каким должен быть и как замерить
Для обеспечения высокой компрессии в двигателе, а это сильно влияет на его КПД и прочие способности по отдаче, лёгкости запуска и удельному расходу, поршни должны стоять в цилиндрах с минимальным зазором. Но сводить его к нулю невозможно, из-за разной температуры деталей двигатель заклинит.
Содержание статьи:
- 1 Почему изменяется зазор между поршнем и цилиндром
- 2 Нормы соответствия
- 3 Результат нарушения зазора
- 4 Как проверить зазор между поршнем и цилиндром
Поэтому зазор определяется расчётным путём и строго соблюдается, а необходимое уплотнение достигается применением пружинных поршневых колец в роли газового и масляного уплотнения.
Почему изменяется зазор между поршнем и цилиндром
Конструкторы автомобилей стремятся, чтобы детали двигателя работали в режиме жидкостного трения.
Это такой способ смазки трущихся поверхностей, когда благодаря прочности масляной плёнки или подаче масла под давлением и при требуемом расходе непосредственного соприкосновения деталей не происходит даже под значительной нагрузкой.
По теме: Как понять что пробита прокладка ГБЦ
Не всегда и не во всех режимах подобное состояние можно удержать. Влияют на это несколько факторов:
- масляное голодание, подвода смазывающей жидкости, как это делается в подшипниках скольжения коленчатого и распределительного валов, под давлением в зону между поршнем и цилиндром не производится, а прочие способы смазки не всегда дают стабильный результат, лучше всего работают специальные масляные форсунки, но по разным причинам ставят их неохотно;
- некачественно сделанный или изношенный рисунок хонингования на поверхности цилиндра, призван он удерживать масляную плёнку и не давать ей полностью исчезнуть под усилием поршневых колец;
- нарушения температурного режима вызывают обнуление теплового зазора, исчезновение масляного слоя и появление задиров на поршнях и цилиндрах;
- применение некачественного масла с отклонением по всем значимым характеристикам.
Кажется, парадоксальным, но больше изнашивается поверхность цилиндра, хотя она обычно изготовлена из чугуна, это цельный чугунный блок или различные сухие и мокрые гильзы, залитые в алюминий блока.
Даже если гильза отсутствует, поверхность алюминиевого цилиндра подвергается специальной обработке, и на ней создаётся слой специального твёрдого износостойкого покрытия.
Связано это с более стабильным давлением на поршень, которое при наличии смазки почти не снимает с него металл при движении. А вот цилиндр подвержен грубой работе пружинных колец с высоким удельным давлением из-за малой площади контакта.
Это интересно: Как проверить датчик положения распредвала ДПРВ
Естественно, поршень тоже изнашивается, даже если это происходит с меньшей скоростью. В результате суммарного износа обеих поверхностей трения зазор непрерывно увеличивается, причём неравномерно.
Нормы соответствия
В исходном состоянии цилиндр полностью соответствует своему названию, это геометрическая фигура с постоянным диаметром по всей высоте и окружностью в любом сечении, перпендикулярном к оси. Однако, поршень имеет куда более сложную форму, к тому же он располагает термофиксирующими вставками, в результате чего неравномерно расширяется при работе.
Для оценки состояния зазора выбирается разница диаметров поршня в зоне юбки и цилиндра в средней его части.
Формально принято считать, что тепловой зазор должен составлять примерно от 3 до 5 сотых долей миллиметра по диаметру у новых деталей, а его максимальная величина в результате износа не должна превышать 15 сотых, то есть 0,15 мм.
Разумеется, это некие средние значения, двигателей великое множество и отличаются они как разными подходами к конструированию, так и геометрическими размерами деталей, зависящими от рабочего объёма.
Результат нарушения зазора
При увеличении зазора, а обычно оно связано ещё и с ухудшением работоспособности колец, всё больше масла начинает проникать в камеру сгорания и расходоваться на угар.
Теоретически при этом должна снижаться компрессия, но чаще она наоборот, повышается, из-за обилия масла на компрессионных кольцах, герметизирующего их зазоры. Но это ненадолго, кольца коксуются, залегают, и компрессия пропадает окончательно.
Поршни при увеличенных зазорах нормально работать уже не смогут и начинают стучать. Стук поршневой хорошо слышно на перекладке, то есть в верхнем положении, когда изменяет направление своего движения нижняя головка шатуна, а поршень проходит мёртвую точку.
Юбка отходит от одной стенки цилиндра и выбирая зазор с силой ударяет по противоположной. С таким звоном ездить нельзя, поршень может разрушиться, что приведёт к катастрофе всего мотора.
Как проверить зазор между поршнем и цилиндром
Для проверки зазора используется измерительная аппаратура в виде микрометра и нутромера, эта пара обладает классом точности, позволяющим реагировать на каждую сотую долю миллиметра.
Микрометром замеряется диаметр поршня в зоне его юбки, перпендикулярно пальцу. Стержень микрометра фиксируется зажимом, после чего нутромер устанавливается на ноль при опоре своим измерительным наконечником на стержень микрометра.
После такого обнуления индикатор нутромера будет показывать отклонения от диаметра поршня в сотых долях миллиметра.
Замер цилиндра производится в трёх плоскостях, верхней части, средней и нижней, вдоль зоны хода поршня. Замеры повторяются вдоль оси пальца и поперёк.
В результате можно оценить состояние цилиндра после износа. Главное, что потребуется – это наличие неравномерностей типа «эллипс» и «конус». Первое – отклонение сечения от окружности в сторону овала, а второе – изменение диаметра вдоль вертикальной оси.
Наличие отклонений в несколько соток говорит о невозможности нормальной работы колец и необходимости ремонта цилиндров или замены блока.
Заводы стремятся навязывать клиентам блок в сборе с коленвалом (шорт-блок). Но часто оказывается гораздо дешевле отремонтироваться расточкой, в тяжёлых случаях – гильзовкой, с заменой поршней на новые стандартные или ремонтного увеличенного размера.
Даже не новых двигателях со стандартными поршнями существует возможность точного подбора зазоров. Для этого поршни распределяются по группам с отклонением диаметра на одну сотку. Это позволяет выставить зазор с идеальной точностью и обеспечить оптимальные характеристики мотора и его предстоящий ресурс.
Зазор между поршнем и цилиндром
Как только вы завели двигатель и вам послышался звук, похожий на стук, а потом, когда двигатель прогрелся он пропал, либо немного стих, это значит, что пришла пора для проверки зазора между поршнями и цилиндрами. А это говорито том, что в руки нужно взять в руки инструмент и начать разбирать ГБЦ.
- Какие изменения могут быть с зазором между поршнем и цилиндром
- Существуют ли какие-то нормы соответствия поршней и цилиндров
- Причины изменения зазора между поршнем и цилиндром
- К чему может привести возникшая проблема зазора между поршнем и цилиндром
- Как самостоятельно проверить зазор между поршнем и цилиндром
По Вашему мнению может ли быть что-то общее между человеком и мотором машины.
У этого стука могут быть разные проблемы происхождения. Это может как распредвал так и коленвал стучать или какие-либо другие детали. Как упоминали ранее возможно это зазор между поршнем и цилиндром. Именно о такой проблеме двигателя пойдет сегодня речь. Нужно знать, что рано или поздно стук появится и эту проблему необходимо будет решать, а не откладывать на потом.
Какие изменения могут быть с зазором между поршнем и цилиндром
При правильной эксплуатации мотора со временем естественным путем сужается зазор между этими деталями.
Причиной уменьшения зазора между описываемыми деталями, является полусухое трение, из-за чего увеличивается температура деталей блока цилиндров. Со временем смазка пропадает и зазор исчезает из-за появления задир на поршне.
Для определения состояния блока цилиндров проводят диагностику, после которой выносят вердикт о ремонте цилиндров и элементов поршневой группы мотора. Но полностью сказать на сколько поршни, гильзы и другие детали деформировались можно при полном разбирании ГБЦ.
Если вы дошли до поршневой группы можно начинать дефектовку цилиндров и поршней.
Существуют ли какие-то нормы соответствия поршней и цилиндров
Перед началом ремонта поршневой группы, вам нужно узнать о том, что бывают группы диаметров поршней, и таблицы в которых указаны номинальные размеры цилиндров и поршней. Именно этими знаниями нужно пользоваться при ремонте. Существует определенная классификация поршней в зависимости от наружного диаметра, их всего пять: А, В, С, D, E через каждый 0,01 миллиметр размера. К этому еще категории размеру отверстия под поршневой палец через каждые 0,004 миллиметра. Эти данные в форме цифры — это категория отверстия, а буквы – это класс поршня, они написаны на днище поршня. Расстояние между поршнем и цилиндром должно соответствовать определенным расчетным нормам. Норма для новеньких деталей считается от

В общем-то для этого и делается промер зазора между поршнем и цилиндром, чтобы купить поршни такого класса, какого и цилиндры. Но может быть и так, что зазор превышает размер 0,15 мм, то нужно подобрать поршень к цилиндру, с наибольшим близким значением к расчетному размеру. Сначала нужно делать расточку цилиндров с максимальным приближением близкому к цифрам ремонтного размера. Но еще необходимо не забыть оставить припуск около 0,03 миллиметра для хонингования поверхности цилиндров после расточки. Только после этого всего можно приобретать поршни. Во время хонингования нужно выдерживать диаметр, чтобы при устанавливании поршня зазор входил в пределы допускаемой максимальной цифры зазора новых деталей 0,045 миллиметров.
Микрометр служит для определения размера поршней, а нутрометр для определения размера цилиндров. При покупке поршней к цилиндрам нужно учитывать не только номинальный или ремонтный размер, а также нужно знать и вес поршней. Он может быть нормальным, а может больше или меньше на пять грамм. К ремонтным поршням нужно подбирать ремонтные кольца ремонтных размеров.
Только после всех нужных проведенных манипуляций с зазором между этими деталями, вы быстро подберете необходимые размеры, и после растачивания установите поршень.
Причины изменения зазора между поршнем и цилиндром
Почему так происходит? Вроде бы стараешься эксплуатировать двигатель согласно инструкции. Масло моторное заливаем как советует производитель. Не жалеем денег на то чтобы двигатель был всегда «накормлен», так как говорят производители.
Но все же есть причины изменения зазора:
Даже во время правильной эксплуатации мотора, не может вам с точностью объяснить почему появляется увеличение зазора между этими двумя деталями. Нужно помнить, что все детали работают в экстремальных условиях, то есть при высоких температурах. Поэтому избежать изменения свойств металла не получится, можно только отодвинуть не надолго, но избежать не удастся. У поршня со временем начинают изнашиваться естественным путем канавки для колец, отверстия под палец и др.
Причинами могут стать неисправности появляющиеся во время эксплуатации мотора: перегрев мотора незафиксированный, не правильно урегулированные движущиеся детали, перекос мотора, плохого качества моторное масло, попадание в моторное масло топлива или охлаждающей жидкости и другие причины.
Все эти возникающие проблемы приводят к образованию такого зазора, который не соответствует заданным параметрам.К чему может привести возникшая проблема зазора между поршнем и цилиндром
Увеличенный по размерам зазор может привести к стуку, к плохой компрессии мотора, увеличению расхода масла, и к поломке двигателя. А вот уменьшенный зазор может привести к появлению задир на цилиндрах, перегреву деталей блока.
Как при увеличении зазора, так и при его уменьшении понадобится ремонтировать поршневую группу. Тут без вариантов. Можно конечно задуматься о приобретении нового мотора. Но дешевле будет если сделать ремонт такого рода поломки. Весь процесс будет исходить из замены цилиндров и их расточке и хонинговании.
Как самостоятельно проверить зазор между поршнем и цилиндром
Конечно, чтобы проверить зазор, необходимо для начала разобрать ГБЦ. В общем то вы начинаете капитальный ремонт мотора. Так как по результатам диагностики скорее всего появятся проблемы с распредвалом, коленвалом, заменой прокладок, подшипников, вкладышей, работы вам будет предостаточно. Но сегодня мы рассматриваем зазор между цилиндрами и поршнями. Для начала нам необходимы для измерительных инструмента: нутрометр и микрометр. Для чего они нужны мы упоминали ранее. Останавливаться на структуре материала и технологии изготовления деталей мы не станем. Начнем измерять размеры поршней.
Как и у цилиндров, у поршней тоже есть классификация по наружному диаметру и их пять классов: A, B, C, D, E. Замерять диаметр поршня нужно в районе цилиндрической части юбки, расстояние от днища плоскости в 52,4 миллиметра. Класс поршня вы разгледите на днище поршня.
Расстояние между поршнем и цилиндром должно соответствовать определенным расчетным нормам. Для новых деталей нормой считается от 0,05 до 0,07 мм. А для деталей бывших в использовании зазор должен быть не больше 0,15 мм.
В общем-то для этого и делаются промеры, чтобы купить поршни такого класса, какого и цилиндры. Но возможно и следующее, что зазор превышает размер 0,15 миллиметров, то необходимо подобрать поршень к цилиндру, с наибольшим приближенным значением к расчетному размеру.
Сначала нужно делать расточку цилиндров к максимально близкому по цифрам ремонтному размеру. Также не нужно забывать оставлять припуск около 0,03 миллиметра для хонингования поверхности цилиндров после растачивания. Только после этого всего можно приобретать поршни.
Как только вы сделали ремонт цилиндров, начинаем подбирать поршни нужного ремонтного размера. Для обычных моделей моторов отечественного производства, норма монтажного зазора между этими двумя деталями следующая: 0,06-0,08 миллиметров для двигателей 05 и 06, а 0,05-0,07 для двигателей 01 и 03.
Обязательно при покупке поршней необходимо уделить внимание на их массу. Вес одного поршня двигателя не должен быть меньше или больше на 2,5 грамм. Это нужно для того чтобы снизить вибрацию мотора при разности масс возвратно-поступательного движения. Все необходимые размеры поршня и цилиндра, а также нормы производителя к зазорам для того мотора который у вас можно узнать из руководства по эксплуатации именно вашего типа мотора. Желаем удачи вам при проведении замеров зазора между поршнем и цилиндром, а также в правильном выборе необходимых деталей.
Как проверить зазор между поршнем и цилиндром
Если утром, когда вы запустили холодный двигатель, был слышен металлический стук, который исчез при прогреве мотора, то это говорит только о том, что был нарушен зазор между поршнем и цилиндром. Почему он нарушается, и какие допустимые нормы применяются для зазоров между поршнем и цилиндром? Ответ вы найдете ниже.
Как меняется зазор между поршнем и цилиндром в процессе эксплуатации?
Уменьшение зазора происходит из-за естественного износа рабочих частей поршня и цилиндра. Такое изменение формы металла связано с его свойством поддаваться влиянию перепадов температур.
Помимо этого, уменьшение зазора может произойти и при неправильной сборке двигателя. Например, нарушена установка шатунов или появился перекос цилиндров. Не в стороне остается и перегрев двигателя, так как большие температуры имеют свойство расширять материалы. Особенно это касается алюминия, который, в отличие от чугуна, имеет высокий коэффициент расширения.
Как и любой другой дефект, нарушение зазора между поршнем и цилиндром оказывает негативное влияние на работу двигателя. Соприкосновение поршня и цилиндра под неправильным углом приводит к возникновению сухого трения, которое осуществляется без смазочного материала и повышает температуру деталей. Последствием такого трения почти во всех случаях становится появление различных царапин на рабочих поверхностях цилиндров.
После этого, любой двигатель обязательно подвергнут ремонту. Для проведения диагностики необходимо полностью снять головку блока цилиндров и как только поршневая группа будет на виду, то можно приступать к соответствующим замерам. В процессе замеров вам понадобятся микрометр, который покажет зазор поршней и нутромер для определения диаметра цилиндра.
Как снять головку блока цилиндров?
- В первую очередь, необходимо обездвижить автомобиль. Под колеса устанавливаются противооткатные упоры, а рычаг КПП устанавливается в положение «первая передача». Откройте капот автомобиля и найдите место расположения ГБЦ.
- Вначале, снимаются все части, которые мешают свободному доступу к головке. Таковыми могут быть: воздушный фильтр, карбюратор (или инжектор), «штаны», а также различные тросы, приводы педалей и проводка электрических датчиков. С ГБЦ выкручиваются свечи, при необходимости, снимается трамблер.
- Слейте масло из двигателя и охлаждающую жидкость. Откройте крышку привода ГРМ и демонтируйте ремень. Это нужно для того, чтобы освободить распределительный вал. После этого, открутите гайки крепления крышки ГБЦ и снимите ее вместе с прокладкой. Перед сборкой рекомендуется установить новую прокладку.
- Теперь можно приступать, непосредственно, к демонтажу головки блока цилиндров. Открутите специальные болты крепления и демонтируйте головку вместе с прокладкой. После этого, вы получите открытый доступ к блоку цилиндров.
Какие существуют нормы зазоров между поршнями и цилиндрами
Перед проведением соответствующего ремонта поршневого механизма, необходимо знать, что существуют определенные нормы зазоров, которые расписаны по таблицам и должны соблюдаться в строгой форме.
Диаметр поршней разделяется всего на пять классов: A B C D E. Каждый новый класс определяет увеличение диаметра на 0,01 миллиметра. Кроме того, имеются специальные категории, которые определяют диаметр отверстия под поршневой палец. Они меняются на каждые 0,004 миллиметра. Все эти цифры и маркировка, в обязательном порядке маркируется на нижней части поршня.
Для различных деталей существуют соответствующие нормы. Так, например, новые поршни должны устанавливаться с зазором 0,06 миллиметров по всей его окружности. Если же деталь уже прошла достаточно внушительный километраж, то ее зазор не должен быть больше 0,15 миллиметров.
В случаях, когда зазор начинает превосходить установленные нормы, то следует подобрать и приобрести те поршни, которые обеспечат требуемую зазорность. Совсем необязательно подгонять поршень с высокой точностью. Достаточно лишь иметь образец с приблизительными размерами.
Предварительно, необходимо в обязательном порядке расточить цилиндры до ремонтных размеров и оставить запас, примерно, в 0,03 миллиметра. Он необходим для дальнейшего хонингования поверхности. Во время хонингования обязательно выдерживайте точность диаметра, чтобы при монтаже нового поршня зазор соответствовал требованиям, предъявляемым к установке новых деталей.
Диаметр цилиндра замеряется в четырех поясах, а также в двух перпендикулярных плоскостях. Нутромер необходимо устанавливать строго перпендикулярно блоку цилиндров. Таким образом, можно исключить любые отклонения от правильности измерений.
Видео — Как правильно замерять поршень
Помимо размеров поршней, немало важным показателем является и их масса. Масса поршней бывает нормальная, или с изменением на плюс (минус) 5 грамм. Кроме того, к поршням необходимо правильно подобрать маслосъемные кольца, которые должны быть ремонтных размеров.
После того, как поршни будут подобраны и установлены, необходимо еще раз проверить величину зазоров. Если она находится в пределах нормы, то можно приступать к обратной сборке двигателя. Устанавливается ГБЦ, затем привод газораспределительного механизма. После этого, прикручивается крышка ГБЦ с новой прокладкой и все навесные элементы. Не забудьте залить масло, ОЖ и отрегулировать механизм газораспределения. После этого, скорее всего, придется выставить угол опережения зажигания. Теперь автомобиль полностью готов к работе.
На этом проверка зазора между поршнем и цилиндром завершена. Какой бы простой вам не казалась эта сложная процедура, ее, все же, рекомендуется производить только в специализированных станциях технического обслуживания, так как сборка блока цилиндров – дело ответственное и лучше доверить его профессионалам. Удачи на дорогах!
Как проверить зазор между поршнем и цилиндром самостоятельно
Как вы думаете, – что может быть общего между человеком и двигателем автомобиля? Когда человек маленький, он не может говорить и пожаловаться на то, что его беспокоит. Вырастая, мы начинаем говорить и сообщать о проблемах в организме.
Когда двигатель автомобиля новый, то ему не о чем нам сообщать. Он работает «как часы», но с возрастом двигатель начинает сообщать нам о проблемах «внутри себя». Как? Первое, что мы можем услышать – это стук двигателя. Вернее, стук деталей, расположенных внутри головки блока цилиндров или в самом блоке цилиндров.
Стук в двигателе может происходить по разным причинам, возникать при заводке, и пропадать после прогрева. Это может стучать и распредвал, и коленвал и т.д. Одной из причин появившегося стука может являться зазор между поршнем и цилиндром. Вот именно об этом сегодня и речь.
Важно помнить, как бы мы не хотели услышать стук в двигателе, он, рано или поздно, появится, и нужно быть готовым к этому неприятному явлении.
Содержание
- Почему изменяется зазор между поршнем и цилиндром
- Результат нарушения зазора между поршнем и цилиндром
- Как проверить зазор между поршнем и цилиндром
Почему изменяется зазор между поршнем и цилиндром
Да, а почему? Вроде бы и эксплуатация двигателя проходит в штатных условиях. И моторное масло заливаем в соответствие с рекомендациями производителя. То есть не жалеем денег, лишь бы двигатель был «накормлен» тем, что сказали давать производители.
- даже процесс правильной эксплуатации двигателя не сможет снять с повестки дня объективных причин увеличения зазора между поршнем и цилиндром. Не забывайте, что все детали двигателя работают в условиях экстремальных, а именно, в постоянно высоком температурном режиме.
Естественного изменения свойств металла никак не избежать. Отодвинуть по времени можно, а избежать нельзя. У поршня происходит естественный износ канавок для колец, отверстия под палец, юбки поршня;
- неисправности, возникающие в процессе эксплуатации. Незафиксированный перегрев двигателя, нарушение регулировки движущихся деталей, перекос цилиндров, некачественное масло, попадание топлива или охлаждающей жидкости в масло и т.д.
Эти и другие причины подводят нас к тому, что зазор между поршнем и цилиндром отклоняется от заданных параметров.
Результат нарушения зазора между поршнем и цилиндром
Увеличившийся зазор между поршнем и цилиндром приводит к стуку, ухудшению компрессии двигателя, перерасходу масла, и к выходу из строя двигателя. Уменьшение зазора между цилиндром и поршнем ведет к появлению задиров на зеркале цилиндра, перегреву деталей блока.
И в том и в другом случае требуется ремонт поршневой группы. Без вариантов. Или, если есть желание, подумайте о покупке нового двигателя. Но, всё же, дешевле вовремя провести ремонт цилиндров и поршней. А ремонт будет заключаться в замене цилиндров и расточке или хонинговке цилиндров.
Как проверить зазор между поршнем и цилиндром
Естественно, всё начинается с разборки головки блока цилиндров. По – большому счёту вы приступаете к капитальному ремонту двигателя. Ведь в результате диагностики, обязательно «выползут» проблемы с распредвалом, коленвалом, замена прокладок, подшипников, вкладышей и т.д. работы хватит. Но, начнём с того, с чего начали – замер зазора между поршнем и цилиндром.
