Правильная раскоксовка двигателя, средства, способы, хитрости.
Всем привет. Тема сегодняшней статьи – правильная раскоксовка двигателя. В статье рассмотрены популярные способы раскоксовки и анализируется эффективность каждого из них.
Немного теории.
В двигателях внутреннего сгорания на поршне устанавливаются 3 кольца – 2 компрессионных (именно они обеспечивают сжатие смеси в цилиндре) и одно маслосъемное. При работе двигателя в процессе сгорания топлива на поверхностях поршня и камеры сгорания откладывается нагар. Особенно интенсивно это происходит зимой и при городском цикле движения.
Часть этого нагара неизбежно попадает на поверхность колец и забивает их. Соответственно кольца становятся менее подвижными и лучше пропускают смесь в картер. Как итог мощность двигателя падает, расход топлива растет, а масло быстрее темнеет, все это следствие снижения компрессии….
Раскоксовка – удаление нагара с поверхностей компрессионных и маслосъемных колец…. 3 смеси керосина (80%) и моторного масла (20%), или ацетон (30%), керосин 30%, бензин (30%), масло моторное (10%).
После этого прокручиваем двигатель туда сюда несколько раз (на старых автомобилях это было несколько проще, но и современный двигатель можно, без свечей зажигания, провернуть руками, например, за шкив или за ремень генератора).
Оставляем автомобиль на ночь.
Утром заворачиваем свечи, запускаем двигатель и даем ему поработать на холостом ходу порядка 10ти минут.
После этого меняем масло и эксплуатируем автомобиль в обычном режиме.
Масло менять обязательно, так как керосин и ацетон агрессивны маслу, и оно потеряет свои свойства. Соответственно эту раскоксовку лучше делать перед сменой масла, чтобы не переплачивать за его замену.
Раскоксовка двигателя гидроперитом.
Это сегодня классика жанра, на 5 литров воды разводят шесть таблеток перекиси водорода (гидроперита) и проливают это дело через двигатель. Делается это примерно так:
Не принципиально карбюратор или инжектор…. Главное не перелить воду и не словить гидроудар.
На самом деле гидроперит тут не сильно и нужен, разницы между раскоксовкой водой и раскоксовкой перекисью водорода я не заметил. Огромным плюсом этого метода является то, что водяной пар отмоет нагар и с клапанов и со стенок камеры сгорания и с днища поршня и с колец. Так же если двигатель не сильно изношен то не так много воды попадет в масло и сооответсвенно можно обойтись без его замены (понятно будет после суток езды – если под крышкой маслоналивной горловины не появилась эмульсия, то можно не менять масло).
Раскококсовку этим методом следует делать очень аккуратно, так как при ошибке велик риск словить гидроудар и испортить двигатель.
Достижения современной химии – средство LAVR.
Раскоксовка лавром во многом аналогична дедовскому методу, но химия в его составе несколько иная, поэтому и раскоксовывают им несколько иначе. 3 моторного масла.
Самая правильная раскоксовка двигателя.
Уважаемые читатели я думаю всем очевидно, что любая химия не сможет убрать нагар полностью!
Полностью удалить нагар, и раскоксовать залегшие кольца, можно только разобрав двигатель и вынув поршни.
Когда двигатель разобран нагар с каналов колец и поверхностей поршней отлично убирается 646 растворителем или, по старому дедовскому рецепту, все с чего требуется отмыть нагар, замачивается в керосине и шаркается щетками.
Очевидно, что метод раскоксовки связанный с разборкой двигателя даст самый качественный и гарантированный результат, но это очень дорого и соответственно сегодня так никто не поступает!
Разбирают двигатель только для текущего или капитального ремонта!
С уважением, администратор life-with-cars. ru
Какие расходники и средства нужны для раскоксовки двигателя
При работе мотора смазочные материалы подвергаются воздействию высоких температур. Следствие локальных перегревов — образование относительно твердых лаков и смол. Их невозможно удалить при помощи штатных моющих присадок, которые входят в состав любого масла. Какое средство лучше для раскоксовки двигателя, поможет понять анализ эффективности. Мы провели его по результатам практики освобождения колец от неподвижности.
Содержание
- Зачем мотору нужна глубокая очистка
- Раскоксовка двигателя своими руками: расходники
- Рейтинг средств для раскоксовки двигателя
Зачем мотору нужна глубокая очистка
Любой двигатель со временем загрязняется изнутри. Многим известна промывка мотора с помощью масляных присадок или специализированных моющих составов. Но до поршневых колец, клапанов и впускных каналов эти средства не добираются.
Характерные симптомы залегающих поршневых колец:
- снижение мощности;
- увеличенный расход масла на угар;
- плохой запуск холодного двигателя;
- потеря компрессии в отдельных цилиндрах;
- дымный выхлоп сизого цвета в режиме постоянного оборота.
Рост угара масла приводит к зарастанию каналов в головке блока. На запущенных стадиях создаются препятствия для нормального газообмена — отдача мотора заметно падает. Параллельно ухудшается тепловой режим отдельных деталей и движка в целом. Для решения проблемы потребуется генеральная уборка.
