Диагностика подвески. Как правильно?
Омологированные продукты
Подробнее
Оставить заявку на РЕМОНТ
Новости, статьи
01|09
Новая функция SPACE регистрации подвески на двойных поперечных рычагах.
Компания SPACE выпустила новую функцию регистрации подвески на двойных поперечных рычагах («Double Wishbone»), для всех моделей стендов сход развал.
12|07
Новая модель горизонтально-расточного станка с ЧПУ, модель LBM950 от COMEC (Италия).
Объявляем анонс новой модели горизонтально-расточного станка с ЧПУ, модель LBM950 от COMEC (Италия). Станок оснащен сенсорным экраном TOUCH SCREEN с программным обеспечением под контролем ЧПУ что позволяет….
Читать все
АЛЬПОКА Групп
23.10.2016
Сегодня мы вновь возвращаемся к теме диагностирования подвески автомобиля. Столь пристальное и стабильное внимание к этому вопросу объясняется довольно просто.
Для большинства мультимарочных автосервисов замена деталей подвески и регулировка ходовых характеристик автомобиля — один из основных источников дохода. Соответственно, правильная организация процессов диагностики и ремонта подвески — это верный способ увеличения прибыли и повышения финансовой стабильности предприятия.
Традиционный набор оборудования и инструментов, с помощью которых автослесарь проверяет состояние подвески и рулевого управления не менялся в течение довольно долгого времени.
Входной контроль — в основе всего В настоящее время на рынке есть вполне объективные технологии для проверки состояния тормозной системы и амортизаторов.
Позволяют производить диагностику тормозной системы, рулевого управления, определять размер увода автомобиля от прямолинейного движения в мм/м, тестировать амортизаторы автомобиля (определять показатели демпфирования и резонансную частоту) по методу EUSAMA.
Что же касается шаровых соединений, рулевых наконечников и так далее, то ничего кроме визуального контроля их состояния производители оборудования предложить пока не могут.

Соответственно, максимальная комплектация поста диагностики подвески включает в себя: тормозной стенд, стенд проверки амортизаторов, пластину бокового увода колес, и гидравлический люфт-детектор, расположенный на смотровой яме, либо в составе ножничного подъемника, — отмечает Генеральный директор компании «Альпока Групп» Владимир Платон — данная комплектация позволяет в течение 10—15 минут получить максимально полную информацию о состоянии подвески и загрузить работой посты общего ремонта».
Количество автосервисов, оборудованных данными линиями инструментального контроля, по словам … активно растёт.
Многие владельцы станций технического обслуживания уже осознали, что данная диагностическая линия — эффективный инструмент загрузки автосервиса и привлечения клиентуры.

Смысл данной операции заключается в том, чтобы дать клиенту максимум информации о том, в каком состоянии находится его автомобиль. Вовсе не обязательно, тут же убеждать клиента, отремонтировать все выявленные дефекты. Вы просто сообщаете ему о том, что тормозные усилия на колесах распределяются неравномерно, а рулевые тяги нуждаются в замене через 2—3 тысячи километров. Практика показывает, что через некоторое время эти клиенты возвращаются на СТО, и выполняют данные работы.» — заявляет Владимир Платон.
Расположение поста диагностики в ремонтной зоне может быть любым.
Главное условие —наличие свободного пространства 8 метров в длину и 4 метра в ширину. Целесообразнее устанавливать её на въезде в автосервис, чтобы после прохождения линии, автомобиль мог свободно ехать на любой из постов ремонта, без лишнего руления по ремонтной зоне.
Впрочем, линия инструментального контроля не осложняет проезд автомобилей, поскольку все её элементы устанавливаются заподлицо с полом и не затрудняют маневрирование внутри помещения.

Впрочем, есть и другие точки зрения на саму технологию диагностики подвески, а следовательно и на набор необходимого для этого процесса оборудования. Директор компании «Барклай Холдинг» Дмитрий Буянов считает, что современные условия ремонта автомобилей требуют комплексного подхода во всем, даже в таком, казалось бы, банальном вопросе, как замена шаровых опор, или тормозных колодок.

Давайте рассмотрим предложенный Д. Буяновым подход на нескольких примерах.
Итак, всю работу по ремонту подвески и рулевого управления можно разделить на 4 этапа:
- — определение проблемы,
- — подбор запасных частей,
- — правильная установка запасных частей,
- — обеспечение максимального межремонтного пробега.
Допустим, ваш клиент приезжает на автосервис с неопределенным стуком в подвеске. Источник стука вы можете диагностировать только визуально — других способов диагностики, как справедливо выше отметил Владимир Платон пока не изобретено.
Будете ли вы при этом использовать детектор люфтов, который значительно облегчает физическую работу автомеханика, или нет — ваше дело. Можно лишь отметить, что «раскачивание» вручную подвески таких автомобилей, как Toyota Land Cruiser, Volkswagen Touareg, Mitsubishi Pajero требует довольно серьезной физической подготовки.
В процессе диагностики выясняется, что источником стука является, шаровая опора, либо сайлент- блок. Естественно, первоочередная задача — подобрать клиенту деталь оригинального качества и правильно установить её на автомобиль. Однако на этом работа не должна заканчиваться.
Автомеханик обязан проверить работоспособность сопутствующих узлов, которые могут повлиять на дальнейшую ходимость данной детали. «Если речь идет о шаровой опоре, рычагах, сайлент- блоках, рулевых тягах, то необходимо в обязательном порядке проверить работоспособность амортизаторов. Если его демпфирующие свойства уже сильно далеки от идеальных, то необходимо указать клиенту на это и объяснить, что это может стать причиной преждевременного износа только что установленных автокомпонентов. — поясняет Дмитрий Буянов. — Безусловно, дальнейшие решения о ремонте принимает сам клиент, но он должен обладать всей полнотой информации, чтобы у него потом не возникало вопросов — почему у новой шаровой так быстро порвался пыльник и тому подобное».
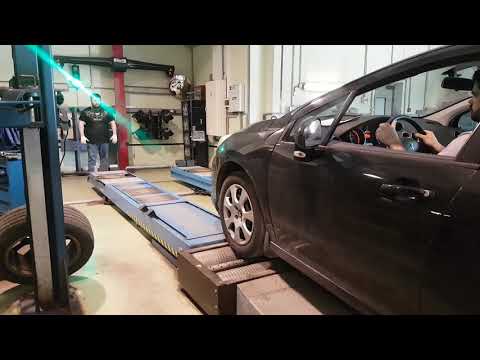
Обратная взаимосвязь должна присутствовать при замене амортизаторов. Если вы меняете стойки, то надо проверять шаровые, сайлент-блоки, рулевые наконечники, рычаги и состояние ступичного подшипника.