Нам понадобятся два измерительных инструмента: нутромер – для измерения внутреннего диаметра цилиндра, и микрометр – для измерения диаметра поршней. Не станем распылять наше внимание на структуру материалов и технологию изготовления поршней. Перейдём к замеру зазора.
Как и цилиндры, поршни по своему наружному диаметру распределены на 5-ть классов: A, B, C, D, E. Замер диаметра поршня проводится в районе цилиндрической части юбки, на расстоянии от днища плоскости в 52,4 мм. Класс нашего поршня вы увидите на днище. Клеймо с соответствующей буквой.
Измерение диаметра цилиндра производится в четырёх поясах и в двух плоскостях, перпендикулярных друг другу (вдоль и поперек блока цилиндров). Если измерив, вы получаете зазор между поршнем и цилиндром выше 0,15 мм, то нужно приступать к подбору ремонтных поршней.
При условии, что зеркало цилиндра никоим образом не нарушено, подбираем поршни. Если же на зеркале цилиндра существуют механические повреждения, то вначале производится расточка или хонингование цилиндров. При этом не следует забывать, что расточка проводится до размера к ближайшему ремонтному размеру поршня.
После проведенного ремонта цилиндров, подбираем поршни соответствующего ремонтного размера. Для классических моделей двигателей отечественного производства, существует норма монтажного зазора между поршнем и цилиндром: 0,06 – 0,08мм (для 05 и 06 двигателей) и 0,05 – 0,07 (для 01 и 03двигателя).
Немаловажно, чтобы при подборе поршней вы обратили внимание и на их вес. Масса поршней одного двигателя не должна отклоняться на 2,5 грамма. Этот показатель важен для того, чтобы уменьшить вибрацию двигателя при разности масс возвратно-поступательного движения.
Ремонтные размеры поршней и цилиндров, а также нормы производителя к зазорам именно для вашего двигателя нужно уточнять в Руководстве по эксплуатации и ремонту именно вашей модели двигателя.
Удачи вам при измерении зазора между поршнем и цилиндром, и правильном подборе ремонтных деталей.
Тепловой зазор между поршнем и цилиндром
Содержание
- Задиры из-за недостаточного зазора на юбке поршня
- Задиры из-за недостаточного зазора соответственно рядом с бобышкой пальца (задиры под углом 45°)
- Задиры из-за недостаточного зазора в нижней части юбки поршня
Зазор между поршнем и цилиндром может в эксплуатации недопустимо сузиться почти до полного отсутствия при неправильной регулировке движущихся деталей, при перекосе цилиндров или же при термической перегрузке. Кроме того, температура поршня в работе значительно выше температуры цилиндра, что в эксплуатации приводит к различным характеристикам теплового расширения поршня и цилиндра. Поршень подвергается более сильному тепловому расширению, чем смежный цилиндр. Кроме того, алюминиевые материалы, по сравнению с серым чугуном имеют двойное тепловое расширение, что необходимо соответственно учесть в конструкции.
При уменьшающемся зазоре между поршнем и цилиндром сначала возникает полусухое трение,потому что масляная пленка на стенке цилиндра вытесняется расширяющимся поршнем. В результате этого несущие поверхности на юбке поршня сначала стираются до высокого блеска. Изза полусухого трения и возникающего тепла трения температура элементов становится еще выше. Поршень при этом оказывает все большее давление на стенку цилиндра. Функция масляной пленки при этом полностью исчезает. Поршень в цилиндре начинает работать без смазки. В результате этого появляются первые задиры с гладкой темной поверхностью.
Обобщенно можно привести следующие характерные признаки задиров из-за недостаточного зазора. За местами противодействия с зеркальным блеском следуют гладкие темные задиры. Задиры при заедании из-за недостаточного зазора имеются как на нагруженной стороне, так и на ненагруженной стороне.
Задиры из-за недостаточного зазора на юбке поршня
На поверхности юбки поршня имеется несколько одинаковых задиров
Задиры возникли на нагруженной и на ненагруженной стороне, т.е., к задирам на одной стороне поршня имеются соответствующие задиры на противоположной стороне. Поверхность задиров переходит от точек давления с зеркальным блеском в относительно гладкие места трения с темным цветом. Зона колец не имеет повреждений.
Зазор между юбкой поршня и рабочей поверхностью цилиндра был или слишком узким или суживался в недопустимой мере перекосами, которые возможно возникли только при эксплуатации двигателя.
В отличие от задиров в результате работы без смазки задиры из-за недостаточного зазора возникают всегда по истечении короткого времени эксплуатации после капитального ремонта двигателя.
Возможные причины повреждения
• недостаточный диаметр цилиндра.
• слишком сильная или неравномерная затяжка головки цилиндра (перетяжка цилиндра).
• неровные торцевые поверхности на цилиндре или на головке цилиндров.
• нечистая или неравномерная резьба в резьбовых отверстиях или на винтах головки цилиндров.
• заедание или неравномерная смазка на опорных поясках головок винтов
• использование неправильных или неподходящих прокладок головки блока цилиндров.
• перекос цилиндров в результате неравномерного нагрева из-за накипи, загрязнение или другие неисправности в системе охлаждения.
Задиры из-за недостаточного зазора соответственно рядом с бобышкой пальца (задиры под углом 45°)
Характерным для этого повреждения являются задиры, появляющиеся соответственно со смещением на 45° относительно оси бобышки, причем как на нагруженной стороне, так и на ненагруженной стороне. Поверхность задиров переходит от точек нажима с зеркальным блеском в относительно гладкие места трения с темным цветом. Поршневой палец имеет синий цвет побежалости, это признак тому, что в данном случае температура поршневого пальца была слишком высокой в результате недостаточного зазора или нехватки смазки.
Повреждение появляется, если зона вокруг крепления поршневого пальца слишком сильно нагревается. Поскольку в этой зоне поршень отличается довольно высокой жесткостью, возникает повышенное тепловое расширение в этой зоне и зазор между поршнем и рабочей поверхностью цилиндра сужается. Относительно тонкостенная и тем самым эластичная направляющая часть поршня может компенсировать повышенное тепловое расширение своей эластичностью. На переходе к жестким бобышкам пальца материал, однако, с большим усилием давит на стенку цилиндра, что в конечном счете приводит к прерыванию масляной пленки и к возникновению трения на поршне.
Возможные причины повреждения
• Слишком высокая нагрузка на двигатель, когда он еще не достиг рабочей температуры
Поршень может достичь своей полной рабочей температуры в течение 20 секунд, в то время как для холодного цилиндра для этого требуется намного больше времени. В результате различий в тепловом расширении обоих элементов поршень расширяется намного больше и быстрее, чем цилиндр. Зазор поршня сильно сужается в вышеописанных местах. Появляются названные повреждения.
• Слишком узкая посадка поршневого пальца в головке шатуна (горяче запрессованные шатуны). Слишком узкая посадка поршневого пальца в бобышке шатуна может привести к некруглости бобышки шатуна и тем самым также поршневого пальца. Это связано с различной толщиной стенки в бобышке шатуна. В то время как в направлении шатуна имеется больше материала и более толстые стенки, толщина стенки в конце шатуна намного меньше. При деформации поршневого пальца зазор в креплении пальца уменьшается. В результате этого недостаточный зазор в креплении вызывает повышенное тепло трения и таким образом повышенное тепловое расширение в данной зоне.
• задиры в бобышке шатуна из-за недостаточной смазки при первом вводе двигателя в эксплуатацию.
При сборке поршневой палец не смазывается или смазывается недостаточно. Перед тем как масло при первом пуске в эксплуатацию поступает к месту опоры, нет достаточной смазки, это вызывает заедание опоры пальца и тем самым повышенное образование тепла.
• Дефект монтажа при горячей посадке поршневого пальца (горяче запрессованный шатун)
Кроме вышеназванной смазки пальца при горячей посадке поршневого пальца бобышки шатуна необходимо обратить внимание на то, чтобы непосредственно после вставки пальца подшипник пальца не был подвергнут контролю на свободный ход путем качающего движения. Непосредственно после вставки холодного пальца в горячий шатун температура между обеими деталями выравнивается. Поршневой палец может стать очень горячим. Он расширяется и заклинивается в еще холодном подшипнике пальца. Если подшипник в этом состояние перемещают, здесь может возникнуть первое место трения или задир, который в эксплуатации приводит к тяжелому ходу подшипника и тем самым к повышенному трению и образованию тепла. По этой причине смонтированные детали должны остыть спокойно, опору следует контролировать на свободный ход только после остывания.
Задиры из-за недостаточного зазора в нижней части юбки поршня
На нижних концах юбки поршень имеет типичные задиры с местами нажима на одной стороне и на противоположной стороне. Следы переходят от места нажима с зеркальным блеском в гладкие темные задиры, (рис. 1) Все остальные части поршня не имеют особенностей. Те же самые задиры имеет соответствующая мокрая рабочая втулка цилиндра (рис. 2) в нижней части, там где она на наружном диаметре несколькими уплотнительными кольцами уплотняется к картеру от попадания воды и масла,. Все остальные части рабочей втулки цилиндра также не имеют особенностей.
Тот факт, что задиры имеют характерные признаки заедания из-за недостаточного зазора как на поршне, так и на рабочей втулке цилиндра, указывает на то, что зазор между поршнем и цилиндром в нижней части, вероятно, из-за деформации цилиндра был настолько сужен, что масляная пленка прервалась.
Возможные причины повреждения
• неправильные по размерам или неподходящие кольца круглого сечения могут привести к деформации рабочей втулки до полного отсутствия зазора юбки поршня. Для обеспечения достаточно большого пространства набухания уплотнительные кольца должны заполнить лишь ок. 70 % объема канавок.
• использование дополнительного уплотнительного средства в кольцах круглого сечения
Для используемых для данной цели уплотнительных колец характерно набухание в работе под воздействием масла. Это свойство так и предусмотрено, чтобы обеспечить герметичность в течение длительного времени. Поэтому не разрешается использование дополнительного уплотнительного средства. Свободное пространство было бы полностью заполнено и кольца круглого сечения не могли бы расширяться в работе.
• В пазах для уплотнительных колец в корпусе, возможно, сохранились еще остатки старых уплотнительных колец (см. выше).
• Уплотнительные кольца не могут обеспечить безупречную герметизацию, если они перекошены при вводе рабочей втулки. Поэтому они должны быть всегда смазаны средством скольжения перед монтажом рабочей втулки.
Все в курсе, что: мощность и «тяга» мотора напрямую зависят от состояния деталей цилиндро-поршневой группы. Знаете и то, что поверхности трения этих деталей изнашиваются из-за попадания на них пыли, использования некачественных масел и просто от длительной работы. Поскольку замерить мощность двигателя в бытовых условиях практически нельзя, многие используют косвенный показатель — максимальную скорость, а кто-то замеряет компрессию в цилиндре. Второй способ оценки мощности более предпочтительный, ведь скоростные возможности аппарата могут снизиться, например, из-за того, что закоксовалась выпускная система, нарушилась регулировка зажигания, разладилась работа карбюратора.
Если двигатель действительно «подсел», не спешите сразу растачивать цилиндр под ремонтный размер. Умудренные опытом люди обычно придерживаются следующей последовательности в действиях: в первый раз меняют кольца, во второй — кольца и поршень (оба раза — на номинальные размеры), потом еще раз меняют кольца (тоже на номинальные) и лишь затем растачивают цилиндр под первый ремонт с последующей установкой ремонтного поршня с кольцами. Когда начинать эти замены,- зависит в основном от условии эксплуатации. Первая замена колец может понадобиться через шесть-семь (и до 25 у большекубатурных аппаратов) тысяч километров, а поршня — через 15-40.
Оценить степень износа можно, если разобрать цилиндро-поршневую группу. Проводя разборку, нужно твердо помнить две вещи.
Первая — не уроните стопорное кольцо в кривошипную камеру. Чтобы избежать этой неприятности, сразу закройте камеру, скажем, тряпкой.
И вторая -не загните шатун, когда станете молотком выбивать палец. Лучше всего пользоваться съемником.
Итак, поршень у вас в руках. Аккуратно снимите с него кольца (используйте три-четыре подкладных пластинки (рис. 1) и вставьте их в верхнюю часть цилиндра.
«Выровняйте» кольца поршнем — вставьте его в цилиндр снизу и измерьте зазоры в замках колец (рис 2) Если они превышают 3 мм, кольца подлежат замене. Зазоры в замках новых колец не должны превышать 0,2-0,4 мм.
Сразу оцените и состояние поршня: если зазор между ним и цилиндром более 0,3-0,4 мм, поршень требует замены. При подборе нового поршня удобно руководствоваться «дедовским» методом: вымытый и смазанный моторным маслом цилиндр лежит на столе, а вы опускаете в него поршень. «Хороший» поршень должен опускаться под тяжестью собственного веса около одной секунды. Если он со стуком провалился или, что еще хуже, застрял «на полпути», — ищите другой поршень. У каждой модели мотоциклов существует от двух до четырех размерных групп поршней, их разница в диаметре может составлять от 0,01-0,025 мм. Маркировка группы обычно наносится клеймом на днище поршня и на нижнем торце цилиндра. Следите, чтобы эти цифры совпадали.
Особое внимание уделите состоянию бывшего в эксплуатации поршня. Осмотрите его на предмет наличия трещин и, если таковые имеются, — выбрасывайте его на помойку. Как правило, трещины возникают в зоне бобышек на внутренней поверхности поршня и по углам продувочных окон. Так или иначе, трещины всегда образуются в местах повышенных концентраций напряжений (рис. 3).
К ним относятся острые внутренние углы, остающиеся после механической обработки поршня, или из-за брака литья. Такие места скруглите надфилем, шарошкой и тщательно заполируйте.
Однако трещины — не единственная опасность, подстерегающая поршень в его бесконечных возвратно-поступательных движениях. Сюрприз могут преподнести и поршневые кольца. Чаще всего приходится чистить от нагара канавки колец, когда сами кольца теряют подвижность («залегают»). Делайте это обломком старого кольца или острым предметом типа шабера. Использовать для чистки надфили или ножовочные полотна крайне нежелательно: можно вместе с нагаром счистить и «мясо» поршня. Последствия вы себе представляете: из-за утечки газов между кольцом и поршнем падает компрессия со всеми вытекающими последствиями.
В этих же канавках установлены стопорные штифты. Они фиксируют кольца, чтобы те не проворачивались на поршне. Если в двухтактном двигателе, в цилиндре которого впускное, выпускное и продувочные окна, кольцо начнет вращаться (что и происходит при выпадении штифта), то в один ужасный момент стык кольца неминуемо окажется в зоне впускного (или выпускного) окна. Кольцо стремится разжаться, его концы немного распрямляются и входят в окно. В следующее мгновение противоположная кромка окна срезает высунувшиеся «на свободу» концы кольца, и двигатель с лязгом и грохотом выплевывает в глушитель его обломки. Но не ищите штифтов на поршнях четырехтактных двигателей. На них кольца просто разводятся стыками в противоположные стороны, ведь «опасных» окон нет вовсе. Разница ясна?! Так вот, теперь мы знаем, что стопорный штифт в двухтактном моторе -очень важная деталь. «Правильный» штифт ориентирует стык кольца на участок гильзы без окон (рис. 4)
Следующий объект изучения — отверстие под поршневой палец. В канавках этого отверстия с каждой стороны поршня установлены стопорные кольца с загнутыми усиками. Назначение усиков — облегчить монтаж-демонтаж стопорных колец в поршне. С ними такая история: конструкция подобных стопорных колец не прижилась на спортивных двигателях — из-за опасности того, что усики подрежутся поршневым пальцем и попадут в цилиндр. Поэтому на всех современных высокофорсированных двигателях применяются исключительно «безусые» стопорные кольца. А для удобства их демонтажа на поршне предусмотрена специальная канавка. Но какой бы формы ни было стопорное кольцо, оно должно утопать в канавке не менее чем на половину диаметра проволоки, из которой изготовлено. Кстати, рекомендуем проверенный способ, страхующий от выталкивания стопорных колец поршневым пальцем. Удалите у колец усики, а на торцах пальца по наружному диаметру немного увеличьте фаски (рис. 5). Теперь палец будет надежнее запирать такой фаской стопорное кольцо.
При нагревании двигателя зазор между поршнем и гильзой должен быть равномерным по всему ее периметру. Поэтому поршень в холодном состоянии имеет весьма сложную форму: по высоте — конический, ступенчатый или бочкообразный, а в поперечном сечении -овальный. Наибольшая овальность — в зоне отверстия под поршневой палец (до 0,03 мм). Поэтому, измеряя поршень, не удивляйтесь тому, что он «неправильный».
Итак, вы подобрали поршень к цилиндру, теперь ищите подходящий палец. Диаметры пальцев, как поршней и цилиндров, делятся на несколько (до четырех) размерных групп. Подбирайте палец согласно предписаниям заводской инструкции. Обычно на торец пальца ставят точку краской определенного цвета. Такого же цвета метка наносится на бобышке внутри поршня. При комнатной температуре поршневые пальцы двигателей современных мотоциклов обычно входят в бобышку поршня под действием небольшого усилия. Однако на старых моделях пальцы в поршень прессовались, для чего поршни нагревали в кипящей воде… Опять-таки, внимательно почитайте инструкцию к своему мотоциклу.
Напоминаем еще раз: работая со стопорными колечками, закройте картер тряпкой. Эта простая операция избавит от того, что вам придется до посинения трясти перевернутый мотор, чтобы удалить упавшую внутрь деталь. Когда установите стопорные колечки (с усами или без), проверьте правильность их посадки: каждое кольцо должно сидеть в канавке плотно, но прокручиваться по окружности при надавливании шилом на один из ее краев.
Уже как анекдот постоянно слышишь об «умельцах», которые устанавливают поршни «задом наперед». Избежать неминуемой поломки колец поможет стрелка, выбитая на всех без исключения днищах поршней отечественных двухтактных двигателей — она и указывает, как следует сориентировать поршень. Правда, у всех «Иж-Юпитеров» стрелка смотрит в карбюратор. Если стрелка отсутствует или не просматривается, сориентируйте поршень по расположению стопорных штифтов: они должны «смотреть» на вертикальные сектора гильзы без окон…….
Причин тому множество. Например, такие повреждения могли случиться из-за недостаточного зазора. Еще одна причина появления задиров — работа мотора без смазки.
Зазор между поршнем и цилиндром, при эксплуатации, может недопустимо уменьшится (почти до полного исчезновения) при неправильном монтаже движущихся деталей, при перекосе гильз цилиндров или же — при перегреве. Кроме того, температура поршня во время работы, значительно выше температуры цилиндра, поэтому поршень расширяется сильнее, чем смежный цилиндр. Кроме того, алюминий, по сравнению с серым чугуном имеет удвоенное тепловое расширение, что тоже необходимо учесть. При уменьшающемся зазоре между поршнем и цилиндром сначала возникает полусухое трение, потому что масляная пленка со стенки цилиндра вытесняется расширяющимся поршнем. Поэтому несущие поверхности на юбке поршня сначала стираются до блеска. Из-за полусухого трения, и нагрева от него, температура деталей становится еще выше. Поршень оказывает все большее давление на стенку цилиндра. Масляная пленка исчезает полностью, и поршень начинает работать без смазки. В результате появляются первые задиры с гладкой темной поверхностью. В общем можно указать следующие характерные признаки задиров из-за недостаточного зазора: за участками с зеркальным блеском следуют гладкие темные задиры. Задиры имеются как на нагруженной стороне, так и на ненагруженной стороне поршня.
Задиры, из-за недостаточного зазора, на юбке поршня
Описание картины: На поверхности юбки поршня имеется несколько одинаковых задиров. Они возникли на нагруженной и на ненагруженной стороне, то есть, задирам на одной стороне поршня соответствуют задиры на противоположной стороне. Поверхность повреждений переходит от точек давления с зеркальным блеском в относительно гладкие места трения с темным цветом.
— Недостаточный диаметр цилиндра;
— Слишком сильная или неравномерная затяжка головки блока цилиндров;
— Неровные привалочные поверхности на блоке цилиндров или на головке блока;
— Грязная или изношенная резьба в отверстиях блока или на болтах;
— Заедание болтов или неравномерная смазка на опорных поясках головок болтов;
— Использование неподходящих прокладок головки блока цилиндров;
— Деформация цилиндров в результате неравномерного нагрева из-за накипи, загрязнения или других неисправностей системы охлаждения.
Задиры, из-за недостаточного зазора, рядом с бобышками пальца (задиры под углом 45°)
Характерными являются задиры, со смещением на 45° относительно оси бобышек, причем как на нагруженной стороне, так и на ненагруженной стороне. Их поверхность переходит от точек нажима с зеркальным блеском в относительно гладкие места трения с темным цветом. Поршневой палец имеет синий цвет побежалости. Это признак того, что температура пальца была слишком высокой из-за недостаточного зазора или нехватки смазки.
Появляется, когда слишком сильно нагревается зона вокруг бобышек поршневого пальца. Поскольку, в этом месте поршень отличается довольно высокой жесткостью, возникает повышенное тепловое расширение и зазор между поршнем и поверхностью цилиндра уменьшается. Относительно тонкостенная направляющая часть поршня может компенсировать повышенное тепловое расширение за счет своей эластичности. Однако, в местах перехода к жестким бобышкам металл с большим усилием давит на стенку цилиндра. Это, в конечном счете, приводит к разрыву масляной пленки и к возникновению задиров на поршне.
Возможные причины повреждения:
— Слишком высокая нагрузка на двигатель, когда он еще не прогрелся. Поршень может достичь своей нормальной рабочей температуры в течение 20 секунд, в то время как холодному цилиндру для этого требуется намного больше времени. В результате поршень расширяется намного больше и быстрее, чем цилиндр. В вышеописанных местах зазор сильно уменьшается, и появляются задиры.
— Слишком плотная посадка поршневого пальца в верхней головке шатуна (горячезапрессованные шатуны). Слишком плотная посадка может привести к некруглости отверстия в шатуне и, тем самым, поршневого пальца. Это связано с различной толщиной стенок верхней головки. В направлении стержня шатуна металла больше и стенки более толстые, а в других направлениях толщина металла намного меньше. При деформации поршневого пальца зазор между ним и отверстиями в бобышках уменьшается. Поэтому в месте контакта выделяется много тепла, что вызывает избыточное тепловое расширение в этой зоне.
— Дефект монтажа при горячей посадке поршневого пальца. Кроме вышеназванного дефекта при установке пальца, необходимо обратить внимание и на то, чтобы сразу после установки пальца подшипники пальца не проверялись на свободный ход путем покачивания поршня. Сразу после монтажа холодного пальца в горячий шатун температура между обеими деталями выравнивается. И поршневой палец может стать очень горячим. Он расширяется и заклинивается в холодном поршне. Если поршень, в этом состоянии, покачать, в отверстиях бобышек может возникнуть задир, который в эксплуатации приведет к подшипников и, тем самым, к местному перегреву. Поэтому собранные детали должны остыть, а свободное перемещение поршня на пальце следует проверять только после охлаждения!