Оптимальное решение — совместить промывку мотора со стороны системы смазки и раскокосовывание цилиндров.
Можно подобрать два состава от одного производителя, которые очистят низ двигателя и верх за одну процедуру замены масла.
Раскоксовка двигателя своими руками: расходники
Процедура очистки не представляет сложности, поэтому ее можно провести в своем гараже. При этом разборка мотора не потребуется — достаточно будет снять впускной коллектор.
Заранее приобретите набор прокладок, свежее масло, фильтр. В интернет-магазине TopDetal.ru можно купить средства для раскоксовки двигателя по выгодным ценам и с быстрой доставкой.
Все манипуляции лучше проводить на слегка прогретом моторе. Необходимо строго соблюдать порядок действий:
- Расстыковывается воздушная магистраль и снимается впускной коллектор.
- Выкручиваются свечи зажигания.
- Поршни устанавливаются в среднее положение поворотом коленчатого вала.
- Пенный состав через трубку наносится во впускные каналы и на клапаны, а также в цилиндры через свечные отверстия.
- Незначительными поворотами коленвала создаются условия для попадания пены на все детали поршневой группы.
- Отработанное средство удаляется при помощи шприца с гибкой насадкой.
- Процедура повторяется несколько раз для более качественного результата.
При удалении отложений этот способ позволяет визуально контролировать прогресс.
Перед запуском двигателя можно добавить одну из моющих присадок и промыть систему смазки.
Рейтинг средств для раскоксовки двигателя
На многочисленных форумах в теме «Раскоксовка двигателя» чаще всего звучит вопрос — чем лучше раскоксовать? Многие автовладельцы, прежде всего, рекомендуют мастер-пену «ВАЛЕРА». Инновационный химический состав возвел продукт в число лучших средств для раскоксовки колец бензинового двигателя. По отзывам покупателей, средство удобно в применении, заполняет весь объем узлов, устойчиво держится в каналах и камере сгорания. В отличие от зарубежных аналогов, практически не оседает.
На вопрос, чем лучше делать раскоксовку дизельного двигателя, бывалые мастера также рекомендуют продукцию ВМП-АВТО. Специфика таких моторов вносит свои особенности. Приходится снимать топливные форсунки или свечи накаливания, что в домашних условиях нелегко. Пенный аэрозоль «Валера» оснащен длинной трубкой, которая позволяет добраться до труднодоступных мест. Состав подходит для очистки клапана EGR и турбокомпрессора.
Эффективным средством для раскоксовки дизельного двигателя называют также декокер FENOM. Он предназначен для очистки поршневых колес. Способствует увеличению мощности мотора, снижает расход масла, эффективно удаляет углеродистые отложения.
Вывод: регулярная чистка двигателя автомобиля и профилактика отложений позволит избежать крупного ремонта.
Как сделать поршневые кольца
Введение
Изготовление компрессионных колец для поршней — тема, которая очаровывает и озадачивает производителей моделей двигателей, пока они не делают это впервые. Способов, которыми это может быть достигнуто, множество, и неудивительно, что обсуждение различных методов часто производит больше тепла, чем работающий двигатель! Довольно поверхностное рассмотрение этой темы появилось в октябрьском техническом совете 2004 г., и, хотя с тех пор технически мало что изменилось, было написано больше слов и изображений, поэтому эта страница действует в основном как страница с кратким изложением и ссылкой на другой материал.
Требуется изготовить кольцо некруглой формы, которое при вдавливании в отверстие цилиндра становится точно круглым, оказывая равномерное радиальное давление на стенки цилиндра. Этого давления должно быть достаточно, чтобы обеспечить достаточную компрессию для запуска и не более того. После запуска давление газа за кольцом прижимает его к цилиндру, повышая эффективность сжатия. Ширину и толщину следует выбирать таким образом, чтобы кольцо не только соответствовало этому критерию, но и могло быть установлено без опасности его поломки или необратимой деформации при раскрытии.
Материалы
Хотя бронзовые кольца известны, особенно в мире острого пара, поршневые кольца для двигателей внутреннего сгорания обычно изготавливаются из мелкозернистого чугуна. Требуемые характеристики могут быть достигнуты как с термообработкой, так и без нее, хотя большинство инженеров-моделей, похоже, предпочитают подход с термообработкой. И в то время как на предмете, забудьте любое предложение об использовании «весов створки» как материальный источник. Во-первых, этот материал — чистый хлам, а во-вторых, у кого еще есть створки? Возьмите несколько стержней из мелкозернистого чугуна — отлитых по центру или пултрузионных. SG или «Meehanite» еще лучше, но они должны иметь мелкий, равномерный размер зерна.
Термообработка формования
Эти страницы содержат два подробных описания применения того, что стало известно как метод Trimble [1], названный в честь человека, который его формализовал, покойного Джорджа Тримбла. Есть те, кто клянется в этом, на самом деле Боб Уошберн, бывший редактор/издатель журнала SIC, где этот подход был сериализован, сказал, что любой, кто делает кольцо любым другим методом, тратит свое время впустую.