При выявлении дефектов — указывать на них клиенту и рекомендовать замену. Не случайно, сервис-центры KYB дают максимальную гарантию на свои амортизаторы только в том случае, если клиент при замене восстанавливает подвеску целиком.
Подобных примеров в сфере ремонта ходовой части и подвески можно привести очень много.
Установка новых деталей рулевого управления обязательно должна сопровождаться проверкой углов установки колес и выставлением руля в нулевое положение. Причем последняя операция на современных автомобилях выполняется с помощью системного сканера, а не «на глаз», как это было принято ещё несколько лет назад.
Тем не менее, на которых автосервисах сегодня до сих пор выравнивают положение руля путем перестановки рулевого колеса на шлицах рулевой колонки, что недопустимо.

Конечным итогом ремонта должно стать предоставление клиенту объективных данных о том, «как было» и «как стало». Если мы будем ориентироваться на такой подход в ремонте подвески, то набор автосервисного оборудования, который так или иначе задействуется в процессе диагностики ходовой части будет включать в себя следующие стенды:
- 1. Люфт-детектор. Не обязателен, но существенно облегчает работу и увеличивает пропускную способность автомобилей давая понять быстро проблемные места подвески.
- 2. Стенд проверки амортизаторов. Проверка автомобиля на данном стенде обязательна, как при замене самих амортизаторов, так и при ремонте сопутствующих узлов, чтобы продлить их ходимость.
- 3. Стенд «развал-схождения». Рекомендуется использовать стенд РУУК 3D, поскольку при большом потоке клиентов, стенды с навесными датчиками могут сдерживать пропускную способность СТО.
А теперь рассмотрим более подробно одно из оптимальных решений люфт детектор, так для чего нужен люфт детектор? это быстрая и точная диагностика всех элементов и узлов подвески автомобиля, это пожалуй единственная профессиональная альтернатива на сегодня.
Повышение конкурентоспособности — это не только увеличение пропускной способности, но и установление доверительных отношений с клиентом. Обслуживать постоянного клиента всегда выгоднее, чем искать нового.
Если вы в своей работе будете помнить об этом, то вам не придется решать проблему с заполняемостью своего предприятия.
Журнал Трансервис Автобизнес Март 2012
Возврат к списку
Новости, статьи
01|09
Новая функция SPACE регистрации подвески на двойных поперечных рычагах.
Компания SPACE выпустила новую функцию регистрации подвески на двойных поперечных рычагах («Double Wishbone»), для всех моделей стендов сход развал.
12|07
Новая модель горизонтально-расточного станка с ЧПУ, модель LBM950 от COMEC (Италия).
Объявляем анонс новой модели горизонтально-расточного станка с ЧПУ, модель LBM950 от COMEC (Италия). Станок оснащен сенсорным экраном TOUCH SCREEN с программным обеспечением под контролем ЧПУ что позволяет. …
Читать все
128. Детектор зазоров ходовой части и подвески.
Детектор (стенд) предназначен для обнаружения дефектов крепления и зазоров в шарнирных соединениях, сайлентблоках, кронштейнах амортизаторов ходовой части легковых и грузовых автомобилей, в подвеске двигателя, рулевом приводе, подшипниках ступиц колес и т.п., а также выявления мест возникновения различных посторонних стуков и скрипов.
Стенд представляет собой одну или две стационарно установленные платформы, состоящие из неподвижных плит с антифрикционными наладками и подвижных площадок, которые лежат на антифрикционных накладках и могут перемещаться под воздействием штоков гидроцилиндров, расположенных во взаимно перпендикулярных направлениях.
Принцип работы детектора заключается в принудительном перемещении колеса передней подвески автомобиля знакопеременными силами и визуальном определении соответствующих люфтов.
В
зависимости от модели стенда площадки,
на которых устанавливаются колеса
автомобиля, передают поперечные,
поперечно-продольные или поперечно-продольные
и диагональные (по диагонали под углом
45°) колебания с частотой примерно одно
движение в секунду, имитируя движение
по дороге. Ход площадок в одном
направлении составляет 40…150 мм (в
зависимости от модели стенда). Детекторы
для проверки легковых автомобилей
развивают усилие около 11 кН, грузовых
– около 30 кН.
Контроль соединений осуществляется визуально с помощью подсветки, вмонтированной в переносной пульт управления. Управление площадками производится кнопкой, размещенной также на переносном пульте управления.
Стенд может монтироваться на осмотровых канавах, эстакадах, платформенных электрогидравлических подъемниках ножничного типа (в двух исполнениях – с заглублением либо установкой на поверхности).
ТО стендов заключатся в смазывании направляющих подвижных площадок через каждые 200 ч работы. В случае применения гидравлического привода следует проверять уровень масла в накопительном бачке и менять его согласно инструкции по эксплуатации стенда.
Амортизаторы
наряду с другими системами и агрегатами
оказывают существенное влияние на
безопасность движения. Известно, что
отсутствие надежного контакта колеса
с опорной поверхностью, особенно при
высоких скоростях движения автомобиля,
приводит к снижению скорости движения,
предельно допустимой по условиям
безопасности, при повороте на 10…15 % и
увеличению тормозного пути на 5…10 %. При
неисправных амортизаторах частота
колебаний может исказить информацию,
поступающую в блок управления АБС;
при этом возможно ошибочное растормаживание
колеса.
Неисправные амортизаторы приводят к нестабильному и неравномерному освещению дороги, ослеплению водителей встречных автомобилей вследствие повышенного колебания кузова или шасси. Переднеприводной автомобиль с амортизаторами, изношенными на 50 %, при движении с постоянной скоростью по дороге, покрытой слоем воды толщиной 6 мм, может начать аквапланирование при скорости, на 10 % меньшей скорости такого же автомобиля, но с исправными амортизаторами.
Износ
и старение деталей амортизаторов
происходят медленно, вследствие чего
постепенно снижается и эффективность. Водитель не чувствует резких изменений
в поведении автомобиля, привыкая к
постепенному ухудшению его характеристик.
