , Н, отличается от нажимного усилия передаточным числом диафрагменной пружины:
, (1.12)
где – внутренний диаметр лепестков диафрагменной пружины, м.
Внутренний диаметр лепестков , м, диафрагменной пружины можно определить из рекомендованного соотношения [4]:
2,5.
Высоту сплошного кольца диафрагменной пружины можно найти, задаваясь значением из рекомендованного соотношения [4]:
= 1,5 ¸ 2,0.
Отношение высоты сплошного кольца диафрагменной пружины к ее толщине определяет нелинейность пружины. При 1,6 на характеристике пружины имеется большая область с постоянной осевой силой; при 2,8 возможно «выворачивание» пружины.
Давление на фрикционные накладки , Па, рассчитывают по формуле
, (1.13)
где F – площадь поверхности одной стороны фрикционной накладки, м2.
Допустимые давления на фрикционные накладки – [ ] = 0,15 ¸ 0,25 МПа [4].
Меньшие значения имеют сцепления грузовых автомобилей и автобусов или автомобилей, работающих в тяжелых дорожных условиях; большие значения – сцепления легковых автомобилей.
К показателям нагруженности деталей сцепления относятся удельная работа буксования (отражающая также износостойкость сцепления) и нагрев деталей сцепления при одном трогании с места.
Удельную работу буксования сцепления , Дж/м2, рассчитывают по формуле
, (1. 14)
где – работа буксования, Дж.
Работу буксования , Дж, определяют по формуле
, (1.15)
где – момент инерции приведенного к коленчатому валу двигателя маховика, заменяющего поступательно движущуюся массу автомобиля, кг×м2; – угловая скорость коленчатого вала, рад/с; – момент сопротивления движению автомобиля, приведенный к коленчатому валу двигателя, Н×м.
При определении работы буксования следует иметь в виду, что формула (1.15) выведена при следующих допущениях:
· для исключения влияния водителя предполагается, что сцепление включается мгновенно;
· угловая скорость коленчатого вала двигателя в процессе включения постоянна;
· крутящий момент двигателя, равный передаваемому сцеплением моменту, растет пропорционально времени;
· момент сопротивления движению – величина постояная.
Такая идеализация процесса включения сцепления позволяет проводить лишь ориентировочные расчеты. Для повышения точности результатов следует учитывать упругие свойства трансмиссии как колебательной системы и изменение переменных, входящих в формулу (1.15) в реальных условиях эксплуатации.
Момент инерции условного маховика , кг×м2, заменяющего собой поступательно движущуюся массу автомобиля, рассчитывают по формуле
, (1.16)
где – момент инерции маховика двигателя, кг×м2; – момент инерции условного маховика, приведенного к ведущему валу коробки передач, кг×м2.
Величины момента инерции маховиков приведены в таблице 1.4 [6].
Таблица 1.4 – Момент инерции маховика двигателя
Автомобиль | ЗАЗ-968 | ВАЗ-2101 | ВАЗ-2121 | Москвич-2140 | ГАЗ-24 |
, кг·м2 | 0,118 | 0,130 | 0,130 | 0,170 | 0,310 |
Продолжение табл. 1.4
Автомобиль | УАЗ-469 | РАФ-2203 | ПАЗ-3201 | ЛиАЗ-677 | ЛАЗ-695Е |
, кг·м2 | 0,360 | 0,314 | 0,510 | 1,070 | 0,991 |
Продолжение табл. 1.4
Автомобиль | ЛАЗ-699Н | ГАЗ-52 | ГАЗ-3307 | ЗИЛ-431410 | ЗИЛ-133 |
, кг·м2 | 1,740 | 0,491 | 0,510 | 0,991 | 0,991 |
Продолжение табл. 1.4
Автомобиль | КамАЗ-5320 | Урал-375 | КрАЗ-257 | МАЗ-5551 | МАЗ-5432 |
, кг·м2 | 2,070 | 1,740 | 4,61 | 2,60 | 4,61 |
Момент инерции условного маховика , кг×м2, приведенного к ведущему валу коробки передач, рассчитывают по формуле
, (1. 17)
где – полная масса автомобиля, кг; – радиус качения колеса, м; – передаточное число главной передачи; – передаточное число первой ступени коробки передач.
Угловую скорость коленчатого вала двигателя , рад/с, для автомобилей с бензиновыми двигателями рассчитывают по формуле
, (1.18)
где – угловая скорость при максимальном крутящем моменте, рад/с.
Для автомобилей с дизелями угловую скорость коленчатого вала двигателя , рад/с, определяют по формуле
, (1.19)
где – угловая скорость при максимальной мощности, рад/с.
Угловую скорость коленчатого вала двигателя , рад/с, определяют по формуле
, (1.20)
где – частота вращения коленчатого вала двигателя, об/мин.
Момент сопротивления движению автомобиля, приведенный к коленчатому валу двигателя , Н×м, рассчитывают при допущении о равенстве радиусов качения всех колес автомобиля по формуле
, (1. 21)
где g – ускорение свободного падения, м/с2; – коэффициент общего дорожного сопротивления; – КПД трансмиссии.
Ускорение свободного падения – g = 9,8 м/с2 [5].
Коэффициент общего дорожного сопротивления – = 0,02 [4].
КПД механической трансмиссии принимают согласно данным таблицы 1.5 [5] в зависимости от типа АТС и типа главной передачи.
Таблица 1.5 – КПД механической трансмиссии
Легковые АТС | Грузовые АТС и автобусы | Много- приводные АТС | ||
классической компоновки | передне-приводные | с одинарной главной передачей | с двойной главной передачей | |
0,92 | 0,95 | 0,9 | 0,86 | 0,84 |
Допустимая удельная работа буксования [4]:
· для легковых автомобилей – [ ] = 50 ¸ 70 Дж/см2;
· для грузовых автомобилей – [ ] = 15 ¸ 120 Дж/см2;
· для автопоездов – [ ] = 10 ¸ 40 Дж/см2.
При определении теплового режима сцепления рассчитывается нагрев ведущего диска. Маховик имеет значительно большую массу, чем нажимной диск, и поэтому температура его нагрева сравнительно невелика.
При расчете нагрева ведущего диска принимается допущение, что теплопередача в окружающую среду отсутствует и вся работа буксования используется на нагрев диска.
Нагрев ведущего диска , °С, при одном трогании с места рассчитывают по формуле
, (1.22)
где – доля теплоты, поглощаемая диском; – масса нажимного диска, кг; – удельная теплоемкость стали, Дж/(кг×град).
Доля теплоты, поглощаемая диском [4]:
· для ведущего диска однодискового сцепления и среднего диска двухдискового – = 0,5;
· для наружного нажимного диска двухдискового сцепления – = 0,25.
Радиальные размеры дисков выбираются, исходя из размеров фрикционных накладок. Толщина нажимного диска , м, предварительно принимается в зависимости от наружного диаметра накладок и затем уточняется по результатам теплового расчета сцепления:
. (1.23)
Удельная теплоемкость стали – = 481,5 Дж/(кг×град) [5].
Плотность стали – = 7600 ¸ 7800 кг/м3 [5].
Допустимый нагрев нажимного диска – [ ] = 10 ¸ 15 °С [4].
Полученная расчетная температура является условной (определение ее проведено при одном трогании автомобиля с места) и используется при сравнительной оценке конструкций сцеплений различных типов. В действительности же процесс нагрева дисков значительно сложнее, и поэтому температура деталей сцепления в процессе работы автомобиля значительно выше.
При выборе основных параметров сцеплений и их приводов могут быть использованы данные таблицы 1.6 [5].
Расчет привода сцепления
Удобство управления сцеплением обеспечивается правильным выбором передаточного числа привода, чтобы иметь:
1. Оптимальную величину перемещения педали, не более [5]:
· для легковых автомобилей – = 160 мм;
· для грузовых автомобилей – = 190 мм.
2. Максимальную величину усилия на педали, не более [3]:
· сцепления с усилителем – = 150 Н;
· сцепления без усилителя – = 250 Н.
Механические приводы (рисунок 1.3, а) в настоящее время применяются только на легковых автомобилях особо малого класса; на грузовых автомобилях, автобусах и легковых автомобилях малого класса и выше применяют гидропривод (рисунок 1.3, б).