Фини
Циррус
Этот подход может многим понравиться, но я считаю, что утверждение о том, что он будет производить *идеальные* кольца, не требующие приработки, просто неверно! Чугун, нагретый выше критической температуры, как описывает Trimble, будет расти. Так что, если кольцо подходило к отверстию раньше, оно не подходит потом. Чтобы кольцо поместилось в отверстии, зазор должен быть немного открыт, после чего закрытое кольцо больше не будет идеально круглым. Разница небольшая, но измеримая. Мой опыт показывает, что на кольце диаметром 0,625 дюйма можно ожидать роста до 0,0015 дюйма.
Этого можно было бы избежать. Как упоминалось на страницах выше, другие авторы отмечают, что более длительное нагревание до точки ниже критической температуры приводит к затвердеванию без снижения твердости, не образует «накипь» и не увеличивает материал. Но для этого требуется печь с регулируемой температурой, которой у большинства из нас нет.
Несколько иной подход к отожженным кольцам описал покойный профессор Деннис Чеддок, написав о конструкции четырехтактного двигателя в уважаемом британском журнале 9.0015 Model Engineer [2] (не следует забывать, что до того, как он появился в SIC, Trimble также опубликовал свой метод в этом журнале [3]). В подходе профессора изготавливаются кольцевые заготовки размером в несколько тысяч больше. После «замораживания» зазора с помощью тепла кольца сжимаются и зажимаются, как показано на рис. (d), для доводки до фактического отверстия. Этот вариант удаляет любую накипь, образовавшуюся на периферии во время термообработки, а также любой «рост» в чугуне, возникающий в результате отсутствия контроля температуры и последующего прохождения через критическую температуру.
Брайан Винч, пишущий как Airborne Engin-ear (sic) в австралийском журнале Airborne , выступал за привязывание кольца к стальной пластине толщиной 3 мм тонкой проволокой, а также с помощью прямоугольного кляпа. Затем пластину довели до красного каления, прикладывая тепло к другой стороне, позволяя кольцу поглощать тепло за счет теплопроводности. Этот подход позволяет избежать опасности того, что прямое приложение тепла может вызвать локальную горячую точку, что приведет к тому, что кольцо «поддастся» в этой точке, что приведет к образованию зазора, который выглядит правильно, но кольцо, которое не сомкнется обратно до круглого. Затем светящуюся тарелку бесцеремонно бросили в удобную бочку с отработанным отстойным маслом. Я бы поставил Винчи именную галочку, если бы он не испортил ее, упомянув эти ужасные веса створки в начале статьи … [4]
Наконец, Лес Стоун объяснил метод, который он использует, который первоначально появился в Машинист Домашнего Магазина . Заготовки для колец изготавливаются по внутреннему и внешнему диаметру, а затем разрезаются на гвозди большого пальца. Они расклиниваются до необходимого свободного зазора небольшим стальным бруском. Этот блок с кольцом, свисающим снизу, держится перед огнеупорным кирпичом. Затем тепло от газового топора направляется на кольцо и кирпич, от которых пламя отскакивает назад, обеспечивая достаточно равномерное распределение тепла, при условии, что вы поддерживаете движение пламени. Когда кольцо принимает комплект, оно отваливается от затычки и отжиг готов! Теперь, прежде чем вы вызовете забавный фермерский фургон, посмотрите на количество работающих многоцилиндровых кольцевых двигателей, которые Лес сделал, используя этот подход. Как ни грубо, с успехом трудно поспорить. Ни слова о весе створки.