В связи с этим в процессе эксплуатации
автомобиля весьма актуальны периодическое
диагностирование амортизаторов и оценка
эффективности их работы.
Для оценки состояния подвески (в первую очередь, амортизаторов) автомобиля в процессе эксплуатации применяются стенды, имитирующие движение автомобиля по неровностям. Их действие основано на моделировании резонанса в подвеске автомобиля, который возникает в результате воздействия внешней силы от неровностей опорной поверхности. При этом частота колебаний подвески оказывается близкой к частоте свободных колебаний неподрессоренной массы. При резонансе резко возрастают амплитуды и ускорения вынужденных колебаний масс, их уровень зависит от качества (технического состояния) амортизаторов.
Стенд
для проверки амортизаторов представляет
собой две площадки, на которых
устанавливается автомобиль последовательно
передними и задними колесами (рис. 1.69).
Рис. 1.69. Схема стенда для проверки амортизаторов:
1 – колесо автомобиля; 2 – площадка; 3 – электродвигатель; 4 – маховик; 5 – эксцентрик; 6 – рычаг
Каждая из площадок 2 снабжена встроенными датчиками для измерения как статической, так и динамической нагрузки на колеса автомобиля. Колебания площадок производятся с помощью эксцентрика 5 электродвигателя 3 и рычага 6.
При подключении стенда платформы начинают совершать вертикальные колебания с различными для выпускаемых стендов амплитудой (6,0, 7,5 или 9,0 мм) и частотой возбуждения, изменяющейся от максимальной (16 или 23 Гц), которая выше, чем резонансная частота колебаний неподрессоренной массы, до нулевой (при отключении стенда). За счет пружин малой жесткости в приводе стенда обеспечивается постоянный контакт колес автомобиля с платформами.
При
достижении максимальной частоты
источник питания электродвигателей
отключается, и система начинает
совершать свободные затухающие
колебания. В случае приближения частоты
собственных колебаний неподрессоренной
массы к области высокочастотного
резонанса происходит увеличение
амплитуды колебаний; чем оно
значительнее, тем хуже работает
амортизатор.
Результаты колебательного процесса при работе стенда автоматически обрабатывается и заносится в память компьютера, а по окончании измерений отдельно для подвески каждого колеса автомобиля распечатываются результаты проверки.
Оценка состояния подвески автомобиля производится по методу EUSAMA (Европейская комиссия по стандартизации вибрационных методов испытаний в машиностроении) в зоне высокочастотного резонанса посредством измерения изменяющейся при колебаниях платформы силы воздействия колеса на измерительную площадку.
Стенды
для проверки амортизаторов, например
фирмы МАХА (серии FVT) могут быть
предназначены для линейного поста. При
этом заезжать на площадку надо строго
по продольной оси. Рычаги привода таких
стендов качаются вокруг оси. Стенды
другой серии (SA), этой же фирмы благодаря
параллелограммному рычагу под
площадкой дают этой площадке возможность
перемещаться вверх и вниз поступательно.
Благодаря этому автомобиль может
заезжать на площадку под любым углом,
что позволяет оптимально использовать
площади, на которых производится проверка
подвесок.
4. Стенды для экспресс-диагностики ходовой части автомобиля. Диагностическое оборудование
Диагностическое оборудование
курсовая работа
Рис. 3.3. Модули платформенного стенда динамической проверки автомобилей: а — с одним тормозным модулем; б — с двумя тормозными модулями
Необходимость точной и объективной инструментальной диагностики ходовой части автомобиля (рис. 3.2) понятна всем. Надежные тормоза, синхронное срабатывание амортизаторов, отсутствие чрезмерного износа шин часто спасают не только автомобиль, но и жизнь его владельца. Тем не менее очень немногие автосервисы обладают необходимыми стендами или линиями инструментального контроля ходовой части. Причина этого банальна — такое оборудование очень дорого, сложно в установке, занимает площадь, которой всегда не хватает на СТОА и отнимает время клиента. Выходом из этой ситуации являются платформенные стенды динамической проверки автомобилей. Платформенный стенд динамической проверки автомобилей состоит из платформ тормозного модуля и модуля измерения схождения колес (рис. 3.3).
Принцип платформенного стенда прост: диагностика ходовой части проводится «на ходу», в динамике, т. е. когда автомобиль «движется по дороге», когда на него действует не только сила тяжести, но и сила инерции, перераспределяющая нагрузки на переднюю или заднюю ось, на правый или левый амортизатор. Современный платформенный стенд диагностики ходовой части представляет собой две полосы плоских металлических платформ, уложенных на уровне пола, соединенных между собой кабелями и оснащенных дисплеем и компьютером. Толщина платформ составляет 40 мм, вместо приводов или других силовых установок используются тензометрические датчики. Дисплей и коммутационный блок крепятся на стене или потолочном перекрытии, а компьютер устанавливается в любом удобном для мастера месте.
Приняв автомобиль клиента, мастер приемки проезжает по стенду, тормозит на нем и проезжает к месту обслуживания. В течение 30 с компьютер обрабатывает полученные от тензо-метрических датчиков сигналы и выдает мастеру распечатку результатов диагностики.
В основу работы тормозных модулей положен принцип прямого измерения тормозной силы с помощью силоизмерительных датчиков, установленных под рельефными платформами. Датчики измеряют приложенную к поверхности платформы силу, возникающую при торможении испытуемого автомобиля. Тормозные усилия сканируются датчиками в течение всего времени торможения и обрабатываются компьютером, при этом значение максимальной тормозной силы в ньютонах высвечивается на дисплее стенда. Все текущие значения тормозной силы с интервалом в 0,15 с выдаются на принтер и показываются на распечатке. Если в память компьютера ввести вес автомобиля и нормы схождения колес, то программа рассчитает эффективность и устойчивость торможения, сравнит их с нормами ГОСТ (они заложены в компьютерную программу стенда) и на распечатке выдаст не только их значение, но даст заключение о соответствии полученных данных требованиям ГОСТ.
Динамический метод измерений позволяет легко определять тормозные усилия даже на автомобилях с полным постоянным приводом колес.