Таблица 1.6 – Основные параметры фрикционных дисковых сцеплений
Параметр, размерность | МеМЗ-968 | АЗЛК-412 | ВАЗ-2101 | ВАЗ-2103 | ВАЗ-2121 | ГАЗ-24 | ГАЗ-53 | ЗИЛ-130 | ЯМЗ | ||
14 | 236К | 238 | |||||||||
1 | 2 | 3 | 4 | 5 | 6 | 7 | 8 | 9 | 10 | 11 | 12 |
Максимальный крутящий момент двигателя, Н·м | 74,5 | 111,8 | 87,3 | 105,9 | 121,6 | 186,3 | 284,4 | 402,1 | 637,4 | 666,9 | 882,6 |
Число ведомых дисков | 1 | 1 | 1 | 1 | 1 | 1 | 1 | 1 | 2 | 2 | 2 |
Коэффициент запаса сцепления | 2,08 | 1,57 | 2,05 | 1,62 | 1,44 | 1,55 | 1,81 | 2,15 | 2,0 | 2,35 | 2,14 |
Допустимая частота вращения, об/мин | 4400 | 5800 | 7000 | 7000 | 7000 | 4500 | 3200 | 3200 | 2600 | 2100 | 2100 |
Фрикционные накладки, мм: наружный диаметр внутренний диаметр толщина | 190 130 3,5 | 204 146 3,3 | 200 142 3,3 | 200 142 3,3 | 200 130 3,3 | 225 150 3,5 | 300 164 4,0 | 342 186 4,0 | 350 200 4,5 | 400 220 4,0 | 400 220 4,0 |
Максимальный диаметр кожуха сцепления, мм | 245 | 270 | 263 | 263 | 263 | 279 | 352 | 400 | 410 | 464 | 460 |
Число рычагов выключения | 3 | 181 | 181 | 181 | 181 | 3 | 3 | 4 | 4 | 4 | 4 |
Нажимные пружины: число усилие в выключенном сцеплении, кН усилие во включенном сцеплении, кН радиус установки, мм | 6 4,07 3,72 80 | 1 – – 1942 | 1 – – 1952 | 1 – – 187,52 | 1 – – 187,52 | 9 2 5,50 5,14 89 | 12 8,39 7,54 108 | 16 12,00 10,90 126 | 12 13,30 11,18 125 | 14 2 11,84 11,06 168 и 128 | 12 2 13,78 12,90 168 и 128 |
Продолжение табл. 1.6
1 | 2 | 3 | 4 | 5 | 6 | 7 | 8 | 9 | 10 | 11 | 12 |
Параметры нажимной пружины: жесткость, Н/мм диаметр проволоки, мм средний диаметр, мм усилие в рабочем состоянии, Н число рабочих витков | 40,2 4,0 25 623 4,0 | – 2,293 – 33404 – | – 2,23 – 34944 – | – 2,23 – 30894 – | – 2,323 – 36204 – | 5,7 и 10,1 3,0 28,5 и 21,5 257 и 314 7 и 9,5 | 28,5 4,2 24,8 628 7 | 38,1 4,5 25,5 682 8,5 | 21,2 5,5 38,5 931 7,5 | 14,4 4,5 31,5 461 9 | 14,4 4,5 31,5 461 9 |
Давление на фрикционные накладки, МПа | 0,235 | 0,210 | 0,224 | 0,198 | 0,200 | 0,233 | 0,153 | 0,165 | 0,167 | 0,140 | 0,115 |
Расчетный коэффициент трения | 0,3 | 0,3 | 0,3 | 0,3 | 0,3 | 0,3 | 0,3 | 0,3 | 0,22 | 0,25 | 0,25 |
Передаточные числа: рычагов вилки | 4,5 1,69 | 3,5 1,8 | 3,5 2,5 | 2,43 2,45 | 2,43 2,45 | 3,79 1,44 | 4,68 1,68 | 5,33 2,12 | 4,85 1,67 | 4,7 ¸ 5,4 1,86 | 4,7 ¸ 5,4 1,86 |
Ход муфты выключения, мм: холостой рабочий | 2 ¸ 3 10 | 4,5 ¸ 5,5 7,1 | 2 8 | 2 8 ¸ 9 | 2 8 ¸ 9 | 2,5 10 | 4 11,7 | 3 ¸ 4 9,6 | 3,6 16 | 3,6 15 | 3,6 16 |
Масса сцепления (без маховика, картера и механизма привода), кг | 4,1 | 6,1 | 4,38 | 5,52 | 5,55 | 14,0 | 20,0 | 20,5 | – | 63,8 | 64,2 |
Примечание:
1число лепестков диафрагменной пружины.
2диаметр приложения нагрузки диафрагменной пружины.
3толщина диафрагменной пружины.
4рабочее усилие на нажимном диске.
а) б)
Рисунок 1.3 – Схемы приводов сцепления:
а – механический привод; б – гидравлический привод
При расчете привода рассчитываются его передаточное число, усилие на педали и ход педали.
Общее передаточное число привода от педали до нажимного диска можно определить по формуле
, (1.24)
где – передаточное число педали сцепления; – передаточное число вилки выключения; – передаточное число рычагов выключения; a, b – плечи педали; c, d – плечи вилки выключения; е, f – плечи рычагов.
Полный ход педали механического привода складывается из свободного хода педали, рабочего хода и упругих деформаций элементов привода. Полный ход педали , мм, механического привода рассчитывается по формуле
, (1.25)
где – свободный ход педали, мм; – рабочий ход педали, мм; d – зазор в механизме выключения (между муфтой и рычагами выключения), мм; DS – ход нажимного диска, мм.
Величина зазора в механизме выключения [2]:
· сцепления с периферийными цилиндрическими пружинами – d = 1,5 ¸ 2,0 мм;
· сцепления с центральной диафрагменной пружиной – d = 3,5 ¸ 4,0 мм.
Ход нажимного диска [5]:
· однодисковых сцеплений – DS = 1,5 ¸ 2,0 мм;
· двухдисковых сцеплений – DS = 2,4 ¸ 2,8 мм.
Выполненные конструкции приводов имеют обычно следующие значения передаточных чисел:
= 30 ¸ 45; = 3,8 ¸ 5,5; = 1,4 ¸ 2,2 [5].
Передаточное число гидропривода определяют по формуле
, (1. 26)
где – диаметр главного цилиндра, мм; – диаметр исполнительного цилиндра, мм.
Диаметры главного и исполнительного цилиндров выполняются обычно равными:
1,0.
Полный ход педали сцепления при гидроприводе рассчитывают аналогично (формула (1.25)).
Усилие на педали , Н, определяют по формуле
, (1.27)
где – КПД привода сцепления.
КПД привода сцепления [3]:
· механического привода – = 0,7 ¸ 0,8;
· гидравлического привода – = 0,8 ¸ 0,9.
Если усилие на педали больше допустимого, то в привод необходимо устанавливать усилитель.
2 Расчет коробки передач
Коробка передач – механизм трансмиссии автомобиля, предназначенный для изменения силы тяги на ведущих колесах путем изменения передаточного числа, длительного отсоединения двигателя от ведущих колес, а также обеспечения движения автомобиля задним ходом.
2.1 Определение основных параметров коробки передач
Основные размеры коробки передач определяют после выбора ее схемы (рисунок 2. 1).
а) б)
Рисунок 2.1 – Принципиальная кинематическая схема четырехступенчатой коробки передач:
а – двухвальной, б – трехвальной;
1 – ведущий вал, 2 – ведомый вал, 3 – промежуточный вал.
В первую очередь оценивается межосевое расстояние.
Межосевое расстояние А, мм, приближенно можно определить по формуле:
, (2.1)
где а – эмпирический коэффициент.
Величина эмпирического коэффициента зависит от типа транспортного средства [3]:
· для легковых автомобилей – a = 14,5 ¸ 16,0;
· для грузовых автомобилей – a = 17,0 ¸ 19,5;
· для транспортных средств с дизелями – a = 20,5 ¸ 21,5.
Для коробок передач легковых автомобилей:
А = 65 ¸ 80 мм [5].
Для коробок передач грузовых автомобилей рекомендуется следующий рациональный ряд межосевых расстояний (таблица 2.1) [5].
Таблица 2.1 – Рекомендуемые значения параметров коробок передач
, Н·м | 170 | 260 | 340 ¸ 420 | 700 ¸ 850 | 900 ¸ 1150 |
А, мм | 85 | 105 | 125 | 140 | 160 |
Число передач | 4 | 5 | 5 | 5 | 10 |
Затем устанавливается нормальный модуль зубчатых колес. Нормальный модуль определяется из условий изгибной прочности на усталость или статической прочности при действии максимального момента.
При выборе модуля необходимо учитывать, что его уменьшение при увеличении ширины зубчатого венца зубчатых колес приводит к уменьшению уровня шума. Для уменьшения массы коробки передач следует увеличивать модуль путем уменьшения ширины венцов (при том же межосевом расстоянии).
Для грузовых автомобилей уменьшение уровня шума имеет меньшее значение, чем для легковых, и следует большее внимание уделять уменьшению массы зубчатых передач.
Нормальный модуль , мм, определяют по формуле:
, (2.2)
где d – диаметр начальной окружности, мм; b – угол наклона спирали зубьев, град; Z – число зубьев зубчатого колеса.
Торцевой модуль , мм, рассчитывают по формуле:
. (2.3)
Как правило, модуль принимается одинаковый для всех зубчатых колес коробки передач, что дает некоторые технологические преимущества. Величина модуля зависит от передаваемого момента и типа транспортного средства (таблица 2.2) [4].
Таблица 2. 2 – Значения нормального модуля зубчатых колес коробок передач
, Н×м | , мм | Тип транспортного средства |
100 ¸ 200 | 2,25 ¸ 2,75 | Легковые автомобили особо малого и малого класса |
200 ¸ 400 | 2,75 ¸ 3,5 | Легковые автомобили среднего класса и грузовые малой грузоподъемности |
400 ¸ 600 | 3,5 ¸ 4,25 | Грузовые автомобили средней грузоподъемности |
Продолжение табл. 2.2
600 ¸ 800 | 4,25 ¸ 5,0 | Грузовые автомобили большой грузоподъемности |
800 ¸ 1000 | 5,0 ¸ 6,0 | Первая передача в коробках передач грузовых автомобилей большой грузоподъемности при малом числе зубьев шестерни (Z=12) |
Стандартные значения нормального модуля, мм [5]:
= 1,0; 1. 25; 1,5; 2,0; 2,5; 3,0; 4,0; 5,0; 6,0; 8,0; и т. д.