Холодная штамповка
В этом методе используется заготовка большего диаметра и меньшего размера отверстия. Кольца нарезаются по ширине, вырезается необходимый зазор и подпиливается в заготовке.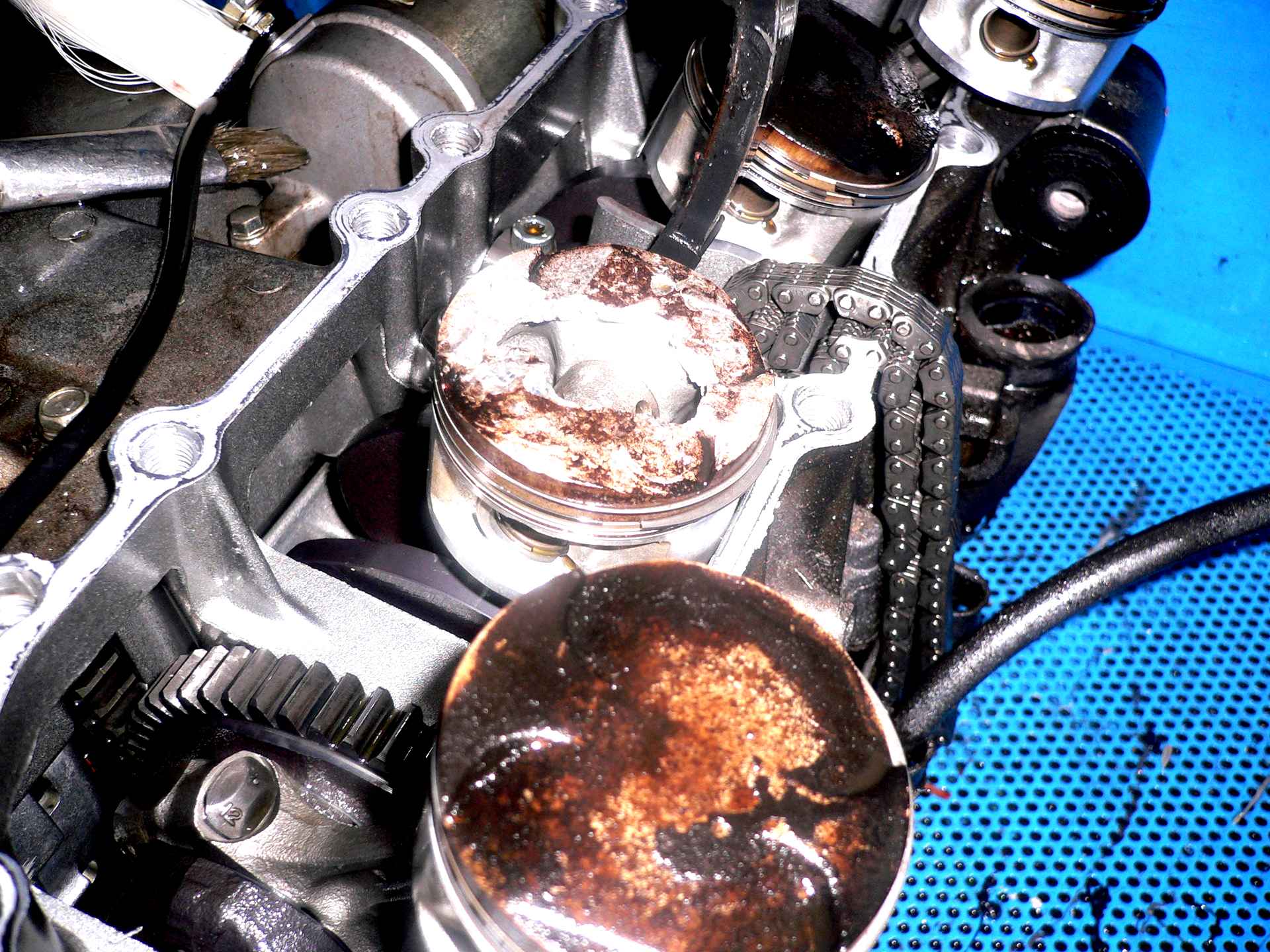
Еще один способ холодной штамповки, который, по-видимому, сработал для дизайнера, был описан в Техническом совете за октябрь 2004 года. Этот метод восходит к Model Maker от апреля 1960 года, и, несмотря на дату публикации, я полагаю, это не шутка! Как видно здесь, точеное и разрезное кольцо деформируется давлением прокатки до тех пор, пока не будет достигнут требуемый зазор. Щелкните ссылку для фактических слов, которые сопровождали иллюстрацию.
Выводы
Говорят, что изготовление хорошего поршневого кольца — это искусство, а изготовление действительно хорошего поршневого кольца — искусство! Я согласен. Сделать кольцо, которое выполняет эту работу, несложно. После этого вы захотите улучшить свой подход и сделать кольца, которые требуют меньше обкатки, производят меньше дыма и требуют меньше усилий. В этом обсуждении мы проигнорировали маслосъемные кольца и специальные типы колец, такие как 9.Кольцо 0015 Дайкс . Но как только базовые навыки будут освоены, они также должны быть в пределах навыков и оборудования среднего инженера по моделированию.
Ссылки
Изготовление поршневых колец для газовых двигателей
Статья Мика Коллинза:
Ниже приводится введение в предложен метод изготовления малых поршневых колец, основанный на статьях Проф. Чеддок и Том Уолшоу (Тубал Каин), но я должен признать, что Я еще НЕ пробовал окончательную операцию обработки.
В этих пояснительных примечаниях
будут использоваться следующие сокращения: D = диаметр цилиндра. т = радиальный
толщина кольца.
w = осевая ширина кольца. p = давление на стенку. Fdd = усилие, необходимое для
замкнутое кольцо, нанесенное под углом 90 градусов к зазору, и
» » = фактические цитаты из статей.
В статье в Model Engineer (21.04.67 стр. 396) Профессор Чеддок описывает эффективную 5cc Four Ход двигателя I / C, построенный для попытки установить рекорд продолжительности полета модели самолета, и он подробно описывает свой метод изготовления поршневых колец с помощью «теплообразование».
«Кольца точены на диаметр D+0,002» и
толщина не более 1/25 или менее 1/30 диаметра отверстия.
Современная тенденция состоит в том, чтобы сделать ширину равной или даже меньше
их толщины, поэтому то же правило можно применить и к ширине. Кольцо
теперь необходимо разрезать как можно более тонкой пилой или (предпочтительный метод)
ломается, удерживая его пальцами и щелкая им. Крошечный кусок кляпа,
шириной t x 4, теперь вставляется в зазор, чтобы расширить кольцо
прежде чем зажать его, с несколькими другими, если требуется, между двумя
металлические пластины центральным болтом и нагрев всей сборки до
температуры отжига в газовом пламени или муфеле».