Величина схождения колес на каждой оси автомобиля определяется при проезде испытуемого автомобиля по платформам модуля измерения схождения колес. Модуль состоит из двух установленных параллельно платформ — подвижной и неподвижной. Поперечное отклонение подвижной платформы под действием силы, вызванной наличием угла схождения, измеряется встроенным датчиком и обрабатывается компьютером. Величина суммарного схождения колес на данной оси (в мм) высвечивается на дисплее и отображается в распечатке.
Информация о динамических колебаниях автомобиля после его остановки на платформах тормозного модуля распечатывается на принтере в виде графиков и позволяет оценить эффективность работы подвески испытуемого автомобиля. Максимальные значения амплитуд колебаний выдаются в относительных единицах.
Если остальные детали подвески (рычаги, рессоры, опоры и т. д.) исправны, то полученные данные напрямую соответствуют состоянию амортизаторов.
Делись добром 😉
Диагностическое оборудование
5. Стенды диагностики бокового увода колес
Увод автомобиля от направления прямолинейного движения зависит от величины углов установки управляемых колес (схождение и развал). Правильная установка колес (УКК) — залог хорошей управляемости автомобиля, снижение нагрузки, а следовательно…
Организация технического обслуживания и текущего ремонта с планировочным решением участка по диагностике и ремонту ходовой части легковых автомобилей
6.3 Стенды для диагностики и контроля ходовой части
Стенды контроля увода автомобиля. Эти стенды представляют собой площадочное устройство, платформа которого имеет возможность смещаться в сторону, противоположную силам увода автомобиля с траектории прямолинейного движения (рис. 7.)…
Организация технического обслуживания и текущего ремонта с планировочным решением участка по диагностике и ремонту ходовой части легковых автомобилей
6.

Участок по диагностированию и ремонту ходовой части автомобилей может размещаться отдельно или в общем помещении. В ряде случаев в составе участка по ремонту ходовой части выделяется помещение для мойки агрегатов, узлов и деталей…
Проект диагностического участка станции технического обслуживания автомобилей
4.2 Техническое диагностирование ходовой части автомобиля
Основные неисправности ходовой части, возможные причины их возникновения, способы проверки и устранение дефектов представлены в таблице 2.1. Таблица 2…
Проект реконструкции зоны агрегатного ремонта в ремонтно-механической мастерской
2.4 Планировочное решение участка по диагностированию и ремонту ходовой части автомобиля
Участок по диагностированию и ремонту ходовой части автомобилей может размещаться отдельно или в общем помещении. В ряде случаев в составе участка по ремонту ходовой части выделяется помещение для мойки агрегатов, узлов и деталей. ..
Проектирование локомотива
1. Расчет ходовой части электровоза
Нагрузка от колесной пары на рельсы и сцепная масса локомотива связаны известным соотношением: , кН (1.1) где 2П — нагрузка от колесной пары на рельсы, кН; Мсц — сцепная масса локомотива, т; nкп — количество колесных пар локомотива. Следовательно…
Разработка технологии технического обслуживания и ремонта силовых агрегатов, трансмиссии и ходовой части автомобиля
4.Техническое обслуживание ходовой части
…
Регистрация и контроль технического состояния автомобиля
6. Неисправности ходовой части, электрооборудования кузовов и прочих элементов конструкции с которыми запрещена эксплуатация транспортного средства
6.1. Количество, тип, цвет, расположение и режим работы световых приборов не соответствует требованиям конструкции транспортного средства. 6.2. Регулировка фар не соответствует ГОСТу Р 51709-2001 6.3…
Ремонт и техническое обслуживание ходовой части ГАЗ-3102
3.
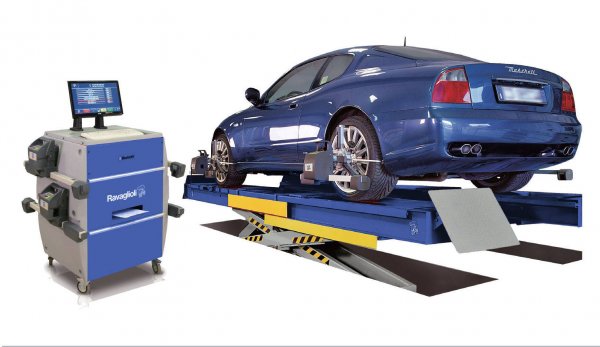
Таблица 3.1 — Возможные неисправности передней подвески…
Ремонт и техническое обслуживание ходовой части ГАЗ-3102
4. Техническое обслуживание ходовой части ГАЗ 3102
Техническое обслуживание передней подвески. Через первые 1000 км проверить сходимость передних колес…
Ремонт и техническое обслуживание ходовой части ГАЗ-3102
6. Приспособления и инструменты применяемые при техническом обслуживании и ремонте ходовой части ГАЗ 3102
Домкрат Ключи комбинированные (рожковый — накидной) Торцевые головки Крестообразная отвертка Шлицевая отвертка Выколотки из мягкого металла. Зубило. Молоток. Тиски. Надфиль. Бородок. Монтажная лопатка. Пассатижи. Раздвижные пассатижи…
Ходовая часть автомобиля
1.1.1. Назначение ходовой части
Рама — это несущая система грузового автомобиля. Она воспринимает все нагрузки, возникающие при движении автомобиля и служит основанием, на котором монтируют двигатель, агрегаты трансмиссии, механизмы органов управления. ..
Ходовая часть автомобиля
1.1.4. Устройство ходовой части
Рама. На грузовых автомобилях наибольшее распространение получили лонжеронные рамы. Они состоят из двух продольных параллельных блок-лонжеронов, соединённых поперечинами, с использованием заклёпок или сварки. В зонах…
Ходовая часть автомобиля
1.2.1. Техническое обслуживание ходовой части
Неисправности элементов ходовой части (рамы, подвески осей и колёс) в основном возникают при эксплуатации автомобилей с нагрузкой, превышающей максимальную грузоподъёмность…
Ходовая часть автомобиля
1.2.2. Выбор оборудования и приспособлений для ремонта ходовой части
Для разборки заклепочных соединений рамы применяют пневматические рубильные молотки. Качество правки деталей рамы контролируют проверочными линейками и шаблонами. При сборке рам применяют гидравлическую клепальную установку…
Что такое тестирование K&C? — Morse Measurements, LLC
Проверка кинематики и соответствия (K&C):
Испытания на кинематику и соответствие требованиям (испытания K&C) — это тип квазистатических испытаний подвески, при котором к шасси и шинам транспортного средства применяются реалистичные нагрузки и смещения для определения геометрии подвески и характеристик жесткости.