— Задиры верхней головки шатуна, из-за недостаточной смазки, при первом запуске двигателя после ремонта. При сборке поршневой палец не смазывали или смазывали недостаточно. Перед тем, как масло при первом запуске поступит во втулку ВГШ, смазка недостаточна, что вызывает заедание пальца и, тем самым, повышенное выделение тепла.
Задиры, из-за недостаточного зазора, в нижней части юбки поршня
На нижней части юбки поршень имеет типичные задиры с местами нажима на одной и на противоположной стороне. Следы переходят от места нажима с зеркальным блеском в гладкие темные задиры. Все остальные части поршня повреждений не имеют. Те же самые задиры имеет соответствующая мокрая гильза цилиндра в нижней части, там, где она уплотняется с картером, от попадания воды. Остальная поверхность гильзы цилиндра также не повреждена.
Детали имеют характерные признаки заедания из-за недостаточного зазора. Это указывает на то, что зазор между поршнем и цилиндром в нижней части, вероятно, из-за деформации цилиндра, был настолько мал, что масляная пленка разрушилась.
Возможные причины повреждения:
— Уплотнительные кольца круглого сечения не смогли нормально расшириться при работе. Неподходящие кольца круглого сечения могут привести к деформации гильзы, вплоть до полного отсутствия зазора между ней и юбкой поршня. Для получения достаточной свободы уплотнительные кольца должны заполнять примерно 70 % объема канавок;
— Для уплотнительных колец, используемых для данной цели, характерно набухание под воздействием масла. Эта особенность предусмотрена, чтобы обеспечить герметичность в течение длительного времени. Поэтому нельзя использовать дополнительный герметик;
— В проточках, для уплотнительных колец, возможно, сохранились остатки старых уплотнений;
— Уплотнительные кольца не могут обеспечить отличную герметизацию, если они были перекошены при монтаже гильзы. Поэтому их всегда надо смазывать перед монтажом.
Зазоры между поршнем и цилиндром ваз
Содержание
- маркировка поршней
- маркировка поршней ваз 2106, подгруппа
- Как меняется зазор между поршнем и цилиндром в процессе эксплуатации?
- Как снять головку блока цилиндров?
- Какие существуют нормы зазоров между поршнями и цилиндрами
- Видео – Как правильно замерять поршень
Поршневая группа двигателя включает в себя – поршень, поршневые кольца и поршневой палец. Общая конструкция поршневой группы сложилась еще в период появления первых двигателей внутреннего сгорания. С тех пор ни один из элементов поршневой группы не утратил своего функционального назначения.
Поршень, является наиболее важным элементом любого двигателя внутреннего сгорания.
Именно на эту деталь, выпадает основная нагрузка по преобразованию энергии расширяющихся газов в энергию вращения коленчатого вала. Свойства, которыми должен обладать поршень, трудно совместимы и технически тяжело реализуемы. Вот некоторые требования, которым должна соответствовать эта деталь:
– температура в камере сгорания может достигать более 2000°С а температура поршня, без риска потери прочности материала, не должна превышать 350°С;
– после сгорания бензино-воздушной смеси, давление в камере сгорания может достигать 80 атмосфер. При таком давлении, оказываемое на днище усилие, будет составлять свыше 4-х тонн. Толщина стенок и днища поршня должна обеспечивать возможность выдерживать значительные нагрузки. Но любое увеличение массы изделия приводит к увеличению динамических нагрузок на элементы двигателя, что в свою очередь, ведет к усилению конструкции и росту массы двигателя;
– зазор между поршнем и поверхностью цилиндра должен обеспечивать эффективную смазку и возможность перемещения с минимальными потерями на трение. Но в тоже время зазор должен учитывать тепловое расширение и исключить возможность заклинивания.
– изготовление должно быть достаточно дешевым и отвечать условиям массового производства.
Очертания поршня за более стопятидесятилетнюю историю двигателя внутреннего сгорания мало изменились.
В конструкции поршня можно выделить несколько зон, каждая из которых, имеет свое функциональное назначение.
Днище поршня – поверхность, обращенная к камере сгорания. Днище, своим профилем, определяет нижнюю поверхность камеры сгорания.
Форма днища зависит от формы камеры сгорания, расположения клапанов, от особенности подачи топливо-воздушной смеси в камеру сгорания и объема самой камеры.
маркировка поршней
Днища разных моделей применяемых на двигателях ВАЗ приведены на рисунке. Поршни ВАЗ 21213 и ВАЗ 21230 отличаются нанесенной маркировкой.
Маркировка наносится на поверхность рядом с отверстием под поршневой палец.
На поршне ВАЗ 21213 нанесены цифры -«213», на модели ВАЗ 2123 – «23».
На модели ВАЗ 21080, ВАЗ 21083, ВАЗ 21100 нанесена соответствующая маркировка – «08»,»083″, «10».
Поршень 2108 имеет диаметр 76мм , модели 21083 и 2110 – 82мм.
Поршни ВАЗ 2112 и ВАЗ 21124, имеют соответствующую маркировку – «12»и «24» и отличаются глубиной выборки под клапана.
Модели 21126 и 11194 отличаются диаметром.
маркировка поршней ваз 2106, подгруппа
Если углубления на днище увеличивают объем камеры сгорания, то для уменьшения объема применяют вытеснители. Вытеснителем называют объем металла, который находится выше плоскости днища.
«Жаровым поясом»(огневым) , называют расстояние от днища до канавки первого поршневого кольца. Чем ближе располагаются поршневые кольца к днищу, тем более высокой тепловой нагрузке они подвергаются, тем больше сокращается их ресурс.
Уплотняющий участок – это участок канавок, расположенных на боковой цилиндрической поверхности поршня. Канавки предназначены для установки поршневых колец. Поршневые кольца обеспечивают подвижное уплотнение. На всех моделях для двигателей ВАЗ, выполнены две канавки под компрессионные кольца и одна канавка под маслосъемное кольцо.
В канавке под маслосъемное кольцо есть отверстия, через которые отводится излишек масла во внутреннюю полость поршня. Уплотняющий участок выполняет еще одну очень важную функцию – через установленные поршневые кольца, осуществляется отвод значительной части тепла от поршня к цилиндру. Если конструкция изделия не будет предусматривать эффективный отвод тепла от днища, то это приведет к его прогоранию.
По расчетам, через компрессионные кольца, передается до 60-70% выделенного тепла. Однако это требует плотного прилегания поршневых колец к цилиндру и к поверхностям канавок. Для обеспечения работоспособности, торцевой зазор первого компрессионного кольца в канавке должен составлять 0,045-0,070мм.
Для второго компрессионного кольца зазор – 0,035-0,060мм, для маслосъемного – 0,025-,0050мм. Между внутренней поверхностью кольца и канавки должен быть радиальный зазор – 0,2-0,3мм.
Головку поршня образуют днище и уплотняющая часть.
Расстояние от оси поршневого пальца до днища, называют компрессионной высотой поршня.
«Юбкой», называют нижнюю часть поршня. На этом участке находятся бобышки с отверстиями – место, куда устанавливается поршневой палец. Внешняя поверхность юбки, исполняет роль опорной и направляющей поверхности. Юбка обеспечивает соосность положения детали к оси цилиндра блока.
Кроме того, боковая поверхность юбки участвует в передаче к цилиндру возникающих поперечных усилий. На поверхность юбки(или на все изделие) могут наноситься защитные покрытия улучающие прирабатываемость и снижающих трение.
Покрытие слоем олова позволяет сгладить неточности профиля и предотвратить наволакивание алюминия на поверхности цилиндра. Могут применяться покрытия созданные на основе графита и дисульфида молибдена. Другой способ, снижающий потери на трение – нанесение на юбке канавок специального профиля. Глубина канавок составляет 0,01-0,015мм. При движении, канавки не только удерживают масло, но и создают гидродинамическую силу, которая препятствует контакту со стенками цилиндра.
Одним из факторов определяющих геометрию поршня, является необходимость снижения сил трения. Для этого требуется обеспечение определенной толщины масляного слоя в зазоре между поршнем и стенками цилиндра. Причем маленький зазор повлечет за собой увеличение сил трения и как следствие повышение нагрева деталей и их ускоренный износ а возможно и заклинивание.
Слишком большой зазор, увеличит шумность двигателя, приведет к росту динамических нагрузок на сопрягаемые детали и будет способствовать их ускоренному износу. Поэтому величина зазора подбирается в соответствии с рекомендациями для конкретного типа двигателя.
В истории применения конструкций поршней для двигателей ВАЗ, просматриваются этапы влияния нескольких европейских конструкторских школ. На первых моделях двигателей ВАЗ применяется «итальянская» конструкция. Поршни отличаются большой компрессионной высотой, широкой опорной поверхностью юбки. Поверхность изделия покрыта слоем олова. В разработке последующих конструкций принимают участие немецкие компании.
У поршней уменьшается компрессионная высота. На юбке применяется микропрофиль – специальный профиль канавок, для удержания смазки в зоне трения. Поршни моделей ВАЗ 21126 и ВАЗ 11194 получают Т-образный профиль и рассчитаны на установку «тонких» поршневых колец. Так внешне сравнивая модели от 2101 до 21126, можно получить представление об общих тенденциях совершенствования конструкции , основанных на новых научных разработках.
В процессе работы, различные участки поршня нагреваются не равномерно, следовательно, и тепловое расширение будет больше там, где выше температура и больше объем металла.
В связи с этим, на уровне днища размер выполняют меньшим, чем диаметр в средней части. Таким образом, в продольном сечении профиль будет коническим. Нижняя часть юбки тоже может иметь меньший диаметр. Это позволяет, при движении вниз, в пространстве между юбкой и цилиндром, создавать масляный клин, который улучшает центрирование в цилиндре.
Для компенсации тепловых деформаций, в поперечном сечении поршень выполнен виде овала. Это связано с тем, что в районе бобышек под поршневой палец сосредоточен значительный объем металла. При нагреве, в плоскости поршневого пальца, расширение будет осуществляться в большей степени. Овальность и бочкообразность детали в холодном состоянии, позволяет иметь поршень, приближающийся к цилиндрической форме, при работающем двигателе.
Такая форма изделия создает сложности при контроле его диаметра. Фактический диаметр можно определить, только замеряя его в плоскости перпендикулярной оси отверстия под поршневой палец на определенном расстоянии от днища.
При этом, для разных моделей это расстояние будет отличаться. Тепловые нагрузки порождают еще одну проблему. Поршни изготавливают из алюминиевого кремнесодержащего сплава, а для блока цилиндров используют чугун. У этих материалов разная теплопроводность и разный коэффициент теплового расширения. Это приводит к тому, что в начале работы двигателя, поршень нагревается и увеличивается в диаметре быстрее, чем увеличивается внутренний диаметр цилиндра.
При и без того малых зазорах, это может приводить к повышенному износу цилиндров, а в худшем случае, к заклиниванию поршня. Для решения этой проблемы, во время отливки поршня, в тело заготовки внедряют специальные стальные или чугунные элементы, которые сдерживают резкое изменение диаметра. Для уменьшения теплового расширения и отвода тепла, на некоторых типах двигателя, используются системы подачи масла во внутреннюю полость поршня.
Поршневой палец обеспечивает шарнирное соединение поршня и верхней головки шатуна. Во время работы двигателя, на поршневой палец воздействуют значительные переменные силы.
Палец и отверстия под палец должны сопрягаться с минимальным зазором, обеспечивающим смазку. На двигателях ВАЗ используется два типа шарнирного соединения «поршень-палец-шатун». На поршнях моделей 2101, 21011, 2105, 2108, 21083 – палец устанавливается в верхней головке шатуна по плотной посадке, исключающей его вращение. Отверстие в поршне под поршневой палец выполнено с зазором, обеспечивая свободное вращение.
В дальнейшем от этой схемы отказались и перешли на схему с «плавающим» пальцем. На поршнях моделей 21213, 2110, 2112, 21124, 21126, 11194, 21128 – палец устанавливается с минимальным зазором и в головке шатуна, и в отверстиях поршня. Для исключения осевого смещения пальца, в поршне, в отверстиях под поршневой палец устанавливаются стопорные кольца. Во время работы, у пальца есть возможность проворачиваться, обеспечивая равномерный износ поверхностей.
Для обеспечения надежной смазки пальцев, в бобышках предусмотрены специальные отверстия.
По результатам фактического замера отверстия под поршневой палец, поршням присваивается одна из трех категорий(1-я, 2-я, 3-я). Разница в размерах для категорий составляет – 0,004мм. Номер категории клеймится на днище. Для обеспечения необходимого зазора, поршневые пальцы, по наружному диаметру подразделяются на три класса.
Отличие в размерах составляет – 0,004 мм. Маркировка класса производится краской по торцу пальца: синий цвет – первый класс, зеленый – второй, красный – третий класс. При сборке, поршню первой категории должен подбираться палец первого класса и т.д.
Особенностью работы шатунного механизма, является то, что до достижения верхней мертвой точки, поршень прижат к одной стороне цилиндра, а после прохождения ВМТ – к другой стороне цилиндра.
При приближении к верхней мертвой точке, на поршень действует максимальная нагрузка, следовательно растет сила давления на палец. Возростающие силы трения препятствуют повороту поршня на пальце. При таких условиях поворот может происходит скачкообразно, со стуком о стенку цилиндра.
Для того, чтобы снизить динамические нагрузки и шум, применяют поршни со смещенным отверстием под поршневой палец. Ось отверстия смещена в горизонтальной плоскости от оси поршня. В работающем двигателе это приводит к возникновению момента силы, который облегчает преодоление сил трения. Такое конструктивное решение позволяет добиться плавности, при смене точек контакта поршня с цилиндром.
На такие изделия обязательно наносится метка для правильной ориентации при его установке. Однако, чем больше будет износ цилиндров и юбки, тем в большей степени будет проявляться стук в цилиндре.
Существуют поршни, в которых применяется не только горизонтальное смещение оси пальца, но и вертикальное. Такое смещение ведет к уменьшению компрессионной высоты.
Поршни, с дополнительным смещением оси отверстия под палец вверх, применяются для тюнинговой доработки двигателя. В качестве основной характеристики для таких поршней используется величина смещения, указывающая на сколько смещен центр отверстия под палец, по сравнению со стандартным изделием.
На рынке продаж, поршень представлен значительным количеством отечественных и иностранных производителей. Независимо от производителя, они должны соответствовать требованиям, рассчитанным для конкретной модели двигателя. Поршни, входящие в комплект, не должны отличаться по массе более чем на ±2,5 грамм. Это позволит снизить вибрации работающего двигателя. Для розничной сети, в комплекты подбираются поршни одной весовой группы. В случае необходимости можно осуществить подгонку поршня по массе.
Зазор между цилиндром и поверхностью поршня должен соответствовать величине установленной для данной модели двигателя.
Поршни номинального размера по своему диаметру относят к одному из пяти классов. Различие между классами составляет 0,01 мм.
Классы маркируются на днище буквами – (А, В, С, D, Е).
В качестве запасных частей поставляются поршни классов – А, С, Е. Этих размеров достаточно, чтобы осуществить подбор деталей для любого блока цилиндров и обеспечить необходимый зазор.
Поршни ВАЗ 11194 и ВАЗ 21126 имеют только три класса (A, B, C) с размерным шагом – 0,01 мм. Кроме номинальных размеров, изготавливаются поршни 2-х ремонтных размеров, с увеличенным наружным диаметром на 0,4 и 0,8 мм.
Для распознавания, на днищах ремонтных изделий ставится маркировка: символ «треугольник» соответствует первому ремонтному размеру(с увеличением наружного диаметра на 0,4 мм), символ «квадрат» – увеличение диаметра на 0,8 мм. До 1986 г. ремонтные размеры отличались от современных.
Так для двигателя 2101 существовало три ремонтных размера: на 0,2мм., 0,4мм., 0,6 мм; для двигателя 21011 два размера: 0,4 мм. и 0,7 мм.
В качестве материала для изготовления поршней применяются сплавы алюминия. Использование кремния в составе сплава, позволило снизить коэффициент теплового расширения и увеличить износостойкость.
Сплавы, где содержание кремния может достигать 13%, называют – эвтектическими. Сплавы с более высоким содержанием кремния относят к заэвтектическим сплавам. Повышение процента содержания кремния улучшает теплопроводные характеристики, однако приводит к тому, что при охлаждении в сплаве происходит выделение кремния в виде зерен размером 0.5-1.0мм.
Это приводит к ухудшению литейных и механических свойств. Для улучшения физико-механических свойств, в сплавы вводят легирующие добавки меди, марганца, никеля, хрома.
Существует два основных способа получения заготовки поршня. Отливка в кокиль – специальную форму, является более распространенным способом. Другой способ – горячая штамповка(ковка). После этапов механической обработки, изделие подвергают термической обработке для повышения твердости, прочности и износостойкости, а также для снятия остаточных напряжений в металле.
Структура кованого металла позволяет повысить прочностные характеристики изделия. Но есть существенные недостатки кованых изделий классической конструкции( с высокой юбкой)– они получаются более тяжелыми. Кроме того, в кованных деталях, невозможно использовать термокомпенсирующие кольца или пластины. Увеличенный объем металла ведет к увеличенной тепловой деформации и необходимости увеличивать зазор между поршнем и цилиндром.
И как следствие – повышенный шум, износ цилиндров, расход масла. Применение кованых поршней оправдано в тех случаях, когда большую часть времени двигатель автомобиля эксплуатируется на предельных режимах.
В современном конструировании поршней, наблюдаются следующие тенденции: уменьшение веса, использования «тонких» поршневых колец, уменьшение компрессионной высоты, использование коротких поршневых пальцев, применение защитных покрытий.
Все это, нашло свое применение, в конструкции Т-образных поршней. Наименование конструкции обусловлено схожестью профиля детали с буквой «Т». На этих изделиях, юбка уменьшена и по высоте и по площади направляющей части. В качестве материала для изготовления таких поршней используется заэвтектический сплав, с большим содержанием кремния. Поршни Т-образной конструкции практически всегда изготавливаются горячей штамповкой.
Принятие разработчиками решения о применении той или иной конструкции поршня всегда предшествует расчет и глубокий анализ поведения всех узлов шатунно-поршневой группы.
Детали современных двигателей рассчитаны на пределе возможностей конструкции и материалов. В таких расчетах предпочтение отдается конструкциям с минимальной стоимостью обеспечивающих утвержденный ресурс и не более. Поэтому любое отклонение от штатных режимов работы двигателя ведет к сокращению ресурса тех или иных деталей и узлов.
Вопрос-ответ
Для чего выемки на поршнях ваз?
Это выемки под клапана. Для того что бы не погнуло клапана при обрыве.
Проверьте отклонение от плоскостности поверхности разъема блока с головкой цилиндров. Приложите штангенциркуль (или линейку) к плоскости:
– в середине блока;
– в продольном и поперечном направлениях;
– по диагоналям плоскости. В каждом положении плоским щупом определите зазор между линейкой и плоскостью. Это и есть отклонение от плоскости. Если отклонение превышает 0,1 мм, замените блок.
Проверьте зазоры между поршнями и цилиндрами.
Зазор определяется как разность между замеренными диаметрами поршня и цилиндра. Номинальный зазор равен 0,025–0,045 мм, предельно допустимый – 0,15 мм.
Если зазор не превышает 0,15 мм, можно подобрать поршни из последующих классов, чтобы зазор был как можно ближе к номинальному.
Если зазор превышает 0,15 мм, расточите цилиндры и установите поршни соответствующего ремонтного размера.
Измерьте диаметр поршня на расстоянии 10 мм от нижнего края юбки в плоскости, перпендикулярной поршневому пальцу.
При замене деталей шатунно-поршневой группы необходимо подобрать поршни к цилиндрам по классу и одной группы по массе, а также поршневые пальцы к поршням по классу и шатуны по массе.
Для подбора поршней к цилиндрам вычислите зазор между ними.
Для удобства подбора поршней к цилиндрам их делят в зависимости от диаметров на пять классов через 0,01 мм: A, B, C, D, E (таблица).
В запасные части поставляют поршни номинального размера трех классов: A, C, E и двух ремонтных размеров (1-й ремонтный размер — увеличенный на 0,4 мм, 2-й — на 0,8 мм).
По массе поршни разбиты на три группы: нормальную, увеличенную на 5 г и уменьшенную на 5 г. На двигатель должны быть установлены поршни одной группы.
Для поршней ремонтных размеров в запчасти поставляют кольца ремо
нтных размеров, увеличенных на 0,4 и 0,8 мм. На кольцах 1-го ремонтного размера выбито число «40», 2-го – «80».
Обозначения класса цилиндров выбиты на нижней плоскости блока (привалочная поверхность под масляный картер) напротив каждого цилиндра.
На днище поршня выбиты следующие данные:
1 – класс поршня по диаметру;
2 – стрелка, показывающая направление установки поршня;
3 –модель двигателя.
Пальцы с трещинами замените.
Палец должен легко входить в поршень от усилия большого пальца руки.
Вставьте палец в поршень.
Если при покачивании пальца ощущается люфт, замените поршень.
При замене поршня подберите к нему палец по классу.
Замените сломанные кольца и расширитель маслосъемного кольца.
Замените сломанные или треснувшие стопорные кольца, удерживающие поршневой палец.
Концы стопорных колец должны находиться в одной плоскости.
Погнутые кольца замените.
Замените погнутые шатуны.
Замените шатун, если во втулке 1 верхней головки есть задиры и глубокие царапины.
Замените шатун, если при разборке двигателя обнаружено, что шатунные вкладыши провернулись в шатуне.
Шатуны обрабатывают совместно с крышками, поэтому их нельзя разукомплектовывать.
Если утром, когда вы запустили холодный двигатель, был слышен металлический стук, который исчез при прогреве мотора, то это говорит только о том, что был нарушен зазор между поршнем и цилиндром. Почему он нарушается, и какие допустимые нормы применяются для зазоров между поршнем и цилиндром? Ответ вы найдете ниже.
Как меняется зазор между поршнем и цилиндром в процессе эксплуатации?
Уменьшение зазора происходит из-за естественного износа рабочих частей поршня и цилиндра. Такое изменение формы металла связано с его свойством поддаваться влиянию перепадов температур.
Помимо этого, уменьшение зазора может произойти и при неправильной сборке двигателя. Например, нарушена установка шатунов или появился перекос цилиндров. Не в стороне остается и перегрев двигателя, так как большие температуры имеют свойство расширять материалы. Особенно это касается алюминия, который, в отличие от чугуна, имеет высокий коэффициент расширения.