Профессор Чеддок не указывает требуемую температуру, но говорит что практический тест состоит в том, что если после охлаждения кольцо пружинит внутрь от зазора t x 4, то он не полностью снимает напряжение и процесс должен быть повторен. (но см. позже) Он говорит: «Завершение колец после того, как они были «нагреты» сформированы» могут следовать общепринятой практике, то есть они могут быть замкнуты в трубку и зажаты между пластинами оправки —— для отделка периферии и боковых сторон притертой от руки на камне или наждачная бумага. Очень мало, одну или две нужно только снять в этих последних операциях, чтобы довести их до размеров. — они держат компрессия такая же или лучше, чем у шлифованного и притертого поршня и цилиндр.»
Он не упоминает о необходимости «рабочего» зазора и кольцах, которые он
на самом деле изготовлены были 0,025 «x 0,025″ поперечного сечения, чтобы соответствовать
отверстие 18 мм (0,709»).
Эссе Тома Уолшоу (Тубал Каин) в журнале SMEE (декабрь 1992 г.) в основном занимается проектированием кольца с правильным давлением стенки для их конкретных приложение, и он ссылается на статью Майкла Смарта (M.E. 8.16.1974 стр.824), в которой объясняется, как правильно подогнанное кольцо расширяется за счет давления позади него, чтобы увеличить первоначальную стену давление.
Выводы Тома заключаются в том, что большинство моделей двигателей были работает с чрезмерным давлением на стену, и он включил таблицу давления на стенки, которые он измерил на ряде серийно выпускаемых «модельные» кольца.
Затем он описывает простой метод
измеряя его, сжимая кольцо до его диаметра отверстия с усилием,
Fdd, приложенный в диаметрально противоположных точках, 90 градусов от
зазор. Затем: —
р = (Fдд х 0,881)/(ш х Г)
Выражение для вычисления p
определяется как: —
p = g x E/7,06 x D x (D/t — 1) в кубе
Где g = разница между свободным и закрытым зазорами, дюймы. и Е =
Модуль Юнга, фунт-сила/кв. дюйм.
«Значения E могут варьироваться от 12
миллионов до 24 миллионов фунтов на квадратный дюйм. и ссылка на поставщика
желательно. Цифра
18 млн характерна для 20-22-тонных УТС, а между 15 и 17
миллионов для 17-тонного UTS из центробежного чугуна обычно
доступны для самодельных колец.»
«Чтобы завершить это исследование
арифметически, напряжение в кольце можно рассчитать в
обычный способ от изгибающего момента — — — — — и упрощенный до:-
f = 3 x p x (D/t)квадратный фунт-сила/кв. дюйм»
После долгого рассуждения о модели Практика поршневых колец, в которой Том использует каждую статью, которую только может найти в модельной инженерной прессе он обсуждает критерии для дизайн и приходит к следующим выводам:-
«Давление на стенку для моделей (а)
Паровой завод. Понятно, что пристеночные давления, используемые в наших моделях
выше, чем нужно, даже у простого типа Рамсботтома; все еще
тем более с современными термоформованными кольцами. Для стационарных, морских и
двигатели дорожных локомотивов, каждый из которых может быть приведен в действие для начального
постельных принадлежностей, 6-8 фунтов/кв. дюйм. должно быть адекватным. Однако есть
небольшая проблема; радиальная толщина настолько мала с
«классические» зазоры, которые могут быть затруднены при отрезке.* Для
по этой причине я установил минимальное значение «t» на уровне 0,035″,
и используйте меньший зазор, когда это необходимо. Фиксация на g = D/10 вместо
4 x t упрощает формулу давления до:-
D/t = кубический корень из E/(70,6 x p) + 1
, но это соотношение не следует использовать для
давление на стенку выше примерно 12 фунтов силы/кв. дюйм. без проверки
«подходящий» стресс. (см. далее)
Для железнодорожных локомотивов целесообразно использовать немного более высокое давление. Нижний предел «стандарта чаддока» обеспечивает около 13 фунт-сила/кв. дюйм с «Е» на 17 миллионов. (т.е. D/t = 30 и g = 4 x t), но это будет меняться пропорционально значению Е».0005
*Это не так — см. метод.
«(b) Двигатели внутреннего сгорания. Для классическая модель горизонтального газо-бензинового двигателя, которую я заменил кольца на 6 1/2 lbf/sq.in. без проблем, но где конструктор призвал два кольца я использовал три. Это давление лежит вне «стандарта Чаддока» (t = D/33-35), так что, снова используются кольцевые зазоры D / 10. Во многих опубликованных проектах используются кольца. которые слишком широки, и я предлагаю w = 0,03 x B в качестве ориентира с минимум 0,04 дюйма
Для всех остальных I. C. двигатели это нет
с удивлением обнаружив, что соблюдение правил проф. Чеддока даст
удовлетворение, хотя на верхнем уровне (D/25) важно проверить
напряжения, так как напряжения выше, чем обычно доступные 17
тонн железа может нести.
Для тех, кто не знаком с данными правилами, цифры являются: —
Радиальная толщина, t = от D/25 до D/30; кольцевой зазор, g = 4 x t.