Давайте разберем это.
Испытания K&C представляют собой особый вид испытаний подвески транспортных средств.
«К» означает кинематику — это геометрия подвески (схождение, развал и т. д.). «C» означает соответствие — это жесткость подвески (т. е. насколько сильно изгибаются вещи, когда дорожные нагрузки проходят через шины).
Измерение кинематики подвески и характеристик податливости очень сложно без соответствующих инструментов. Представьте, что вы пытаетесь приложить к шине боковую нагрузку в 2000 фунтов, измеряя отклонение схождения! В компании Morse Measurements измерения K&C упрощаются благодаря нашему современному испытательному стенду Anthony Best Dynamics K&C, первому в своем роде независимо управляемому и общедоступному в Северной Америке.
Испытательная машина AB Dynamics K&C в компании Morse Measurements специально разработана для перемещения и загрузки транспортного средства на нашем объекте способами, которые было бы очень трудно сделать другими способами.
Как работает тестирование K&C?
Этот испытательный стенд крепится к шасси автомобиля снизу и перемещает его в вертикальном направлении, крене и тангаже. Шины остаются в контакте с ровной «дорожной плоскостью» на четырех отдельных колесных колодках. Эти колесные колодки могут поддерживать нулевое усилие трения (благодаря непрерывному контролю силы с обратной связью) или они могут создавать силы на уровне земли для имитации тормозных, ускоренных и поворотных нагрузок в пятнах контакта шин. Прецизионные цифровые энкодеры и тензодатчики постоянно измеряют нагрузку на шины и ориентацию колес.
Все эти силы и перемещения применяются медленно (квазистатически) для захвата зависимости силы подвески от смещения и трения. Измеряя все эти параметры в компании Morse Measurements, где все доступно и воспроизводимо, вы можете сократить количество догадок и сократить расходы, связанные с дорожными/дорожными испытаниями.
После завершения испытаний мы получаем огромное количество информации и идей о подвеске автомобиля. Мы можем разделить характеристики и тесты на кинематику и соответствие.
Кинематика относится к геометрии подвески. Общими кинематическими характеристиками являются схождение и развал колес, поворот на неровностях, изменение ширины колеи и колесной базы при отскоке/крене и повороте по крену. Эти характеристики имеют решающее значение при сравнении сборки прототипа с предполагаемой конструкцией, при оценке плавности хода и управляемости автомобиля или при создании точной модели автомобиля.
Мы используем набор тестов для всесторонней оценки кинематики подвески. Вот несколько наиболее распространенных тестов кинематики, которые мы проводим:
- Испытание на отскок: Стол перемещается вверх и вниз, при этом подушки поддерживают нулевые силы трения и выравнивающие моменты. Мы используем его для определения скорости вращения колес, скорости движения, поворота/развала/кастера, движения центра колеса, кинематической высоты центра крена, угла/длины виртуального поворотного рычага и многого другого.
- Прокатное испытание: Стол вращается вокруг продольной оси, а колодки колеса сохраняют нулевые силы трения и выравнивающие моменты. Мы используем тесты на качение для определения управляемости по крену, поворота оси, жесткости по крену, распределения жесткости по крену, коэффициента статической передачи веса по крену, смещения центра колеса и многого другого.
- Проверка рулевого управления: На этот раз стол удерживается неподвижно, пока робот-рулевой перемещает маховик в пределах его диапазона перемещения. Затем измеряются нагрузки и перемещение на передних колесах. Мы используем тест рулевого управления для определения характеристик оси шкворня, механического следа, процента Аккермана, мгновенного передаточного числа рулевого управления и многого другого.
- Щелкните здесь, чтобы ознакомиться с дополнительными тестами.
В этом контексте податливость является обратной величиной жесткости. Это связано с тем, насколько компоненты подвески изгибаются или двигаются под нагрузкой. Эта информация необходима для полного понимания системы подвески.
Вот несколько тестов, которые мы используем для измерения характеристик податливости:
- Испытание на боковую податливость: В этом испытании стол фиксируется, в то время как боковые силы передаются на шины через колесные колодки. С помощью этого теста мы определяем управляемость оси, боковую жесткость схождения, боковую жесткость развала и многое другое.
- Испытание на продольную податливость: Подобно поперечному испытанию, в ходе испытания на продольную податливость стол фиксируется, в то время как продольные силы передаются на шины через колесные колодки. С помощью этого теста мы определяем, среди прочего, продольную жесткость схождения, жесткость развала и углы, препятствующие нырянию/приседанию.
- Испытание на выравнивающий крутящий момент: В этом испытании стол фиксирует шасси, в то время как выравнивающий момент передается на шины через колодки.
В ходе этого теста мы определяем такие характеристики, как жесткость схождения, жесткость при выравнивании шин, гистерезис и обратную связь по крутящему моменту.
- Щелкните здесь, чтобы ознакомиться с дополнительными тестами.
Ни одна другая компания не может дать мне подробное представление о динамике подвески и совместимости компонентов, как Morse Measurements со своей установкой K&C.
Джефф Браун
Владелец Transact Race Engineering Inc.
Как вы планируете тест K&C?
Мы помогаем нашим клиентам планировать свои тесты K&C с учетом целей, которых они хотят достичь. За последние 15 лет мы наблюдаем появление некоторых общих тенденций, вот несколько общих целей:
- Получить данные, необходимые для CarSim или другой модели динамики автомобиля.
- Оценить качество и эффективность сборки прототипа.
- Сравните автомобили конкурентов, чтобы оценить их конструктивные решения.
- Сравните характеристики различных компонентов подвески.
- Настройте втулки, стабилизаторы поперечной устойчивости и т. д. для достижения желаемых целей автомобиля.
Узнайте больше о планировании теста K&C для достижения ваших целей.
Свяжитесь с нами, чтобы узнать больше о тестировании K&C, запросить бесплатное предложение или задать вопрос.
Есть вопросы о тестировании K&C?
Тестирование K&C имеет огромный потенциал для программы разработки вашего автомобиля… но понять этот потенциал и как его использовать не всегда просто. Если у вас есть вопросы о тестировании K&C, посетите нашу страницу часто задаваемых вопросов или посмотрите бесплатный веб-семинар с ответами на самые распространенные вопросы.