Как и любой другой дефект, нарушение зазора между поршнем и цилиндром оказывает негативное влияние на работу двигателя. Соприкосновение поршня и цилиндра под неправильным углом приводит к возникновению сухого трения, которое осуществляется без смазочного материала и повышает температуру деталей. Последствием такого трения почти во всех случаях становится появление различных царапин на рабочих поверхностях цилиндров.
После этого, любой двигатель обязательно подвергнут ремонту. Для проведения диагностики необходимо полностью снять головку блока цилиндров и как только поршневая группа будет на виду, то можно приступать к соответствующим замерам. В процессе замеров вам понадобятся микрометр, который покажет зазор поршней и нутромер для определения диаметра цилиндра.
Как снять головку блока цилиндров?
- В первую очередь, необходимо обездвижить автомобиль.
Под колеса устанавливаются противооткатные упоры, а рычаг КПП устанавливается в положение «первая передача». Откройте капот автомобиля и найдите место расположения ГБЦ.
- Вначале, снимаются все части, которые мешают свободному доступу к головке. Таковыми могут быть: воздушный фильтр, карбюратор (или инжектор), «штаны», а также различные тросы, приводы педалей и проводка электрических датчиков. С ГБЦ выкручиваются свечи, при необходимости, снимается трамблер.
- Слейте масло из двигателя и охлаждающую жидкость. Откройте крышку привода ГРМ и демонтируйте ремень. Это нужно для того, чтобы освободить распределительный вал. После этого, открутите гайки крепления крышки ГБЦ и снимите ее вместе с прокладкой. Перед сборкой рекомендуется установить новую прокладку.
- Теперь можно приступать, непосредственно, к демонтажу головки блока цилиндров. Открутите специальные болты крепления и демонтируйте головку вместе с прокладкой. После этого, вы получите открытый доступ к блоку цилиндров.
Какие существуют нормы зазоров между поршнями и цилиндрами
Перед проведением соответствующего ремонта поршневого механизма, необходимо знать, что существуют определенные нормы зазоров, которые расписаны по таблицам и должны соблюдаться в строгой форме.
Диаметр поршней разделяется всего на пять классов: A B C D E. Каждый новый класс определяет увеличение диаметра на 0,01 миллиметра. Кроме того, имеются специальные категории, которые определяют диаметр отверстия под поршневой палец. Они меняются на каждые 0,004 миллиметра. Все эти цифры и маркировка, в обязательном порядке маркируется на нижней части поршня.
Для различных деталей существуют соответствующие нормы. Так, например, новые поршни должны устанавливаться с зазором 0,06 миллиметров по всей его окружности. Если же деталь уже прошла достаточно внушительный километраж, то ее зазор не должен быть больше 0,15 миллиметров.
В случаях, когда зазор начинает превосходить установленные нормы, то следует подобрать и приобрести те поршни, которые обеспечат требуемую зазорность. Совсем необязательно подгонять поршень с высокой точностью. Достаточно лишь иметь образец с приблизительными размерами.
Предварительно, необходимо в обязательном порядке расточить цилиндры до ремонтных размеров и оставить запас, примерно, в 0,03 миллиметра. Он необходим для дальнейшего хонингования поверхности. Во время хонингования обязательно выдерживайте точность диаметра, чтобы при монтаже нового поршня зазор соответствовал требованиям, предъявляемым к установке новых деталей.
Диаметр цилиндра замеряется в четырех поясах, а также в двух перпендикулярных плоскостях. Нутромер необходимо устанавливать строго перпендикулярно блоку цилиндров. Таким образом, можно исключить любые отклонения от правильности измерений.
Видео – Как правильно замерять поршень
Помимо размеров поршней, немало важным показателем является и их масса. Масса поршней бывает нормальная, или с изменением на плюс (минус) 5 грамм. Кроме того, к поршням необходимо правильно подобрать маслосъемные кольца, которые должны быть ремонтных размеров.
После того, как поршни будут подобраны и установлены, необходимо еще раз проверить величину зазоров. Если она находится в пределах нормы, то можно приступать к обратной сборке двигателя. Устанавливается ГБЦ, затем привод газораспределительного механизма. После этого, прикручивается крышка ГБЦ с новой прокладкой и все навесные элементы. Не забудьте залить масло, ОЖ и отрегулировать механизм газораспределения. После этого, скорее всего, придется выставить угол опережения зажигания. Теперь автомобиль полностью готов к работе.
На этом проверка зазора между поршнем и цилиндром завершена. Какой бы простой вам не казалась эта сложная процедура, ее, все же, рекомендуется производить только в специализированных станциях технического обслуживания, так как сборка блока цилиндров – дело ответственное и лучше доверить его профессионалам. Удачи на дорогах!
Разъяснение мифов, тайн и заблуждений
Toggle Nav
Поиск
Зазор между поршнем и стенкой является важным параметром для любого двигателя, и для разных применений могут потребоваться совершенно разные характеристики. Мы объясняем науке, почему.
Среди блестящих предметов, которые появляются из новой коробки с высокопроизводительными поршнями, вам также предоставляется спецификация с подробным описанием критических размеров поршня и, помимо прочего, важнейшего отношения поршня к цилиндру. зазор стены. Это основная спецификация, на которую производители двигателей всегда ориентируются, чтобы обеспечить безотказную работу своих двигателей.
Чтобы узнать больше советов, приемов и приемов по сборке двигателей, НАЖМИТЕ ЗДЕСЬ!
Зазор между поршнем и стенкой устанавливается в нижней части юбки со стороны упора, как показано здесь. Между точкой зазора и пакетом колец ни одна часть поршня не соприкасается со стенкой цилиндра. Общеизвестно, что правильный зазор необходим для успешной работы, и что слишком большой или слишком маленький зазор может легко привести к фатальному повреждению двигателя. Небольшой зазор необходим для обеспечения места для смазочной среды, но большая часть зазора встроена для обеспечения скорости расширения компонентов по мере того, как двигатель достигает рабочей температуры.
Большинство конечных пользователей считают рекомендуемый зазор между поршнем и стенкой всеобъемлющим показателем оптимальной посадки поршня в отверстии цилиндра для безопасной работы.
В целом они верны, и внимательное отношение к рекомендуемой посадке почти всегда предотвратит такие ужасные бедствия, как чрезмерное трение, удары поршня, повреждение колец и сопутствующие неисправности.
Рекомендуемой точкой измерения на поршне является точка наибольшего диаметра на поршне, поэтому она должна быть установлена с надлежащим зазором производителя. Думайте об этом как о точке безопасности, которую производители предоставляют для предотвращения неправильной установки и последующего повреждения двигателя. Но это еще не все. Когда двигатель работает при рабочей температуре, каждая точка на юбке поршня и в области контакта с кольцом имеет определенный зазор, предназначенный для обеспечения надлежащего функционирования поршня и связанного с ним пакета колец.
При определении оптимального зазора между поршнем и стенкой конструкторы учитывают все физические и тепловые условия эксплуатации поршня, оценивая следующие факторы и их взаимосвязь для каждой конструкции поршня.
- Приложение
- Тип блока (материал)
- Материал поршня (сплав)
- Тип (литой, кованый, заэвтектический)
- Размер поршня
- Смазка
- Охлаждение
ПРИМЕНЕНИЕ:
Различные приложения предъявляют различные требования. Частота вращения двигателя, давление в цилиндре, нагрузка на юбку, угол наклона штока и другие факторы играют роль в оценке проектировщиком требований к конечному зазору поршня. Во многих низкоскоростных серийных двигателях до сих пор используются недорогие литые поршни с очень контролируемыми характеристиками расширения. Они могут быть установлены очень плотно в канале ствола и служить долгое время при нормальной эксплуатации. Они не гремят при запуске, что является серьезной проблемой для автопроизводителей, и год за годом обеспечивают плавную и безотказную работу.
Непрерывная работа в режиме WOT резко увеличивает тепловую нагрузку на поршень, вызывая его большее расширение. Двигатели, подвергающиеся длительному WOT, почти всегда требуют дополнительного зазора, чтобы обеспечить повышенное расширение и обеспечить достаточное пространство для разбрызгивания пленки смазочного масла на стенках цилиндра. Гоночные двигатели и судовые двигатели, которые выдерживают длительную работу WOT, являются яркими примерами необходимости увеличения зазора.
Другие соображения включают двигатели с высоким форсированием и двигатели с впрыском закиси азота. Рекомендуемые зазоры зависят от области применения, и разработчики поршней учитывают это, помогая вам с набором нестандартных поршней. Подобные высоконагруженные двигатели, как правило, испытывают более высокие тепловые нагрузки и гораздо более высокое давление в цилиндрах, что может увеличить отклонение поршня и потребовать большего зазора. В то время как поршень и шток являются механизмом, с помощью которого усилие передается на коленчатый вал, поршню также поручено поддерживать стабильную платформу для поддержки колец. Нестабильный поршень снижает уплотнительное кольцо и, следовательно, мощность.
Тип блока и материал
Тип блока имеет огромное значение в требованиях к зазору между поршнем и стенкой. Алюминиевый блок, такой как этот блок Chevrolet LS3, будет расширяться больше, чем чугунный блок, что значительно изменит требования к зазору.Чугун и алюминий являются преобладающими материалами, из которых изготавливаются корпуса цилиндров. Эти материалы оказывают значительное влияние на зазор между поршнем и стенкой, в первую очередь из-за их характеристик теплового расширения. Чугунные блоки расширяются меньше, чем алюминиевые блоки с чугунными гильзами цилиндров, и поэтому более термически стабильны.
В некоторых блоках используются алюминиевые цилиндры с никасиловым покрытием без вкладышей — они расширяются еще больше. В любом случае необходимо учитывать изменения размеров из-за нагрева, чтобы получить надлежащий зазор поршня. И это включает в себя учет тепловых характеристик материала поршня. Деформация отверстия из-за усилия зажима крепления головки блока цилиндров также влияет на окончательные значения зазора поршня. В зависимости от двигателя и конструкции блока возможно искривление канала ствола и другими креплениями. Это могут быть опоры двигателя, насосы, кронштейны и так далее.
МАТЕРИАЛ ПОРШНЯ
Основной материал поршня, вероятно, является самым большим фактором, определяющим требования к прилеганию поршня к стенке. Для поршней из материала 2618 потребуются немного большие зазоры, чем для поршней из материала 4032, который содержит термостабилизирующий силикон.Литые поршни со встроенной компенсационной стойкой были обычным явлением в течение многих лет, и они до сих пор обеспечивают очень надежную работу в условиях малой мощности и низких оборотов. Около века назад было обнаружено, что добавление 12 процентов кремния в качестве легирующего компонента значительно стабилизирует расширение алюминиевых компонентов, таких как поршни.
Известный как эвтектический алюминиево-кремниевый сплав, он позволил разработать литые поршни с высоким содержанием кремния, содержащие до 20 процентов кремниевого сплава. Они известны как заэвтектические поршни, и их главным преимуществом является очень низкая скорость расширения. Они могут быть установлены с зазором между поршнем и стенкой всего 0,0005 дюйма по основному диаметру.
Интересно, что когда современный кованый поршень с большим начальным холодным зазором достигает рабочей температуры, разница в рабочем зазоре меньше, чем можно было бы предположить. Например, Wiseco использует сплавы 2618 и 4032 для всех своих поковок. Несмотря на то, что степень расширения различна для каждого сплава, компания Wiseco изготовила поршни из каждого сплава для одного и того же двигателя, которые успешно работают практически с одинаковым рабочим зазором. Поршень 2618 с более высоким расширением может иметь больший начальный зазор, чем поршень 4032, но как только двигатель достигает рабочей температуры, оба поршня будут иметь одинаковые рабочие зазоры.
Профиль поршня
Бочкообразная форма поршня помещает точку критического контакта на нижнюю часть юбки, чтобы обеспечить точку стабилизации вблизи нижней части поршня.
Профиль поршня играет важную роль в определении зазора. Более узкие зазоры, как правило, уменьшают стук поршня при холодном пуске и обеспечивают более стабильную посадку, что способствует хорошему уплотнению колец.
Поршни с юбками полного радиуса (в отличие от профилей бочкообразной формы), как утверждается, способны к более плотной посадке. Реальность такова, что поршень с полной юбкой, поскольку он имеет профиль полного радиуса, измеряется в самом низу и имеет гораздо больший зазор везде, кроме точки измерения. Это пример того, как общий зазор поршня значительно отличается от опубликованной спецификации зазора.
Размер поршня
Чем больше поршень, тем больше он расширится. Хот-роды и американские двигатели V8, как правило, используют большие поршни, которые требуют большего начального зазора между поршнем и стенкой, чем, скажем, двигатель Honda с меньшим размером отверстия.
Для поршней большего размера обычно требуется больший зазор, чем для поршней меньшего размера. Сравнение крайностей иллюстрирует этот момент, если мы рассмотрим разницу в двух несвязанных поршнях, используемых для полета. Поршень размером с наперсток от Cox .049Двигатель модели самолета работает просто отлично с таким минимальным зазором, что ему даже не требуется поршневое кольцо какой-либо формы для герметизации продуктов сгорания.
И наоборот, поршень диаметром 5400 дюймов от двигателя Merlin V-12, который приводил в действие истребитель P-51 времен Второй мировой войны, требует зазора от 0,012 до 0,014 дюйма для удовлетворительной работы. Здесь мы также отмечаем, что тепловая нагрузка от трения далека. больше в двигателе Мерлина, чем в двигателе Кокса.В экстремальных условиях авиагонок в двигателе Мерлина возникает большая тепловая нагрузка с соответствующим расширением поршней.
Установка зазора между поршнем и стенкой часто зависит от процесса хонингования.
Смазка
Масло на стенке цилиндра адаптируется к местным условиям при рабочей температуре, но зазор поршня должен оставлять некоторое пространство для того, чтобы смазочная пленка выполняла свою работу. Масляная пленка создается брызгами, исходящими от быстро вращающегося коленчатого вала. Проще говоря, масло, вытекающее из боковых зазоров штока и коренных подшипников, отбрасывается на стенки цилиндра и контролируется тонким слоем маслосъемного кольца. Масляная пленка может быть менее 0,001 дюйма и учитывается в окончательном зазоре поршня. Масляная пленка должна присутствовать не только для смазки поверхностей, но и для передачи тепла от поршня к блоку цилиндров, а затем к системе охлаждения.
Способ охлаждения двигателя влияет на зазор между поршнем и стенкой.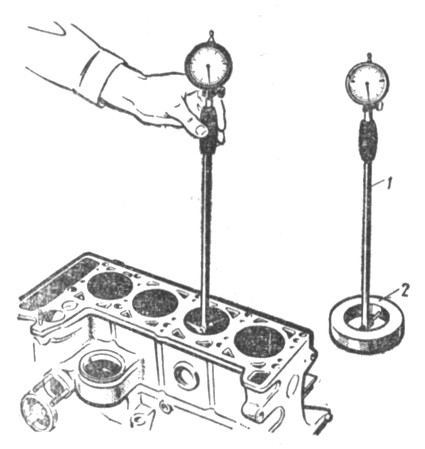
Тип системы охлаждения
Существует значительная разница в требованиях к зазорам для двигателей с воздушным охлаждением и жидкостным охлаждением. Системы с воздушным охлаждением, такие как в автомобилях Volkswagen или Porsche, по сути являются нерегулируемыми системами, зависящими от условий воздушного потока. Они более склонны к деформации отверстия и неравномерному расширению. Воздушное охлаждение более привередливо из-за больших колебаний воздушного потока. Например, в авиационном двигателе охлаждение также уменьшается с высотой, поскольку воздух становится тоньше и уносит меньше тепла.
Жидкостное охлаждение обеспечивает большую стабильность благодаря легко регулируемой системе и более быстрому прогреву в качестве бонуса. Охлаждающая среда подается внутрь и наружу в соответствии с тепловыми условиями и регулированием, обеспечиваемым термостатом. Эти факторы влияют на результирующий зазор между поршнем и цилиндром.
Инженеры идут на многое, чтобы определить правильный зазор между поршнем и стенкой. Это включает в себя испытания в реальных условиях на работающих двигателях с различными конфигурациями юбки и различными зазорами, чтобы определить пригодность каждого поршня для конкретного применения. Когда конструкция завершена, зазор и место проверки указываются в инструкциях, прилагаемых к поршням. Если эти рекомендации строго соблюдаются, вы можете рассчитывать на бесперебойную работу ваших новых поршней и оптимальное уплотнение цилиндра для достижения максимальной мощности.
АВТОРСКИЕ ПРАВА © 2022 WISECO PERFORMANCE PRODUCTS. ВСЕ ПРАВА ЗАЩИЩЕНЫ. WISECO PERFORMANCE PRODUCTS ЯВЛЯЕТСЯ ЧАСТЬЮ СЕМЕЙСТВА БРЕНДОВ-ПОБЕДИТЕЛЕЙ ГОНОК.
Зазор между поршнем и цилиндром: обучающее видео с Mahle
Сборка двигателя требует измерения нескольких компонентов для обеспечения адекватных зазоров. Зазор между поршнем и цилиндром является одной из таких критических областей. Хотя зазор обычно устанавливается оператором во время хонингования цилиндров, крайне важно, чтобы сборщик знал, как проводить измерения, чтобы перепроверить работу оператора. Mahle Motorsports подготовила это информативное видео о процессе.
Для измерения зазора между поршнем и отверстием требуются специальные инструменты. Список включает следующее: микрометр, штангенциркуль и нутромер. Микрометры имеют диапазон в один дюйм и будут использоваться для измерения поршня. Выберите микрометр с диапазоном, включающим диаметр поршня. Штангенциркуль используется для определения точки измерения на поршне. Будет достаточно штангенциркуля от нуля до шести дюймов.
Наконец, нутромер будет использоваться для измерения диаметра цилиндра. Как и микрометр, нутромеры охватывают определенный диапазон. Тем не менее, нутромер поставляется с рядом удлинителей и прокладок, чтобы покрыть больший диапазон, например от двух до шести дюймов.
После того, как все инструменты были приобретены, необходимо найти спецификацию зазора и точку измерения поршня. Оба они предоставляются производителем поршня. Mahle предоставляет онлайн-версию своего руководства по применению через свой веб-сайт.
Руководство по применению Mahle очень простое. Найдите свое приложение, затем найдите номер детали поршня справа. Слева от номера детали указаны минимальный и максимальный зазоры и точка измерения поршня.
Определение правильной точки измерения имеет решающее значение, поскольку каждый поршень имеет уникальный профиль. Измерения, проведенные выше или ниже указанной точки, будут неверными. Неверное измерение поршня приведет к неправильному расчету зазора между поршнем и отверстием.
Штангенциркуль устанавливается на нужное расстояние для определения точки измерения (см. выше), а затем маркером отмечается точка на поршне (см. ниже).
Не забудьте поставить по одной отметке на каждой юбке для справки. Крайне важно, чтобы микрометр располагался на каждой юбке на правильной высоте.
Наковальня и шпиндель микрометра должны быть перпендикулярны юбке. Если одна сторона немного отклонится, вы получите неправильные измерения. Запишите размер поршня.
Существует несколько способов установки нутромера. В этом примере Mahle настроил нутромер для измерения фактического диаметра отверстия. Нутромер показывает ноль на отметке 4,040 дюйма. Альтернативный метод заключается в измерении зазора без выполнения каких-либо расчетов путем установки нутромера на ноль при измерении поршня. Показанием нутромера будет зазор между поршнем и отверстием.
Покачайте датчик вперед и назад и возьмите наименьшее показание. Наименьшее показание получается, когда манометр расположен перпендикулярно стенке цилиндра. Добавьте показание к 4,040, чтобы определить размер отверстия. Этот калибр показывает 0,0002 дюйма (две десятитысячных дюйма), что обычно называют «двумя десятыми». Это в 15 раз тоньше среднего человеческого волоса!
Если цилиндр был отточен с помощью динамометрической пластины, скорее всего, отверстие имеет некруглую форму без затяжки головки цилиндра на месте. Поэтому рекомендуется проверять размер отверстия при установленной пластине крутящего момента. Если его нет, произведите измерение в нижней части цилиндра в месте выхода гильзы из сердечника блока. Деформация цилиндра в этой области ограничена.
Размер отверстия цилиндра минус диаметр поршня равняется зазору между поршнем и отверстием.
Переменные, влияющие на зазор между поршнем и цилиндром Точность измерений, таких как размер отверстия и диаметр поршня, имеет решающее значение для долговечности двигателя. Учитывайте любые внешние факторы, которые могут исказить измерения. Мале указал на два общих.
Во-первых, температура заставляет цилиндры и поршни расширяться и сжиматься. Крайне важно, чтобы и блок цилиндров, и поршни были комнатной температуры. Небольшие различия в температуре могут значительно изменить измерения, учитывая, что микрометр и нутромер измеряют с шагом в одну десятитысячную долю дюйма.
Измерительные инструменты также должны иметь комнатную температуру. Сведите к минимуму контакт рук с инструментами. Проведите измерение, затем отложите инструмент, чтобы записать показания. Тепло тела от удержания датчика в руке сдвинет стрелку на две десятых. Вручную прогрейте манометр перед обнулением и альтернативным измерением.
Как упоминалось ранее, хонингование цилиндра приводит поршень в соответствие с зазором отверстия. Предоставьте машинисту поршни, чтобы можно было получить правильный зазор. Шаги, изложенные Мале, позволят сборщику перепроверить работу слесаря.
Влияние зазора канала поршня на характеристики вторичного движения поршня и износа юбки
Механика и промышленность 20 , 205 (2019)
Штатная статья
Влияние зазора канала поршня на характеристики вторичного движения поршня и юбки носить
Сюй Сяохуа *
Shanghai Volkswagen Powertrain Co. Ltd., Шанхай 201807, КНР
* электронная почта: [email protected]
Получено:
3
Май
2018
Принято:
12
Сентябрь
2018
Abstract
Проведено динамическое моделирование износа юбки поршня после испытания бензинового двигателя. Кроме того, изучаются вторичное движение и износ для предложения по усовершенствованию различных зазоров цилиндров. Результаты показывают, что при исходном зазоре цилиндра 0,0325–0,0575 мм минимальный рабочий зазор юбки поршня меньше; это не способствует образованию смазочной масляной пленки, которая вызывает износ на напорной и антинапорной сторонах юбки поршня. При увеличении зазора цилиндра до 0,0400–0,0650 мм износная нагрузка на упорную и противоосевую сторону юбки поршня уменьшилась на 68,3% и 68,1% соответственно, эффект улучшенного износа лучше, и результат хорошо совпадает. с результатом проверки двигателя.