Большинство зубчатых колес в коробках передач выполняют косозубыми для уменьшения шума при работе и повышения прочности. При выборе угла наклона учитывают ряд факторов: необходимость обеспечения достаточного осевого перекрытия зубьев; ограничение осевой силы, действующей на подшипники валов; необходимость выдержать заданное межосевое расстояние; условие уравновешивания осевых сил на промежуточном валу (для трехвальных коробок передач).
Угол наклона линии зубьев [5]:
· для зубчатых колес двухвальных коробок передач легковых автомобилей – b = 20 ¸ 25°;
· для зубчатых колес трехвальных коробок передач легковых автомобилей – b = 22 ¸ 34°;
· для зубчатых колес коробок передач грузовых автомобилей – b = 18 ¸ 26°.
Рабочую ширину венцов зубчатых колес коробки передач b, мм, можно определить из соотношения:
. (2. 4)
При определении ширины венцов зубчатых колес следует учитывать, что при применении зубчатых колес большей ширины повышаются требования к жесткости валов коробки передач.
Число зубьев колес определяется по известному передаточному числу коробки передач (при условии равенства модулей).
Так, например, для второй передачи трехвальной четырехступенчатой коробки передач (рисунок 2.1, б):
, (2.5)
где – передаточное число привода промежуточного вала; – передаточное число зубчатой пары второй передачи.
В обозначении числа зубьев принято следующее: нечетные индексы относятся к ведущим зубчатым колесам, четные – к ведомым. Меньшее из пары зубчатых колес называют шестерней, большее – колесом.
Число зубьев шестерни первичного вала = 17 ¸ 27 [5], передаточное число привода промежуточного вала = 1,6 ¸ 2,5 [2].
Задаваясь числом зубьев шестерни первичного вала и передаточным числом привода промежуточного вала, можно определить число зубьев зубчатого колеса привода промежуточного вала.
После этого необходимо проверить межосевое расстояние по числу зубьев:
. (2.6)
При определении числа зубьев необходимо учитывать, что нечетное число суммы зубьев передачи предпочтительнее, так как уменьшается возможность получения суммы чисел зубьев с общим множителем, что приводит к неравномерности износа зубьев.
Путем варьирования углом наклона спирали зубьев в заданных пределах необходимо добиться точного совпадения определяемого межосевого расстояния с вычисленным по формуле (2.1). В крайнем случае можно изменять модуль зубчатых колес.
Передаточное число зубчатой пары , можно определить из формулы (2.5)
. (2.7)
Число зубьев зубчатого колеса на промежуточном валу можно рассчитать по формуле
, (2.8)
где – угол наклона спирали зубьев для данной зубчатой пары.
Затем определяется число зубьев шестерни на ведомом валу, после чего необходимо проверить межосевое расстояние по числу зубьев рассчитанной зубчатой пары. При этом необходимо помнить, что число зубьев зубчатого колеса должно быть целым числом. После определения числа зубьев для каждой пары зубчатых колес необходимо уточнить передаточные числа коробки передач на каждой передаче.
Число зубьев шестерни первой передачи, располагающейся на промежуточном валу коробки передач, выбирается минимальным – = 13 ¸ 17 [3], что обусловливается применением шестерни первичного вала с достаточно большим диаметром (для размещения в ней подшипника вторичного вала).
Передаточное число пары зубчатых колес должно быть [2]:
· на низшей передаче – 3,5 ¸ 4,0;
· на высшей – 0,6 ¸ 0,8.
Для двухвальной коробки передач расчет ведется аналогично, однако в формулах отсутствует передаточное число привода промежуточного вала и по формуле (2.8) определяется число зубьев зубчатых колес с четными индексами.
При выборе основных параметров зубчатых колес коробки передач могут быть использованы данные таблицы 2.3 [5].
Расчет зубчатых колес коробки передач на прочность и долговечность
При расчете коробки передач расчетный момент определяется по максимальному крутящему моменту двигателя. Расчет зубчатых колес производится: на прочность – по напряжениям изгиба зубьев и на долговечность – по контактным напряжениям.
Напряжение изгиба , Па, рассчитывают по формуле
, (2.9)
где Р – окружное усилие, Н; y – коэффициент формы зуба.
Окружное усилие Р, Н, рассчитывают по формуле
, (2.10)
где – передаточное число до рассчитываемого зубчатого колеса; r – радиус начальной окружности зубчатого колеса, м.
Таблица 2.3 – Параметры зубчатых колес механических ступенчатых коробок передач
Шестерни передачи | Межосевое расстояние, мм | Число зубьев ведущих шестерен | Число зубьев ведомых колес | Рабочая ширина венцов, мм | Нормальный модуль, мм | Угол наклона линии зубьев, град | |
1 | 2 | 3 | 4 | 5 | 6 | 7 | |
ЗАЗ-968 | |||||||
Первой Второй Третьей Четвертой | 72,88 | 10 17 22 27 | 38 36 31 26 | 13,0 14,0 14,0 15,0 | 2,75 2,50 2,50 2,50 | 25 24 24 24 | |
ВАЗ-2101 | |||||||
Привода промежуточного вала Первой Второй Третьей | 68,00 | 17 15 20 24 | 29 33 27 21 | 16,0 15,5 15,0 16,0 | 2,50 | 31 27 29 31 | |
ГАЗ-24 | |||||||
Привода промежуточного вала Первой Второй Третьей | 77,00 | 16 15 20 25 | 29 29 25 20 | 15,5 17,5 16,5 16,5 | 2,75 3,00 3,00 2,75 | 34º22’31» 29º8’42» 29º8’42» 34º22’31» | |
ГАЗ-53А | |||||||
Привода промежуточного вала Первой Второй Третьей | 110,63 | 17 14 25 34 | 41 38 32 24 | 20,0 24,0 20,0 22,0 | 3,50 4,25 3,50 3,50 | 23º26’5» 0 23º26’5» 23º26’5» | |
ЗИЛ-130 | |||||||
Привода промежуточного вала Первой Второй Третьей Четвертой | 123,25 | 20 13 22 31 38 | 43 45 42 33 26 | 25,0 30,0 29,0 28,0 26,0 | 3,50 4,25 3,50 3,50 3,50 | 24º40’15» 0 24º40’15» 24º40’15» 24º40’15» | |
Продолжение табл. 2.3
1 | 2 | 3 | 4 | 5 | 6 | 7 |
ЯМЗ-238А | ||||||
Привода промежуточного вала Первая Второй Четверто |
Коробка буксовая — Энциклопедия по машиностроению XXL
Коробка буксовая 729, XV. Коробка огневая 207, XI. [c.484]Поверхности трения расположены в буксовой коробке и смазочный материал последней используется для осевого упора [c.577]
Боковые брусья выполнены в виде открытой снизу коробки, внутреннее пространство которой используется для размещения элементов рессорного подвешивания. В нижней части боковина имеет приливы 9, образующие буксовые проемы рамы и являющиеся буксовыми челюстями, которые сами вьшолняют роль буксовых направляющих. Снизу они имеют выступы (каблучки) для крепления. струнок. На раме смонтированы кронштейны для подвески рычажной тормозной передачи, приливы 10 для установки коленчатого вала главного тормозного рычага и кронштейны 8 для укрепления продольного балансира рессорного подвешивания.