Проверка кинематики и соответствия (K&C):
Испытания на кинематику и соответствие требованиям (испытания K&C) — это тип квазистатических испытаний подвески, при котором к шасси и шинам транспортного средства применяются реалистичные нагрузки и смещения для определения геометрии подвески и характеристик жесткости.
Давайте разберем это.
Испытания K&C представляют собой особый вид испытаний подвески транспортных средств.
«К» означает кинематику — это геометрия подвески (схождение, развал и т. д.). «C» означает соответствие — это жесткость подвески (т. е. насколько сильно изгибаются вещи, когда дорожные нагрузки проходят через шины).
Измерить кинематику подвески и характеристики податливости очень сложно без соответствующих инструментов. Представьте, что вы пытаетесь приложить к шине боковую нагрузку в 2000 фунтов, измеряя отклонение схождения! В компании Morse Measurements измерения K&C упрощаются благодаря нашему современному испытательному стенду Anthony Best Dynamics K&C, первому в своем роде независимо управляемому и общедоступному в Северной Америке.
Испытательная машина AB Dynamics K&C компании Morse Measurements специально разработана для перемещения и загрузки транспортного средства на нашем объекте способами, которые было бы очень трудно сделать другими способами.
Как работает тестирование K&C?
Этот испытательный стенд крепится к шасси автомобиля снизу и перемещает его в вертикальном направлении, крене и тангаже. Шины остаются в контакте с ровной «дорожной плоскостью» на четырех отдельных колесных колодках. Эти колесные колодки могут поддерживать нулевое усилие трения (благодаря непрерывному контролю силы с обратной связью) или они могут создавать силы на уровне земли для имитации тормозных, ускоренных и поворотных нагрузок в пятнах контакта шин. Прецизионные цифровые энкодеры и тензодатчики постоянно измеряют нагрузку на шины и ориентацию колес.
Все эти силы и перемещения применяются медленно (квазистатически) для захвата зависимости силы подвески от смещения и трения. Измеряя все эти параметры в компании Morse Measurements, где все доступно и воспроизводимо, вы можете сократить количество догадок и сократить расходы, связанные с дорожными/дорожными испытаниями.
После завершения испытаний мы получаем огромное количество информации и идей о подвеске автомобиля. Мы можем разделить характеристики и тесты на кинематику и соответствие.
Кинематика относится к геометрии подвески. Общими кинематическими характеристиками являются схождение и развал колес, поворот на неровностях, изменение ширины колеи и колесной базы при отскоке/крене и повороте по крену. Эти характеристики имеют решающее значение при сравнении сборки прототипа с предполагаемой конструкцией, при оценке плавности хода и управляемости автомобиля или при создании точной модели автомобиля.
Мы используем набор тестов для всесторонней оценки кинематики подвески. Вот несколько наиболее распространенных тестов кинематики, которые мы проводим:
- Испытание на отскок: Стол перемещается вверх и вниз, при этом подушки поддерживают нулевые силы трения и выравнивающие моменты. Мы используем его для определения скорости вращения колес, скорости движения, поворота/развала/кастера, движения центра колеса, кинематической высоты центра крена, угла/длины виртуального поворотного рычага и многого другого.
- Прокатное испытание: Стол вращается вокруг продольной оси, а колодки колеса сохраняют нулевые силы трения и выравнивающие моменты. Мы используем тесты на качение для определения управляемости по крену, поворота оси, жесткости по крену, распределения жесткости по крену, коэффициента статической передачи веса по крену, смещения центра колеса и многого другого.
- Проверка рулевого управления: На этот раз стол удерживается неподвижно, пока робот-рулевой перемещает маховик в пределах его диапазона перемещения. Затем измеряются нагрузки и перемещение на передних колесах. Мы используем тест рулевого управления для определения характеристик оси шкворня, механического следа, процента Аккермана, мгновенного передаточного числа рулевого управления и многого другого.
- Щелкните здесь, чтобы ознакомиться с дополнительными тестами.
В этом контексте податливость является обратной величиной жесткости. Это связано с тем, насколько компоненты подвески изгибаются или двигаются под нагрузкой. Эта информация необходима для полного понимания системы подвески.
Вот несколько тестов, которые мы используем для измерения характеристик податливости:
- Испытание на боковую податливость: В этом испытании стол фиксируется, в то время как боковые силы передаются на шины через колесные колодки. С помощью этого теста мы определяем управляемость оси, боковую жесткость схождения, боковую жесткость развала и многое другое.
- Испытание на продольную податливость: Подобно поперечному испытанию, в ходе испытания на продольную податливость стол фиксируется, в то время как продольные силы передаются на шины через колесные колодки. С помощью этого теста мы определяем, среди прочего, продольную жесткость схождения, жесткость развала и углы, препятствующие нырянию/приседанию.
- Испытание на выравнивающий крутящий момент: В этом испытании стол фиксирует шасси, в то время как выравнивающий момент передается на шины через колодки.
В ходе этого теста мы определяем такие характеристики, как жесткость схождения, жесткость при выравнивании шин, гистерезис и обратную связь по крутящему моменту.
- Щелкните здесь, чтобы ознакомиться с дополнительными тестами.
Как вы планируете тест K&C?
Мы помогаем нашим клиентам планировать свои тесты K&C с учетом целей, которых они хотят достичь. За последние 15 лет мы наблюдаем появление некоторых общих тенденций, вот несколько общих целей:
Получить данные, необходимые для CarSim или другой модели динамики автомобиля.
Оценить качество и эффективность сборки прототипа.
Сравнивайте автомобили конкурентов, чтобы оценить их конструктивные решения.
Сравните характеристики различных компонентов подвески.
Настройте втулки, стабилизаторы поперечной устойчивости и т. д. для достижения желаемых целей автомобиля.
Узнайте больше о планировании теста K&C для достижения ваших целей.
Свяжитесь с нами, чтобы узнать больше о тестировании K&C, запросить бесплатное предложение или задать вопрос.
Есть вопросы о тестировании K&C?
Тестирование K&C имеет огромный потенциал для программы разработки вашего автомобиля… но понять этот потенциал и как его использовать не всегда просто. Если у вас есть вопросы о тестировании K&C, посетите нашу страницу часто задаваемых вопросов или посмотрите бесплатный веб-семинар с ответами на самые распространенные вопросы.