Ключевые слова: зазор между поршнями / динамика поршня / вторичное движение / нагрузка от износа
© AFM, EDP Sciences 2019
1 Введение
Поршень двигателя внутреннего сгорания движется вверх и вниз внутри цилиндра двигателя под действием давления газа, силы инерции, бокового давления и т.д. Кроме того, поршень также колеблется и движется вбок, что называется вторым движением. По сравнению с возвратно-поступательным линейным движением секундное движение очень мало, но оказывает существенное влияние на износ поршня [1–7]. Существуют различные факторы, влияющие на механизм износа поршня, такие как зазор поршня, эксцентриситет отверстия под цапфу, эксцентриситет коленчатого вала, центр масс поршня, деформация поршня и конструкция линии формы и т. д. [8-13]. Точнее, эксцентриситет коленчатого вала влияет на относительный качание юбки и головки в момент переключения при возвратно-поступательном движении поршня; деформация поршня обычно влияет на контакт между поршнем и соответствующими частями после запуска двигателя; зазор между поршнем и каналом влияет не только на амплитуду второго движения, но и играет ключевую роль в трении и износе между поршнем и цилиндром [14–19].].
Данная статья посвящена изучению механизма износа поршня. Было проведено испытание поршня бензинового двигателя, а затем было проанализировано состояние износа юбки после испытания. С помощью программного обеспечения для динамического анализа и моделирования поршней «Pisdyn» компании Ricardo были проведены динамические расчеты с различными зазорами поршня. При динамическом моделировании расчета различных условий зазора цилиндра была окончательно получена оптимизированная схема, а также закон влияния зазора поршня на характеристики вторичного движения и на износ бензинового двигателя.
2 Основное уравнение вторичного движения поршня
Сила поршня при движении в цилиндре показана на рисунке 1. На этом рисунке ось цилиндра определена как ось X с положительным направлением к верхней части цилиндра. Ось Y определяется как направление, перпендикулярное обеим осям оси штифта, и направление, указывающее на сторону вторичного упора, является положительным. При условии, что давление газа в цилиндре равно F газ и его линия действия проходит через центральную линию цилиндра, давление газа создаст крутящий момент М газ , вращающий поршень вокруг поршневого пальца в случае смещения отверстия поршневого пальца.
Поршень считается подвижным только в плане стороны главного напора и стороны подтяги. Согласно принципу баланса динамических сил при движении поршня в цилиндре уравнение динамики поршня можно получить следующим образом:
В направлении X(1)
В направлении Y:(2)
Вращение вокруг оси поршневого пальца:(3)
В приведенных выше формулах m c — масса поршня, Θ c — момент инерции поршня относительно оси поршневого пальца, F gc — массовая сила поршня, F газ — давление газа в цилиндре, F r — контактное усилие между поршневым кольцом и поршнем, — контактное усилие в поперечном сечении i основной стороны тяги и стороны подтягивания, F штифт — усилие, приложенное к поршневому пальцу, F звено — сила, приложенная к маленькому концу шатуна, M c — крутящий момент поршня вокруг оси поршневого пальца, вызванный боковой силой, M gc — крутящий момент поршня вокруг поршня M r — момент поршня, вызванный осевой и радиальной силой поршневого кольца и M pc — момент трения поршня о поршневой палец.
Когда поршень совершает прямолинейное возвратно-поступательное движение в отверстии цилиндра, скольжение вдоль стенки может привести к эффекту сдвига. Причем эффект выдавливания предполагается создавать как в ВМТ, так и в НМТ при поперечном движении поршня. И все это похоже на характеристику жидкостной смазки, аналогичную подшипнику скольжения. После учета влияния шероховатости и волнистости между юбкой поршня и смазывающей поверхностью стенки цилиндра было применено двумерное среднее уравнение Рейнольдса для жидкостной смазки на шероховатой контактной поверхности между отверстием цилиндра и поршнем, модифицированное по Патиру и Ченгу. и описан в формуле ниже: (4) где p h среднее давление жидкости, t время, h номинальная толщина пленки, среднее фактическое значение толщины пленки, µ вязкость смазочного масла, U скорость поршня, Ф с — коэффициент поперечного течения, Φ x , Φ и — коэффициенты текучести под давлением, а σ — среднеквадратичное значение шероховатости поверхности между отверстием цилиндра и поршнем.
рисунок 1 Сила поршня при движении в цилиндре. |
3 Основные граничные условия для расчета динамики поршня
3.1 Основные параметры двигателя
В данной статье в качестве объекта исследования в основном взят поршень четырехцилиндрового бензинового двигателя, основные параметры которого приведены в таблице 1.
Таблица 1
Основные параметры двигатель.
3.2 Термическая деформация юбки поршня
Поршень контактирует непосредственно с высокотемпературным газом в рабочих условиях. В результате внутри поршня может возникать температурный градиент, что приводит к термической деформации, которую можно рассчитать в моделировании методом конечных элементов. Чтобы обеспечить точность расчета моделирования, температура поршня должна быть проверена пробкой твердости перед моделированием. Полученные тестовые значения затем использовались для калибровки и проверки моделирования температурного поля. Расположение контрольных точек температурного испытания поршня показано на рисунке 2. На этом рисунке 1 — центральное положение камеры сгорания поршня, 2–5 — расположение вокруг камеры сгорания, 6–9— положение пожарного берега, а 10–11 — медиальная сторона точечного отверстия.
Результаты испытаний пробки поршня каждого цилиндра на твердость, а также результаты испытаний средней температуры каждой контрольной точки показаны на рисунке 3.
Из результатов испытаний видно, что самая высокая температура поршня составляет 241 °C, которая появляется в центральном положении камеры сгорания. Температура окружающего пространства и берега пожара составляет примерно 211 °C, а температура медиальной стороны прокола – 185 °C.
Температурное поле поршня и тепловая деформация юбки рассчитываются путем итеративного расчета численного моделирования с помощью программного обеспечения ANSYS, которые показаны на рисунках 4 и 5. Очевидно, что термическая деформация верхнего конца юбки составляет 0,132 мм, а нижнего конца юбки — 0,092 мм. Кроме того, увеличивается градиент термической деформации при замыкании на верхний конец юбки. Точно так же градиент термической деформации уменьшается при закрытии нижнего конца юбки.
Рис. 2 Расположение точек измерения температуры поршня. |
Рис. 3 Распределение температуры поверхности поршня. |
Рис. 4 Результаты моделирования температурного поля поршня. |
Рис. 5 Термическая деформация юбки поршня. |
3.3 Характеристики жесткости поршня
Жесткость поршня используется для обозначения сопротивления упругой деформации, когда определенная часть поршня находится под действием внешней нагрузки. И жесткость юбки поршня является ключевым фактором, который следует учитывать при кинетическом анализе. Жесткость поршня может быть количественно определена величиной упругой деформации. На рис. 6 показана упругая деформация, полученная методом конечных элементов в направлении 0 °C поршня. Как видно из рисунка, жесткость юбки уменьшается сверху вниз, а лучшую гибкость можно найти в месте под отверстием под палец, что является преимуществом для уменьшения ударов поршня при переключении.
Рис. 6 Упругая деформация поршня. |
4 Результаты динамических расчетов и проверка испытаний
4.1 Схема расчета
Начальный зазор между поршнем и каналом в этом исследовании был случаем 1; зазор в цилиндре 0,0325–0,0575 мм. По мере появления износа юбки после нагрузочного испытания зазор между поршнем и каналом был оптимизирован, как показано в таблице 2.
По полученным граничным условиям построена гидродинамическая модель смазки поршня, сочетающая геометрические и числовые параметры модели поршня, гильза цилиндра, звено, поршневой палец и так далее. Относительные расчеты также проводились для трех случаев при полной скорости и полной нагрузке.
Таблица 2
Схема зазора гильзы цилиндра поршня.
4.2 Результаты
4.2.1 Угол движения поршня и радиальное смещение
На рис. 7 показан угол поворота поршня вокруг поршневого пальца, полученный расчетным путем, а на рис. 8 — кривые радиального смещения поршня, в которых 0° является верхней мертвой точкой. Видно, что при угле поворота коленчатого вала 12° максимальный угол поворота поршня в случае 1 составил 0,112°; угол поворота поршня в случае 2 увеличился на 58,9% по сравнению со случаем 1 и достиг максимума, который составил 0,178°; угол поворота в случае 3 составил 0,133°. Согласно графику 8 при угле поворота коленчатого вала 128° максимальное радиальное смещение поршня в случае 1 составило 0,039 мм; радиальное смещение поршня в случае 2 увеличилось на 33,3% по сравнению с вариантом 1 и достигло максимального значения, равного 0,052 мм; максимальное радиальное смещение в случае 3 составило 0,043 мм. Таким образом, угол поворота второго движения, а также радиальное смещение поршня увеличиваются с увеличением зазора между поршнем и отверстием, и это увеличение является чрезвычайно очевидным.
Рис. 7 Угол поворота поршня. |
Рис. 8 Радиальное смещение поршня. |
4.2.2 Кинетическая энергия детонации поршня
Кинетическая энергия детонации поршня является важным параметром, используемым для косвенной оценки NVH двигателя. Действительно, ожидается, что пиковые значения, а также общая кинетическая энергия в цикле кинетической энергии удара поршня о гильзу цилиндра будут слабыми. Полная кинетическая энергия складывается из кинетической энергии осевого движения поршня E a , кинетическая энергия радиального движения E l и кинетическая энергия колебаний E r и выражается в следующих уравнениях: (5)
(6)
(7)
(8) где M — вес поршня в сборе, v — осевая скорость, u — радиальная скорость и w — угол поворота поршня.
На рис. 9 показаны кривые кинетической энергии удара поршня. Пиковое значение ударной кинетической энергии поршня в случае 1 составляет 8,0 Н мм; пиковое значение ударной кинетической энергии поршня в случае 2 составляет 22,3 Н мм, увеличившись в 1,8 раза по сравнению с вариантом 1; пиковое значение кинетической энергии детонации также возрастает и достигает 11,4 Н мм. По-видимому, увеличение зазора поршня приводит к явному увеличению стука поршня, который является сильным для шума бензинового двигателя.
Рис. 9 Кинетическая энергия стука поршня. |
4.2.3 Контакт и износ юбки поршня
Состояние износа поверхности юбки поршня является еще одним важным показателем для оценки рациональности конструкции поршня. Нагрузку от износа можно использовать для выражения износа поверхности поршня. Предполагается, что на величину износной нагрузки влияет не только контактное давление, но и скорость движения поршня в гильзе цилиндра, которая может быть выражена произведением контактного давления на скорость движения поршня 9. 0199 V выражается следующим образом.(9)
В этой формуле W — нагрузка на износ в Н м/с или Вт/м 2 , P c — контактное давление, а V — скорость вращения поршня, включая первую порядок движения и скорость второго движения.
Окончательный износ юбки поршня фактически формируется циклическим процессом накопления. В то время как двигатель был испытан в условиях полной скорости и полной нагрузки, вертикальная царапина на внутренней стороне отверстия цилиндра была обнаружена с помощью эндоскопии во время плановой проверки двигателя на остановке. Оценка показана на рисунке 10.
После разборки двигателя был обнаружен очевидный износ на главной и вторичной сторонах упора четырех поршней в корпусе 1, как показано на рисунке 11. сверху вниз по главной и вторичной упорным сторонам юбки поршня. По контуру линии и глубине ножа было установлено, что глубина ножа на верхнем конце юбки изменялась от 0,010–0,011 мм до испытания до 0,002–0,003 мм; аналогично глубина ножа на нижнем конце юбки изменилась с 0,012–0,013 мм до испытания до 0,008–0,010 мм; покрытия и глубина ножа в других зонах износа были равны 0, а глубина износа находилась в пределах от 0,015 до 0,024 мм.
При движении поршня в гильзе цилиндра зазор между ними все время меняется. На рис. 12 показаны минимальные зазоры юбки в трех случаях, полученные при динамическом моделировании поршня. Из диаграммы видно, что минимальный рабочий зазор поршня в случае 1 составляет около 4,6 µ м, в этом случае масляная пленка не может быть хорошо сформирована. Напротив, зазор в холодном состоянии был увеличен в случаях 2 и 3, чтобы увеличить минимальный зазор юбки, что способствует образованию масляной пленки юбки поршня.
Результат расчета совокупной нагрузки износа юбки поршня в случае 1 показан на рисунке 13. Согласно графику нагрузки износа основной и вспомогательной упорных сторон поршня составляют 88,589 МВт/м 2 и 80,268 МВт /м 2 соответственно. Прогнозируется, что явный износ более вероятен в средней части юбки с обеих упорных сторон, что подтверждается состоянием износа поршня, полученным в случае 1 в процессе стендовых испытаний двигателя и представленным на рисунке 11. 9.0003
На рисунках 14 и 15 показаны результаты расчета суммарной нагрузки на износ юбки поршня для случаев 2 и 3 соответственно. Действительно, результаты основной и вспомогательной сторон тяги в варианте 2 уменьшились на 63,9% и 57,7% соответственно по сравнению с вариантом 1; аналогично, результаты в случае 3 уменьшились на 68,3% и 68,1% соответственно. Точные значения нагрузки на износ показаны в Таблице 3.
Таким образом, нагрузка на юбку на износ будет значительно снижена после увеличения зазора в холодном состоянии. Действительно, зазор поршня в гильзе цилиндра является более целесообразным для предотвращения разрушения масляной пленки избыточным давлением. В результате обеспечивается жидкостная динамическая смазка юбки поршня.
После увеличения зазора между поршнем и отверстием в обоих случаях 2 и 3 износ юбки был уменьшен, чтобы уменьшить риск износа юбки. Согласно серии анализов, хотя увеличение зазора поршня в случае 2 более важно, чем в случае 3, снижение контактного давления, а также износа не является очевидным. Однако амплитуда второго движения и кинетическая энергия удара сильно возросли. Таким образом, вариант 2 считается наилучшей схемой улучшения, и эта оценка была дополнительно подтверждена во время второго стендового испытания двигателя. На рис. 16 показаны результаты установки собранного поршня в случае 3 после работы на полной скорости и под нагрузкой. Судя по всему, юбка поршня после испытаний хорошо прилегает и износа не обнаружено.
Рис. 10 График эндоскопии отверстия цилиндра. |
Рис. 11 Диаграмма износа основной и вспомогательной упорной стороны поршня. |
Рис. 12 Минимальный рабочий зазор поршня гильзы цилиндра. |
Рис. 13 Износная нагрузка на основную и вспомогательную сторону поршня. |
Рис.![]() Износная нагрузка на основную и вспомогательную сторону поршня. |
Рис. 15 Износная нагрузка на основную и вспомогательную сторону поршня. |
Таблица 3
Результат износа.
Рис. 16 Фото поршней после испытаний. |
5 Заключение
Зазор между поршнем и отверстием является одним из наиболее важных факторов, влияющих на характеристики износа. По результатам исследований сделаны следующие выводы:
Увеличение зазора между поршнем и гильзой цилиндра приводит к увеличению угла поворота, радиального смещения и ударной кинетической энергии вторичного движения поршня. Таким образом, разумный зазор может обеспечить плавность хода поршня и уменьшить удары поршня о гильзу цилиндра.
Согласно расчету динамики поршня, начальный зазор в случае 1 мал, что приводит к небольшому зазору масляной пленки и большей нагрузке на износ.
После увеличения зазора поршня в корпусе 3 нагрузка на основную и вторичную упорные стороны в корпусе 3 уменьшилась на 68,3% и 68,1% соответственно по сравнению с вариантом 1, что значительно улучшило износ юбки поршня. . Этот результат подтверждается стендовыми испытаниями двигателя.
Оптимальный выбор зазора между поршнем и гильзой цилиндра должен определяться с учетом плавности второго движения, износа, задиров, детонации и т.д. В то же время должна быть гарантирована хорошая гидродинамическая смазка юбки поршня, а также другие эксплуатационные требования.
Каталожные номера
- Дж.Л. Лей, Л.З. Шен, Д.Д. Чен, Ю.Х. Би, Дж. М. Чен, Влияние конструкции поршневого комплекта на вторичное движение поршня с учетом термической деформации, Китай. Внутреннее возгорание. Двигатель инж. 33 (2012) 86–92. [Google ученый]
- П.
Ван, З.Х. Дэн, Х. Луо, С.Г. Ян, Исследование стука поршня и индуцированного шума в двигателях внутреннего сгорания, Пер. CSICE 28 (2010) 475–479 [Google ученый]
- Р. Б. Эдара, Обзор литературы о вторичном движении поршня поршневого двигателя, Серия технических документов SAE 2008 -01-1045, 2008. [Google ученый]
- Р.М. Хоффман, А. Суджанто, К.П. Ду, Дж. Стаут, Прочная конструкция поршня и оптимизация с использованием анализа вторичного движения поршня, Серия технических документов SAE 2003-01-0148, 2003.
[Google ученый]
- Ю.К. Тан, З.М. Рипин, Анализ вторичного движения поршня, J. Sound Vib. 332 (2013) 5162–5176 [Перекрестная ссылка] [Google ученый]
- К. Кирнер, Дж. Хальбхубер, Б. Улиг, А. Олива, С. Граф, Г. Вахтмайстер, Экспериментальные и моделирующие исследования в области поршневого узла двигателя внутреннего сгорания, Tribol. Междунар. 99 (2016) 159–168 [Перекрестная ссылка] [Google ученый]
- Б.
Чжао, X.D. Дай, З.Н. Чжан, Ю.Б. Се, Новый численный метод для анализа динамики поршня и смазки, Tribol. Междунар. 94 (2016) 395–408 [Перекрестная ссылка] [Google ученый]
- О. Гюнелсу, О. Акалин, Влияние профилей юбки поршня на вторичное движение и трение, J. Eng. Мощность газовых турбин 136 (2014) 062503. [Перекрестная ссылка] [Google ученый]
- Z.
He, W. Xie, G. Zhang, Z. Hong, J. Zhang, Анализ динамических характеристик поршня на основе метода FEM, часть I: влияние параметров юбки поршня, Adv. англ. ПО 75 (2014) 68–85 [Перекрестная ссылка] [Google ученый]
- П.Ю. Сюн, Дж. Чжан, С.Ю. Лю, Ф. Х. Лин, Исследование влияния смещения отверстия поршневого пальца на трение и износ поршня, Китай. Внутреннее возгорание. Двигатель инж. 38 (2017) 117–122 [Google ученый]
- С.
Нараян, Влияние различных параметров на вторичное движение поршня, SAE Technical Papers, Vol. 2015, март, 2015. [Google ученый]
- Р. Мазузи, А. Келлачи, А. Карас, Влияние параметров конструкции поршня на динамическое поведение гильзы юбки, Ind. Lubr. Трибол. 68 (2016) 250–258 [Перекрестная ссылка] [Google ученый]
- Ю.Дж.Лу, Л.Ша, П.Ванг, К.Лю, Ю.Ф. Чжан, Н.
Мюллер, Анализ вторичного движения и характеристик смазки поршня с учетом профиля юбки поршня, Shock Vib. 2018 (2018) 3240469. [Google ученый]
- Дж. Л. Чжу, З.Ю. Хао, К. Чжэн, Анализ и оптимизация вторичного движения поршня бензинового двигателя, J. Zhejiang Univ. 2014. № 48. С. 334–341. [Google ученый]
- П.Ю. Сюн, X. Сун, X.B. Син, Л. Ван, Ф.Г. Ли, Исследование жесткости юбки поршня бензинового двигателя на основе динамического моделирования, I.C.E. Силовая установка 33 (2016) 47–51 [Google ученый]
- Х.
Кагеяма, С. Мачида, Исследование контактных давлений и деформаций юбки поршня в бензиновом двигателе, Технический документ SAE 2000-01-1784, 2000. [Google ученый]
- Ю.К. Тан, З.М. Рипин, Методика определения мгновенного трения юбки поршня при ударе поршня, Трибол. Междунар. 74 (2014) 145–153 [Перекрестная ссылка] [Google ученый]
- П. Оберт, Т. Мюллер, Х. Й.
Фюссер, Д. Бартель, Влияние подачи масла и температуры гильзы цилиндра на трение, износ и задиры контактов гильзы цилиндра поршневого кольца — тест новой модели, Tribol. Междунар. 94 (2016) 306–314 [Перекрестная ссылка] [Google ученый]
- Ю.К. Jiang, J.P. Zhang, G. Hong, LP Wang, X. Liu, 3D EHD смазка и износ гильзы поршневого кольца цилиндра на дизельных двигателях, Int. Дж. Автомот. Технол. 16 (2015) 1–15 [Перекрестная ссылка] [Google ученый]
Цитируйте эту статью как : X. Xiaohua, Влияние зазора поршня на характеристики второго движения поршня и износа юбки, Механика и промышленность 20 , 205 (2019)
Все Таблицы
Таблица 1
Основные параметры двигателя.
В тексте
Таблица 2
Схема зазора гильзы цилиндра поршня.
В тексте
Таблица 3
Результат износа.
В тексте
Все фигурки
рисунок 1 Сила поршня при движении в цилиндре. | |
В тексте |
Рис. 2 Расположение точек измерения температуры поршня. | |
В тексте |
Рис. 3 Распределение температуры поверхности поршня. | |
В тексте |
Рис.![]() Результаты моделирования температурного поля поршня. | |
В тексте |
Рис. 5 Термическая деформация юбки поршня. | |
В тексте |
Рис. 6 Упругая деформация поршня. | |
В тексте |
Рис. 7 Угол поворота поршня. | |
В тексте |
Рис. 8 Радиальное смещение поршня. | |
В тексте |
Рис. 9 Кинетическая энергия стука поршня. | |
В тексте |
Рис. 10 График эндоскопии отверстия цилиндра. | |
В тексте |
Рис. 11 Диаграмма износа основной и вспомогательной упорной стороны поршня. | |
В тексте |
Рис. 12 Минимальный рабочий зазор поршня гильзы цилиндра. | |
В тексте |
Рис. 13 Износная нагрузка на основную и вспомогательную сторону поршня. | |
В тексте |
Рис. 14 Износная нагрузка на основную и вспомогательную сторону поршня. | |
В тексте |
Рис. 15 Износная нагрузка на основную и вспомогательную сторону поршня. | |
В тексте |
Рис.![]() Фото поршней после испытаний. | |
В тексте |
Влияние зазора между поршнем и цилиндром на трение поршня (Конференция)
Влияние зазора между поршнем и цилиндром на трение поршня (Конференция) | ОСТИ.GOVперейти к основному содержанию
- Полная запись
- Другое связанное исследование
Желательно минимизировать зазор между поршнем и цилиндром, чтобы уменьшить шум и подавить вибрацию. Хотя для этой цели были предприняты значительные усилия, повышенная сила трения поршня и возникновение заедания по-прежнему не позволяют реализовать идеальный зазор. Для определения нижнего предела поршневого зазора важно выяснить следующие неизвестные; какая часть поршня способствует увеличению трения при уменьшении зазора поршня, на какой фазе движения поршня происходит увеличение трения и как зазор поршня влияет на явления смазки.
- Авторов:
- Такигучи, М; Кикучи, Х; Фурухама, С.