[c.16]
Верхняя обойма имеет гнездо для размещения хомута листовой рессоры, а в нижней части находятся цилиндрические шипы и гнезда для фиксации пружин. Нижняя обойма имеет сверху шипы и гнезда, одинаковые с верхней обоймой, а в нижней части — ножки, опирающиеся на буксовую коробку роликовой буксы. Обоймы в средней части снабжены ограничителями хода пружин, не допускающими полного сжатия рессор, для предохранения их от поломок. [c.45]
Подшипник, передавая нагрузку от буксовой коробки на шейку оси, обычно выступает из буксы на 2 — 3 жж в обе стороны во избежание трения ступицы колеса [c.422]
Осевое масло Л и 3 Машинное масло Л 610-48 1077-42 Буксовые направляющие и скользуны, пяты тележек, опорная коробка.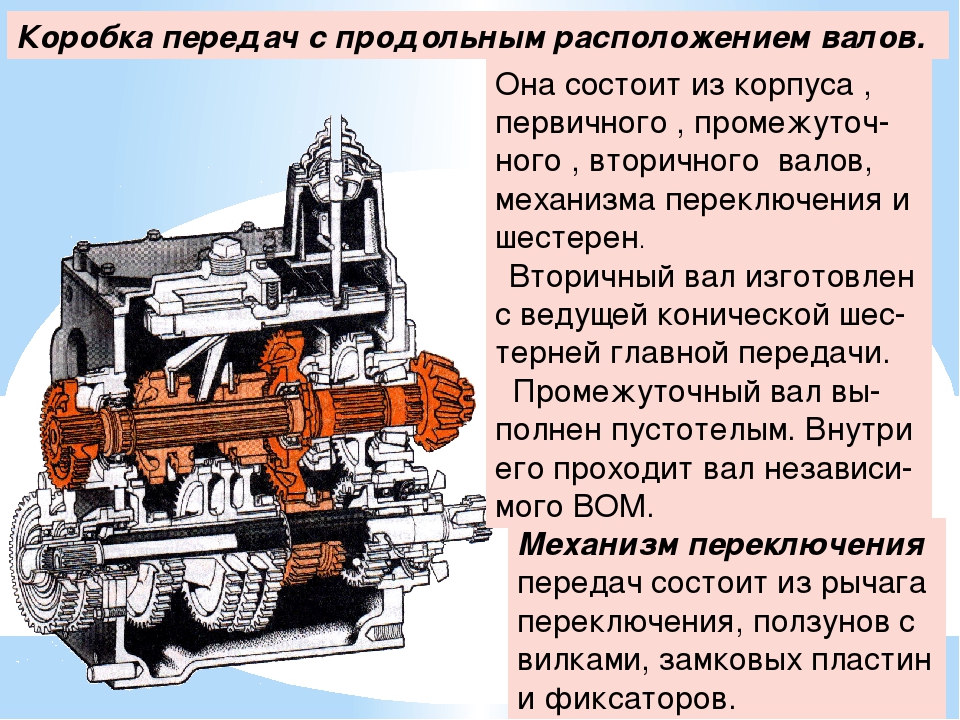
У букс скользяш,его трения (фиг. 57 и 67—69) внутри буксовой коробки—корпуса буксы 72 помещается бронзовый подшипник (вкладыш) 75 (фиг. [c.51]
С наружной торцовой стороны букса закрывается крышкой 14 (см. фиг. 57 и 68) из листовой стали толщиной 4— мм, которая под действием пружины плотно прилегает к буксовой коробке эта крышка предохраняет буксу от попадания в неё пыли, грязи и влаги. [c.52]
Толщина заднего бурта буксовой коробки без наличника [c.602]
Ширина гнезда для подрессорной стойки в буксовой коробке или вкладыше [c.602]
Глубина гнезда для подрессорной стойки в планке(вкладыше) или буксовой коробке, не оборудованной вкладышами [c.602]
Толщина верхней части буксовой коробки от места соприкосновения буксового подшипника до дна гнезда для подрессорной стойки
[c. 602]
Паровозные буксы составляются следующими тремя основными. частями корпусом, подшипником и нижней (смазочной) коробкой. В буксах наших старых типов паровозов имеются еще и бронзовые наличники, укрепляемые с боков корпуса и служащие для уменьшения трения между корпусом буксы и буксовыми направляющими. [c.503]
Сразу за подступичной частью оси колесной пары расположена буксовая шейка 7, на которую опирается подшипник, заключенный в коробку, предохраняющую его от пыли, обеспечивающую смазывание и передающую через него нагрузку на ось эту коробку называют буксой. Для ограничения разбега подшипника вдоль оси колесной пары ее средняя часть о на паровозе отделена от шейки буртом. Как у этого бурта, так и у хорошо видных на рисунке разделительных мест на пальце кривошипа между центровой шейкой и посадочной частью пальца и между центровой и поршневой шейками может произойти концентрация напряжений вызывающая появление микротрещин, которые развиваются в крупные трещины.

Тележки оборудованы двойным рессорным подвешиванием. На буксовых коробках установлены листовые рессоры, а на подвесках рессор надеты цилиндрические пружины. С помощью кронштейнов, укрепленных на раме, тележка опирается на цилиндрические пружины, от которых через подвески и листовые рессоры нагрузка передается на буксы. Буксы тележки оборудованы подшипниками скольжения. [c.194]
Подготовка рамы к заварке трещины (помимо разделки последней) включает в себя еще ряд операций, которые обеспечивают хорошее качество произведенной работы и неизменность конфигурации рамы. В качестве примера дается описание подготовки к заварке сквозной трещины в буксовом вырезе (рис. 210). Ставят на место подбуксовую связь 2 и нормально закрепляют ее. Против каблучков рамы устанавливают под подбуксовой связью домкраты-тумбочки 1 и слегка поджимают ими раму, чтобы предотвратить ее прогиб при подогреве. Примерно на середине высоты распирают вырез домкратом-распоркой. На подбуксовую связь надевают железную дырчатую коробку с подожженным древес-
[c.326]
При нижнем рессорном подвешивании могут иметь место растрескивание и излом корпуса букс от ударов хомута рессоры о подбуксовую связь, от задевания хвостовика буксового клина о заплечик рессорной серьги, а также проушины буксы о выступ хвостовика буксового клина или о подбуксовую связь и т. п. Все это объясняется значительной выработкой и уменьшением размера буксового подшипника по вертикали, вследствие чего и сама букса, и соединенные с ней части опускаются. Несвоевременное крепление буксового клина и большая слабина подбуксовой коробки в корпусе буксы могут тоже вызвать излом корпуса буксы. [c.341]
Обнаружение неисправностей. Во всех случаях выкатки колесной пары из-под паровоза ее буксы тш,ательно осматривают с применением магнитной дефектоскопии. Одновременно проверяют плотность посадки подшипника в буксе и при обнаружении слабины его выпрессовывают. Во избежание появления трещин и надрывов в корпусе буксы выбивать подшипник кувалдой или превышать установленное давление запрессовки категорически запрещено. Попутно проверяют состояние баббитовой заливки, замеряют толщину стенок буксы, осматривают крепление смазочных трубок и проверяют плотность резервуара для смазки, устанавливают, нет ли задиров или ненормальной выработки буксовых наличников и их толщину, выявляют, не чрезмерна ли слабина подбуксовой коробки в корпусе буксы.
[c.341]
Ползун, навар, неравномерный прокат можно обнаружить по следующим признакам отсутствует буксовая крышка или оборваны ее петли наличие меловых разметок на вагоне о частой смене подшипников нарушено торцовое крепление роликовой буксы поврежденьр или отсутствуют резиновые и волокнитовые втулки в узлах подвесок башмаков имеется овальный износ отверстий отсутствуют валик подвески башмака, шплинты имеются срезанные шплинты металлический блеск на шайбах валиков рычажной передачи тележки повреждена резьба триангеля и гайка крепления наконечника триангеля металлический блеск болтов коробки скользуна ослабли заклепки фрикционных планок тележки ЦНИИ-ХЗ-0 и имеется металлический блеск на них.
[c.110]
Колесные скаты состоят из осей с напрессованными на них колесами. Оси (см.) бывают прямые, одно- и двухколенчатые. Число спиц равно числу дм. диаметра колеса. Диаметр втулки в 1,6—2,0 раза больше диаметра подступичной части оси. Толщина бандажей в СССР б. ч. 75 мм, а при давлениях от оси на рельс свыше 20 ш доходит до 90 мм и более. Предельный износ бандажей допускается у нас до толщины 40 мм. Способы укрепления бандажей на колесном центре весьма различны наилучшее укрепление—непрерывное без стопорных болтов (по русско-гермамск. способу). Осевая букса (см. Букса осевая) состоит из верхней коробки, имеющей вид буквы П и плотно прилегающей боковыми поверхностями к буксовым челюстям, приваленным к вырезу в главных рамах. Для уменьшения трения между буксой и челюстями к боковым поверхностям буксовой коробки прикреплены бронзовые наличники. Между телом буксы и скошенной стороной буксовой челюсти вставлен клин с натяжным болтом, подтягивая который можно уменьшать образующийся от изнашивания зазор. В верхнюю часть буксы плотно закладывается бронзовый подшипник, охватывающий верхнюю половину осевой шейки. Смазочная коробка закрывает осевую шейку снизу и наполнена набивкой, пропитанной смазкой. Буксовая короб-
[c.376]
К волокнистым материалам относят хлопчатобумажные, льняные, шелковые, шерстяные и синтетические ткани пряжу, обтирочные, концы, подби-вочные материалы и салфетки шпагат, веревки, нитки, канаты, бумажную продукцию кожевенные, резинотехнические и шубно-меховые изделия войлок, пластикаты, полиэтилен, асбест и т. д. Все эти материалы и изделия из них (спецодежда, форменное обмундирование, постельное и нательное белье, польстерные щетки, буксовые валики и др.) поступают на склады в мягкой упаковке (тюках, кипах, рулонах, пачках, завернутых в ткань или оберточную бумагу). Исключение составляют резиновая и кожаная обувь, асбестовые и другие изделия, которые поступают в деревянной таре (фанерных, дощатых ящиках и обрешетках) или картонных коробках.