Технологии | kw_7post
крепление колеса по умолчанию:
разболтовка: | отверстие ступицы: | нить: | сиденье: | длина вала: мм
- Койловеры
- Демпфирование и клапан — 2-ходовой
- Демпфирование и клапан — 3-ходовой
- Демпфирование и клапан — 4-ходовой
- Демпфирование и клапан — 5-ходовой
- Линия из нержавеющей стали
- 7-постовое динамическое испытание
- Функция и качество
Испытательный центр KW в Фихтенберге предоставляет автоспортивным командам и отраслевым партнерам возможность моделировать ход подвески автомобиля на реальных гоночных трассах. Это делается на гидравлическом семистоечном испытательном стенде компании KW. Независимо от того, используете ли вы развертку с 4 постами, воспроизведение трека с 4 постами или воспроизведение трека с 7 постами. Испытательный центр KW позволяет спортивным командам считывать от 50 до 100 измерений в день в зависимости от типа гоночного автомобиля. Установка системы демпфера для соревнований KW окажется полезной, поскольку вы сможете максимально использовать дополнительные преимущества системы демпфера для соревнований.
Во время цикла испытаний шасси KW можно снять и сразу адаптировать к результатам измерений. При измерениях на 7-стоечном стенде для проверки динамики транспортных средств не происходит износа транспортных средств, как в реальных ездовых операциях, и, помимо капитала, наши клиенты экономят время. Испытательный стенд с широким спектром возможностей для испытаний представляет интерес для всех, кто хочет получить больше от своего шасси с помощью технологии испытаний Формулы-1.
Преимущества
Стенд для испытания динамики вождения 7post, принадлежащий KW Automotive, предлагает клиентам возможность выполнять анализ и оптимизацию вертикальной динамики своего автомобиля.
- Повторяемость благодаря постоянным условиям внешней среды
- Экономия времени (50-100 измерений в день / в зависимости от типа автомобиля)
- Отсутствие износа автомобиля
- Без проката гусениц
- Возможность тестировать автомобили, которые не готовы к вождению
- Непрерывное документирование всех измерений
- Анализ данных с помощью Matlab® и MS Excel®
- Оптимизация различных параметров
- Резонансные частоты тела
- Степень демпфирования
- Кивание
- Строительные грузчики
- уровень динамического автомобиля
- Колебания нагрузки на колесо
- Для амортизаторов KW возможна непосредственная замена узла амортизатора и выбор пружины.
Характеристическую кривую демпферов можно регулировать.
Инфраструктура
В дополнение к испытательному стенду имеется мастерская с двухстоечным автомобильным подъемником. Кроме того, доступны возможности тестирования амортизаторов от компаний Schenk (кривошипно-шатунный механизм), API Dyno (электронно-механический) и Röhrig (гидравлический).
Требования
- Колесная база: мин. 1500 мм/макс. 3450 мм
- Гусеницы: мин. 1100 мм/макс. 1900 мм
- Вес: макс. 3,5 т
Контрольный список
- Транспортное средство в эксплуатации:
- Подшипники шасси
- Шины (возможно дополнительные шины со значениями давления горячего воздуха)
- Колесные нагрузки (соответствующее содержимое бака, доступны балластные мешки)
- Геометрия оси
- Высота автомобиля
- Принесите дополнительные пружины и амортизаторы
- Принесите специальные инструменты (например, накладной замок, центральный замок, баллон со сжатым воздухом для подъемной системы)
- Для датчиков по индивидуальному заказу, подходящий адаптер для разъема типа LEMO (PHG.
1B.304.CLLD62Z)
Методы анализа — 4-х постовый свип
Процедура испытаний
Возбуждение четырехколесных приводов посредством синусоидальных колебаний хода с постоянной максимальной скоростью при пересечении нуля 50, 100, 150, 200 или 250 мм/с и возрастающей частотой 1-20 Гц.
Услуги/анализ
- Оптимизация резонансных частот тела (использование по назначению)
- Оптимизация степени демпфирования (соотношение между усилиями пружины и демпфирования)
- Оптимизация поведения кивания (баланс)
- Оптимизация движения тела (управление автомобилем/комфорт)
- Оптимизация динамического уровня автомобиля (коэффициент сжатия/отбоя)
- Оптимизация колебаний нагрузки на колесо (тяговое усилие)
- Оптимизация минимальной движущей силы колеса (тягового усилия)
- Определение динамической жесткости шины
В дополнение к этому частотному анализу также возможны частоты и скорости возбуждения, а также режимы в соответствии с требованиями заказчика. Также могут быть проведены испытания на жесткость валков. Постоянные аэродинамические силы можно имитировать с помощью двух дополнительных пневматических рессор.
Оборудование
- четыре датчика ускорения колес
- два датчика ускорения кузова
- два или четыре датчика смещения на гасителях вибрации или между ободом и крылом
4-кратное воспроизведение трека
Процедура тестирования
Стимулирование приводов с помощью файла диска, который был создан путем итерации трека из реальных данных трека. Анализ проводится по конкретным трекам, глобально и по секторам.
Услуги/Анализ
- Обработка данных и итерация данных трека для создания драйв-файла на испытательном стенде
- Определение участков пути с проблемными зонами для дифференцированной оценки
- Оптимизация ускорений раскачки и тангажа в зависимости от маршрута
- Отраслевая оптимизация колеи колебаний нагрузки на колесо
- Опционально: реализация анализа 4 постов
Дополнительные требования
- Должны быть доступны данные о маршруте измеряемого транспортного средства.
Запись:
- Вертикальное ускорение четырех колес / колесных опор (датчики можно взять напрокат)
Внимание: Постоянные аэродинамические силы можно имитировать с помощью двух пневматических рессор, но нельзя качать и качать из-за продольного или поперечного ускорения. Для этого необходимо сделать повтор трека 7post.
Воспроизведение 7-стоечного трека
Процедура испытаний
В дополнение к работе четырех колесных домкратов инерция и выходная сила вводятся непосредственно в конструкцию транспортного средства с помощью трех дополнительных приводов. Приводы стимулируются с помощью файла диска, который был создан с использованием итерации маршрута из реальных данных маршрута и Aeromap. Анализ проводится по конкретным маршрутам, в глобальном масштабе и по секторам.