Если «E» равно 17 миллионам фунтов силы/кв. дюйм. эти правила предлагают давление на стенку от 28 до 13 lbf/sq.in. давление на стенку будет, конечно, изменяться в зависимости от значения Е в прямом пропорция. Чем ниже давление стенки, тем меньше трение. курс!
Для очень мощных двигателей
само собой разумеется, что эксперимент всегда необходим, и
хотя это может увеличить время и стоимость одноцилиндрового двигателя
прототип, приспособленный для измерения как расхода масла, так и прорыва картерных газов
(а также производительность и расход топлива) стоит того. Даже
здесь я не ожидал бы найти больше, чем около 25 фунтов силы/кв. дюйм. быть
необходимо, и только тогда, когда одно прижимное кольцо поддерживается
ступенчатый скребок между верхним кольцом и основным масляным
контроллер.»
«Фитинг с кольцом
(a) Рабочий зазор» После иллюстрированного пояснения
сравнительной незначительности этого разрыва, Том рекомендует: —
«Минимальный зазор — для пара или
IC. — должно быть 0,002» и направляющая вполне может быть установлена
зазор равен
0,001″ + 0,001″/дюйм диаметра цилиндра.»
«(b) Монтажный зазор. Это
размер G, когда кольцо нависает над наружным диаметром поршня, когда
примерка. Если это чрезмерно, кольцо может быть перегружено, но это
является размерность G — g, которая имеет значение, так что, как уже
отмечено, что риск перенапряжения увеличивается по мере увеличения свободного зазора. уменьшенный. К сожалению, все «книги», кажется, предполагают, что
кольцо плотно обхватывает поршень при установке, но это не
случае, и напряжения, основанные на этом допущении, будут слишком низкими.
Геометрический анализ практически невозможен, так как кольцо не предполагает
форму пары полукругов и, во всяком случае, фактический
направление сил, удерживающих кольцо врозь, неопределенно.
Эксперименты с рядом колец с различными отношениями и значениями D/t
D показывают, что G изменяется от 6,6 т до 7,5 т. Если g = 4, как при
Правил чаддок, тогда кольцо не будет перенапрягаться при
установлены — при условии, конечно, что рабочая нагрузка безопасна. Как
очень грубое приближение, напряжение при установке можно оценить по формуле
написание:-
fi = fw x (7 x t — g)/g Где fi =
напряжение установки, fw = макс. рабочее напряжение, t и g, как прежде.
Эта оценка никоим образом не является точной, но проверить «риск» можно, сравнив значение «g» до и после пробной примерки. Если есть заметное и постоянное увеличение «g», тогда кольцо очень близко к пределу.»
Оригинальный «Рэмсботтом»
кольца представляли собой простые круги, из которых вырезали зазор так, чтобы закрытый
кольцо подходило к цилиндру не более чем с рабочим зазором. Это было реализовано
что такое кольцо не подходит должным образом, и поэтому не может
оказывать равномерное давление даже после нескольких часов работы. Необходимость
форма для достижения этого была известна, конечно, и требует свободного
кольцо имеет радиус в любой точке, который изменяется как синус
угол сечения от точки, прямо противоположной зазору.
Ланчестер изобрел машину, которая придавала кольцам такую форму.
но сомнительно, чтобы какой-нибудь инженер-модельер взялся
сделай один. Однако на современных станках с ЧПУ процесс значительно усложняется.
проще, и таким образом изготавливаются многие большие кольца двигателей».0005
Затем Том описывает, как внутри простое кольцо можно отшлифовать для получения необходимого эффекта — и считает, что с маленьким кольцом слишком сложно.
Затем он рассматривает коническое кольцо, изготовленное путем растачивания внутреннего диаметра эксцентрично к OD, но исключает это, чтобы получить правильный характеристики, он требует, чтобы «t» было уменьшено до нуля при разрыв.
Тогда «Почти идеальное кольцо может быть
достигается за счет «термоформования», процесса, который можно приспособить
для крупносерийного производства, и которые могут быть использованы для очень небольших
действительно кольца. Здесь вырезается круговое кольцо одинаковой толщины с
очень маленький зазор. Затем его вдавливают в или на формованную форму,
и напряжение снято, так что при охлаждении кольцо имеет правильную форму.
форма, обеспечивающая как истинную округлость, так и равномерное давление на стенку
при установке в цилиндр, хотя почти во всех случаях
Операция механической обработки выполняется для «снятия» наружного диаметра. к
допускайте неизбежные допуски. Форма первого, из
конечно, аверс формы, которую использовал Lanchester много лет назад.
Это адаптация этого метода, который был описан проф. Чаддок ———— »
«К сожалению,
было неправильное понимание природы процесса некоторыми,
включая мистера Тримбла и мистера Таллоха. Во-первых, процесс НЕ
копия используемого в промышленности и не может образовывать
«идеальное» кольцо. Хотя он зависит от отношений в
выражение (2), в том, что клин оказывает «тангенциальное
сила», о которой здесь говорится, процесс не имеет и не может
производить точно правильную форму, эта сила может вызвать правильную
изгибающий момент в кольце, но не воспроизводит правильный
прогиба, так как тангенциальная сила вводит дополнительную
сжимающее напряжение. Это мало, но оказывает разрушительное воздействие на
форма колец, прилегающих к зазору. «и т. д. (см.