[c.151]
Между подшипником и потолком буксы ставится буксовый вкладыш, служащий для центрирования подшипника и облегчения выемки его. У букс, имеющих вертикальное перемещение в буксовых лапах, вкладыш плотно прилегает к буксе и подшипнику у букс, неподвижно связанных с рамой тележки, верхняя поверхность вкладыша — цилиндрическая. Сопротивление от трения подшипника по шейке — ок. 1,5 кг/т передаваемого веса, причем при трогании с места зто сопротивление в песколько раз больше. Для уменьшения этого сопротивления применяют в Б. о. роликовые подшипники. На фиг. 6 показана Б. о. с роликовыми подшипниками электрифицированного пригородного вагона. Коробка буксы / — разрезная и составлена из верхней и нижней частей, стягиваемых болтами. Самые подшипники состоят из двух пар стальных закаленных колец II и III, между к-рыми располагаются паленые ролики IV. Внутренние кольца плотно паса- [c.567]
На фиг, 473 показана передняя тележка паровозов сер. С последнего выпуска. Рассматривая чертеж, мы видим, что в передней части тележки— обычное водило Бисселя (с геометрической длиной 1 350 мм). В верхней средней части отливки, соединяющей обе буксы бегунка в одно целое, устанавливаются детали шарнира (см, поперечный разрез) горизонтально продольного балансира. Последний своим задним концом соединяется (также шарнирно) с буксовой поперечной коробкой передней сцепной оси (см. план). В средней части балансир имеет точку вращения, при чем прорез в теле балансира под подшипник шкворня сделан продолговатым (прямоугольным в плане), так что балансир может не только вращаться около шкворня, закрепленного к раме паровоза, но перемещаться в стороны на некоторую величину, определяемую условиями вписывания паровоза в кривые—у паровоза сер. на 20 мм в каждую сторону. [c.529]
Профилактические и технические осмотры. Осмотр тележки необходимо производить в соответствии с правилами эксплуатации и должностными инструкциями. Кроме того, следует проверять состояние подвесок (тяги, валики, серьги) и литого поддона пружин центрального и буксового подвешивания болтовых соединений (наличие гаек и шплинтов) предохранительных скоб тормозных траверс и надрессорного бруса продольных тяг гидравлических гасителей опорных скользунов тележки (крепление коробок скользунов), допустимого износа вкладышей (ДСП-Г). Вкладыш-скользун должен равномерно выступать из коробки на высоту не менее 5 мм. Необходимо также проверять зазор а (см. рис. 18), который должен быть не менее 9 мм. Зазор менее 9 мм необходимо увеличить до величины 16+ мм. [c.35]
Конструктивные особенности коробок передач
После выбора кинематической схемы производится расчет и выбор конструктивных параметров коробки передач: межцентрового расстояния, показателей шестерен, валов, опор и механизмов переключения. Все эти параметры определяются по соответствующим формулам или на основании опытных данных.
Межцентровые расстояния должны определяться исходя из контактной прочности зубьев; в существующих конструкциях КП средние величины межцентровых расстояний лежат в пределах 100-200 мм.
Шестерни.В коробках передач применяются цилиндрические и конические шестерни. Первые изготавливаются с прямыми или косыми зубьями, вторые – с прямыми или спиральными. Косые и спиральные зубья по сравнению с прямыми обладают большей работоспособностью, плавностью и меньшим шумом, поэтому их рационально применять при передаче больших мощностей. Однако шестерни с косыми и спиральными зубьями сложны в производстве и создают добавочные усилия, для компенсации которых необходимо принимать специальные меры.
Шестерни с малым числом зубьев часто нарезаются непосредственно на валу. При большом числе зубьев, когда диаметр впадин значительно отличается от диаметра вала, шестерни изготавливают отдельно.
В целях сохранения лучшей работоспособности, а также приемлемых габаритов коробки передаточное число одной пары шестерен не должно быть более трех.
Модуль шестерен определяется исходя из напряжений на изгиб. В большинстве отечественных КП применяются шестерни с постоянным модулем. Так как он рассчитывается по наиболее нагруженным шестерням (на первой передаче), то его величина довольно большая и в зависимости от передаваемого момента и конструктивных особенностей лежит в пределах 6,5-9 мм. В некоторых коробках применяются разномодульные шестерни. Тогда в зависимости от передач модуль изменяется от 3,0 до 6,75 мм (эти цифры приведены для коробки, в которой установлены шестерни с косыми зубьями и постоянным зацеплением). Разномодульные шестерни позволяют сделать КП более компактной и легкой.
Зубья бывают нормальными и укороченными. Шестерни с укороченными зубьями являются более компактными и обладают большей прочностью, минимальное число зубьев у них меньше. Например, для шестерни с углом зацепления 20°, нарезанной рейкой, минимальное число укороченных зубьев равно 14, а нормальных – 17. Но укороченный зуб имеет и существенный недостаток – меньшую продолжительность зацепления, что приводит к большему износу. В связи с этим укороченный зуб применяется в том случае, когда определяющим фактором является прочность зуба, а не его износ. Зубья, как правило, бывают корригированными.
Валы.Двухвальные КП обычно имеют валы, расположенные в одной плоскости, у трехвальных один вал смещается и лежит в другой плоскости. Этим уменьшается длина коробки.
Для крепления шестерен и муфт валы имеют шлицы, и только в единичных случаях вместо шлицев применяются шпонки. В большинстве коробок валы выполняются постоянного диаметра с нарезанными почти по всей длине шлицами, но в некоторых случаях вал делается ступенчатым, примерно равнопрочным. В последнем случае вес и габариты коробки снижаются. В выполненных конструкциях валы устанавливаются или на двух, или на трех опорах. Все валы и расположенные на них детали должны быть надежно зафиксированы в радиальном и осевом направлениях.
Так как валы передают большие крутящие моменты и в то же время должны иметь достаточную прочность и жесткость при малых габаритах и весе, то они изготавливаются из высококачественных легированных сталей.
Опоры.В качестве опор в коробках передач применяются подшипники качения всех типов. Тип подшипника выбирается в зависимости от действующих сил, числа оборотов, а также других обстоятельств (характера нагрузки, жесткости валов, подвода смазки и т. д.). В большинстве случаев на опоры валов воздействуют комбинированные нагрузки – радиальные и осевые, поэтому часто устанавливают не один, а несколько, притом разнотипных подшипников, воспринимающих соответствующую нагрузку. Особенно сложными и ответственными узлами являются опоры конических шестерен, которые кроме восприятия больших осевых и радиальных нагрузок еще должны обеспечивать регулирование зазора в зубчатом зацеплении.
В многоопорных конструкциях (от двух и выше) лишь одна из опор является жесткой в осевом направлении, остальные выполняются плавающими. В качестве плавающих опор выбираются менее нагруженные, что способствует лучшему осевому перемещению. В трехопорных валах жесткой обычно является средняя опора.
Механизмы переключения.В простых КП переключение производится каретками, муфтами, синхронизаторами и индивидуальными фрикционами. Чтобы переключение было легким и надежным, в механизмах переключения предусматриваются специальные устройства (различные замки, фиксаторы и стопоры), позволяющие легко передвигать муфты, производить безударное включение, надежно удерживать передачу во включенном, выключенном и нейтральном положениях.
Каретки.Переключение передачи с помощью кареток применяется очень редко из-за больших ударных нагрузок и повышенных усилий со стороны водителя. Иногда с помощью кареток включаются передачи заднего хода и вспомогательные агрегаты (лебедки, валы отбора мощности и т. д.). Так как последние включаются в основном при стоянке машины, такое включение допустимо.
Муфты.Муфты применяются в коробках, в которых шестерни находятся в постоянном зацеплении. Муфты бывают зубчатыми или кулачковыми. В отечественных коробках используются первые. По сравнению с предыдущим случаем переключение с помощью муфт является более легким, быстрым и сопровождается меньшими ударными нагрузками. Объясняется это малым диаметром, а следовательно, и весом муфт, а также специальным профилированием боковых кромок зубьев. Так как полностью избавиться от ударных нагрузок нельзя, муфты должны изготавливаться из сталей, хорошо переносящих удары.
Индивидуальные фрикционы.При включении передачи в этом случае соединение вала с соответствующей шестерней происходит за счет фрикциона, включаемого на каждой передаче вместо муфты. Такое переключение является наиболее совершенным, так как позволяет сократить до минимума разрыв в передаче мощности на ведущие колеса. Кроме того, за счет гидропривода имеется возможность полностью снять ударные нагрузки и обеспечить водителю легкое и удобное управление коробкой передач. Применение индивидуальных фрикционов делает излишним установку главного фрикциона. Однако индивидуальные фрикционы увеличивают габариты и вес КП делают ее более сложной и дорогой.
Картер.Картер воспринимает нагрузки от опор, является остовом для монтажа всех деталей и одновременно обеспечивает коробке условия закрытой передачи. Картер делают из чугунных или алюминиевых сплавов. В КП большое распространение получили картеры из алюминиевых сплавов. Они более легкие, проще в изготовлении, имеют лучшую теплопроводность, но чугунные более жесткие, имеют меньшие линейные расширения при нагреве.
Чтобы обеспечить достаточную жесткость и распределить нагрузку по всей поверхности, картер делают с внутренними перегородками и ребрами, стягивают шпильками и иногда поперечными струнами. Для лучшего охлаждения картеры с мокрым поддоном оребряются, обдуваются потоком воздуха, внутренние полости делаются сообщающимися. Сухие картеры охлаждаются с помощью радиатора. Последние начинают применяться для КП, имеющих ограниченные объемы и передающих большие мощности. Разъем картера чаще всего делается по оси валов. Крепится картер или только к корпусу машины, или к двигателю и корпусу.
Конструкции КП в целом.Рассмотрим некоторые конструкции коробок передач, содержащие характерные для гусеничных машин элементы.
На рис. 103 показана двухвальная коробка передач с поперечным расположением валов. Число передач вперед – пять, назад – одна, диапазон передач 6,67. Шестерни находятся впостоянном зацеплении, они прямозубые и имеют одинаковый модуль, равный 9 мм. Переключение передач осуществляется: на заднем ходу и первой передаче – с помощью зубчатых муфт; на второй – простого синхронизатора, на третьей, четвертой, пятой – инерционного синхронизатора. Ведущий вал 1 – двухопорный, промежуточный 2 и ведомый 3 – трехопорные, при этом средние опоры являются жесткими, крайние – плавающими. Масло для смазки заливается в картер, который сделан из алюминиевого сплава и имеет разъем по оси валов в горизонтальной плоскости.