- Дата публикации:
- Идентификатор ОСТИ:
- 5893146
- Номер(а) отчета:
- КОНФ-8810120-
- Тип ресурса:
- Конференция
- Связь с ресурсами:
- Конференция: собрание и выставка Общества автомобильных инженеров по горюче-смазочным материалам, Портленд, штат Орегон, США, 10-13 октября 1988 г.
; Дополнительная информация: технический документ 881621
.
- Страна публикации:
- США
- Язык:
- Английский
- Тема:
- 33 УСОВЕРШЕНСТВОВАННЫЕ ДВИГАТЕЛИ; ДВИГАТЕЛЬ ВНУТРЕННЕГО СГОРАНИЯ; СМАЗКА; ЦИЛИНДРЫ; ТРЕНИЕ; КОЭФФИЦИЕНТ ТРЕНИЯ; ПОРШНИ; ТЕСТИРОВАНИЕ; ДВИГАТЕЛИ; ТЕПЛОВЫЕ ДВИГАТЕЛИ; 330100* — Двигатели внутреннего сгорания
Форматы цитирования
- MLA
- АПА
- Чикаго
- БибТекс
Такигучи М., Кикучи Х. и Фурухама С. Влияние зазора между поршнем и цилиндром на трение поршня . США: Н. П., 1988.
Веб.
Копировать в буфер обмена
Такигучи М.
, Кикучи Х. и Фурухама С. Влияние зазора между поршнем и цилиндром на трение поршня . Соединенные Штаты.
Копировать в буфер обмена
Такигути М., Кикучи Х. и Фурухама С. 1988.
«Влияние зазора между поршнем и цилиндром на трение поршня». Соединенные Штаты.
Копировать в буфер обмена
@статья{osti_5893146,
title = {Влияние зазора между поршнем и цилиндром на трение поршня},
автор = {Такигучи, М., Кикучи, Х., Фурухама, С.},
abstractNote = {Желательно минимизировать зазор между поршнем и цилиндром, чтобы уменьшить шум и подавить вибрацию. Хотя для этой цели были предприняты значительные усилия, повышенная сила трения поршня и возникновение заедания по-прежнему не позволяют реализовать идеальный зазор. Для определения нижнего предела поршневого зазора важно выяснить следующие неизвестные; какая часть поршня способствует увеличению трения при уменьшении зазора поршня, на какой фазе движения поршня происходит увеличение трения и как зазор поршня влияет на явления смазки. },
дои = {},
URL-адрес = {https://www.osti.gov/biblio/5893146},
журнал = {},
номер =,
объем = ,
место = {США},
год = {1988},
месяц = {1}
}
Копировать в буфер обмена
Дополнительную информацию о получении полнотекстового документа см. в разделе «Доступность документа». Постоянные посетители библиотек могут искать в WorldCat библиотеки, в которых проводится эта конференция.
Экспорт метаданных
Сохранить в моей библиотеке
Вы должны войти в систему или создать учетную запись, чтобы сохранять документы в своей библиотеке.
Аналогичных записей в сборниках OSTI.GOV:
- Аналогичные записи
Задир из-за недостаточного зазора на юбке поршня · Технипедия · Motorservice
Настройки
Вернуться к поиску
Информация о диагностике
Что мы имеем в виду, когда говорим о судорогах, вызванных отсутствием разрешения? Что вызывает сухой ход между поршнями и цилиндрами? Что вызывает заедание частей юбки поршня? Почему поршневой палец стал синего цвета? А как на дне юбки поршня появляются точки упора и противодействия? В этой статье вы найдете подробные ответы.
Задир из-за недостаточного зазора на юбке поршня
Описание повреждения
- Несколько похожих участков задиров вокруг юбки поршня.
- Задиры на нажимной и противодействующей сторонах юбки поршня, т.е. задиры на противоположных сторонах.
- Изменение поверхности от ярких следов износа до гладких темных участков износа, вызванных трением.
- Неповрежденная кольцевая зона.
Оценка ущерба
Зазор между юбкой поршня и рабочей поверхностью цилиндра был либо слишком узким по конструкции, либо ограничивался искривлением, которое, возможно, не возникало до тех пор, пока двигатель не работал.
Примечание:
В отличие от задира из-за недостатка смазки, задир из-за недостаточного зазора всегда возникает после короткой обкатки после ремонта двигателя.
Возможные причины повреждения
- Диаметр цилиндра слишком мал.
- Головка цилиндра затянута слишком сильно или затянута неравномерно (деформация цилиндра).
- Неровные сопрягаемые поверхности на блоке цилиндров или головке цилиндров.
- Грязные или поврежденные резьбовые отверстия или болты головки блока цилиндров.
- Заклинившие или недостаточно смазанные посадочные поверхности.
- Использование неправильных или неподходящих прокладок головки блока цилиндров.
- Деформация цилиндра, вызванная неравномерным нагревом из-за отложений извести, грязи или других неисправностей в системе охлаждения.
следы задиров под углом 45°
Описание повреждения
- Задиры как на нажимной, так и на противодействующей стороне, смещены примерно под углом 45° к оси поршневого пальца.
- Области задиров меняются от ярких следов износа до относительно гладких, темных участков износа, вызванных трением (рис. 1).
- Поршневой палец имеет синий цвет закалки (рис. 3). Причина: ложе поршневого пальца нагрелось из-за недостаточного зазора или недостатка масла.
Оценка ущерба
Прилив поршневого пальца сильно нагрелся. Тонкостенная и эластичная юбка поршня способна компенсировать повышенное тепловое расширение на напорной и антираспорной сторонах. Бобышка поршневого пальца становится более жесткой, и ее расширение увеличивается. Зазоры сужаются и происходит заедание поршня. Задир поршня происходит в районе перехода между бобышкой поршневого пальца и юбкой поршня.
рисунок 1 Рис. 2 Рис. 3Возможные причины повреждения
- Механическая перегрузка шатунного подшипника, напр. из-за ненормального горения.
- Неисправность/трещина в жиклере впрыска масла.
- Недостаточное или отсутствующее давление масляного насоса.
- Недостаточное количество смазки при первом запуске двигателя. Поршневой палец не был смазан или был недостаточно смазан при сборке.
- Выход из строя втулки шатуна (заедание поршневого пальца) из-за недостаточного зазора или смазки.
- Ошибка установки в процессе опрессовки поршневого пальца (шатуна горячей посадкой).
В процессе усадки необходимо следить за тем, чтобы сразу после вставки поршневого пальца не проверялась свобода перемещения основания поршневого пальца путем наклона поршня вперед и назад. Температуры между двумя компонентами выравниваются сразу после того, как холодный поршневой палец вставляется в горячий шатун. Подвод тепла увеличивает тепловое расширение поршневого пальца, как это имеет место во время работы двигателя. Если кровать перемещается в этом состоянии, это может привести к возникновению начальных следов трения или заедания. Это может привести к жесткости или выходу из строя постели поршневого пальца во время работы двигателя. По этой причине дайте собранным компонентам остыть перед проверкой свободы движения.
Задир из-за недостаточного зазора в нижней части юбки
Описание повреждения
- Задир из-за недостаточного зазора на концах нижней юбки, со следами износа и следами обратного износа.
- Следы износа меняются от ярких следов износа до гладких темных участков износа, вызванных трением (рис.
1).
- В остальных частях поршня нет ничего необычного.
- Задиры на гильзе цилиндра в районе нижних уплотнительных колец (рис. 2).
Оценка ущерба
Задир поршня на нижней кромке юбки поршня был вызван деформацией/ограничением зазоров в нижней части гильзы цилиндра.
рисунок 1 Рис. 2Возможные причины повреждения
- Неподходящие уплотнительные кольца: чрезмерно толстые уплотнительные кольца могут деформировать гильзу цилиндра и уменьшить рабочий зазор поршня.
- Дополнительное использование жидких герметиков в канавке уплотнительного кольца. Для герметизации поверхностей уплотнительные кольца должны иметь возможность упруго деформироваться. Необходимое для этого свободное пространство в канавке нельзя заполнять дополнительным герметиком.
- Перед установкой не были удалены остатки уплотнительного кольца или грязь в канавках уплотнительного кольца.
- Если уплотнительные кольца перекручиваются при вставке гильзы цилиндра или выскальзывают из канавки для уплотнительного кольца, гильза цилиндра сжимается в этой области.
Во избежание этого при установке гильзы цилиндра всегда следует использовать смазку.
Ключевые слова :
поршень , поршневое кольцо , комплект поршневых колец , поршневой палец, поршневой палец , Зазор в замке поршневого кольца, Зазор поршневого кольца , канавка поршневого кольца , бобышка поршневого пальцаГруппа товаров :
Поршни и компонентыГруппы продуктов на ms-motorservice.

Только для технического персонала. Все содержимое, включая изображения и диаграммы, может быть изменено. Для назначения и замены обратитесь к текущим каталогам или системам, основанным на TecAlliance.
Использование файлов cookie и защита данных
Motorservice Group использует файлы cookie, сохраненные на вашем устройстве, для оптимизации и постоянного улучшения своих веб-сайтов, а также для статистических целей. Дополнительную информацию об использовании нами файлов cookie можно найти здесь, а также информацию о нашей публикации и уведомление о защите данных.
Нажав «ОК», вы подтверждаете, что приняли к сведению информацию о файлах cookie, заявлении о защите данных и деталях публикации. Вы также можете в любое время изменить настройки файлов cookie для этого веб-сайта.
Настройки конфиденциальности
Мы придаем большое значение прозрачной информации, касающейся всех аспектов защиты данных. Наш веб-сайт содержит подробную информацию о настройках, которые вы можете выбрать, и о том, какое влияние оказывают эти настройки. Вы можете изменить выбранные настройки в любое время. Независимо от того, какой выбор вы выберете, мы не будем делать никаких выводов о вас как о личности (за исключением случаев, когда вы явно указали свои данные). Для получения информации об удалении файлов cookie обратитесь к функции справки в вашем браузере. Вы можете узнать больше в заявлении о защите данных.
Измените настройки конфиденциальности, нажав на соответствующие кнопки
- Необходимый
- Удобство
- Статистика
Необходимый
Файлы cookie, необходимые для системы, обеспечивают правильную работу веб-сайта. Без этих файлов cookie могут возникнуть сбои или сообщения об ошибках.
Этот веб-сайт будет:
- Сохранение файлов cookie, необходимых системе
- Сохранение настроек, которые вы делаете на этом веб-сайте
Этот сайт никогда не будет делать следующее без вашего согласия:
- Сохраните ваши настройки, такие как выбор языка или баннер cookie, чтобы вам не пришлось повторять их в будущем.
- Оценивайте посещения анонимно и делайте выводы, которые помогут нам оптимизировать наш веб-сайт.
- Сделать выводы о вас как о личности (за исключением случаев, когда вы явно указали свои данные, например, в контактных формах)
Удобство
Эти файлы cookie упрощают использование веб-сайта и сохраняют настройки, например, чтобы вам не приходилось повторять их каждый раз, когда вы посещаете сайт.
Этот веб-сайт будет:
- Сохранение файлов cookie, необходимых системе
- Сохранение ваших настроек, таких как выбор языка или баннер файлов cookie, чтобы вам не пришлось повторять их в будущем.
Этот сайт никогда не будет делать следующее без вашего согласия:
- Анонимно оценивайте посещения и делайте выводы, которые помогут нам оптимизировать наш веб-сайт.
- Сделать выводы о вас как о личности (за исключением случаев, когда вы явно указали свои данные, например, в контактных формах)
Конечно, мы всегда будем соблюдать настройку «не отслеживать» (DNT) в вашем браузере. В этом случае файлы cookie для отслеживания не устанавливаются и функции отслеживания не загружаются.
Тепловое моделирование тонкой смазочной пленки в месте соединения поршневого компрессионного кольца и грубой гильзы цилиндра
Введение
Двигатель внутреннего сгорания представляет собой термодинамическую систему, которая работает при повышенных температурах порядка 100–500°C. Термомеханические отказы, такие как задиры, износ, термическая усталость и т. д., очевидны из-за непрерывного сгорания и рассеивания тепла с последующим контактным трением из-за относительно движущихся частей работающего двигателя. Поэтому важно смоделировать тепловое поведение движущегося компонента, такого как поршневое компрессионное кольцо и смазываемый контакт гильзы цилиндра, который считается парой, вносящей наибольший вклад в трение в работающем двигателе. Это может помочь более точно прогнозировать срок службы смазки и компонентов.
В последние годы было предпринято много попыток смоделировать поршневое кольцо и гильзу цилиндра с помощью различных численных и аналитических методов. Почти в каждом случае эта контактная проблема решается для трения и других рабочих параметров. Это достигается путем рассмотрения смазываемого контакта кольца и гильзы как соединения гидродинамического или упругогидродинамического типа, которое приспосабливается к глобально деформированной форме кольца. В некоторых случаях рассматривается осевое, а также боковое наклонное движение юбки поршня и его влияние на смазку витого кольца и гильзы. На протяжении многих лет исследователи пытались понять модель недостаточной смазки (Finol et al., 2009).), влияние искривленного отверстия на смазку (Mishra, 2013), искривление отверстия цилиндра при работающем двигателе (Ma et al., 1995), а также трение и износ при контакте поршневого кольца и гильзы цилиндра (PRCL). Влияние шероховатости футеровки на фрикционные характеристики изучалось с использованием как детерминированной модели, так и модели среднего течения. В шероховатой футеровке заштрихованная поверхность ее поверхности оказывает значительное влияние на текучесть и удержание смазки.
Кроме того, существует несколько экспериментальных методов, разработанных для проверки численных результатов такой тепловой трибодинамической системы. В контакте поршневого кольца и гильзы цилиндра наблюдается переход режима смазки. Это означает, что, несмотря на наличие гидродинамического режима (h > 1,0 мкм) на большей части такта двигателя, из-за повышенного давления дымовых газов (между 300 и 400° положения кривошипа) на сжатии и переходе рабочего такта большая часть трения теряется. в этом регионе из-за смешанного режима. Как обсуждалось ранее, двигатель, являясь термомеханической системой, развивает температуру, достаточную для изменения его реологических свойств (вязкости, плотности и гидродинамического давления) связанных с ним смазываемых контактных пар.
Текущие исследования связаны с нестационарной термогидродинамической моделью для изучения теплового поведения тонкой пленки смазки микропорядка между поршневым кольцом и гильзой цилиндра в одноцилиндровом четырехтактном двигателе, работающем на метаноле. Детали спецификации двигателя приведены в дополнительных материалах. Поскольку смазочные материалы синтезируются с учетом их температурной стабильности при максимальной брутто-температуре горячего двигателя (Finol et al., 2009). Опять же, повышение температуры из-за трения является преходящим явлением и сильно варьируется. Это зависит от различных факторов, таких как частота вращения двигателя, крутящий момент, фиктивные потери, продолжительность эксплуатации, реология смазочного материала, динамика поршневой подсистемы и т. д. (Мишра, 2013).
Возникающее в этой ситуации трение иногда обусловлено гидродинамическим трением только при преобладании гидродинамического условия (2 мкм < h < 5 мкм) (Ma et al., 1996). При высоком давлении сгорания в межкривошипном пространстве (300–400°) возникает смешанный режим (Мишра, 2012). Опять же, при реверсировании ВМТ и НМТ граничный режим и контакт неровностей происходит за счет мгновенного прекращения и смены направления скольжения поршня (Mishra et al. , 2008).
По этой причине температурный профиль формируется за счет конвективного теплообмена в гидродинамическом режиме и преимущественно кондуктивного теплообмена в смешанном и граничном режимах. Эта температура изменяет реологию смазки (Shimada et al., 2004). Поэтому необходимо исследовать температуру в различных условиях эксплуатации.
Теплопередача от камеры сгорания к внешней поверхности цилиндра является сильно нелинейным явлением (Finol et al., 2009). Он проходит прямо или опосредованно на стенку цилиндра из горячей камеры сгорания, содержащей продукт сгорания воздушно-топливной смеси. Прямая теплопередача включает в себя излучение, а также кондуктивное тепло, которые инициируются камерой сгорания, зависящей от времени. Но косвенная теплопередача включает поток тепла сначала к подвижному поршневому узлу, а затем к гильзе цилиндра через масляную пленку контакта кольцевой гильзы и юбки гильзы (Finol et al., 2009).). Косвенный теплообмен и его режим зависят от режима, который испытывает контакт. Например, в гидродинамическом режиме, сохраняющемся на большей части цикла двигателя контакта юбка-втулка и кольцо-втулка, толщина пленки составляет от 2 до 10 мкм. При положении коленчатого вала 300–400° четырехтактного двигателя преобладает смешанный режим из-за более высокого давления сгорания на задней части кольца, которое выполняет функцию уплотнения (Mishra et al., 2009). Тепловой баланс между теплоносителем и дымовыми газами необходим с дополнительными источниками тепла за счет контактного трения из-за вязкого сдвига, а также взаимодействия шероховатостей (Morris et al., 2013). Такое тепло трения и причина его образования, а также его влияние на температурный профиль смазочного материала будут изучены в данной исследовательской работе. Повышение температуры смазки изменяет реологические свойства. Уменьшение трения может свести к минимуму повышение температуры. Следовательно, необходимо понять механизм трения в таком смазочном контакте.
Контактное трение в смазываемом соединении возникает за счет сдвига слоя смазки. Свою роль играет гидродинамическое или ЭДЖ-действие (Dowson et al., 1983). Действие ЭДЖ количественно определяется давлением пленки. Такой демпфирующий эффект зависит от толщины пленки; уносят скорость, вязкость и плотность (Harigaya et al., 2003). Снижение трения достигается заменой гладкой гильзы цилиндра на шероховатую гильзу цилиндра с шероховатостью поверхности в виде крестообразной формы. Можно сохранить гладкую вершину и глубокую впадину в таком образце шероховатости, который изготовлен методом двойного хонингования. Поверхность контакта имеет гладкую верхнюю часть и глубокую впадину благодаря поперечному рисунку, что приводит к меньшему трению из-за гладкой верхней части и более легкому сбору частиц износа из-за глубокой впадины (Spencer et al., 2011). Для моделирования поверхность крестообразной формы трудно охарактеризовать с помощью традиционных параметров, таких как среднее значение, среднеквадратичное значение, R к . Так как такая характеристика дает значительные ошибки и полностью изменяет профиль поверхности.
Следовательно, подходит характеристика шероховатости на основе кривой площади опоры. Таким образом, характеристика R k по DIN считается более подходящей. В смешанном режиме смазки гидродинамический эффект/эффект EHL оценивается с помощью уравнения Рейнольдса, основанного на усредненном расходе. Используемые коэффициенты текучести модифицированы введением в них R k . Таким образом, численно оцененное трение совпадает с трением, измеренным экспериментально Фурухамой и Сасаки (19).83).
На контактное трение поршневой подсистемы также влияет овальность отверстия и соответствие кольца в круглом отверстии (Ma et al., 1995). Прилегаемость — это способность кольца сидеть на отверстии, не оставляя зазора. Это функция упругого давления кольца, давления газа, геометрии отверстия кольца и порядка отверстия (Hill and Newman, 1984). Кроме того, овальность отверстия возникает из-за неправильной обработки, термоупругой деформации (Sun, 1991) из-за тепла, выделяемого в камере сгорания.
Эффект овального профиля отверстия также изменяет профиль пленки и изменяет трибологические характеристики. Более высокий порядок отверстий способствует повышенному трению и значительному износу. Прорыв газов при более высоком давлении сгорания во время сжатия и рабочего такта также может привести к снижению выходной мощности двигателя (Rahmani et al., 2012). Все условия в работающем двигателе, такие как динамика, тепловое воздействие, контакт и т. д., взаимосвязаны друг с другом. Даже характер износа связан с зазором между кольцом и гильзой (Ma et al., 2006). Переходный характер осевого, позднего и наклонного движения юбки поршня не только снижает вероятность задира поршня, но также способствует изгибу кольца во время одновременного движения уплотнения и скольжения (Балакришнан и Рахнежат, 2005). Некруглая форма отверстия отвечает за неравномерный зазор конформного кольца и имеет решающее значение для продувки газа Абэ и Судзуки (19).95) и Окамото и Сакаи (2001). Хотя такие контакты в основном работают в гидродинамическом режиме, потери на трение больше в смешанном режиме из-за меньшей толщины пленки из-за повышенного давления продуктов сгорания. Даже если в смешанном режиме контакт с неровностями отсутствует, микроструктурная ориентация поверхности изменяет геометрию пленки и требует модели уравнения Рейнольдса типа среднего потока для решения проблем контакта (Патир и Ченг, 1978, 1979). Существует вероятность контакта шероховатости в контакте кольца с отверстием, хотя он кратковременный и в основном вблизи мертвых точек (ВМТ и НМТ). Здесь скорость скольжения прекращается и преобладает гидродинамическое воздействие из-за сжатия. Поскольку сжимающего действия недостаточно, шероховатость контакта очевидна. В этой ситуации баланс сил находится между контактным давлением выступа и суммой давления газа и упругого давления кольца. Это также известно как граничный режим, при котором контактное трение в значительной степени зависит от плотности неровностей и радиуса вершины неровностей (Гринвуд и Трипп, 19).70). В контексте смены режима сообщается о многих исследованиях (Hu et al., 1994), и вычисленные таким образом сила трения и потери мощности проверяются с помощью механизма результатов испытательного стенда (Akalin and Newaz, 2001a,b; Bolander et al.
, 2005). ). Детерминистическая характеристика шероховатости и предположение о круглой форме вершины неровности с измеренным значением шероховатости (Xu and Sadeghi, 1996) также используются при решении задач EHL. В последних достижениях эластогидродинамическая смазка поршневых колец (Oh et al., 1987), термосмешанная гидродинамическая методика (Shahmohamadi et al., 2013), аналитическая оценка модального поведения подогнанного компрессионного кольца (Baker et al., 2011) и экспериментальная оценка трения узла поршня в условиях двигателя и воспламенения (Mufti and Priest, 2005 ) разработаны в дополнение к исследованиям колец. В дополнение к этому, корреляционное исследование конструкции поршневых колец и смазки (Söderfjäll et al., 2017), мониторинг состояния поршневых колец на основе характеристик сгорания и тепловых характеристик (Mohamed, 2018) оказались полезными при анализе колец. Влияние покрытия поршневых колец (Peng and Huang, 2017), эластогидродинамической смазки поршня (Asaulyak et al.
, 2016), текстурирование колец и рассмотрение некруглости отверстия цилиндра (Usman and Park, 2017) как в численных, так и в экспериментальных методах дают много полезная информация для увеличения срока службы колец и вкладышей.
Несмотря на то, что в недавних и более ранних исследованиях было получено много полезных результатов в области анализа контактного трения поршневых колец и гильз цилиндров, анализ температуры пленки с учетом всей этой области вместе будет шагом вперед и, следовательно, является целью данной исследовательской работы.