схемы)
«Нет возможности исправить
напряжения, изменяя характер клина (например, применяя
сила под углом, а не по касательной) и тот факт, что
клин может выпасть после зажима пакета колец не
разница. да и смысла «подгонять» клин нет
к углу зазора. Однако, как понял профессор Чеддок,
эффект можно смягчить, выполнив окончательную операцию скимминга
на О.Д. после термической обработки. Это обеспечивает истинную округлость и
уменьшает отклонение от условия равномерного давления до
ничтожные пропорции. Эта окончательная операция механической обработки имеет важное значение.
Однако это должно быть не более чем снятие
0,001 дюйма металла должно быть достаточно для кольца диаметром 1 дюйм и пропорционально
для больших размеров. Для моделей истинная округлость важнее, чем
равномерное давление».
По-видимому,
непонимание процесса снятия стресса, возможно
потому что в исходной статье также упоминается «отжиг».
Большинство последующих авторов цитировали «хорошую красную жару».
хотя г-н Тримбл приводит реальную цифру в 800 град/с. как и мистер
Таллох. Это ошибка, 800град/с. или «хорошая красная» ложь
выше критической температуры, и произойдет металлургическое превращение.
происходить. Твердость по Бринеллю будет снижена, как и U.T.S. и
значение руды и некоторый рост зерна произойдет — просто неправильно
требования к поршневым кольцам. Если материал представляет собой легированное железо
результаты могут быть еще более серьезными. Есть еще тот факт, что
может быть вызвано масштабирование. Не исключено, что использование этого высокого
температура привела к тому, что пользователи переходили на более жесткие кольца, чем были
необходимо просто потому, что термическая обработка привела к снижению
значение «Е» с последующей потерей давления на стенку.
«Правильная» температура
составляет 480 — 520 град/с. при медленном нагреве, температура поддерживается
в течение 1 часа на дюйм толщины, но не менее 10 минут для
очень тонкие кольца. Стопку можно охлаждать на воздухе от этой температуры,
хотя кажется, что никакого вреда от закалки маслом не возникает. Металл не имеет цвета
при этой температуре, но господа Левермор, 24 Endeavour Way,
Лондон, SW19 8UH являются импортерами «Markall Thermomelt».
мелки. Метка с одним из них станет глянцевой в указанное время.
температуры, и они доступны от 100 град/c. до 1200 град/с.
В качестве альтернативы, это приведет к очень незначительному ухудшению свойств.
от нагрева до 550 — 600 град/с. когда металл будет просто виден
при тусклом свете, но ни в коем случае нельзя допускать повышения температуры
подняться выше. (Критическая температура составляет 720 град/с. )
предпочтительнее использовать более низкую температуру в течение всего времени, а не
чем пытаться ускорить процесс, поднимаясь выше. Кстати,
накипь при этих температурах минимальная — сойдет с
полировка металла.»
Том также посвящает пару страниц маслосъемные и маслосъемные кольца, прежде чем сделать вывод о ступенчатом скребок с давлением на стенку от 20 до 30 фунтов/кв. дюйм. и с адекватные отверстия для выпуска масла должны быть адекватными — и это при условии свечи не замасливаются, разумнее мириться с большим расходом масла в модели. (Деннис Чеддок не использует их в своем движке.)
Кольца из бронзы упоминаются справедливо
часто, как правило, для использования в цилиндрах из бронзы. у меня было мало
опыт этих для моделей, но не сомневаюсь, что они могут быть
удовлетворительный. Однако следует иметь в виду некоторые моменты. Первый,
рабочее напряжение должно быть ниже предела текучести (или 0,1% доказательства)
цифра — обычно около 20тонн/кв.дюйм. — особенно во время
монтаж. Модуль Юнга того же порядка, что и у железа — 15.
миллион фунтов силы / кв. дюйм. Во-вторых, температура снятия напряжения лежит
очень близко к температуре отжига, и требуется большая осторожность
при термоформовании. Ни в коем случае не должно 350град/c. быть превышена и
температура 300град/с. должны быть нацелены. Это
температура, при которой яркая сталь становится синей — полезный ориентир!»
————————————————— —————
Окончательные выводы Тома заключаются в том, что для паровых двигателей и для
классическая модель I.C. бензиновые/газовые двигатели, которые можно обкатать на
скамья 6 — 8 фунт-сила/кв. дюйм. должно быть адекватным. Локомотивным кольцам может понадобиться
более высокое давление для ускорения прилегания, но не более 12 фунтов силы/кв. дюйм.
Более низкие давления должны быть возможны с правильно сформированными кольцами, с
последующий более свободный ход. Тип рабочей лошадки I.C. двигатель может понадобиться
16 — 18 lbf/sq.in., если только нагрузка не является серьезной, но даже в этом случае
Нельзя нарушать «правила Чаддока»; 20 — 22lbf/кв.дюйм.
рекомендуется как максимум, но может потребоваться эксперимент на скоростях
более 12000 об/мин.
Наконец, чтобы предотвратить вопросы, я должен добавить, что Том не цитировал никаких «рабочих примеров», для колец, предназначенных для этих выводов.