Услуги/Анализ
- Обработка данных и итерация данных трека для создания драйв-файла на испытательном стенде
- Моделирование аэродинамических нагрузок согласно спецификации или aeromap
- Определение участков пути с проблемными зонами для дифференцированной оценки при различных условиях движения
- Варианты разделения: секторы торможения, прохождения поворотов, тяги и выемки, секторы низкой, средней и высокой скорости и определение недостаточной и чрезмерной управляемости
- Оптимизация ускорения раскачки и тангажа в зависимости от сектора маршрута
- Оптимизация колебания нагрузки на колеса в зависимости от сектора маршрута
- Отслеживание секторальной оптимизации динамического уровня автомобиля
- Опционально: Проведение анализа 4-кратной развертки с постоянным выходным усилием
Дополнительные требования
- Должны быть данные по аэродинамике
- Должно быть известно положение центра тяжести автомобиля
- Должны быть доступны данные о маршруте измеряемого транспортного средства.
Запись:
- Вертикальное ускорение четырех колес / колесных опор (датчики можно взять напрокат)
- Скорость автомобиля
- Продольное ускорение
- Боковое ускорение
- Кронштейны аэродинамических приводов / ЛВЦ
Подробный контрольный список предоставляется по запросу.
Контакты — проверка динамики автомобиля
KW 7-Пост-тест на динамику автомобиля
Электронная почта: [email protected]
Брошюры, контрольные списки и цены предоставляются по запросу.
Установка для испытаний на автомобильную вибрацию с четырьмя плакатами
Вернуться к архиву блогашейкеры, Контроль вибрации
Для испытаний на надежность автомобилей испытания на открытом воздухе идеальны, но не всегда практичны. В ответ индустрия разработала внутренние тестовые установки для воспроизведения треков на открытом воздухе. Эти тесты должны воспроизводить операционную среду, чтобы быть эффективными. Тем не менее, они обеспечивают повторяемость и ускорение испытаний.
Установка с четырьмя опорами является общепринятым методом моделирования профиля дороги. Как правило, это гидравлическая система, в которой четыре колеса неуправляемого автомобиля установлены на отдельных опорах. Инженеры используют эту установку для испытаний на долговечность, NVH-тестирования, определения частотных характеристик и многого другого. Дорожные условия больше всего влияют на подвеску и раму автомобиля, поэтому 4 постера часто используются для проверки этих конкретных компонентов.
Стенд с четырьмя плакатами для тестирования BSR
Компоненты, возбуждаемые дорожными условиями, создают шум в той или иной форме, и слышимые помехи должны быть минимальными для комфорта пассажиров. При тестировании на жужжание, скрип и дребезжание (BSR) выводится вибрационный сигнал, вызывающий реакцию автомобиля, которая затем обнаруживается с помощью акустического анализа.
Инженеры используют этот тип испытаний для оценки компонентов автомобиля на основе шума, который они издают во время работы. Результаты теста зависят от интерпретации человеком шума или показателей качества звука, таких как громкость, эксцесс и шероховатость.
Инженеры часто используют стенд с четырьмя стойками для тестирования BSR, поскольку тестовая установка отражает рабочую среду. Они могут провести тест в камере с четырьмя балдахинами для более специализированного контроля температуры или шума.
Разработка тестового профиля
Чтобы выполнить испытание на вибрацию с четырьмя постами, инженер сначала создает тестовый профиль для управления системой. Контроллер вибрации использует профиль для отправки сигналов в гидравлическую систему для соответствующего возбуждения тестируемого устройства (ИУ).
Тестовый профиль для установки с 4 стойками должен максимально точно отражать условия эксплуатации. В идеале инженер делает записи испытаний на открытом воздухе для разработки профиля испытаний в помещении. Тем не менее, инженеры могут использовать исторические данные или стандарты испытаний, когда запись в полевых условиях невозможна.
После того, как инженер разработал тестовый профиль, он может решить ускорить его. Автомобили годами выдерживают удары и вибрации. Ускоренные профили испытаний могут помочь выявить потенциальную усталость и определить срок службы компонента или транспортного средства в целом.
Управление установкой с 4 плакатами
Конфигурация с четырьмя стойками возбуждает четыре вибростенда вдоль одной и той же оси (обычно оси z). Инженер воспроизводит записанные файлы данных для каждого колеса. Затем они воспроизводят записи одновременно, как если бы автомобиль находился в движении.
Контроллер вибрации формирует управляющий сигнал, сравнивая управляющее ускорение от вибростенда/тестируемого устройства с требуемым заданием. Алгоритмы управления минимизируют разницу между сигналами управления и запроса, регулируя форму и амплитуду управляющего сигнала.
Эта ссылка на управление и спрос образует то, что называется контуром управления. Когда контроллер(ы) посылает независимые управляющие сигналы на несколько шейкеров, система выполняет многоконтурное управление. Многоконтурное управление распространено, когда несколько шейкеров управляют тестовым элементом на одной оси.
Пример настройки
Для многоконтурного теста в VibrationVIEW требуется один VR9500 на контур управления или VR10500 с включенными несколькими контурами. Для каждого VR9500 требуется соответствующее программное обеспечение VibrationVIEW (в зависимости от тестового режима). Основной контроллер VR10500 должен управлять всеми выходами, но система может иметь стекированные контроллеры для более чем 16 входов (до 512).
Режимы тестирования Sine, Random, Shock и FDR могут запускать 2, 3 или 4 выходных контура возбуждения одновременно, но предлагают различные варианты/возможности для управления. Многоконтурная синусоида доступна только с VR10500.
Система с четырьмя стендами для автомобильных испытаний
Производители автомобилей тестируют автомобили на открытых трассах, чтобы воспроизвести конечное использование. Тем не менее, тестирование в помещении на стенде с 4 стойками сравнимо по точности, если профиль тестирования отражает рабочую среду. Система с несколькими контурами управления гарантирует, что сигнал возбуждения соответствует требованиям, а запись в полевых условиях помогает разрабатывать более точные профили.
Четырехстоечная страница программного обеспечения
Дата
16 февраля 2022 г.
Автор
Джаред Ван Барен
Ссылки
[1] Чиндамо, Даниэль, Марко Гадола и Фелипе П. Марчезин. «Воспроизведение профилей реальных дорог на стенде с четырьмя стойками для тестирования шасси автомобиля и подвески в помещении». Успехи машиностроения 9, вып. 8 (2017): 1–10. Journals.sagepub.com/doi/10.