На рис. 104 представлена трехвальная коробка передач с продольным расположением валов. Число передач вперед – семь, назад – одна, диапазон передач 13,4. Шестерни находятся в постоянном зацеплении и имеют косые зубья, шестерни разномодульные, и в зависимости от передач модуль изменяется от 3,0 до 6,75 мм. У конической шестерни модуль равен 8 мм. Переключение осуществляется таким образом: задняя и первая передача с помощью шестерен-кареток, вторая – муфты, с третьей по седьмую – синхронизаторов. Ведущий 1 и промежуточный 2 валы располагаются на двух опорах; правые опоры – жесткие, левые – плавающие. Ведомый вал 3 – трехопорный, от осевых смещений он фиксируется левой и средней опорами. У конической шестерни радиальную нагрузку воспринимает в основном роликовый цилиндрический подшипник, а осевую – шариковый радиально-упорный. В коробке применяются роликовые цилиндрические подшипники без наружной обоймы. Две шестерни на ведомом валу устанавливаются на шпонках. Масло заливается в чугунный картер, имеющий две плоскости разъема.
На рис. 105 приведена коробка передач колесного трактора общего назначения. Она обеспечивает высокое качество переключения и имеет много конструктивных элементов, характерных для КП многоцелевых гусеничных машин. У коробки четыре вала, расположенных продольно. На ведущем валу 1 установлены шестерни, обеспечивающие включение четырех передач с помощью индивидуальных фрикционов. Последние приводятся в действие с помощью гидравлического управления. На промежуточном валу 2 крепятся только шестерни. На грузовом 3 и раздаточном 4 валах размещены зубчатые муфты, посредством которых включаются четыре режима на переднем и два на заднем ходу, а всего коробка передач позволяет включать 16 передач при движении вперед и восемь при движении назад. Диапазон передач 10,9. Высокое качество переключения обеспечивается за счет индивидуальных фрикционов при включении передач в пределах одного режима, а также тем, что при переключении режимов используется тормоз-синхронизатор. Все шестерни прямозубые и находятся в постоянном зацеплении. Они имеют разные модули – 6 и 8 мм. Валы, кроме раздаточного, трехопорные. Раздаточный вал состоит из двух частей, каждая из которых опирается на две опоры. Все валы в осевом направлении фиксируются шариковыми подшипниками. Смазка осуществляется под давлением, картер – с сухим поддоном.
Рис. 103. Конструкция двухвальной коробки передач
Рис. 104. Конструкция трехвальной коробки передач
Рис. 105. Конструкция коробки передач с индивидуальными фрикционами
Читайте также:
Двухвальные коробки передач легковых автомобилей ВАЗ и АЗЛК
Такие коробки передач применяются в переднеприводных и заднеприводных (с задним расположением двигателя) легковых автомобилях. Эти коробки просты по конструкции, имеют небольшую массу и высокий КПД. Конструктивно они объединены в одном блоке с двигателем, сцеплением, главной передачей и дифференциалом.
Конструкция двухвальной коробки передач во многом зависит от того, какое расположение на автомобиле имеют двигатель и коробка передач – продольное или поперечное. При поперечном расположении коробки передач применяется цилиндрическая главная передача и дистанционный привод переключения передач. При продольном расположении – коническая или гипоидная главная передача и непосредственный привод переключения передач.
В двухвальной коробке передач на любой передаче, кроме заднего хода, крутящий момент двигателя передается двумя шестернями 2 и 3 (схема 1) непосредственно с первичного вала 1 на вторичный вал 4, который соединен с ведущими колесами автомобиля. Движение автомобиля задним ходом обеспечивается промежуточной шестерней 6, которая вводится в зацепление между шестернями 5 и 7. В результате этого вторичный вал коробки передач вращается в сторону, противоположную вращения первичного вала 1.
Схема 1 – Работа двухвальной коробки передач
а – движение вперед; б – движение задним ходом; 1 – первичный вал; 2, 3, 5, 6, 7 – шестерни; 4 – вторичный вал
Коробка передач ВАЗ
Конструкция двухвальной коробки передач, применяемой на переднеприводных легковых автомобилях ВАЗ, представлена на схеме 2. Коробка передач механическая, четырехступенчатая, трехходовая, с постоянным зацеплением шестерен, с синхронизаторами и ручным управлением.
Картер 18 коробки передач, отлитый из алюминиевого сплава, соединен шпильками с картером 17 сцепления и образует с ним единый картер, в котором размещены первичный и вторичный валы с шестернями и синхронизаторами, главная передача и межколесный дифференциал.
Главная передача – одинарная, цилиндрическая, косозубая. Дифференциал – конический, двухсателлитный, симметричный, малого трения. Картер коробки передач сзади закрыт крышкой 27, в которой установлен сапун 1 для связи внутренней полости коробки передач с атмосферой.
Схема 2 – Коробка передач переднеприводных легковых автомобилей ВАЗ
а – общий вид; б – схема; в – включение заднего хода; г – синхронизатор; 1 – сапун; 2 – первичный вал; 3, 6 – синхронизаторы; 4, 7, 9, 12, 13, 23, 24, 25, 26, 35 – шестерни; 5 – зубчатый венец; 8 – вторичный вал; 10 – корпус; 11 – сателлит; 14, 22 – шарниры; 15 – привод спидометра; 16, 34 – оси; 17, 18 – картеры; 19, 20 – пробки; 21 – подшипник; 27 – крышка; 28 – кольцо; 29 – муфта; 30 – фиксатор; 31 – пружина; 32 – сухарь; 33 – ступица; 36 – вилка
Первичный вал 2 представляет собой блок ведущих шестерен I, II, III, IV передач и заднего хода. Вал вращается в двух подшипниках, один из которых установлен в картере коробки передач, а другой – в картере сцепления.
Вторичный вал 8 изготовлен вместе с ведущей шестерней 7 главной передачи. Он вращается в двух подшипниках, установленных в картере сцепления и в картере коробки передач. На вторичном валу свободно установлены ведомые шестерни 23, 24, 25 и 26 соответственно I, II, III и IV передач, находящиеся в постоянном зацеплении с соответствующими ведущими шестернями первичного вала. На вторичном валу жестко закреплены ступицы синхронизаторов 3 и 6. На скользящей муфте синхронизатора 6 имеется з
виды, устройство и принцип работы
Механическая коробка передач уже не является наиболее распространенным типом КПП из применяемых на автомобилях сегодня. Однако она все еще остается достаточно востребованной благодаря своей надежности, простоте конструкции и ремонтопригодности. МКПП получила свое название от “ручного” (или механического) способа переключения передач. Трансмиссия относится к ступенчатым коробкам, в которых крутящий момент изменяется ступенями (передачами). Механическая КПП считается самой надежной, но и самой сложной в управлении, особенно для начинающего водителя.
Принцип работы механической коробки передач
Механическая коробка передачПринцип работы механической КПП следующий: крутящий момент от двигателя через сцепление передается на первичный вал коробки передач, далее преобразуется при помощи пар взаимодействующих между собой шестерен и затем передается на колеса. Каждая пара шестерен (ступень) имеет определенное передаточное число, которое преобразует скорость вращения и крутящий момент коленвала двигателя. Причем если передача увеличивает крутящий момент, то скорость вращения уменьшается и наоборот. В первом случае передача будет называться понижающей, а во втором – повышающая.
Передаточное число определяется отношением количества зубьев у выходной и входной шестерен в паре. В свою очередь, количество зубьев напрямую зависит от размера самой шестерни: чем больше зубьев – тем больше диаметр шестерни. Например, у первой передачи самое большое передаточное число, и, следовательно, входная шестерня (на первичном валу) имеет минимальный размер, а выходная – максимальный. Переключение скоростей в механической КПП происходит только при нажатии на педаль сцепления, поскольку необходимо прервать поток мощности, передающийся от двигателя.
Движение автомобиля, оснащенного МКПП, всегда начинается с первой передачи. Исключение составляют тяжелые грузовики – там это можно делать со второй передачи. Для этого необходимо вручную перевести селектор рычага в соответствующее положение. Переход на повышенные передачи осуществляется последовательным переключением передач друг за другом. Сам момент переключения скорости зависит от показаний спидометра и тахометра, поскольку каждая передача рассчитана на работу в определенном диапазоне оборотов двигателя.
Виды механических КПП
По количеству ступеней механическая коробка передач в основном подразделяется на:
- 4-х ступенчатую;
- 5-и ступенчатую;
- 6-и ступенчатую.
Наиболее распространенной механикой считается трансмиссия 5МТ, т.е. пятиступенчатая коробка передач.
В зависимости от количества валов различают следующие виды КПП:
- двухвальные механические трансмиссии, устанавливаемые на легковые переднеприводные автомобили;
- трехвальные МКПП, которые применяются в основном на заднеприводных автомобилях, а также на грузовых машинах.
Устройство механической коробки передач
Крышка оси и направляющая крышки ступицы
Во-первых: мне нужна крышка ступицы или крышка оси?