Фу!!
————————————————— ——
Предлагаемый метод изготовления малых Поршневые кольца:-
Сначала обработайте отверстие цилиндра — до диаметра D.
Определите сечение кольца
требуется и, если вы используете обычный, неразборный,
поршень, затем закончите его, сделав кольцевые канавки достаточно глубокими, чтобы дать
Зазор 0,004 дюйма за кольцами.
Изготовление стальной втулки для приспособление для обработки, расточенное до D+0,002″, длина прибл. D.
Патрон центробежно-литой по длине утюг и просверлите его в пределах 1/16 дюйма от внутреннего диаметра кольца на достаточную глубину. (см. далее)
Поверните наружный диаметр до D+0,002″ (используйте втулку в качестве калибра) для длина равна: — (w + ширина отрезного инструмента) x количество колец требуется плюс несколько запасных частей.
Используйте узкий разделительный инструмент, чтобы сделать ряд канавок. Глубина канавки должны быть точно равны t + 0,001 дюйма. ровно w + ширина отрезного инструмента + 0,001″ (припуск на притирку).
Теперь используйте острое тонкое сверлильное приспособление, чтобы открыть отверстие внутри кольца.
диаметр. По мере приближения к этому уменьшите разрез до 0,001 дюйма и
«опираться» на инструмент, чтобы предотвратить его резку «на выходе». Когда ты
достигнув финальной версии, вы будете вознаграждены небольшой связкой колец
на шейке инструмента.
Используйте швейцарский напильник, чтобы сломать острие
уголки внутри колец, чтобы они свободно двигались к низу
из их канавок.
Сделайте крошечный надрез на внутренней стороне каждого кольца очень тонкой
треугольным надфилем и сломайте его между указательным и большим пальцами или
используя большой палец, чтобы надавить на кусок проволоки на плоской
поверхность. Очень аккуратно зачистите поврежденные поверхности швейцарским напильником.
(№ 6 вырез)
Сделайте клин, чтобы держать щели открытыми.
Уложите клиновые кольца вокруг болта,
зажать их между двумя стальными пластинами и равномерно нагреть до 550 — 600
град/c (900 — 1000 град/F), т.е. просто видно в темноте, НЕТ
ГОРЯЧЕ! Выдержать при этой температуре 10 мин, затем дать остыть. — кольца не должны иметь окалины. (Я сделал это успешно на
электрическая плита с конфоркой, которую можно настроить на правильный
сначала температуру а потом кольца положили на нее и оставили на 30
мин.)
Упакуйте кольца в гильзу и наденьте втулку на стержень. Установите диск и зажимные кольца надежно с помощью гайки. Сдвиньте рукав и используйте двигатель цилиндр в качестве калибра взять один ты отрезал кольца и уменьшил их диаметр до D.
Наконец, притрите боковые стороны колец. чтобы соответствовать их пазам. Они должны быть совершенно свободными, но с зазор всего 0,001 дюйма или менее.
Примечания.
Этот рисунок скопирован с рисунка, сопровождающего статью Тома.
На чертеже профессора Чеддока размер D — 0,002 дюйма обозначен как D,
т. е. требуемый диаметр кольца, а также только одно зажатое кольцо
в этом.
Я успешно сделал и использовал, К.И. кольца до 1/4″ x 0,010″ x 0,010″ (принимая 25% поломок) используя этот метод, но должен повторить, что я не предпринята последняя операция скимминга. Осмотр кольца на мой Stuart 10 после очень интенсивного использования показывает идеально ровную полировку, но близкое микроскопическое исследование двух квадратных колец 0,016 дюйма на моем миниатюрном судовом двигателе после нескольких часов работы показывает мельчайшие выступы в промежутках с более темным металлом на несколько градусов простирающийся вокруг них. Тем не менее, сжатие/производительность отлично с очень низким трением — несколько тысяч оборотов в минуту при 15 psi..
————————————————— ——————————-
После написания вышеизложенного я должен
признаться, у меня были серьезные опасения по поводу моей способности
последний ты’ из одного из моих миниатюрных колец. Нет проблем с
шлифовальные станки или кольца, где t превышает 30 тыс., но для
действительно маленькие кольца, и инструментами сомнительной точности я бы
предпочитаю более безопасный метод.
Поэтому я взял на себя смелость внести поправку в Чаддока/Уолшоу. приспособление для превращения кольца I/D диаметром минус 0,010 дюйма в втулка, плотно входящая в регистр, выточенный в зажимном диск: аранжировку, которую мне было бы легче сделать с требуемой точности, и я бы также придерживался рекомендаций профессора Чеддока. иллюстрации и установите кольца по отдельности.
Требование предельной точности при зажиме приспособления может можно преодолеть, сделав его последним объектом, подлежащим механической обработке перед обрабатывая кольца — и оставляя их в патроне.
Однако я бы предпочел сделать приспособление из
серебряной стали, закалите ее перед использованием и (пуристам не нужно читать
дальше!) сними последний тычок тонким алмазным напильником; с использованием
приспособление в виде пары «кнопок подачи» и с работающим токарным станком
примерно при 200 об/мин.