Формулировка задачи и управляющее уравнение
Как было сказано ранее, долговечность компонентов и смазочного материала в значительной степени зависит от потерь на трение в работающем двигателе. Из-за более высокого повышения температуры развиваются напряжения термической усталости, которые приводят к выходу из строя детали. Также пониженная вязкость увеличивает контактное трение за счет снижения гидродинамического давления.
Почему тепловое моделирование контакта поршневого кольца с гильзой цилиндра?
Прежде чем перейти к определению теплового моделирования соединения поршневого компрессионного кольца и гильзы цилиндра, сначала поясним значение соединения кольцо-гильза системы поршень-цилиндр. Согласно недавней работе (Mishra et al., 2009), соединение в контексте контакта кольца с гильзой определяется как переменный зазор, остающийся для прохождения смазки после выполнения уплотняющего действия. Он образован за счет собственной конструкции системы уплотнений, предназначенной для остановки газа высокого давления, образующегося при сгорании воздушно-топливной смеси. При переходе толщина пленки между соединениями кольца и лайнера варьируется от 0,5 до 5,0 мкм (Mishra et al., 2009).) за счет действия давления дымовых газов на тыльную сторону кольца вместе с силой упругого давления кольца. Это приводит к переходу режима смазки от гидродинамического к граничному через смешанный. Соответственно изменяются скорость теплопередачи и характеристики износа. В большей части цикла двигателя это соединение работает гидродинамически, что приводит к меньшему износу вкладыша или кольца. Но в зоне высокого давления цикла двигателя, так как в окрестности мертвой точки преобладает смешанный режим, происходит мгновенное прекращение; есть контакт металла с металлом из-за наличия очень тонкой пленки. Износ выше из-за этого условия, хотя из-за наличия ультратонкой пленки происходит значительная передача тепла (Ma et al., 2006). Фрикционный нагрев во всех этих случаях существенно отличается друг от друга из-за вязкости, шероховатости и сдвига кольца сильно различаются от случая к случаю. Следовательно, тепловая модель, включающая этот переменный фрикционный нагрев с теплопередачей двигателя, необходима для более четкого понимания рассеивания тепла двигателем.
Настройка параметров соединения для теплового моделирования
Тепловое моделирование основано на концепции теплопередачи и науки о смазке, связанной с поршневым кольцом и юбкой, контактирующими с гильзой цилиндра (Balakrishnan and Rahnejat, 2005). Для достижения этого необходимы геометрия кольца, профиль юбки, текстура поверхности гильзы и детали прилегания к каналу кольца. Количественная оценка всех из них для модели имеет важное значение.
Кольцевая геометрия
Кольцевая геометрия является определяющим параметром, определяющим форму толщины пленки. Форма кольца, представленного на рисунке 1, аппроксимируется параболой, таким образом:
sij=xij2Δij(0,5b)2
Здесь дельта — это коэффициент смещения, который представляет собой расстояние между вершиной кольца и хордой кривизны. Параболический профиль, созданный из-за смещения кольца, устанавливает минимумы в одной точке и идеальную зону схождения-расхождения, способствующую лучшему гидродинамическому действию для обоих направлений возвратно-поступательного движения (Mishra et al., 2009). Параметр «b» представляет собой ширину лицевой поверхности кольца и видимую линию контакта.
Рис. 1. (A) Геометрия профиля кольца. (B) Изменение профиля из-за смещения геометрии.
Прилегаемость отверстия кольца
Прилегаемость — это способность кольца подходить к внутренней окружности отверстия без образования зазора (Abe and Suzuki, 1995). Более точное расположение отверстий и колец обеспечивает лучшую герметизирующую способность. Так как минимальная толщина пленки неравномерна по окружности из-за овальности отверстия в гильзе цилиндра. Следовательно, кольцо вряд ли полностью соответствует отверстию и предлагает анализ прилегания, чтобы найти изменяющийся по окружности зазор кольцевой гильзы. Уравнение (1) показывает минимальный зазор кольцевого отверстия.
{h0(θc)=ΔR(θc)−ξn(θc), если ΔR(θc)>ξn(θc)h0(θc)=0, если ΔR(θc)≤ξn(θc) (1)
Где, ΔR(θc)=∑i=2n(Aicosiθc+Bisiniθc).
А ξ n (θ c ) – коэффициент соответствия. Это функция силы давления газа, силы упругого давления кольца, геометрии кольца и прочности материала. Канал считается четвертого порядка ( n = 4).
ξn(θc)=3[Fe+Fg(θc)]Rb2(D-a)2Eba3(n2-1)2 (2)
Параметр «a» – глубина кольца или радиальная толщина кольца. Чистая сила давления продуктов сгорания, действующая на кольцо, представляет собой разность сил сзади и спереди кольца и определяется как:
Fg(θc)=[Pgb-Pgf(θ)]b (3)
Где,
Pgf(θ)=Pt+(Pl-Pt)xin(θ)+xc(θ)2b (4)
Упругое давление по окружности кольца неравномерно (Окамото и Сакаи, 2001). Она максимальна в точке 90° от свободного конца. Установлено, что максимальное значение составляет 0,2 МПа. Мы взяли равномерное давление 0,2 МПа по окружности кольца.
Fe=Peb (5)
Значение F г получено из давления дымовых газов согласно (Mishra, 2012). При таком анализе оценивается неосесимметричный минимальный зазор по окружности кольца с учетом давления газа. Формы колебаний из-за овальности отверстия количественно определяются порядком отверстия. Различные формы мод и их отклонение от номинального радиуса приведены на рис. 2.
Рис. 2. (A) Некруглое отверстие второго порядка, радиальная разница 15 мкм. (B) Некруглое отверстие четвертого порядка, радиальная разница 5 мкм. (C) Некруглое отверстие восьмого порядка, радиальная разница 5 мкм.
Отверстие считается в этом случае овальным после термической и упругой деформации. Следовательно, предполагается, что это отверстие четвертого порядка. Шероховатость поверхности с гладкой вершиной и глубокой впадиной намеренно создана на поверхности гильзы для лучшей смазки. Очень важно понимать текстуру внутренней поверхности вкладыша.
Состав пленки соединения юбка-вкладыш и кольцо-вкладыш в смешанном режиме
Толщина пленки между контактным соединением кольцевого вкладыша представляет собой сумму номинальной пленки, формы профиля кольца, локальной деформации кольца и общей деформации кольца. Порядок пленки, как сообщается (Mishra, 2012), составляет 0,5–5,0 мкм. Сила давления газа и сила упругого давления кольца оказывают доминирующее влияние на пленку кольцевой футеровки.
hr=h0(θc)+Sj+Δj+δi (6)
Пленка между юбкой и подкладкой представляет собой сумму номинальной пленки, профиля юбки и наклона юбки из-за относительного эксцентричного расположения верхней и нижней частей. Пленка в основном определяется силами инерции и моментом, возникающими при возвратно-поступательном движении поршня (Balakrishnan and Rahnejat, 2005).
hsk=C+εtcosφ+(εb-εt)yLcosφ+Sk(y) (7)
Порядок пленки юбки-вкладыша 5–20 мкм, режим смазки всегда элостогидродинамический. В большинстве случаев при больших потерях на трение из-за уменьшенной толщины пленки 1–3 мкм реализуется смешанный режим смазки. Это ситуация, когда контакта металл-металл нет, но профиль шероховатости сильно влияет на течение смазки в стыке. Условие, лучше всего описанное с помощью уравнения Рейнольдса среднего расхода Патиром и Ченгом, 1979) и дается уравнением (8).
∂∂x(ϕxh412η∂ph∂x)+∂∂y(ϕyh412η∂ph∂y)=U1+U22∂(ϕgh)∂x+U1-U22σ∂ϕs∂x+∂h∂t (8)
3
В уравнении (8) p h представляет собой гидродинамическое/EHL давление, создаваемое в смазочной пленке. Размерное давление, из которого рассчитывается p h , получается путем решения уравнения среднего расхода Рейнольдса (Патир и Ченг, 1978, 1979), приведенного в уравнении (8). Факторы текучести являются функцией параметра пленки. При изменении характеристики шероховатости для одной и той же поверхности будет разное значение коэффициента текучести. В этом анализе такие коэффициенты получены на основе R к и приведен в Приложении 1. Направление уноса масла – по оси абсцисс, бокового подтекания – по оси у.
Существует взаимозависимость между плотностью смазки, давлением пленки, повышением температуры и окружающим давлением согласно (Houpert, 1985). Это дается уравнением (9а). Опять же, изменение вязкости при изменении температуры и давления рассматривается с помощью комбинированного закона (Dowson and Higginson, 1959; Mufti and Priest, 2005), приведенного в уравнении (9).б) как.
ρ=ρ0(1-0,65×10-3Δθ)[1+6×10-10(p-Patm)1+1,7×10-9(p-Patm)] (9a)
η=η0exp{( ln η0+9,67)[(Θ-138Θ0-138)-S0(1+p-Patm1,98×108)Z-1]} (9b)
Где: Θ = θ + 273 и Θ 0 = θ 0 + 273, и:
Z=α05,1×10-9[ln η0+9,67]и S0=β0(Θ0-138)ln η0+9,67 (10)
Сдвигающее действие в смешанном режиме
Касательное напряжение, возникающее в смешанном режиме, возникает из-за быстрого относительного движения слоя смазки в смежной геометрии поверхности (Патир и Ченг, 19).79) затронутое сопряжение и задается как:
τ=ηUh(ϕfg+ϕfs)-ϕfph3∂p∂x (11)
Следовательно, сила трения представляет собой интегрирование напряжения сдвига по площади контакта и составляет:
F=∬τdxdy (12)
Граничное трение для контакта поршневой подсистемы
В режиме граничной смазки контакт между неровностями воспринимает нагрузку. Первоначально это адресовано Гринвуду и Триппу (1970); Ма и др. (1995 г.); Акалин и Ньюаз (2001a,b); Боландер и др. (2005) и Мишра (2012) выполнили и использовали нелинейную аппроксимацию, применимую к грубому соединению поршневого кольца и отверстия, и предсказали p asp as:
pasp=K*E′F2.5(λrk) (13)
В котором шероховатость поверхности кольца и отверстия считается изотропной. Функция F 2,5 (λ rk ) относится к вероятностному распределению высот неровностей. Для гауссовского распределения неровностей F 2,5 (λ rk ) имеет предельную форму (Hu et al., 1994) как:
F2,5(λrk)=12π∫λrk∞ -λrk)5/2es22ds (14)
Аппроксимация кривой этой функции больше подходит для численного анализа шероховатой поверхности гильзы. Для типичного контакта с кольцевым отверстием Hu et al. (1994) формулируют эту функцию как:
F2. 5(λ)={A(β−λrk)z λrk≤β0 λrk>β (15)
Где: −5 , z = 6,804 и λrk=hRk (параметр масляной пленки Штрибека).
K * в уравнении (17) является функцией шероховатости поверхности как: K*=5,318748×1010Rk5/2.
Wc=∑∑pcdxdy
And,Fb=∫τ0dA+μWc (16)
При замене R k стандартное отклонение шероховатости поверхности улучшается до более реалистичного значения коэффициента пленки. . Поскольку параметр R k является правильным представлением шероховатости в виде крестообразной шероховатости, встроенной в гильзу цилиндра.
В уравнении (16) F b представляет собой силу трения из-за граничной смазки. Тонкий адсорбированный слой смазки находится на вершине неровности и проявляет неньютоновское напряжение сдвига. µ = 0,17 – коэффициент трения между кольцом и материалом футеровки. Этот анализ предназначен только для граничного взаимодействия (Bolander et al., 2005). При смешанном режиме метод расчета трения меняется. Хотя в недавней литературе сообщается о многих детерминированных моделях контакта со смазкой на шероховатой поверхности, текущая исследовательская работа ограничивается количественным определением поверхности с помощью методов подбора кривой.
Двигатель внутреннего сгорания предназначен для создания более высокого давления газа (в диапазоне 120 бар) в каждом цикле двигателя. Только тогда такая сила давления может быть преобразована в инерционную динамику поршня для совершения возвратно-поступательного движения и превращения ее в требуемый крутящий момент коленчатого вала. Это стало возможным благодаря взрывному горению воздушно-топливной смеси, создающей огромное количество тепла и давления. На рис. 3 показано циклическое давление в камере сгорания вместе с межкольцевым давлением газа в диапазоне углов поворота коленчатого вала 180–540°. Причиной выбора этого диапазона кривошипа является нарастание давления в камере в основном в этой зоне. В положении покоя кривошипа она стремится к нулю и оказывает незначительное влияние на рабочие параметры. В поршневом узле с тремя кольцами имеется два межкольцевых зазора. Из-за утечек газа в поршневом узле также присутствует межкольцевое давление газа.
Рисунок 3 . Давление в камере сгорания и межкольцевое давление газа.
Тепловой поток
Стационарное распределение конвективного и радиационного теплового потока по длине хода в соответствующем месте в канале цилиндра. Эти тепловые потоки являются результатом прямой передачи тепла от рабочего тела к стенке цилиндра. Поток тепла в стационарном состоянии (Finol et al., 2009) согласно закону охлаждения Ньютона определяется уравнением (17):
qg=hg(Tg-Twg) (17)
H G — коэффициент теплопередачи на стороне газа,
T G — температура газа,
T —
T —
T . диаметр отверстия и
q g скорость теплового потока.
Теплопроводность через поршневое кольцо и юбку к гильзе цилиндра
Теплопередача посредством теплопередачи происходит между поршневым кольцом и стенкой цилиндра и юбкой и гильзой цилиндра (Shahmohamadi et al., 2013). Допущение включает передачу тепла от поршневого кольца к смазочному маслу, а также от юбки к гильзе цилиндра в соответствии с законом теплопроводности Фурье в радиальном направлении, который определяется как:
qpr=QAbr=-k0Tr-TL(h0)r (18)
q pr представляет собой мгновенный тепловой поток между кольцом и частью кольца, контактирующей с вкладышем.
Аналогично,
qpsk=QAbsk=-k0Ts-TL(h0)sk (19)
q psk представляет собой мгновенный тепловой поток между юбкой и частью юбки, контактирующей с гильзой.
( h 0 ) sk минимальная толщина пленки между юбкой и той частью юбки, которая контактирует с гильзой.
А, ( h 0 ) r минимальная толщина пленки между кольцом и частью кольца, контактирующей с гильзой. Температура поперек пленки из-за горения над кольцом в контакте с частью лейнера:
Tr(z)=Tr-Tr-TL(h0)rh0(z)r (20)
контакт юбки и вкладыша:
Tsk(z)=Tsk-Tsk-TL(h0)skh0(z)sk (21)
Граничные условия, наложенные для анализа:
At z = a, h 0 (z) = (h 0 ) r , and at z = 0, h 0 = 0
T r ( z ) и T sk ( z ) — изменение температуры по всей пленке. В направлении скольжения происходит повышение температуры из-за фрикционного нагрева. Пусть это будет T r ( y ) и T sk ( и ). Поэтому результирующее изменение температуры (Shahmohamadi et al. , 2013) в таком случае задается как:
Tr(y,z)=T(y)+{Tr+Tr-TL(h0)rh0(z)r} (22)
для кольца и части вкладыша, соприкасающейся с вкладышем.
А,
Цк(у,з)=Т(у)+{Цк+Цк-Тл(ч0)сх0(з)ск} (23)
для юбки и части вкладыша, соприкасающейся с вкладышем.
( ч 0 ) р и ( ч 0 ) sk можно определить по релаксации пленки после схождения приложенной нагрузки с реакцией смазки. Приложенная нагрузка представляет собой сумму силы давления газа и силы упругого давления кольца. Однако в этом анализе мы рассмотрели систему в термически стабильном состоянии, а передача тепла происходит за счет движения пленки жидкости и сдвига.
Теория повышения температуры в направлении захвата из-за фрикционного нагрева
Дальнейшее повышение температуры смазочного материала происходит из-за фрикционного нагрева. Такое повышение температуры может быть получено путем решения связанных уравнений Рейнольдса и уравнения энергии, как указано в уравнении (24). Это случай подшипника скольжения. Контакт поршневого кольца и гильзы цилиндра также является скользящим контактом, но с частым изменением направления захвата (Jang and Chang, 19).88).
Aenergy∂θ*∂x+Benergy∂θ*∂y=αdissipationη*h*2(Eenergy+Fenergy) (24)
Где
A=12-112(h*2η*∂P*∂x)
Или,
A=12-112(h*2e-θ*∂P*∂x) (25)
B=-112(h*2η*∂P*∂y)
Или,B= -112(h*2e-θ*∂P*∂y) (26)
E=∫01{1-12h*2η*∂P*∂x(1-2ψ)}2dψ где,ψ=Zh
Или,E=1+112h*4e-2θ*(∂P*∂x)2 (27)
F=∫01{1-12h*2η*∂P*∂x(1-2ψ)}n-1 {-12h*2η*∂P∂y(1-2ψ)}2dψ
Или,F=112(h*βe-θ*)2(∂P*∂y)2 (28)
Подставляя значения A, B, E, F выше уравнения (24), получаем *2e-θ*∂P*∂y)(∂θ*∂y)=αрассеивание-2θ*h*2{1+112h*4e-2θ*(∂P*∂x)2}+(αрассеивание-2θ* h*2)112(h*βe-θ*)2(∂P*∂y)2 (29)
Уравнение перестановки (29)
[12∂θ*∂x-eθ*{112h*2∂P *∂x∂θ*∂x+112β2h*2∂P*∂y∂θ*∂y}]=αрассеиваниеe-2θ*h*2+αрассеивание12h*2(∂P*∂x)2+αрассеивание12β2h*2(∂ P*∂y) 2 (30)
или,
αdissipationh*2 (1-2θ*)+(1+θ*) (112h*2∂p∂xac∂*∂x+112β2h*2? ∂y∂θ*∂y)=[12∂θ*∂x−{αрассеивание12h*2(∂P∂x)2+αрассеивание12β2h*2(∂P∂y)2}]
Следовательно,
θ*=[12∂θ*∂x*-{αdissipation12h*2(∂P*∂x*)2+αdissipation12h*2(∂P*∂y*)2}]-[{112h *2∂P*∂x*∂θ*∂x*+112h*2∂P*∂y*∂θ*∂y*}+αdissipationh*2][{112h*2∂P*∂x*∂θ* ∂x*+112h*2∂P*∂y*∂θ*∂y*}-2αdissipationh*2] (31)
Где коэффициент рассеивания тепла определяется как:
αdissipation=(2πN)η0βthermalρCp(Rh0 )2
N=13000 об/мин, ρ=881,46 кг/м3, Cp=1840 Дж/кг ◦C, η=0,00416 Па·с, βthermal=0,0315 ◦C-1, {θ*=βthermal(θ-θ0)}и{ h*=(h/h0)}
Наконец, T(y)=θ*βthermal+θ0.
Данные, взятые для расчета тепловыделения в режиме онлайн при условии работы двигателя гоночного автомобиля с использованием синтетического масла в качестве смазки (Mishra, 2012).
Граничное условие для расчета давления и температуры
Граничное условие входа масла изменяется при изменении направления движения поршня. При ходе вверх граничное условие входа масла устанавливается на верхнюю кромку кольца, а при ходе вниз — на нижнюю кромку. В положении на входе соединение считается полностью затопленным. При таком допущении скорость увлечения всегда положительна. Наклон кольца, как показано на рисунке 4, составляет <3°. Следовательно, эффект наклона на данном этапе в анализе не рассматривается.
Рисунок 4 . Граничные условия потока и давления масла для хода вверх и вниз.
Таким образом, p = p в при x = –b/2. Кольцо опирается на верхний пояс во время хода вверх (сжатие и выпуск). В то время как он опирается на дно во время хода вниз. Давление на входе соответствует давлению в камере сгорания при движении поршня вверх, тогда как при ходе поршня вниз оно равно первому межкольцевому давлению газа для поршневого узла с тремя кольцами. Для сборки поршня с одним кольцом это блок картера. Точка разрыва пленки на выходе применяется к граничному условию Свифта-Штибера как p = p c и dp/dx = 0 при x = x c . Где p c – давление кавитации в месте разрыва масляной пленки (см. рис. 4).
Температура масла на входе, рассчитанная по конвекции от твердой поверхности в объемную температуру масла. Повышение температуры поперек пленки происходит за счет теплопроводности и конвекции. По направлению уноса за счет фрикционного нагрева. Температура на входе из-за фрикционного нагрева является температурой окружающей среды на входе. Температура при h = 0 — это температура кольца или юбки. Аналогично при h = h max , температура это температура цилиндра.
Пошаговая итерационная процедура и соответствующие критерии сходимости по изотермическому давлению, температуре пленки, тепловому давлению и нагрузке на пленку задаются следующим образом:
)
Errorpth=∑im∑jn|PthK+1-PthK|∑im∑jnPthK≤0,001 (33)
Errorθ=∑im∑jn|θK+1-θK|∑im∑jnθK≤0,002 (03)
|Fap-WFap|≤0,001 (35)
, где F ap = F e + F г . Для удовлетворения этому критерию сходимости проводится соответствующая релаксация пленки:
h0(θ)k=h0(θ)k-1-{ϑ|Fap-WFap|} (36) предназначен для работы на высоких скоростях и высоких требованиях к крутящему моменту. В этих экстремальных условиях эксплуатации компоненты, изготовленные OEM-производителями, проверяются на долговечность. Двигатель гоночного автомобиля отличается от серийно используемых тем, что первый имеет ресурс менее 1500 км, а второй до капитального ремонта проходит более 200 000 км. Прочность на выносливость, стабильность смазки и т. д. проверяются с большей точностью в ходе гоночных испытаний. Поэтому мы моделируем наш результат, используя данные двигателя гоночного автомобиля.
Подтверждение результата
Важным параметром анализа является температура смазочной пленки в месте соединения кольцо-отверстие. Вычисленная температура должна быть подтверждена. Модель упрощена до однонаправленного скользящего контакта, чтобы подтвердить доступный результат Jang and Chang (1988) в литературе. Сравнительный график, представленный на рис. 5, показывает хорошее соответствие между смоделированными выходными данными и стандартными данными.
Рисунок 5 . Проверка температуры.
Исходные данные для применения в высокопроизводительном двигателе
Поршневое компрессионное кольцо с параболическим профилем торца используется с коэффициентом смещения 1,5 мкм. Кольцо имеет номинальный диаметр 82,2 мм и осевую ширину 2 мм. Он также имеет радиальную глубину кольца 3 мм. Свойства материала кольца, такие как модуль упругости, составляют 203 ГПа, а коэффициент Пуассона составляет 0,23. Двигатель, на который установлено это компрессионное кольцо, работает с рабочей скоростью 13 000 об/мин. В двигателе развивается максимальное давление сгорания 120 бар. Натяжение кольца за счет пружинящего действия наружу составляет 10 Н. Предполагается, что в двигателе используется смазка с вязкостью 0,004 Па·с при 100°С и индексом пьезовязкости 10 -8 Па -1 . Футеровка считается изотропной шероховатостью и имеет значение R k 0,49 мкм.