Колпачки ступиц будут работать только на передних ступицах OIL. Крышки моста работают как на смазанных, так и на масляных передних ступицах.Крышки переднего и заднего мостов
Крышки оси подходят для большинства колес диаметром 22,5 и 24,5 дюйма с направляющими ступицами или шпильками.Сначала проверьте, есть ли у вас гайки с проушинами 33 мм или 1,5 дюйма. Если вы не уверены, какая из них у вас есть, ознакомьтесь с нашим руководством по крышкам гайки с проушинами здесь.
Также убедитесь, что у вас есть как минимум 1/2 дюйма резьбы или более. Если у вас менее 1/2 дюйма открытой резьбы, вам нужно будет надавить на крышки гайки наконечника.
Колпачки передних ступиц
Шаг 1: Подсчитайте количество выемок на колесе и сопоставьте его с правильной крышкой ступицы.
Вот пример колеса с 5 выемками и передней крышки ступицы с 5 соответствующими выемками.Если на вашем колесе 4 зубца, то потребуется колпачок с 4 зубцами.
Вы также можете использовать универсальный колпачок ступицы для всех количеств выемок, если на колесе нет 6 РОВНО разнесенных выемок.Для этого потребуется крышка с ровными отметками на 6.
Шаг 2: Измерьте высоту кромки колеса.
Колпачки задних ступиц
Первое: Измерьте диаметр шпилек оси.
Если у вас очень длинные шпильки, вам может понадобиться крышка с боковой стенкой 1 1/2 дюйма. Вот пример:
Купите наши аксессуары для колес!
Комплект ведущей оси — полный мост 38 дюймов —
Создано с помощью Sketch.Создано с помощью Sketch. Переключить меню866-846-5278
- Войдите или зарегистрируйтесь
- 0
- долларов США
- Австралия
- Канада
- Доллар США
- GoPowerPit
- Запчасти для картинга
- Новые поступления
- Мерч
- Аксессуары
- Оси и детали осей
- Подшипники и уплотнения
- Тормоза, колодки, барабаны и Rotos
- Carbuetors
- Цепи и охранники
- Китайский квадроцикл
- Сцепления и фрикционные диски
- Вариатор и запчасти
- Электрические
- Детали двигателя
- Крылья и кронштейны
- Фильтры
- Топливные баки и детали
- Подарочный сертификат
- Кабели для картинга
- Оборудование и ключи
- Промежуточные валы и звездочки
- Педали и пружины
- Рабочие части и комплекты
- Обеспечить регресс
- Сиденья и ремни безопасности
- Спрингс
- Звездочки
- Стартерные двигатели
- Рулевое управление
- Подвеска
- Подвеска и амортизаторы
- Шины и диски
- Преобразователи крутящего момента и ремни
- Приваривать детали
- Гонки / Производительность
- Запчасти для квадроциклов и мини-велосипедов
- Запчасти для квадроциклов
- Велосипедный мини-комплект Lil Rascal
- Запчасти MB200 и Baja
- Запчасти MegaMoto
- Coleman Parts
- Детали рамы MB
- Детали руля MB
- Детали двигателя MB
- Газовые баллоны MB
- Детали MB Performance
- Сиденья MB
- Звездочки и цепь MB
- Шины и диски MB
- Поломка деталей
- О нас
- Галерея клиентов
- Менеджер по доставке FedEx
- График технического обслуживания картинга
- Отзывы
- Доставка и возврат
- Блог GoPowerSports
- Связаться с нами
- политика конфиденциальности
- Условия и положения
- Видео
- Фотогалерея клиентов
- Наши обучающие видео
- Встреча по обмену пате
- Просмотр корзины
- GoPowerPit
- Черная пятница распродажа
- Закрытие и специальные предложения
- `—— Без категории ——
- Братья Картеры
- Новые поступления
- Картинг TrailMaster
- Мерч
- Шляпы
- Запчасти для картинга
- Аксессуары и товары
- Оси и детали осей
- Подшипники и уплотнения
- Тормоза, колодки, барабаны и роторы
- Кабели
- Карбюраторы
- Цепи и охранники
- Китайский квадроцикл
- Клатчи
- Вариатор и запчасти
- Электрические
- Детали двигателя
- Крылья, кронштейны и пластик кузова
- Фильтры
- Топливные баки и детали
- Оборудование и ключи
- Промежуточные валы и звездочки
- Закрытые и специальные предложения Manco
- Педали и пружины
- Детали исполнения
- Обеспечить регресс
- Звездочки
- Сиденья и ремни безопасности
- Спрингс
- Стартерные двигатели
- Рулевое управление
- Подвеска
- Шины и диски
- Преобразователи крутящего момента и ремни
- Приваривать детали рамы
- Запчасти для Ерф-Дог
- Детали блейзера — Детали рамы
Главное меню
Сортировать по категориям
Тележки | Железнодорожный технический сайт
Тележки (тележки)
Железная дорога тележки почти не замечает средний пассажир, но они существенная часть поезда, его приводная система и его руководство механизм.Стандартный железнодорожный вагон будет иметь две тележки, обычно расположен недалеко от транспортных средств. Каждая тележка представляет собой 4- или 6-колесную тележку. грузовик, который обеспечивает опору для кузова транспортного средства и который используется для обеспечения его тяги и торможения.Каждый вагон (в Северной Америке он называется автомобилем, а в некоторых других англоязычных страны и до сих пор так называемые в сфере электрической тяги) две тележки. Тележки выдерживают массу автомобиля, используются колеса направлять его по рельсам и обеспечивать некоторую амортизацию против ударов, передаваемых от гусеницы во время движения.См. Также «Системы подвески автомобиля».
Тележки может приводиться в действие либо электродвигателями какого-либо типа механических привод подключен к двигателю дизельного двигателя. Они также могут просто предоставить несущая функция — так называемые прицепные тележки.И мотор, и прицеп тележки нормально тормозятся, под контролем торможения поезда система.
А Пара колес поезда жестко закреплена на оси и образует колесную пару. Колеса прижимаются к оси так, что они оба вращаются. все вместе.Как мы видели выше, обычно две колесные пары устанавливаются в тележка, так что тележка — это просто 4-х колесный грузовик — американцы называют это грузовик — установлен под вагон с целью поддерживать и направлять вагон по трассе.
Рисунок 1: Стандартная американская трехкомпонентная тележка, используемая на грузовых вагонах вокруг Мир. Это очень простая конструкция, в которой поперечный элемент, известный как валик сидит на паре двойных винтовых пружин, чтобы обеспечить некоторый уровень демпфирования для автомобиля, стоящего на двух боковых опорах.Тележка вращается вокруг центрального штифта, чтобы тележка могла преодолевать повороты. Пассажирские тележки имеют дополнительные рессоры на буксах. Диаграмма: Амстед, изменено автором.
А Стандартная тележка грузового вагона показана на рисунке 1.Это просто и имеет только одна система подвески. На пассажирской тележке также установлены пружины. в верхней части букс колесные пары.Эти Пружины буксы известны как первичная подвеска. Пружины балки известны как вторичные подвеска.Кузов машины поэтому разделены от гусеницы двумя наборами пружин (рис. 2).
Рисунок 2: Простая схема подвески легкового автомобиля, показывающая общее расположение и расположение пружин первичной подвески на буксы и вторичная подвеска, на которую опирается кузов автомобиля отдыхает.Схема: Автор.
Традиционно, пружины были стальные, катушка или плоская.В настоящее время они часто представляют собой резиновые или пневматические подушки или что-то подобное сочетание.Попутно не стоит забывать, что железнодорожные колеса приходите парами, прикрепленными к общая ось на правильном расстоянии друг от друга (датчик) и вся жесткая система называется колесной парой (рисунок 3).В рама традиционной тележки состоит из двух боковых рам штук и два передние бабки, образующие коробчатую конструкцию.Чтобы добавить силы, пара поперечины, называемые фрамуги, добавлены.
Рисунок 3: Типичная железнодорожная колесная пара с буксами. Колеса давят на к оси, а затем нажимаются буксы. Фото: Данобат.
Управляемые тележки
A обычная рама тележки превращается в кривую ведущей колесная пара, поскольку она направляется по рельсам.Однако есть степень скольжение и большое усилие, необходимое для изменения направления. В в конце концов, тележка несет примерно половину веса транспортного средства, на котором она поддерживает. Он также ведет автомобиль, иногда на высокой скорости, в кривая против его естественной тенденции двигаться по прямой.
Кому преодолеть некоторые из механических проблем жесткой колесной пары, установленной в жесткой раме тележки некоторые современные конструкции включают радиальную форму движение в колесной паре (рисунок 4).
Рисунок 4: конструкция управляемой тележки.В этом японском дизайне оси допускаются определенные перемещения в раме тележки и буксах связаны с кузовом автомобиля через рулевую балку. Есть ряд различных систем для снижения износа колес и напряжения рамы тележки и это одна из первых систем.Схема: JRTR F52.
Моторная тележка
Тележки бывают разных форм и размеров, но в наиболее развитой форме моторная тележка электровоза, тепловоза или электропоезда. Вот это должен нести двигатели, тормоза и системы подвески в пределах плотный конверт.Он подвергается сильным нагрузкам и ударам и может должны работать со скоростью более 300 км / ч на высокой скорости. Следующее параграфы описывают части, показанные на фотографии ниже, которая является Британский дизайн.
Рисунок 5: Тележка с тяговым электродвигателем со сварной стальной рамой и носовой частью. подвесные тяговые двигатели. Названные здесь детали описаны в следующие параграфы.
Рама тележки
Банка быть из листовой стали или литой стали. В данном случае это современный дизайн. из сварного стального короба, в котором конструкция сформирована в полую сечения необходимой формы.
Транец тележки
Поперечный структурный элемент рамы тележки (обычно два шт.), который также поддерживает детали наведения кузова и тяговые двигатели.
Тормозной цилиндр
An Пневматический тормозной цилиндр предусмотрен для каждого колеса.Цилиндр может работать протекторные или дисковые тормоза. Некоторые конструкции включают стояночные тормоза в качестве хорошо. Некоторые тележки имеют два тормозных цилиндра на колесо для тяжелых условий эксплуатации. требования к торможению. Каждое колесо снабжено тормозным диском с каждой стороны и тормозной колодкой, приводимой в действие тормозным цилиндром.К раме тележки подвешена пара подкладок, которые активируются прикрепленными звеньями. к поршню в тормозном цилиндре. Когда воздух попадает в тормозной цилиндр, внутренний поршень перемещает эти звенья и вызывает тормозные колодки прижать к дискам.Опорный кронштейн тормозной подвески несет тормозные подвески, на которых подвешены колодки.
Катушка первичной подвески
A стальные винтовые пружины, по две из которых установлены на каждой буксирной коробке в этом дизайн. Они несут вес рамы тележки и всего прикрепленного к нему.
Трубка подвески двигателя
Многие двигатели подвешены между поперечными балками рамы тележки называется транец и ось. Этот мотор называется «носовой подвес». потому что он подвешен между подвесной трубкой и одиночным креплением на транец тележки называется носом.
Рисунок 6: Чертеж тягового двигателя с носовой подвеской. Двигатель приводит в движение ось через комплект шестерни / шестерни, при этом шестерня прижата к ось. Вес двигателя распределяется между транцем тележки. и ось.Ось несет вес двигателя через подвесная трубка. Графика: Voith.
Рисунок 7: Более современная конструкция — это рама , установленная на двигателе . Вес двигатель полностью установлен на раме тележки.Ось проходит через гибкая муфта. Такое расположение снижает неподрессоренную массу на колеса и, следовательно, снижает износ. Графика: Voith.
Коробка передач
Содержит шестерню и шестерню, соединяющую привод от якоря с осью.
Проушина для подъема
Позволяет поднимать тележку с помощью крана без необходимости обвязывания цепей или веревок вокруг рамы.
Двигатель
Обычно, каждая ось имеет свой двигатель. Он приводит в движение ось через коробку передач. В некоторых конструкциях, особенно на трамваях, используется двигатель для привода двух осей
Детектор переключателя нейтральной секции
In Великобритании ВЛ разделена на участки с короткой нейтралью. разделы, разделяющие их.Необходимо выключить ток на поезд, когда пересекается нейтральный участок. Установлено магнитное устройство на трассе отмечает начало и финиш нейтрального участка. В устройство обнаруживается коробкой, установленной на ведущей тележке поезда к проинформируйте оборудование, когда нужно выключить и включить.
Вторичная подушка безопасности подвески
Резина Пневмоподвески предусмотрены в качестве вторичной системы подвески для самые современные поезда. Воздух подается из сжатого воздушная система.
Система защиты от скольжения колеса, ведущая к буксе
Где Установлена система защиты от скольжения колес (WSP), установлены буксы с датчиками скорости. Они подключаются с помощью кабеля, прикрепленного к крышка коробки WSP на конце оси.
Ослабленные провода для соединения с кузовом
Цепи двигателя подключаются к тяговому оборудованию в вагоне или локомотиве с помощью гибких проводов, показанных здесь.
Амортизатор
Для уменьшения эффекта вибрации, возникающей в результате контакта колеса с рельсом.
Крышка оси
Простая защита для щетки обратного тока, если она есть, и смазки подшипника оси.
Конструкции тележек
Существуют различные конструкции тележек, как показано на следующих рисунках.
Рисунок 8: Тележка со сварной Н-образной рамой, оснащенная двумя электродвигателями. установлен в конфигурации «с подвешиванием на носу», где масса двигателя разделяется между транцем тележки и ведущей осью.В этом В конструкции вторичной подвески используются подушки безопасности. Подушки безопасности заполнены со сжатым воздухом, подаваемым от бортового воздушного компрессора. Рисование: Автор.
Рисунок 9: Тележка со сварной Н-образной рамой, оснащенная двумя электродвигателями. установлен в конфигурации « на раме», где масса двигателя равна в значительной степени поддерживается рамой тележки.Графика: Автор.
Рисунок
10: Тележка под дизель-электрическим тягачом британского класса 222.
У этого есть конструкция внутренней рамы, так что колеса почти полностью
выставлены снаружи.Тормозные диски очевидны с тормозом
приводы, установленные вокруг внутренней части каждого колеса. Кузов вагона с рамой тележки соединяет большой горизонтальный торсион.
для уменьшения бокового движения или «охоты». Фото: Автор.
Рисунок 11: Тележка трамвая типа Bombardier Flexx 3000.Потребность в низком полы современных трамвайных вагонов и легкорельсового транспорта требуют очень компактного дизайн. Здесь тяговые двигатели небольшие и устанавливаются вне тележку, приводящую в движение конец оси через коробку передач на 90 градусов.Тормозные диски и приводы также установлены вне колес. Эта тележка была разработана для трамвая Блэкпул. Фото: Автор.
Рисунок 12: Трехосная тележка, нарисованная с помощью CAD.3-осная тележка выполняет следующие функции: то же самое, что и двухосная тележка, но дополнительная ось необходима для распределите большую массу по трассе. Ограничения веса для трека определяется как нагрузка на ось, т. е. допустимая нагрузка на каждую ось.Максимальная нагрузка на ось магистральных линий в Великобритании составляет 25 тонн в Европа 22,5 тонны. На маршрутах тяжеловесных грузов может быть до 36 тонн. Недостаток трехосной тележки — длинная жесткая колесная база, который ограничивает радиус кривой, который можно использовать.Чертеж: 3dcadbrowser.com.
Jacobs Bogie
Тележка Jacobs — это конструкция, в которой одна тележка поддерживает концы двух соседних транспортных средств. Название происходит от немецкого железнодорожного инженера Вильгельма Якобса. (1858–1942). Его версии используются как на грузовом, так и на легковом транспорте.
Общий вид показан на Рисунке 13.
Рис. 13: Схема, показывающая разницу между тележкой Jacobs, поддерживающей концы двух соседних вагонов (верхний чертеж), и традиционной конструкцией, в которой каждый конец кабины поддерживается собственной тележкой (нижний чертеж).Идея Джейкобса предусматривает меньшее количество тележек для набора транспортных средств, но имеет недостатки, заключающиеся в большей массе оси и более сложной конструкции. Также требуются специальные меры для подъема транспортных средств. Рисунок: Wikipedia Fr 2008.
Детали моста для внедорожников
- Моя тележка
- Моя учетная запись
- Блог
- БЕСПЛАТНАЯ ДОСТАВКА ПРИ КВАЛИФИКАЦИОННЫХ ЗАКАЗАХ НА СУММУ ОТ 150 ДОЛЛАРОВ США
Меню
Меню Переключить навигацию Корзина (0) ПоискИскать
- Одежда
- Оси аксессуары
- Осевые фермы
- Крышки дифференциала
- Кронштейны дискового тормоза
- Защита шестерни
- Изготовление
- Батарейный ящик
- Трубка DOM
- Гайки и болты, класс восемь
- Вставки
- Разное.Части DIY Fab
- Полиэтиленовые втулки и комплекты втулок
- Трубные фланцы
- Шайба сварная
- Детали по модели
- Jeep JT 2020-текущий
- Jeep JL 2018-Текущий
- Джип JK 2007-2018
- Джип TJ / LJ 1997-2006 гг.
- Джип YJ 1987-1995
- Джип CJ 1976-1986
- Джип XJ и MJ 1984-2001 гг. Запчасти для Polaris RZR
- Рулевое управление
- Комплекты рулевого управления Heim
- Комплекты рулевой тяги
- Комплекты рулевого управления Superduty
- Jeep JK Комплекты рулевого управления
- Dana 44 Комплекты рулевого управления
- Комплекты рулевого механизма Kingpin Dana
- Комплекты полного гидравлического рулевого управления
- Подвесные аксессуары
- Кронштейны винтовой пружины
- Детали подвески листовой рессоры
- Кронштейны Rockwell Link
- Подвесные язычки
- Амортизаторы
- Монтажные кронштейны направляющей
- 3 звена и 4 скобы
- Комплект трехзвенной подвески
- Комплект четырехзвенной подвески
- Подвесные шарниры
- Эндуро сустав
- Кованое соединение из хромированного полимера
- Термообработанные трехкомпонентные подрубки
- Термообработанные двухкомпонентные соединения на кромке
- Magnum серии Heims
- Швы со смещением кромки
- Economy Heim Joints
- Женские суставы эконом-класса
- Орехи для варенья
- Трубные вставки
- Проставки с сильным перекосом
- Прокладки смещения
- Защитная шайба