Обсуждение результатов
Тепловая модель контакта поршневого компрессионного кольца и цилиндра смоделирована для случая гоночного автомобиля. Разница между двигателем коммерческого или легкового автомобиля и двигателем гоночного автомобиля заключается в том, что предыдущий имеет срок службы до 100 000 миль, а более поздний — менее 1500 миль. Двигатели гоночных автомобилей рассчитаны на экстремальные условия эксплуатации, необходимые для победы в гонках, в то время как двигатели коммерческих автомобилей рассчитаны на долговечность и безопасность. Большинство OEM-производителей тестируют свои компоненты в условиях гонок, прежде чем задействовать оригинальное оборудование для использования в легковом или коммерческом автомобиле.
Прилегаемость , как обсуждалось ранее, определяется как способность гибкого кольца прилегать к поверхности отверстия во время установки и эксплуатации с минимальным зазором. Из-за неравномерной поперечной прочности материала и погрешности измерения степень прилегания в свободном состоянии иногда меняется и не обязательно согласуется с численным выводом (см. рис. 6). Давление продуктов сгорания в двигателе циклически изменяется и регулирует уплотняющее действие. Сгоревший газ поступает в заднюю часть кольца через отверстие и создает в кольце противодавление.
Рисунок 6 . Свободно согласующееся кольцевое отверстие.
При приложении давления газа установлено, что зазор несоответствующего кольца-канала уменьшается с увеличением значения давления газа (см. рис. 6). Во время цикла двигателя возникает такая проблема прилегания. Для этого анализа очевидно, что хотя соединение кольцо-вкладыш работает в гидродинамическом режиме большую часть цикла двигателя, шероховатость контакта из-за смешанного/граничного режима также имеет место в диапазоне углов поворота коленчатого вала 300–400° (Мишра, 2012).
При самом высоком давлении газа кольцо полностью прилегает, оставляя лишь зазор 10 мкм на малой дуге кольца, который находится в пределах зазора на свободном конце. Трехмерный профиль пленки, представленный на рисунках 7A-D, представляет собой всасывание, сжатие, мощность и выпуск соответственно. Это предполагает, что влияние давления газа преобладает при сжатии и рабочем такте. Следовательно, приведенный график сетки указывает на большее соответствие отверстия кольца, что приводит к более тонкой пленке (0,25 мкм) в сочетании с этими штрихами. В то время как в такте всасывания и такте выпуска в силе противодавления преобладает натяжение кольца с радиальной силой в кольце 10–12 кН. Это приводит к уменьшению соответствия диаметра кольца и увеличению толщины пленки (1,5–2,5 мкм).
Рисунок 7 . Трехмерная толщина пленки: (A) такт всасывания, (B) такт сжатия, (C) рабочий ход и (D) такт выпуска. (A) Ход всасывания (θ c = 90°, P com = 5 бар, η 0 = 0,004 Па.с, U = 25 м/с). (B) Сжатие (θ c = 250°, P com = 95 бар, η 0 = 0,004 Па. с, U = 20 м/с). (С) Мощность (θ c = 273°, P com = 120 бар, η 0 = 0,004 Па.с, U = 5 м/с). (D) Такт выпуска (θ c = 620°, P com = 5 бар, η 0 = 0,004 Па.с, U = 25 м/с).
Из-за увеличения аэродинамической конформности и уменьшения толщины пленки параметр масляной пленки Стрибека предполагает, что взаимодействие кончиков неровностей имеет большое значение при сжатии и рабочем такте. Это приводит к развитию контактного давления (см. рис. 8А,Б). Мишра и др. (2009) представили контактное давление и трение неровностей для изучения их вклада в общие потери на трение. В этом исследовании мы построили контур контактного давления неровности в положении кривошипа 305° (сжатие) и 373° (мощность), полученный в соответствии с уравнением (17) на рисунках 7A,B. Максимальное контактное давление шероховатостей в сетке возникает при 160° < θ c < 220° и 0,3 < b < 0,6 мм площади расположения с величиной 1,5–2,5 МПа.
Рисунок 8 . Контур шероховатости контактного давления в МПа при большей газовой нагрузке, для (А) такта сжатия (θ c = 250°, P com = 95 бар, η 0 = 0,004 Па.с, U = 20 м/с) и (B) рабочего хода (θ c = 273°, P com = 120 бар, η 0 = 0,004 Па.с, U = 5 м/с).
Контакт компрессионного кольца и гильзы цилиндра представляет собой контакт типа взаимодействия с текучей средой. Напряжение сдвига, возникающее в пленке из-за комбинированного действия вязкого действия и взаимодействия неровностей. В смешанном режиме такое напряжение сдвига определяется согласно (Патир и Ченг, 1979) и дается уравнением (20). Из-за появления геометрии шероховатости решение уравнения Рейнольдса среднего потока для напряжения сдвига содержит некоторые факторы течения. На рисунках 9A-D показан контур напряжения сдвига на пленке. В области кавитации такие напряжения сдвига в основном однородны.
Рисунок 9 . Контур изменения напряжения сдвига в пленке жидкости: (A) Такт всасывания, (B) Такт сжатия, (C) Рабочий ход и (D) такт выпуска. (A) Ход всасывания (θ c = 90°, P com = 5 бар, η 0 = 0,004 Па.с, U = 25 м/с). (B) Сжатие (θ c = 250°, P com = 95 бар, η 0 = 0,004 Па.с, U = 20 м/с). (C) Мощность (θ c = 273°, P com = 120 бар, η 0 = 0,004 Па.с, U = 5 м/с). (D) Такт выпуска (θ c = 90°, P com = 5 бар, η 0 = 0,004 Па·с, U = 25 м/с).
Температура пленки, указанная в уравнении (9), является функцией гидродинамического/эластогидродинамического давления. Кроме того, по мере изменения этого давления от одного положения кривошипа к другому изменяется и температура пленки. Изменение температуры масляной пленки в определенном месте коленчатого вала является трехмерным параметром. Для ясности распределение сечения и соответствующая толщина пленки нанесены как в осевом, так и в окружном направлении (см. рис. 10–13). В осевом направлении максимальное повышение температуры смазки происходит в месте минимальной толщины пленки. В окружном направлении минимальная толщина пленки возникает в месте минимальной радиальной деформации. Следовательно, прогнозируется, что повышение температуры смазки находится в обратной зависимости от общей деформации кольца (см. рис. 11А).
Рис. 10. (A) Пленка и изменение температуры в такте всасывания (θ c = 90°, P com = 5 бар, η 0 = 0,004 Па·с, U = 25 м/с). (B) Пленка и изменение температуры в такте сжатия (θ c = 250°, P com = 95 бар, η 0 = 0,004 Па·с, U = 20 м/с). (C) Пленка и изменение температуры в такте сжатия (θ c = 273°, P com = 120 бар, η 0 = 0,004 Па·с, U = 5 м/с). (D) Пленка и изменение температуры в такте сжатия (θ c = 620°, P com = 5 бар, η 0 = 0,004 Па·с, U = 25 м/с).
Рис. 11. (A) Изменение повышения температуры из-за радиальной деформации (θ c = 273°, P com = 120 бар, η 0 = 0,004 Па·с, U = 5 м/с). (B) Изменение повышения температуры в зависимости от типа масла (θ c = 273°, P com = 120 бар, η 0 = 0,004 Па·с, U = 5 м/с).
Большее радиальное отклонение означает меньшее соответствие кольцевому отверстию и меньшую минимальную толщину пленки. Минимальная толщина пленки наименьшая в положении, противоположном свободному концу. Повышение температуры из-за максимальной радиальной деформации на 45% меньше, чем из-за минимальной радиальной деформации.
Реакция смазочного материала на реологические изменения и его влияние на повышение температуры изучается путем моделирования нескольких масел класса SAE (см. рис. 11B). Вязкость смазочного материала считается ключевым параметром работы и изменяется из-за совместного влияния гидродинамического давления и температуры масляного слоя. Значительное изменение вязкости в таком случае происходит в такте сжатия и рабочем такте (см. рис. 12A–D).
Рисунок 12 . Контурное картирование изменения вязкости. (A) Всасывание, (B) сжатие, (C) мощность и (D) выпуск.
На рис. 13 представлены циклические изменения скорости (рис. 13А), давления смазки (рис. 13В) и вязкости (рис. 13С) в цикле двигателя. Вязкость показывает резко высокое значение в зоне высокого давления на сжатии и переходе рабочего такта. Хотя вязкость должна уменьшаться из-за повышения температуры, но одновременно происходит увеличение давления смазки. Чистый эффект приводит к увеличению вязкости.
Рисунок 13 . (A) Циклическое изменение скорости скольжения поршня в цикле двигателя. (B) Циклическое изменение давления смазочной пленки в цикле двигателя. (C) Циклическое изменение вязкости в цикле двигателя.
Смазочные явления в соединениях поршневых компрессионных колец и гильз цилиндров происходят из-за многих параметров. К ним относятся толщина пленки, скорость захвата, геометрия отверстия (микрогеометрия, такая как шероховатость поверхности, и макрогеометрия, такая как овальность отверстия), геометрия кольца, гидродинамическое давление, контактное давление шероховатости, реологические параметры смазки (температура, плотность, и вязкость) взаимозависимость таких параметров довольно сложна, некоторые параметры очень чувствительны к повышению температуры, такие как скорость скольжения и шероховатость отверстия. В то время как другие имеют незначительное или незначительное влияние на температуру пленки. Наиболее влиятельными параметрами являются скорость скольжения, давление газа. Конкретные значения этих параметров предназначены для конкретных мест расположения кривошипа, как показано на рисунках 8–13.
Заключение
Оценка повышения температуры смазки является первым этапом дальнейшего термического анализа любого соединения. Эта проверенная модель лучше всего исследуется для соединения вкладыша компрессионного кольца, включая глобальную деформацию кольца. Будущая работа по анализу трения может быть лучше объяснена за счет теплового воздействия на смазываемое соединение компрессионного кольца и контакта гильзы цилиндра. Краткое изложение результатов этого исследования:
• На повышение температуры в пленке влияет изменение скорости скольжения, а также изменение давления газа в камере сгорания. Замечено, что максимальное повышение температуры составляет 120°C при положении кривошипа 273°, что находится в области рабочего хода.
• Между максимальной и минимальной радиальной деформацией кольца, деформированного по окружности, существует температура около 30°C.
• Расчетная разница составляет 10°C из-за использования масла SAE15 и SAE50W, где в последнем случае повышение температуры будет больше.
• Из-за комбинированного воздействия гидродинамического давления и повышения температуры вязкость продолжает расти и в четыре-пять раз превышает эталонное значение.
Температура и теплопередача поршневой подсистемы и гильзы цилиндра представляет собой очень сложное явление в переходном состоянии. Это связано со сложным температурным граничным условием и изменением материала компонентов. Например, головка поршня находится в стороне от камеры сгорания (650°C), а нижняя часть обращена к картеру (100°C). Кроме того, материал поршня — алюминиевый сплав, а материал гильзы цилиндра — сталь. Такое быстро меняющееся граничное условие, если оно будет реализовано, улучшит текущую модель до значительного уровня.
Заявление о доступности данных
Наборы данных, созданные для этого исследования, доступны по запросу соответствующему автору.
Вклад авторов
PM смоделировал программу, написал статью и сообщил о ней как один автор.
Конфликт интересов
Автор заявляет, что исследование проводилось в отсутствие каких-либо коммерческих или финансовых отношений, которые могли бы быть истолкованы как потенциальный конфликт интересов.
Дополнительный материал
Дополнительный материал к этой статье можно найти в Интернете по адресу: https://www.frontiersin.org/articles/10.3389/fmech.2019.00068/full#supplementary-material
Ссылки
Abe, S., и Судзуки, М. (1995). Анализ деформации отверстия цилиндра при работе двигателя. SAE Technical Paper 950541. doi: 10.4271/950541
CrossRef Полный текст | Google Scholar
Акалин О. и Ньюаз Г.М. (2001б). Моделирование трения поршневых колец в цилиндре в смешанном режиме смазки: Часть. II-Корреляция между данными стендовых испытаний. ASME Дж. Трибол. 123, 219–223. doi: 10.1115/1.1286338
CrossRef Полный текст | Google Scholar
Акалин О. и Ньюаз Г. М. (2001a). Моделирование трения поршневых колец в цилиндре в смешанном режиме смазки: Часть. I-аналитические результаты. ASME Дж. Трибол. 123, 211–218. doi: 10.1115/1.1286337
Полный текст CrossRef | Google Scholar
Асауляк А. А., Рождественский Ю. В., Гаврилов К. В. (2016). Упругогидродинамическая смазка (ЭГС) поршневых колец в двигателе внутреннего сгорания. Elsevier Proc. англ. 150, 536–540. doi: 10.1016/j.proeng.2016.07.037
CrossRef Full Text | Google Scholar
Бейкер К.Э., Ранеджат Х., Рахмани Р. и Феодоссиадес С. (2011). Аналитическая оценка модального поведения поршневого компрессионного кольца и оценка трения . SAE International, Документ SAE № 2011-01-1535. doi: 10.4271/2011-01-1535
CrossRef Полный текст | Google Scholar
Балакришнан С. и Ранеджат Х. (2005). Изотермический переходный анализ контакта юбки поршня со стенкой цилиндра при комбинированном аксиально-боковом наклонном движении. J. Phys. заявл. физ. Д заявл. физ. 38, 787–799. doi: 10.1088/0022-3727/38/5/018
CrossRef Full Text | Google Scholar
Боландер, Н.В., Стинвик, Б.Д., Садеги, Ф., и Гербер, Г.Р. (2005). Переходы режима смазки на границе поршневого кольца и гильзы цилиндра. Проц. ИМех. Деталь J J. Tribol . 129, 19–31. doi: 10.1243/135065005X9664
Полный текст CrossRef | Google Scholar
Доусон Д. и Хиггинсон Г. Р. (1959). Численное решение упругогидродинамической задачи. Дж. Мех. англ. науч. 10, 6–15. doi: 10.1243/JMES_JOUR_1959_001_004_02
CrossRef Полный текст | Google Scholar
Доусон Д., Радди Б. Л. и Эконому П. Н. (1983). Эластогидродинамическая смазка поршневых колец. Проц. Р. Соц. 386, 409–430. doi: 10.1098/rspa.1983.0043
Полный текст CrossRef | Google Scholar
Финол, К.А., Паркер, Д.А., и Робинсон, К. (2009). Модель из первых принципов радиального теплового потока в канале цилиндра современного дизельного двигателя. Дж. Терм. науч. англ. заявл. 1:031003. doi: 10.1115/1.4000583
Полный текст CrossRef | Google Scholar
Фурухама С. и Сасаки С. (1983). Новое устройство для измерения сил трения поршней в малых двигателях. Технический документ SAE 831284. doi: 10. 4271/831284
CrossRef Полный текст | Google Scholar
Гринвуд, Дж. А., и Трипп, Дж. Х. (1970). Контакт номинально плоских поверхностей. Проц. Инст. мех. Eng . 185, 625–633. дои: 10.1243/PIME_PROC_1970_185_069_02
Полнотекстовая перекрестная ссылка | Google Scholar
Харигая Ю., Судзуки М. и Такигучи М. (2003). Анализ толщины масляной пленки на поршневых кольцах дизеля: влияние температуры масляной пленки. ASME J. Eng. Газовые турбины Power 125, 596–603. doi: 10.1115/1.1501078
Полный текст CrossRef | Google Scholar
Хилл С. Х. и Ньюман Б. А. (1984). Конструкции поршневых колец для уменьшения трения . Технический документ SAE, 841222. doi: 10.4271/841222
Полнотекстовая перекрестная ссылка | Google Scholar
Хуперт, Л. (1985). Новые результаты расчета силы тяги в упругогидродинамических контактах. Пер. ASME F J. Tribol. 107, 241–245. doi: 10.1115/1.3261033
Полный текст CrossRef | Google Scholar
Ху Ю. , Ченг Х. С., Араи Т., Кобаяши Ю. и Айома С. (1994). Численное моделирование поршневого кольца в неосесимметричном анализе смешанной смазки. ASME Дж. Трибол . 116, 470–478. дои: 10.1115/1.2928867
Полнотекстовая перекрестная ссылка | Google Scholar
Jang, JY, and Chang, CC (1988). Адиабатический анализ подшипника скольжения конечной ширины с неньютоновской смазкой. Одежда Elsevier 122, 63–75. doi: 10.1016/0043-1648(88)
-5CrossRef Full Text | Google Scholar
Ма, М.-Т., Смит, С., и Шеррингтон, И. (1995). Трехмерный анализ смазки поршневых колец, часть 2: чувствительный анализ. Проц. IMechE Part J J. Eng. Трибол. 209, 15–27. doi: 10.1243/PIME_PROC_1995_209_402_02
Полный текст CrossRef | Google Scholar
Ма, М.-Т., Смит, С., и Шеррингтон, И. (1996). Реализация алгоритма моделирования недостаточной смазки поршневого кольца в искривленном отверстии: прогноз потока масла и начала продувки газом. Проц. IMechE Part J J. Eng. Трибол. 210, 29–44. doi: 10.1243/PIME_PROC_1996_210_475_02
Полный текст CrossRef | Google Scholar
Ма, З., Хенейн, Н. А., и Брайзик, В. (2006). Модель износа и трения гильз цилиндров и поршневых колец. СТЛЭ Трибол. Транс. 49, 315–327. doi: 10.1080/056981678630
CrossRef Full Text | Google Scholar
Мишра, П. К. (2012). Трибодинамическое моделирование сопряжения поршневого компрессионного кольца и гильзы цилиндра в зоне высокого давления цикла двигателя. Междунар. Дж. Адв. Произв. Технол. 66, 1075–1085. doi: 10.1007/s00170-012-4390-y
CrossRef Full Text | Google Scholar
Мишра, П. К. (2013). Моделирование трения четырехтактного четырехцилиндрового бензинового двигателя. Трибол. Инд. 35, 237–245.
Google Scholar
Мишра П. К., Балакришнан С. и Ранеджат Х. (2008). Трибология контакта компрессионного кольца с цилиндром при реверсировании. Proc Instn Mech Eng. Часть J. Eng . Трибол. 222, 815–826. doi: 10.1243/13506501JET410
Полный текст CrossRef | Google Scholar
Мишра, П. К., Ранеджат, Х., и Кинг, П. Д. (2009). Трибология сопряжения кольцо–отверстие при смешанном режиме смазки. Проц. Инст. мех. англ. Часть C J. Mech. англ. науч. 223, 987–998. doi: 10.1243/09544062JMES1220
Полный текст CrossRef | Google Scholar
Мохамед, Э. С. (2018). Анализ работоспособности и контроль состояния поршневых колец ДВС по характеристикам горения и тепловым характеристикам. Заяв. Терм. англ. 132, 824–840. doi: 10.1016/j.applthermaleng.2017.12.111
CrossRef Полный текст | Google Scholar
Моррис Н., Рахмани Р., Ранеджат Х., Кинг П. Д. и Фицсимонс Б. (2013). Трибология сопряжения поршневых компрессионных колец при переходном термическом смешанном режиме смазки. Трибол. Междунар. 59, 248–258. doi: 10.1016/j.triboint.2012.09.002
CrossRef Полный текст | Google Scholar
Муфтий Р. А. и Прист М. (2005). Экспериментальная оценка трения поршня в сборе в бензиновом двигателе в условиях работы двигателя и пламени. Пер. ASME 127, 826–836. doi: 10.1115/1.1924459
Полный текст CrossRef | Google Scholar
Oh, K.P., Li, CH, and Goenka, P.K. (1987). Эластогидродинамическая смазка юбок поршня. Пер. ASME Дж. Трибол. 109, 357–361. doi: 10.1115/1.3261366
Полный текст CrossRef | Google Scholar
Окамото М. и Сакаи И. (2001). Распределение контактного давления поршневых колец — расчет на основе контура поршневого кольца. Технический документ SAE 2001-01-0571. doi: 10.4271/2001-01-0571
CrossRef Полный текст | Google Scholar
Патир Н. и Ченг Х. С. (1978). Модель среднего потока для определения влияния трехмерной шероховатости на частичную гидродинамическую смазку. ASME Дж. Трибол. 100, 13–17. doi: 10.1115/1.3453103
Полный текст CrossRef | Google Scholar
Патир Н. и Ченг Х. С. (1979). Применение модели среднего потока к смазке между шероховатыми поверхностями скольжения. ASME Дж. Трибол. 101, 221–230. doi: 10.1115/1.3453329
Полный текст CrossRef | Google Scholar
Пэн, Э., и Хуанг, С. (2017). Износоустойчивость текстуры поверхности гильзы цилиндра на узле гильза цилиндра-поршневое кольцо. IMechE J. 232, 291–306. doi: 10.1177/2F1350650117713435
CrossRef Full Text | Google Scholar
Рахмани Р., Теодоссиадес С., Ранеджат Х. и Фитцсимонс Б. (2012). Переходная упругогидродинамическая смазка шероховатого нового или изношенного поршневого компрессионного кольца в сочетании с некруглым отверстием цилиндра. Проц. IMechE Part J J. Eng. Трибол. 226, 284–305. doi: 10.1177/1350650111431028
CrossRef Full Text | Google Scholar
Шахмохамади Х., Рахмани Р., Ранеджат Х., Гарнер С.П. и Кинг П.Д. (2013). Термосмешанная гидродинамика соединения поршневых компрессионных колец. Трибол. лат. 51, 323–340. doi: 10.1007/s11249-013-0163-5
CrossRef Full Text | Google Scholar
Шимада А. , Харигая Ю., Судзуки М. и Такигучи М. (2004). Анализ температуры масляной пленки, толщины масляной пленки и теплообмена на поршневом кольце двигателя внутреннего сгорания: влияние локальной вязкости смазки. Дж. Инж. 113, 1790–1798. Доступно в Интернете по адресу: https://www.jstor.org/stable/44723636
Google Scholar
Söderfjäll, M., Herbst, H.M., Larsson, R., and Almqvist, A. (2017). Влияние на трение конструкции поршневых колец, шероховатости гильзы цилиндра и свойств смазки. Трибол. Междунар. 116, 272–284. doi: 10.1016/j.triboint.2017.07.015
CrossRef Полный текст | Google Scholar
Спенсер А., Альмквист А. и Ларссон Р. (2011). Численная модель для исследования влияния угла хонингования на гидродинамическую смазку между поршневым кольцом двигателя внутреннего сгорания и гильзой цилиндра. Проц. IMechE Part J J. Eng. Трибол. 225, 683–689. doi: 10.1177/1350650111403867
CrossRef Full Text | Google Scholar
Сан, округ Колумбия (1991).